From a lifecycle perspective, stainless steel can often be considered a preferred option compared to competing materials, but there are large opportunities to strengthen this position further, with a focus on improving its production.
By Joachim von Schéele & Peter Samuelsson
Positive Properties
Stainless steel has inherent properties that makes it suitable in structural and infrastructural applications. Corrosion properties have historically been the main driver behind the use of stainless steels, along with hygienic and esthetical properties. In dynamic applications like transport tanks, maintenance and other corrosion related properties are important, as well as the mechanical properties that allow for lighter constructions, and thus higher payloads. In this type of application, the fuel consumption in use is a factor that contributes to the competitiveness of stainless steels from a sustainability and Life Cycle Analysis (LCA) perspective.
In “static” applications like buildings, bridges, and storage tanks, the maintenance cost is typically one of the drivers behind using stainless steel along with the mechanical properties that allow for weight reduction. Thus, stainless uses less material to achieve the same functionality as alternative materials. The maintenance costs usually relate to the corrosion properties, i.e., less need for corrosion protection and longer service time. The energy consumption in use, or LCA, is normally not influenced by using stainless steels in these applications. Therefore, the Green House Gas (GHG) inventory from raw materials, steelmaking and manufacturing processes are important to consider.
The recycling rate of stainless steel is usually quite high, largely driven by the intrinsic value of “end of life” stainless steel products. The collection of scrap and sorting according to alloy content is paramount in retaining the intrinsic value of the alloying elements. The obvious risk is that valuable alloy atoms are lost due to dilution if the categorization and sorting of scrap is not up to the task. This is naturally something that will require attention from all actors in the value chain, from collecting end of life scrap all the way to the melting furnaces.1,2
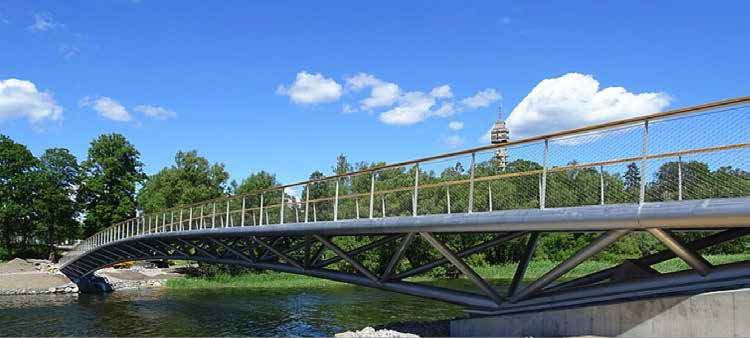
The Importance of Scope 3
Due to the increase in consumption of stainless steel, and thus the production, there will be a need to use relatively pure iron units and primary alloys in the charge mix. There was simply less stainless steel produced about 40-50 years ago, which could now be recycled in the form of scrap, and, therefore, we will have to make up the balance with iron and primary alloys. This requires special attention concerning so-called Scope 3 emissions, i.e., emissions generated in the upstream production of these input materials.
The GHG inventory of the primary alloys, like nickel, molybdenum, and chromium, could be substantial. Not only are these valuable alloying atoms traded in different forms, like electrolytic nickel, FeNi, Nickel Pig Iron (NPI), FeMo, Mo-oxide, etc., but the impact of their respective production varies greatly. There are many aspects to consider when it comes to the GHG inventory of the primary alloys.3,4 This is not limited to the influence of the metallurgical extraction process where the alloy is produced from its ores, but impacted also by the ore type, as well as the kind of energy used in the process from mining to alloying material ready to use in steelmaking operations.
In steelmaking operations, besides the choice of raw materials, there are issues with efficiency, such as energy consumption, yield to consider, and how it is influenced by the process technology employed. Yet another key factor is the source of energy, be it fossil fuels, or energy from renewable sources. These are some of the factors to consider when evaluating the GHG emissions from the steelmaking operations, and therefore its sustainability.
The reduction of GHG emissions will be an important consideration for many years to come. Today, we already see applications that have the potential to exploit the benefits of stainless steel. In the automotive industry, the transformation to Battery Electric Vehicle (BEV) will provide opportunities for an increased use of stainless steels, due to their mechanical properties, and tensile strength, as studied in the project “Next Generation Vehicle: Stainless Steels for automotive lightweight applications.” 5
Cathode material for fuel-cells is already today being produced from stainless steel and could very well also increase the demand for stainless steels in the future. Moreover, to produce the hydrogen needed for fuel cells, stainless steels will be an important construction material in the design of electrolyzers, where high temperature stainless steels could also be of interest.
Improving EAF, AOD, Preheating, and Reheating
Short-term approaches to decarbonization are focused on improvements and minor alterations. However, any technology change today should take the future into account, e.g., being ready for the use of hydrogen. Increase of energy-efficiency immediately reduces carbon footprint, and there are four processes to address: the electric arc furnace (EAF); the AOD converter; ladle preheating; and reheating and annealing.
Using Green Power – based on renewable energy sources – is an obvious step that can be taken wherever possible. The biggest consumer of electricity are the EAFs. However, there is also additional energy input to consider, which supports melting and refining using oxyfuel burners and injection lances. The CoJet technology was introduced by Linde 25 years ago, and has revolutionized EAF operation. Today, more than 170 EAFs are using CoJet.
