Have you ever wondered what happens when metal corrodes? How it gets fixed? Can it be fixed? The world of corrosion is one most are not privy to. Thankfully, there are individuals who have an in-depth knowledge of this subject. Corrosion engineers play an integral role in ensuring that stainless steel applications and structures are well maintained and monitored.
Stainless Steel World Americas had the great pleasure of speaking with Thu Addis, a Corrosion Engineer working with bp, supporting the Gulf of Mexico operations, about the ins and outs of working with stainless steel. She provided knowledgeable insight into the differing types of corrosion, the challenges of pitting corrosion, and offered advice for new engineers entering the corrosion industry.
By Angelica Pajkovic
Pursuit of Knowledge
Addis began her studies in the world of corrosion after immigrating to the United States. Seeking a career that would both feed her love of learning, as well as provide opportunities for growth, she chose to further her understanding of corrosion science.
“I was always interested in STEM (science, technology, engineering, and math), and spent years studying these subjects. It was not until I arrived in the U.S., that I began to learn about corrosion,” Addis reflected. Having already earned her Master’s degree in Process Engineering in France, Addis was able to immerse herself in the study of CO2 corrosion, quickly achieving a PhD in the subject.
Addis began her career with bp as an intern while defending her PhD thesis. Recognizing her talent and potential, she was soon offered a position within the corrosion and engineering sector of bp. Since then, Addis has been able to grow and flourish under the guidance of her mentors and line managers, who have significantly invested in her development.

Day-to-Day
Today, one of Addis’s focus is managing internal corrosion from subsea to topside facilities, providing support on chemical treatment and testing. Once a new chemical is qualified, it is brought to an offshore location to ensure that it works prior to it being deployed. “My work involves risk identification, prevention, and mitigation. I monitor KPI’s on a regular basis to ensure all the corrosion barriers are healthy,” said Addis.
When asked about what her average workday looked like, she replied, “That is a tough one because everyday is different. Since I work in operations, I go wherever the immediate needs are. If, however, there are corrosion issues with any of our equipment or piping, that is my main priority.” Working in corrosion is everchanging, meaning that no two days are the same, as no two projects are identical. Her projects vary from chemical testing, and coating qualification, to cathodic protection assessment covering both internal and external corrosion.
Corrosion engineering involves more than remedying projects that have already been victims to their environment; it also includes risk management and exploring methods of slowing down corrosion.
Internal vs. External Corrosion
Corrosion takes on two main forms; internal and external. While both can lead to significant damage, internal corrosion is caused by different factors than external corrosion. There are therefore different ways of addressing each form.
Internal corrosion refers to corrosion that takes place in the inside of a pipeline. This typically occurs when the presence of compounds like carbon dioxide (CO2), hydrogen sulfide (H2S), water, organic acids, and other molecules react with the internal pipe surface through anodic and cathodic reactions.1
“When dealing with internal corrosion, one of the main barriers we put in place is chemical injection. For CO2 corrosion, we typically inject a corrosion inhibitor, which reduces the corrosion rate to an acceptable level. For some systems, we also inject biocide to mitigate the risk of microbiologically influenced corrosion (MIC). We implement monitoring programs where corrosion probes and coupons are installed to ensure that the chemical is performing as it was intended.”
As the term implies, external corrosion is corrosion found on the outside of a pipe. External corrosion is a kind of electrochemical breakdown that occurs on the surface of a metal. This is mainly caused by environmental factors like water, soil, and air.2
“One of the primary ways to address external corrosion, is to paint the surface of the metal. We implement a fabric maintenance program for our offshore platforms. We typically perform a coating survey to assess the external surface conditions of the facility. We have a workflow to manage the anomalies. It is a joined effort between various Equipment Class Owners, specifically Pressure Systems Integrity Engineers, Structural Integrity Engineers, Subsea Integrity Engineers, Corrosion Engineers, and the Fabric Maintenance Execution team,” explained Addis.
