How does everything work? That is a question that has driven Winston Mosher, Materials and Process Engineer, InnoTech Alberta, throughout his life, and was a large contributing factor to his start in the industrial sector. Stainless Steel World Americas had the opportunity to speak with Mosher about how he entered the materials industry, his experiences as a Senior Research Engineer while working with corrosion resistant alloys (CRAs), and how he hopes the knowledge gap will be addressed in the future.
By Brittani Schroeder
Growing up in a town near Halifax, Nova Scotia (N.S.), Winston Mosher was always interested in how things were made and how they worked. To this day, Mosher is still searching for new ideas on how to improve the things we use daily. “At some point I learned that although many machines can be made more efficient through clever design modifications, eventually you will become limited by the inherent properties of the materials you are working with,” he says. The idea of being on the forefront of technology, by developing new and useful materials, was very interesting to Mosher, and he ultimately decided to study Materials Engineering at Dalhousie University, in Halifax, N.S. He continues, “I was fortunate to participate in a co-op program where I did a brief term in the local aero space sector, followed by eight months in Newfoundland and Labrador working in mineral processing. I learned a lot about both sectors, and how different companies operate. The things I enjoyed most while working in those areas were related to making improvements to processes and running tests to optimize systems and increase efficiency.”
After finishing his undergraduate degree, Mosher continued his education by completing a Master of Applied Science degree, focused on an emerging area of aluminum powder metallurgy for the automotive sector. “I was able to create new alloys and modify them to enhance their performances. I remember being excited to see how adding just a small percentage of specific elements to the mix could increase the strength of the alloy significantly,” he says. “I went on to publish papers on my work and became employed to work as a laboratory manager for some time. These experiences made me well suited to my current role in applied research.”
Around the time Mosher was working through his master’s degree, the economic crash of 2008 hit. When Mosher was searching for job opportunities after finishing his degree, the local economy was still feeling the effects of the crash – so Mosher broadened his search to all of Canada, and abroad. “I was very aware of the oil and gas industry in Western Canada; however, I did not see where I could fit into it,” he admits. “I was contacted by a former colleague who had been working for the Alberta Research Council about a position in their Advanced Materials team. He explained to me how their research efforts aligned with the goals of the pipeline industry, and that I would be immersed in designing experiments and testing technologies like coatings and alloys against degradation. It was a great way to enter the industry while immediately using my existing skillset.”
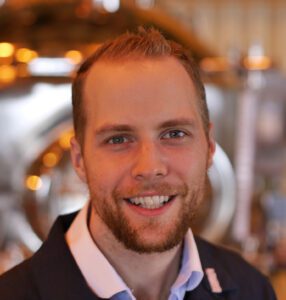
The life of a Senior Research Engineer
In his current role, Mosher is a Senior Research Engineer at InnoTech Alberta, a scientific, engineering, and technological research and testing company. In his role, Mosher has many responsibilities. “I work with clients to develop testing programs, then later manage those projects with a small team of technologists and researchers. Sometimes this will mean getting my hands dirty and building new equipment or designing and constructing pilot facilities,” he says. “I will analyze and interpret the testing results, and report back to the client. Occasionally, I have the opportunity to present some of my work at international conferences and have even organized some smaller conferences on pipeline integrity and corrosion management.”
Each year, it is also Mosher’s responsibility to secure the organization’s investment funds by building a good business case. Examples of this might be the development of a new or novel test method or technology related to corrosion mitigation. He continues, “Recently, I have been involved in developing and demonstrating novel processes related to 3D printing waste materials in support of a circular economy.”
Since the start of the pandemic, Mosher’s daily activities have certainly changed. Instead of heading into the office and laboratories each morning, Mosher has been doing his best to coordinate his projects and meetings remotely. “Generally, I will check in with my project team to get updates and results on the current projects, as well as provide support, direction, and technical solutions.” The rest of his day would be split up between report writing, planning for future projects, and providing project progress updates to his clients and supervisors.
