Bolted-on repairs and retrofits are crucial to the operation and maintenance of above-ground storage tanks (ASTs). Such works ensure the tanks remain compliant with various safety and operational regulations.
By Mathew A. Rybicki, President and CEO, Forge Tech
If an AST is due for maintenance or has developed a fault, repair and retrofit works must be completed promptly to ensure the AST operator avoids fines associated with contravening compliance guidelines.
Another primary consideration when performing tank repairs is downtime. Since most repair works can stretch for weeks, especially if the works are extensive, keeping the tanks offline for this long can result in millions of dollars in downtime costs.
When considering such works, it is, therefore, vital to weigh the pros and cons of various welding methods, specifically friction welding.
What is Friction Welding?
Friction welding is a solid-state welding process that generates heat through mechanical friction between workpieces in relative motion to one another, with the addition of a lateral force called ‘upset’ to displace and fuse the materials plastically.
Friction welding was first used in the Soviet Union in the 1950s and later imported into the United States in the 1960s. Over the years, it evolved into a tried and tested technique used in the aerospace, military, and heavy manufacturing industries.
The most significant benefit of friction welding is that it does not rely on external heat sources to complete the welding process. When implemented as an AST repair technique, it can provide significant benefits.
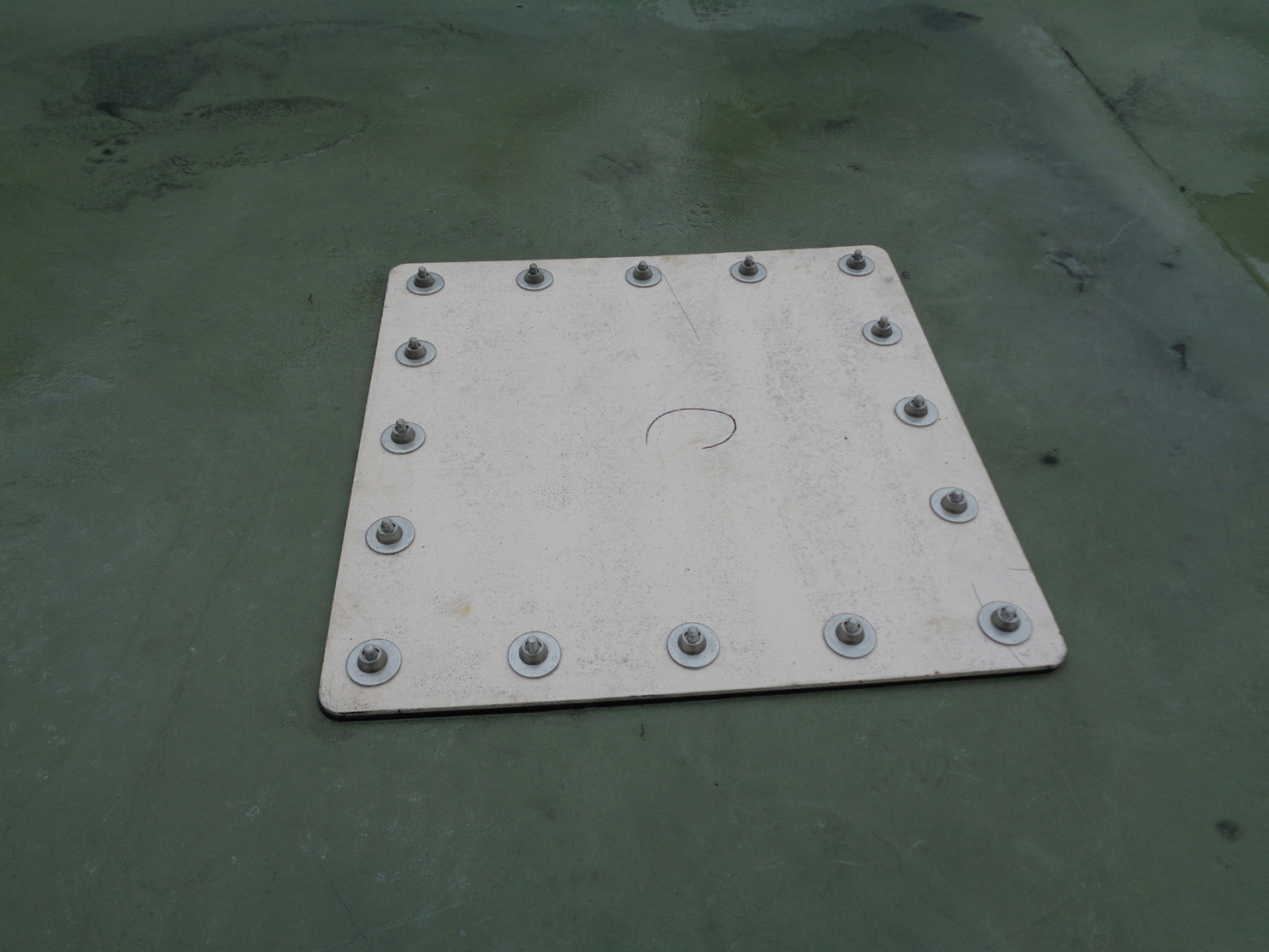
Friction Welding vs. Arc Welding
A standard welding technique used to repair ASTs is arc welding, which uses electricity to create enough heat to melt metal, and the melted metals, when cool, bind together.
