Castings and materials
Please describe the basic concept of what ‘casting’ is.
The team: Casting is the term given to the specific manufacturing method where molten metal is either injected or poured directly into a mold to form the desired shape of an object such as a particular valve shape. To explain in more specific detail, it is the transformation of the metal through heating. The process begins with the metal in a solid state (raw material) and then by being heated it transforms into a liquid state. It is then internally cast in a mold (which could be done in sand, in ceramics or in a metallic shell), where it is in the shape of the desired part. For valve parts that are casted, we can cite these three foundry processes: Sand Casting, Lost Wax Casting, and Casting by Centrifugation.
In terms of valve production, why is casting so important?
Casting is a critical element of the valve manufacturing process because it is related to the geometry of the projected parts with which it is made. That is, we can produce the parts adherering to the specifications of our client without affecting the quality of the final product. Proper quality casting can eliminate some of the machining aspects, thus reducing the final cost to the customer. Saving money for the client, but not at the expense of quality, is always important.
What does the term ‘investment casting parts’ pertain to?
Investment casting or ‘lost wax’ is a casting process in which a mold is made around a wax pattern that is burned away when the molten material is poured in. This particular method is often used to create more intricate parts or for complex materials such as exotic alloys like titanium, cobalt, or duplex.
Can you please summarize what the basic casting process is like at your company?
Yes, we can. Generally speaking, the investment casting process for valves follows these basic steps:
• Die/mold making
• Wax pattern making
• Wax pattern-tree
• Shell building
• De-waxing (wax removal)
• Shell firing
• Casting
• Refractory ceramic removal
• Finishing
• Heat treat
• Finish operation
• Quality inspection
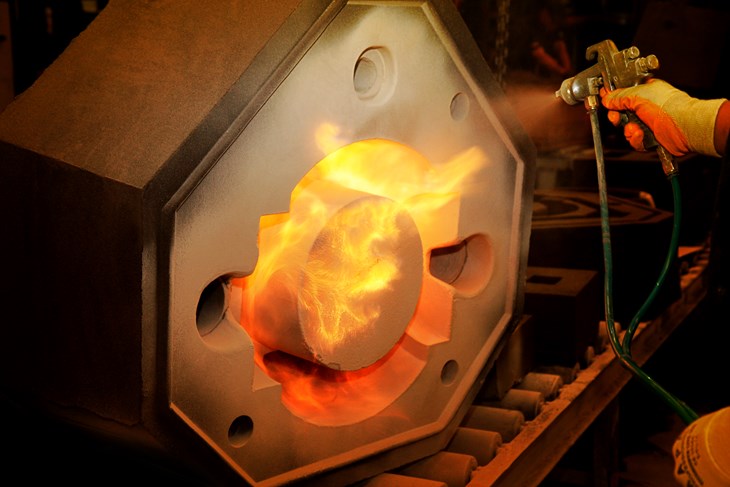
As an engineer, what do you have to keep in mind when deciding what casting to use?
Just some of the many different things that we need to keep in mind when deciding on the casting process are the following: casting configuration, the type of material that will be used based on end-use application, machining elements, surface requirements, what the appearance of the finished part will be, and lastly, what the final cost will be. So basically, I have to consider the entire process as a whole, and not just one aspect of it. I have to think about what will ultimately be the most efficient in terms of time and money, and also what will look the best.
What are some of the different alloys that you have created a casting from?
We have worked with many different types of materials from the common to the exotic. Just some of them include: carbon steel, stainless steels, low alloy steels, austenitic and martensitic steels, super duplex stainless steel, nickel and cobalt-based alloys, etc. We also have experience working with tool steels, which are materials that are used for tools and therefore have a high hardness, as well as vacuum materials, which are materials that react with oxygen from the air. Vacuum materials are often used for end-use applications in the aerospace industry.
Why are some alloys used instead of others during the castings process?
The alloy is chosen depending on the needs of the parts in terms of strength, conditions of use, and all of the requirements of the castings. However, the most common alloys that are used for castings of valves are carbon steel and stainless steels (such as grade 316/316L).
What are some of the general challenges associated with castings that one needs to be aware of?
There can be several different castings challenges depending on the particular valve or part being created, but in our experiences, we have found the following circumstances challenging:
• High resistance with less wall thickness
• Less weight
• Less machining
• Design flexibility
• Less cost, etc.
