Stainless steels have become indispensable in the semiconductor industry, because the special material properties of these alloys can be perfectly tailored to the requirements of semiconductor production. Therefore, highly corrosive gasses and liquids used in the manufacture of semiconductors require tubing and other wetted 316L stainless steel components to be finished with the maximum degree of corrosion resistance.
By Robert McIlvaine, President & Founder, The McIlvaine Company
The cleaner the inner surface of an Ultra High Purity (UHP) system that comes into contact with the media, the better the evacuation and flushing properties. This can significantly reduce the process times with associated cost savings.
Electropolished UHP stainless steel surfaces allow the creation of highly pure and corrosion-free surfaces and weld seams which leads to low-particulate contamination. Stainless steel is used in semiconductor air, water, energy (AWE) process and discrete applications. The process applications are related to the quantity of ultrapure water utilized.
Water scarcities in Arizona, Taiwan, China, and many locations where new semiconductor plants are being built, have underscored the need for water conservation. Another dimension is that water reuse may be cheaper than bringing surface water to the ultrapure level. In industrial areas there are a number of contaminants, which present a challenge. In agricultural areas, water quality can vary considerably due to potential fertilizer contamination.
Water strategy has evolved from the original once-through concept – the principle is now to reuse, which includes treating waste streams separately. Those needing moderate treatment are subject to different processes than those needing extensive treatment. Today, about 40% of the initial water extracted is treated and reused, however the percentage is steadily climbing.
Gradiant has a unique reverse osmosis approach and is targeting 98% reuse. Ovivo has found that reuse is the most economical option when the quality of incoming water varies. Four million gallons of water can be used per day in a 200 mm wafer plant. This increases to up to 10 million gpd in a fabrication using 300 mm wafers. As the linewidths are reduced there is more on a chip which needs to be treated and therefore more water needs to be used. It is also important to take into account the need for greater and greater water purity as the linewidth shrinks.
In terms of flow quantity and stainless AWE product investment, what is important is the quantity of water being circulated, and not the quantity entering or leaving the plant.
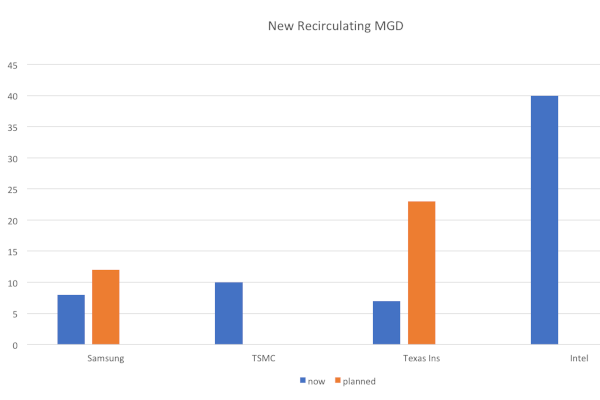
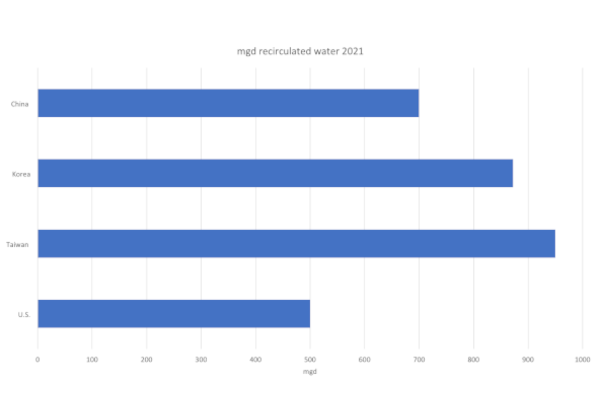
Fabrication Projects and Water Requirements
In the U.S., there are a number of new fabrication projects which will require increases in recirculation of more than 100 million gallons per day (mgd). Intel alone will be adding 40 mgd.
Figure 1 covers projects underway, and those where sites have been chosen but no final commitment has been made. This table only includes major projects. The U.S. is presently behind three other countries in terms of recirculated fabrication mgd. The recently enacted CHIPS act will narrow the lead of others such as Taiwan, but there is a long way to go.
The semiconductor stainless steel market can be separated in two categories, process, and discrete. Water supply represents the biggest process use. The U.S. presently has 500 mgd of water recirculated at fabrication plants, compared to 950 mgd in Taiwan.
Treatment costs per mgd are very high in semiconductor applications. However, the quantities are modest when compared to other applications. A large municipal wastewater treatment plant may be treating more than 1000 mgd, or the entire fabrication recirculated mgd in Taiwan.
A 4000 MW coal fired power plant will be circulating as much as 1 million gallons per minute of FGD slurry or 1,440 mgd. The conclusion is that this a challenging but relatively small market for stainless steel. Nevertheless, it has been shown that the most profitable suppliers are ones who have obtained market leadership in high performance niches.¹
The semiconductor AWE stainless market is unique in that much of it consists of small diameter AWE products used in discrete as opposed to process applications. Ultrapure water is used to wash chips and deliver various chemicals for chip treatment. A fabrication can require hundreds of tools. Various gases and liquids are used to treat each chip.
Therefore, a large numbers of hoses and couplings are needed for each tool, many of which incorporate stainless steel. Products from stainless steel include hoses, tubing, pumps, valves, and various pressure vessels. Additional uses of stainless steel include cleanroom tables and other devices which are made from 304, which has been electropolished.
Technology Development
The semiconductor industry is advancing at an unparalleled rate. Relevant stainless AWE products need to develop along with it. Four subject areas are:
- Product quality
- Energy consumption
- Water consumption
- Cost
Product quality: Ultrapure suppliers need to reduce contamination potential. Discrete suppliers need to keep improving insulation of hoses to insure keeping the needed temperature range.
Energy consumption: There can be thousands of stainless pipes or tubes, which if electropolished, reduce energy consumption.
Water consumption: Stainless AWE products play an integral role in water reuse systems which minimize total water consumed. The potential for a 98% reduction is dependent on additional loops with additional stainless products.
Cost: The potential is not to decrease purchased cost, but to decrease the total cost of ownership.
Stainless AWE product technology needs to develop at the same pace as the production technology. As the linewidth decreases, the damage from smaller particles increases. Many stainless AWE companies are members of SEMI and have direct contact with end users.
Semiconductors are a challenging and important market. The high growth rate and willingness of purchasers to pay for performance are attractive features.
References
- Stainless AWE Products: World Market published by the McIlvaine Company
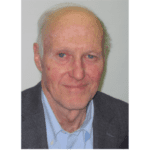