There are many precautions that need to be considered when welding duplex stainless steels. One of the biggest concerns is ensuring a proper ferrite to austenite phase balance. Several aspects will affect the phase balance of the weld metal and heat affected zone (HAZ) of a duplex stainless-steel weldment. Some items of extreme importance to consider are the filler metal composition, thermal cycle during welding, and welding technique.
By Steven Zamantakis, Welding Engineer, Chromalox
The standard duplex stainless steel welding procedure qualification took place to qualify welding ASME P10H material using the GTAW process. The required codes and specifications were ASME Section IX, ASME Section VIII-1 (for impact testing), API Recommended practice 582, along with other customer requirements.
The material chosen was 2205 standard duplex stainless steel. The procedure qualification was performed on SA-790 S32205 8-inch schedule 40 pipe that was machined down to 1/4-inch and was provided in the solution aninch. Filler metal ER2209 was used for welding. The joint design was an open root single v groove with a 100% argon back purge.
Filler metal selection
The chemical composition of the selected filler metal will have a significant impact on the ferrite to austenite ratio in the weld metal. Rapid cooling of duplex stainless steels, which occurs during welding, assists in the retention of ferrite.
To help prevent excessive retention of ferrite, filler metals typically have a higher nickel content relative to their matching base metal. Since nickel is an austenite promoting element, higher amounts are intentionally added to dunealed and water quenched condition. The pipe was machined down to 1/4-inch to qualify the welding procedure down to the desired plex stainless steel filler metals to promote the formation of austenite in the weld metal. The filler metal used for this qualification had a nickel percentage of 8.59, while the base metal had a nickel percentage of 5.21.
Nitrogen also plays a key role in the formation of austenite. It is also an austenite-promoting element, so additions of it will help assist in the formation of austenite during cooling. Nitrogen also helps lower the effective quench temperature, which allows more time for austenite to form during cooling. Together, nickel and nitrogen reduce the chromium equivalent to nickel equivalent ratio, which allows austenite to start forming at higher temperatures after weld solidification. While ASME SFA-5.9 requires the nitrogen content of ER2209 to be between 0.08-0.20 wt.%, the customer specification required the filler metal to obtain a content of 0.14-0.20 wt.% nitrogen.
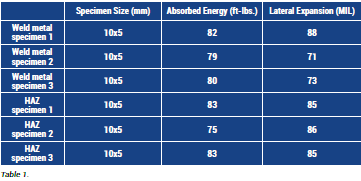
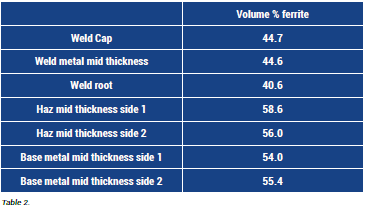
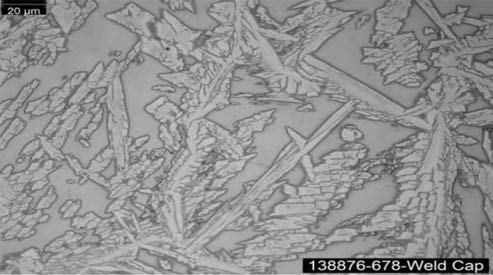
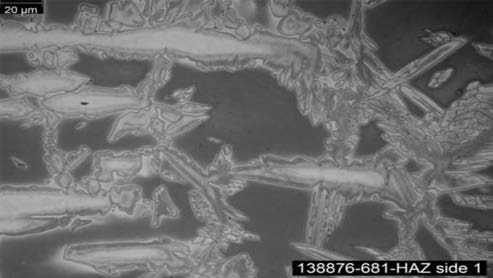
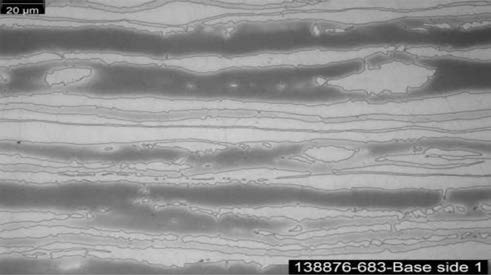
Thermal cycle
To control the thermal cycle during welding, the heat input and the interpass temperature need to be regulated. Welding began at the ambient air temperature, which was 70°F. Controlling the welding heat input and interpass temperature helps to control the cooling rate of the weld metal and the HAZ and helps ensure a proper phase balance. The heat input and interpass temperature must also have limitations to reduce the possibility of undesirable precipitates forming. One technique used during this input used during the root pass. This reduces the time the root pass weld metal spends in the temperature range the precipitates form at.