Challenges in the field are unavoidable when working with corroding metals. While bp uses different types of corrosion resistant alloys, such as 300 series, duplex, and super-duplex stainless steel for various applications, as well as nickel and copper-based alloys, that are durable and reliable in different services, environmental and chemical wear is a reality. The difficulties, for Addis and her team, arise when there are issues that the corrosion engineers are not able to predict.
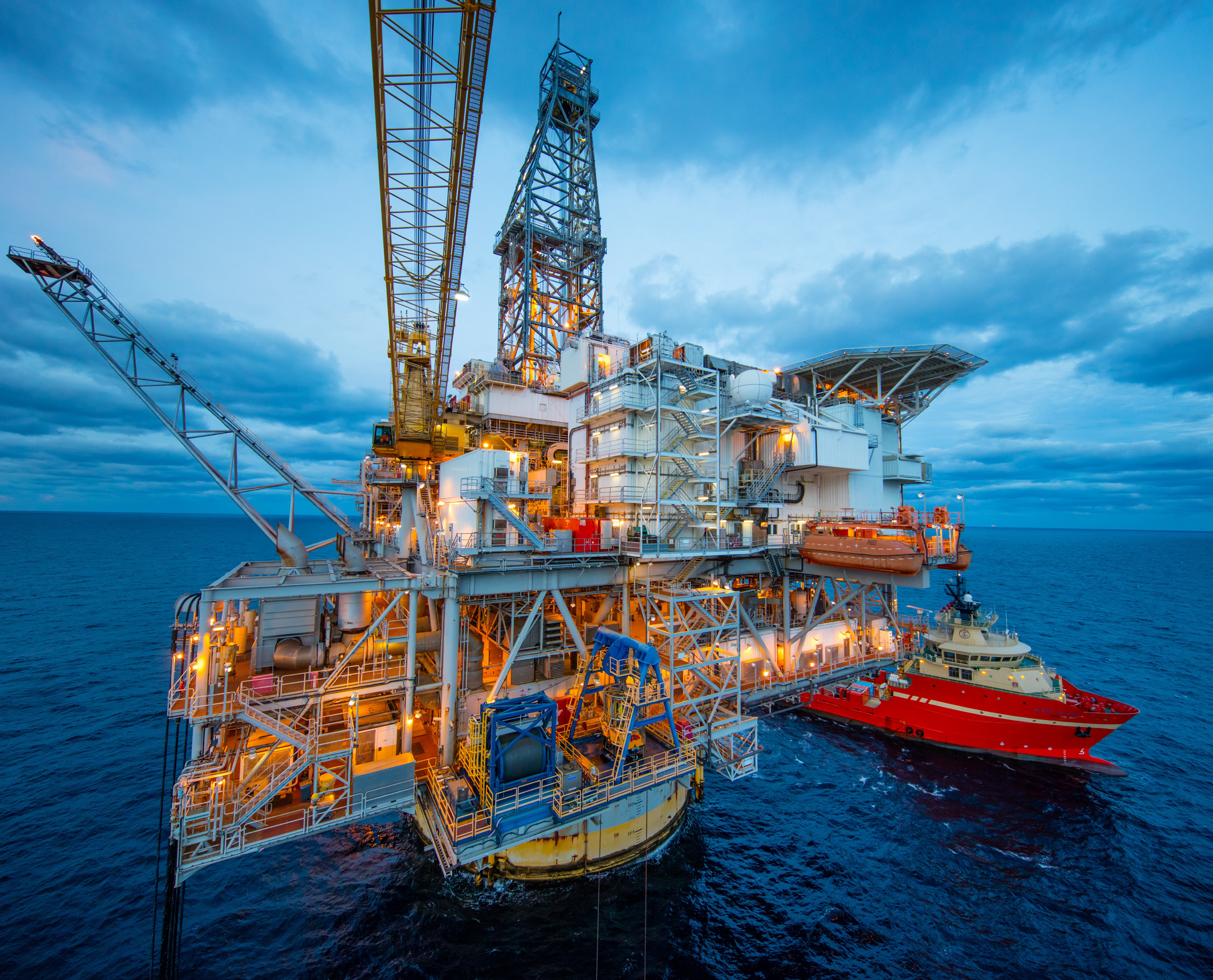
The Challenges of Dealing with Pitting Corrosion
Now that a basic understanding of corrosion has been outlined, dealing with it may not appear very difficult for the engineers who have an intricate understanding of it. A metal begins to corrode, and it is patched up, right? Well, while working with corrosion may appear to be straightforward, there is one unforeseeable instance that continues to stump corrosion engineers: pitting corrosion.