One of the main disadvantages of arc welding is the production of sparks and heat, which can cause accidents in scenarios where flammable materials are present in or around the tanks. Because of this, tanks must be offline, and extensive safety measures should be followed when arc welding is in use.
On the other hand, friction welding, which does not produce sparks or ignitable heat, is a safer tank repair technique. It can be used while tanks are online and contain flammable materials.
Is Friction Stud Welding API Certified?
The American Petroleum Institute (API), which represents all segments of America’s natural gas and oil industry, has approved the inclusion of ‘friction stud welding’ in API 653 to allow tank retrofits and repairs to be made using friction stud welding.
Although friction welding has been in use for many years, the API’s adoption will further ensure that friction welding bolted-on retrofits and repairs are installed in accordance with accepted engineering practices.
In its announcement, the API noted that friction stud welding can be used to retrofit and repair in-service tanks where conventional welding would be unachievable due to the risk of igniting flammable vapors. Friction stud welding reduces and, in many cases, eliminates the chance of ignition by substantially lowering temperatures for shorter durations over smaller surface areas.
Specifically, the API proposed changes to API 653 Section 11, Section 12, and Annex F, to add the following sections.
Section 11.5 Friction Stud Welding
Rotary friction welding may be used to install studs on in-service and out-of-service tanks, including but not limited to tank shells, roofs, and floating roofs, by agreement between the Repair Organization and the Tank Owner-Operator.
Welding procedure specifications (WPSs) and welding operators shall be qualified in accordance with Section IX of the ASME Code, and both shall be certified. A WPS shall be created by the Repair Organization for each material P-No. in ASME Section IX. If the stud material is different than the base material, then a WPS shall be created for each material P-No. combination. Impact testing is not required for procedure qualification record (PQR) testing.

The work shall be performed in accordance with the requirements of API 650 Section 9 and the following requirements:
- The design of retrofits and repairs attached with friction welded studs shall be approved by a Storage Tank Engineer. The design shall consider all anticipated loading conditions and combinations, potential settlement movements, high strains and rotations at structural discontinuities such as the shell-to-bottom joint and shell penetrations, inability of bolted joints to share load with welds due to lesser stiffness, limited ability of bolted joints to carry shell hoop stress, gasket sealing forces, minimum/maximum design temperatures, design metal temperature, friction stud and base metal toughness, material compatibility, internal and external coatings and life span requirements.
- Installations on in-service tanks shall address risks related to the safety of workers and ignition of flammable tank contents specifically addressed in Section 1.4 of this standard. The Repair Organization shall demonstrate ignition safety by testing and submitting a written report to the Tank Owner-Operator. The Tank Owner-Operator and Repair Organization shall agree on the safety criteria and protocols to be used to demonstrate that the potential ignition safety issues have been addressed, providing that the side of the tank opposite to the friction stud welding does not create an ignition source.
- Areas to be friction welded shall be ultrasonically examined for remaining substrate thickness. A stud shall not be friction welded to a tank with less than 0.15” of remaining metal thickness without special consideration for ignition safety, stud strength, and quality of the remaining metal.
- Preheating and PWHT are not required.