The AOD process was invented by Linde already back in 1954 and is today used for more than 75% of the world’s stainless steel production. An example of such a system is IRS (Intelligent Refining System), which was introduced in 1995 and is successfully in operation at more than 100 AOD converters, ranging from 3 tonnes to 120 tonnes and found across 12 countries. The improvement in AOD process efficiency and productivity results in a lower tap to tap time and a lower carbon footprint. 6
To achieve preheating and reheating with a low carbon footprint – and ultimately bring it to zero – the first step is to increase the energy-efficiency. Flameless Oxyfuel has demonstrated the ability to reduce the fossil fuel consumption in ladle preheating and reheat furnaces by 20-60%; it is a well-established solution, which already has led to considerable decarbonization. 7
Ladle preheating using Flameless Oxyfuel achieves shorter heating times, lower NOx emissions, more uniformly heated ladles, longer ladle life, and – if wanted – to higher preheating temperatures. Partial or full conversion of reheat furnaces from air-fuel to Flameless Oxyfuel combustion is not only a relatively easy first step to decarbonization, but it also prepares the furnace for subsequent hydrogen fuels.

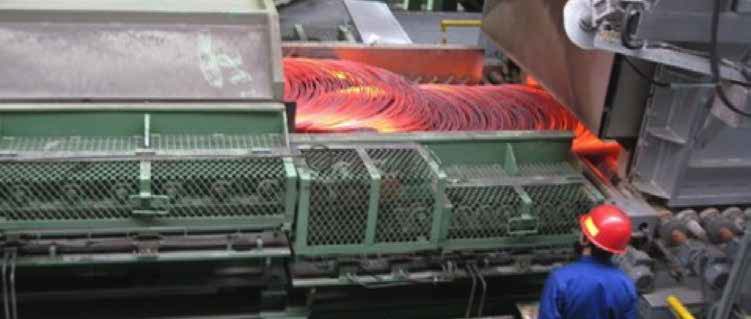

Hydrogen Combustion For Net Zero
The next step is to make the equipment hydrogen-ready and pave the way for replacing natural gas with hydrogen when a viable supply is available. It was concluded from tests that with hydrogen as fuel, the longest jets are produced, and the scrap melting is enhanced.
Based on a positive outcome from pilot tests, engineering steel producer Ovako and Linde decided to make a full-scale demonstration of hydrogen-hydrogen reheating in a soaking pit furnace at Ovako’s Hofors mill in Sweden. This the world’s first heating of steel with 100% hydrogen as fuel was carried out in March 2020 with 25 tonnes of ball-bearing steel ingots. The pit furnace was fired with hydrogen-oxy-fuel using REBOX Hyox. After heating and soaking, the ingots were successfully rolled to bars in the rolling mill. Rolling forces, dimensions, scale losses and temperature uniformity were at the same high level of quality as always. A thorough inspection and analysis of the final bars showed that heating using hydrogen as fuel does not impact the quality. A permanent full-scale installation of REBOX Hyox at Ovako Hofors is planned for 2023, where both the oxygen and the hydrogen will be produced using renewable energy. 8
Certainly, the coming years will bring about an exciting development to further the manufacturing and use of sustainable stainless steel.
References
1. Berlin D., Feldmann A., Nuur C. Supply network collaborations in a circular economy: A case study of Swedish steel recycling. Resources, Conservation and Recycling. 179
(2022). https://doi.org/10.1016/j.resconrec.2021.106112.
2. Compañero, R.J., Feldmann, A. & Tilliander, A. Circular Steel: How Information and Actor Incentives Impact the Recyclability of Scrap. J. Sustain. Metall. 7, 1654–1670 (2021). https://doi.org/10.1007/s40831-021-00436-1
3. Wei, W.; Samuelsson, P.B.; Tilliander, A.; Gyllenram, R.; Jönsson, P.G. Energy Consumption and Greenhouse Gas Emissions of Nickel Products. Energies. 13, 5664 (2020) https://doi.org/10.3390/en13215664
4. Wei, W., Samuelsson, P.B., Tilliander, A. et al. Energy Consumption and Greenhouse Gas Emissions During Ferromolybdenum Production. J. Sustain. Metall. 6, 103–112 (2020). https://doi.org/10.1007/s40831-019-00260-8
5. NGV, 2009 ”Next Generation Vehicle: Stainless Steels for automotive lightweight applications”, https://www. worldstainless.org/Files/issf/non-image-files/PDF/00_-_ Next_Generation_Vehicle.pdf, downloaded 2022-05-09
6. von Schéele, J., Alshawarghi, H., Razzari, D. Technologies Paving the Way to Carbon Neutral Stainless Steel Production. 11th European Stainless Steel Conference Science & Market and the 7th European Duplex Stainless Steel Conference & Exhibition, June 15-17, 2022. Bardolino, Verona, Italy.
7. Mathur P.C., von Schéele J. Decarbonizing Solutions for Steel. Steel Times International, April 2021, 35-39.
8. von Schéele, J. Advancing Use of Hydrogen as Fuel in Steelmaking. Millenium Steel, May, 2022, 20-22.