Welding technique
The root pass of a duplex stainless steel weldment is one area where welding technique has a large influence on the ferrite to austenite phase balance. Since this is the first pass of the weldment, a higher amount of base metal dilution can take place. If no precautions are taken, this could result in a high percent of ferrite in the root pass. Corrosion resistance can also be impaired by this. The root weld will come in direct contact with the process fluid, so corrosion resistance cannot afford to be compromised. To help overcome this, a substantial amount of filler metal needs to be added during the root pass. This helps limit dilution and balance out the percent of base metal versus filler metal present. Subsequent passes do not have this same concern because they will have dilution from the base metal and the previously deposited filler metal.
Other considerations
It is also important to note that SA-790 UNS S32205 was selected for the base metal instead of the alternative UNS S31803. UNS S32205 requires a higher minimum nitrogen content than S31803. For comparison, ASME Section II Part A allows UNS S31803 to have 0.06 wt.% less nitrogen than UNS 32205. The higher nitrogen content has a positive effect on the microstructure of the HAZ, as it does on the weld metal, and contributes to pitting resistance. UNS S32205 also qualification to prevent the formation of these precipitates was to limit the heat input during the second pass, or ‘hot pass’, to 75% of the heat is required to have a higher minimum chromium and molybdenum content than UNS S31803, which contributes to pittance resistance as well.
To help confirm that the proper microstructure was being formed in the weld metal during the welding process, a Fischer Feritescope was used to measure the ferrite content of the root pass and hot pass after they each had cooled down to room temperature. The microstructure will change in each pass after subsequent passes are welded due to the formation of secondary austenite. This was done just to be confident that the ferrite was in a suitable range. The results are based on an average of 10 readings for each pass and are as follows:
Ferrite percentage of root pass: 51.23%
Ferrite percentage of hot pass: 49.76%
Destructive testing
Along with ASME Section IX requirements of tensile and bend test, due to the minimum design temperature that the product will see, impact testing (CVN) was also conducted. Additional testing included hardness and ferrite testing.
Impact testing was originally set to be performed at -40°F, but due to the width along the notch of the specimen being less than 80% of the nominal material thickness, a reduction in temperature was required by ASME Section VIII-1. Two sets of three impact specimens were tested at -48°F: one set for the weld metal and the other set for the HAZ. Results for the test can be seen in Table 1.
For ferrite testing, metallurgical cross-sections were polished and etched to clearly reveal the two-phase austenite/ferrite microstructure. The parent metal, weld metal, and HAZ were examined and photographed at 500X magnification to clearly discriminate between the constituent phases. Ferrite content was measured on the metallurgical cross section using the manual point count method per ASTM E562. Microphotographs can be seen in Figures 1 through 3. Volume percent ferrite results are listed in Table 2. Hardness values were obtained using the 10kg Vickers (HV10) per ASTM E92 with locations complying with NACE MR0103/MR0175 and ISO 9015-1. Three hardness traverses were conducted, which results in 12 base metal, 10 weld metal, and 22 HAZ indentations. The highest hardness came from the middle of the weld metal and resulted in 288 HV10. The hardest HAZ value was 273 HV10 and the hardest base metal value was 271 HV10. The maximum allowed hardness was 320 HV10.
Conclusion
To conclude, duplex stainless steels can be successfully welded and will perform as intended intended in service when proper procedures are set in place. Phase balance (although not the only concern) should always be a key concern. Impact toughness, hardness, and corrosion resistance are all affected by the ferrite to austenite phase balance. With careful consideration of the filler metal, base metal, thermal cycle during welding, and welding technique the phase balance can be properly controlled during welding.
About the author
Steven Zamantakis was born and raised in Price, Utah. He started his college education at Utah State University and then transferred to Weber State University where he received a Bachelor’s degree in Welding Engineering Technology. Zamantakis began his professional career as a welding engineer at Chromalox in Ogden, Utah, and continues to work there at this time. He obtains the credentials of an AWS CWI, ASNT ACCP Level II VT (GI; PE), and ASNT SNT-TC-1A Level II PT.