Are there any specific valves where the casting is more difficult?
Yes, however, it all depends on the type of valve being made, the requirements from the client, and what the end-use application will be for the valve. Generally speaking though, valves that have a lot of variation between wall thicknesses can be a challenge.
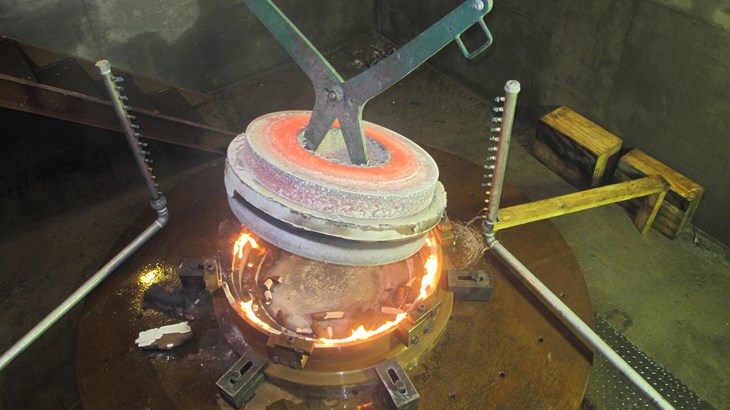
What are some of the end-use applications for valves made out of both common and speciality alloys?
To begin with, special alloys are most often utilized for end-use applications in severe service and/or highly corrosive environments because they can successfully perform within those complex situations. Oftentimes, cast steel valves are most often applied in the chemical & petrochemical, pulp and paper, and oil and gas industries among many others. Micromazza has its own foundry, Usimontec Sul, to produce sand casting parts. Please tell me about the location and what sand casting involves. Please also explain about centrifugal casting.
At Usimontec Sul, we produce pieces anywhere up to 1,350 kg in weight and we have approximately 70 employees who work in an area of more than 8,000 m². Sand casting is the process that occurs after the fabrication of the matrix (or model). The matrix is casted in sand and then this sand is mixed with chemicals. These chemicals coat the model and after five minutes the matrix is rendered extremely resistant. The matrix is then taken out of the sand, so the shape of the piece is molded, painted, and returned to the sand. Then the metal is inserted into the mold. It is a very intricate but important process.
The process of sand casting allows for the manufacture of larger sized parts compared to other casting processes, such as investment casting. Another benefit of sand casting is that it costs less than investment casting. Centrifugal casting is a process where the mold is consistently rotated. The liquid metal is then introduced and the centrifugal force, which surpasses approximately 70G (which is seventy times the force of gravity), forces the metal against the walls of the mold. The metal then solidifies under the homogeneous pressures, thus obtaining excellent mechanical characteristics.
By being cast under pressure (constant rotation), the metal solidifies, forming a perfect accommodation of the grains, which ultimately increases the life expectancy of the piece. This is because centrifugal casting gets rid of all gases and/or impurities that can cause wear and cavitation. The application of centrifugal force in the production of parts reduces the cost and simplifies the manufacturing at the same time. Just some of the valve parts that are created using this method include: Balls, sealing rings, etc.
What are the top three things that you would like to convey about castings and materials?
In our opinion, these three things are important:
1. On average, any particular casted part is made up of 50% molten steel with the other part being made up of 50% feed channels. This ensures there are absolutely no flaws.
2. Our sand is thermally calcined with liquefied petroleum gas (LPG), which greatly reduces the disposal of sand in landfills. Being environmentally conscious is very important to our company.
3. All of the parts we cast are molded with calcined sand. This means that the metal has no contact with ‘old’ sand and we also use zirconium filters in all of our parts to eliminate any possible metal impurities. We use MAGMASOFT® (a comprehensive optimization software tool for improving metal casting quality) to develop all of our parts.
Is there any aspect of the casting process that is a particular favorite?
We all enjoy it when the liquid metal enters into the mold, which is encased in sand, during the sand casting process.