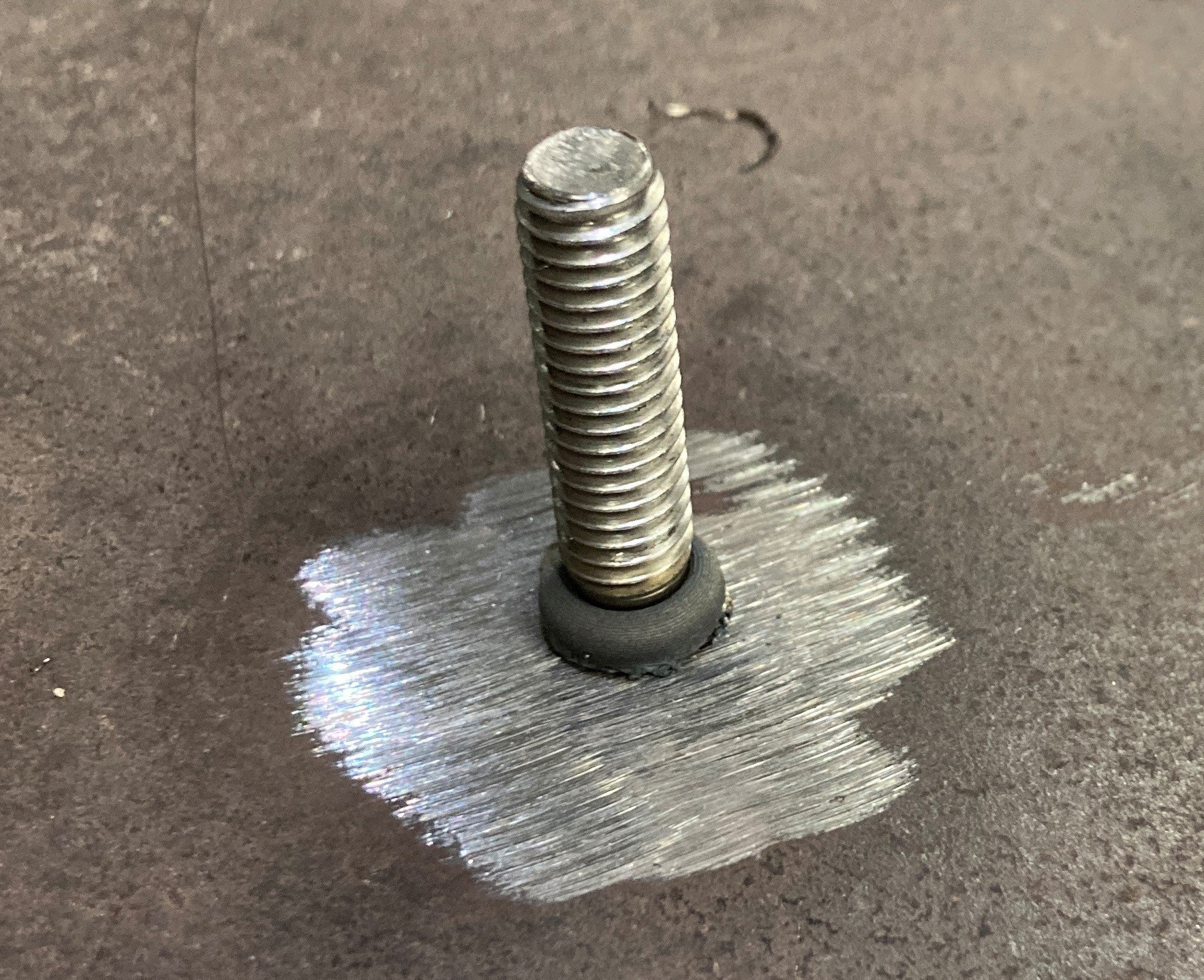
Section 12—Examination and Testing
12.1 NDE
12.1.11 Friction Stud Welds
Friction welded studs shall be visually examined and torque tested in accordance with ASME Section IX torque test requirements. The stress applied to the stud during the torque test shall not yield the stud material. The NDE of the friction welded studs shall apply for all tank and stud P-No. materials.
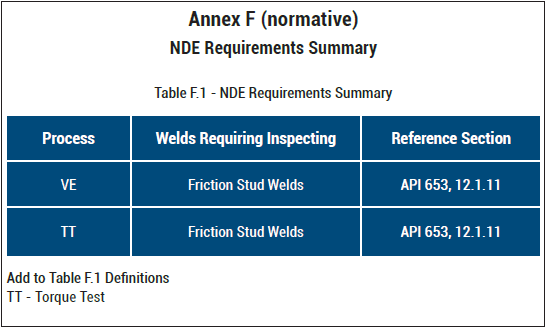
Conclusion
The API’s adoption of friction stud welding establishes it as a standardized option alongside other approved welding methods according to API guidelines. For example, Forge Tech, a global provider of friction welding services, worked closely with the API for three years to actualize this approval.
Forge Tech’s patented Forge Bonding solution utilizes portable forge bonding equipment that can be transported anywhere in the country and the world. The portability of the machines also makes this an ideal solution for repairing hard-to-reach repair areas.
With this approval by the API, AST owners and operators now have the assurance that friction stud welding for bolted-on retrofits and repairs is a standardized, recognized, and approved welding method that delivers exceptional benefits and unmatched safety.