“Pitting corrosion is one of the most common challenge I face when working with stainless steel,” explained Addis. Pitting corrosion is much like a dental cavity in that it is a localized form of corrosion in which a pit or cavity is produced in the metal. Pitting is seen as more dangerous than uniform corrosion because it is difficult to detect, predict, as well as design against.3
“Each pit varies in size and shape, it is very difficult to predict when failure will occur, and the longevity of the equipment also differs,” she continued.
“I worked on a project a few years ago where we were able to qualify coating systems that could be applied to mitigate external corrosion and prevent pit growth on stainless steel. We continue to use these systems to this day,” Addis reflected.
Advice for Newcomers
Many specialists within the stainless steel industry agree that there has been a growing knowledge gap between those entering the field and the professionals leaving. Addis believes that this potential issue can be mitigated by making integration programs more known to new engineers.
When Addis entered the industry, she partook in bp’s Challenger Program. The Challenger Program for graduates hoping to delve into the world of engineering and provides participants the opportunity to work with and learn from knowledgeable industry experts.
“This program acts as a roadmap to follow and aid in the transition from academia to the workforce, and was very beneficial for me,” stated Addis. “It is important that you come into the industry with an open mind and a willingness to learn from others. Find opportunities to broaden your skills even if it is outside of your comfort zone.”
While Addis thinks it is imperative that newcomers learn from established professionals, she also acknowledges the fact that it is crucial for those already in the industry to welcome new faces with open arms. “In terms of the workforce, it is important to remain diverse and build a culture of inclusion to attract and retain talents from different backgrounds. Those now entering the field are going to be the future leaders who drive the industry, which I am really excited about,” Addis said smiling.
Addis’ understanding of the knowledge being passed between both newer and more established generations only further proves how there is space for anyone willing to learn in the stainless steel industry.
Looking to the Future
The stainless steel industry is ever evolving with the creation of new products, the signing of mergers (like that of NACE International and SSPC), and the actualization of sustainability missions. “I think there are a lot of initiatives in the industry to find new materials that are not only safer and more reliable, but also sustainable,” stated Addis. “The ongoing opportunity to learn and grow is what keeps me interested in this field of study, and I am excited for the chance to continue making progress in the industry, not only to lessen the effects of corrosion, but for the betterment of the environment,” she concluded.
References
- https://www.corrosionpedia.com/definition/2841/internal-corrosion#:~:text=Internal%20corrosion%20refers%20to%20 corrosion,organic%20acids%20and%20other%20molecules.
- https://www.corrosionpedia.com/definition/2842/external-corrosion#:~:text=External%20corrosion%20refers%20to%20 a,may%20occur%20in%20any%20circumstance.
- https://www.ampp.org/resources/impact/corrosion-basics/ group-1/pitting-corrosion#:~:text=or%20cup%2Dshaped- ,Pitting%20corrosion%20is%20a%20localized%20form%20 of%20corrosion%20by%20which,products%20often%20 cover%20the%20pits.
- https://inspectioneering.com/tag/risk-based+inspection
- https://www.assessteam.com/risk-management-kpis-list/#:~:text=Risk%20management%20KPIs%20are%20 metrics,objectives%20are%20met%20over%20time