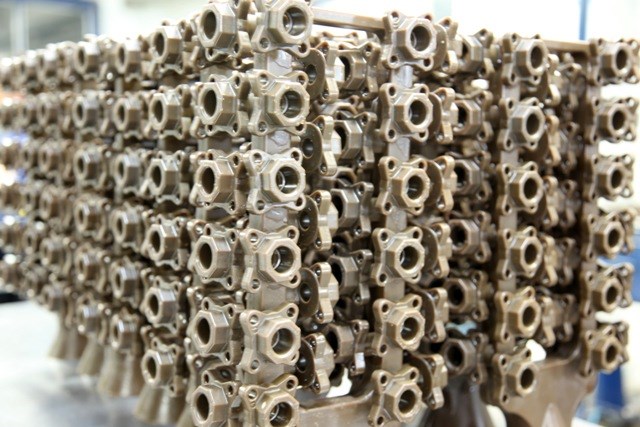
Testing and quality assurance
Micromazza is known for its high performance castings. How is quality maintained?
Just some of the ways we maintain quality with our casted parts are the following:
• 100% of the raw material is analyzed before it is used in the casting process
• 100% of castings are designed in MAGMA to help ensure quality
• 100% of the finished parts are inspected and go through a series of rigorous tests such as ultrasonic testing (UT) and magnetic/liquid penetrant testing.
What are some of the quality assurance processes like for the castings?
We perform many day-to-day tests including ones for resistance that test the tensile in the sand. In fact, there are six tests daily with three in the morning and three in the afternoon. Even before the metal is entered into the molds, its chemical composition is analyzed in the Spectometro. The piece is 100% analyzed with visual tests, ultrasound, magnetic particle, and liquid penetrant testing prior to being sent to the final customer.
Are there any particular challenges associated with the quality assurance process?
Our main challenge used to be manufacturing the parts free from porosities, cracks, etc. However, since investing in the MAGMA software, these challenges have been virtually eliminated.
Do different types of alloys need different quality assurance tests?
Yes, according to the specific material standard or customer specification, different tests are performed.
Depending on the type of valve and its end-use application are additional tests needed?
Sometimes, yes. In some cases, additional testing is ordered. This could be Eddy Current Testing (ECT), which is an electromagnetic testing method, and/or Radiography, which is an imaging technique that uses x-rays to view the internal structure of an object.
Please tell me about the Micromazza Technical Laboratory (LTM) and its role in the quality assurance process.
In the LTM, valve performance is analyzed thoroughly. The opening and closing valve is cycled by simulating actual operating conditions such as pressure, temperature, and torque.
What is the general quality assurance/testing process like for the casted valves?
Pressure tests are performed on the final valve product according to standards of tests such as API 598 and ISO 5208.
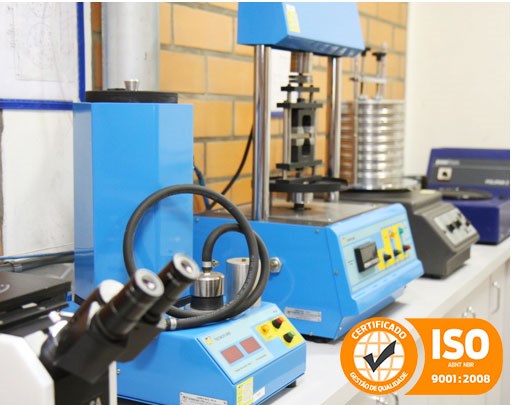
The two groups of metal casting
The casting process can generally be divided into two different groups: the hot forming process and the cold forming process. Both categories are described below with examples provided for each.
Hot forming process
This is a particular manufacturing process which is used to make use of suitable stresses (such as compression, tension, shear, or combined stresses) that cause plastic deformation of the materials to produce a required shape. This method really depends upon the nature of the product being cast. Examples of this process include:
• Centrifugal casting
• Extrusion
• Forging
• Full mold casting
• Investment casting
• Permanent or gravity die casting
• Plaster mold casting
• Sand casting
• Shell mold casting
Cold forming process
This is the process of forging metals at near room temperatures. In this method, metal is formed at high speed and high pressure into tool steel or carbide dies. The cold working of the metal increases the hardness, yield, and tensile strengths. Examples of this process include:
• Squeeze casting
• Pressure die casting
• Gravity die
• Casting
• Burnishing
• Coining
• Cold forging
• Hubbing
• Impact extrusion
• Peening
• Sizing
• Threat rolling