When asked what he enjoys most about his work, Mosher says, “I really like seeing useful and interesting results develop out of the projects we generate. It is fun to answer questions we receive from the industry by providing results that may be counter intuitive. As one client put it, we are sort of like ‘myth-busters’,” he relays. “If I can offer my clients some information through testing that they can immediately take and use to improve their operations, then I am happy and motivated to take on the project.”
As with all research, there are always challenges when trying something new for the first time – these are the kinds of challenges that Mosher does not mind. “The greatest challenge in my role is in securing new clients who may not yet realize how we could help their business through focused applied research. Once I overcome that challenge, the process of working with the clients is considerably easier.”
Corrosion testing and mitigation projects
In Mosher’s work, he has encountered all sorts of corrosion problems with a variety of materials. “We perform several different varieties of corrosion testing for the oil and gas industry. Of course, oil and gas applications require the use of corrosion resistant alloys (CRAs) and other equipment that is capable of withstanding very aggressive environments,” he explains. “We have several Hastelloy C276 autoclaves we operate with hydrogen sulfide (H2S) gas and acidic brines. At temperature (~300°C) and under pressure (3,000 psi), these can mimic some very harsh conditions, even disintegrating carbon steel test samples within.” The intention is to simulate the types of environments encountered in thermal processing and to be able to qualify coatings or alloys for those applications. “It is extremely important when working with H2S that the vessel and its components maintain integrity and all other safety precautions are followed.” Mosher and his team also use more typical stainless steels – types 304, 316L – throughout the facilities in instrumentation and in all parts of process flow loops.
Mosher has worked on many projects that specifically looked at pipeline integrity integrity with a focus on internal corrosion mitigation. “We have studied the effects of cleaning pigs on removing sediment from corroded pipe; investigated different online monitoring technologies for corrosion, and developed our own technology for this purpose. We have conducted many projects where we have evaluated the effects of chemical corrosion inhibitors in flow loops for water treatment applications, and as applied to pipelines via pigging.” Mosher has also worked on projects involving microbiological induced effects on corrosion (MIC), under deposit corrosion (UDC), and sour gas corrosion. “Most recently, we have been working to solve an aggressive phenomenon called ‘tuberculation’, which can appear on stainless steel type 304 near the weld seams in even relatively mild plant conditions.” This type of corrosion is getting more attention lately due to its characteristic of forming large flow restricting growths of corrosion products, as well as quickly forming deep pits though the pipe wall. “Until recently, this type of corrosion was poorly understood, however we are just now discovering its root causes, which will allow us to develop better mitigation strategies going forward.”
Addressing a talent and knowledge gap
Throughout his time working in the industry, Mosher has seen a knowledge gap that is continuously widening. “The knowledge gap is very clear and apparent to me, and I have run into issues many times as a result. However, the senior workforce retiring is not the only cause of problem,” he says. “Often the most valuable workers are very mobile, and unfortunately in many cases, these workers will leave a company with no one qualified to take over their responsibilities.”
Mosher has learned that the talent and knowledge gap is due to a lack of companies’ foresight in terms of mentoring and training staff, as well as an undervaluation of the highly qualified people the companies depend on. “The clear strategy to reduce these effects is to have younger engineers working closely with experienced engineers daily, rather than each level operating independently. Additionally, companies may consider performing a talent gap analysis to then develop strategies for improvement,” he explains. “That said, I believe there is no substitute for decades of on-the-job experience.”
A hope for new engineers
Another lesson that Mosher has learned is that, as much as he learned in university and continues to learn about CRAs and proper material selection throughout his professional career, younger engineers need to understand that economics and asset lifecycles play some of the biggest roles in industrial design.
“Within this industry I have seen plenty of good design choices, however, I have also seen some very poor decisions be made in the name of budgetary constraints,” Mosher says. “Designing for the future has always been a hard sell when looking at the balance sheet. I would love to see a shift from a near-term financial outlook to a longer-term return on investment mentality, and I hope that new engineers will make significant strides in that direction.”