A machine shop in Finland uses machinability-improved 316L bar to boost cutting speeds and improve chip breakage. A fabricator of mechanical seals in Texas switches to a specially tailored 2205 grade of duplex stainless steel in hollow bar to triple turnaround times. These are just two examples of how a new and growing breed of optimized stainless steel grades is helping component makers across the globe boost productivity and service.
By Henrik Zettergren, Global Product Manager, Sandvik Materials Technology
Less Machining, More Output
“We are talking about machinability improved stainless steels that are optimized by steelmakers to increase productivity in the cutting industry,” said Marcus Hillbom, Technical Marketing Manager at Sandvik. “After the first waves of COVID, as the economy picks up and order back-logs grow, we are seeing a growing hunger for smarter ways to reduce tool wear, increase cutting speeds, and drive down costs per article produced. Now, it seems that all OEMs and fabricators are in a big hurry to get their parts delivered on time, on budget, on spec, and of course, with the highest precision quality.”
Optimized Bar and Hollow Bar
According to Hillbom, one of the highest priorities is the need for faster turn-arounds. Clearly, the cutting industry is in a rush to catch up with demand. This is where machinability improved stainless bar and hollow bar can play a decisive role. What exactly is meant by the word ‘machinability’ and how is it ‘improved?’ “If you ask a machine shop what they mean by ‘machinability,’ you will get many different answers. It all depends on what is most important for their particular application and process,” said Hillbom.
He continued: “For some, the crucial goal is extending tool life or producing more components at a faster rate. For others, it comes down to reducing the total cost of components or driving down labor costs. This can vary a lot by market and depends on the price of materials, labor situation and other factors. Ultimately, however, the goal is always to produce low-cost, precision CNC machined parts.”
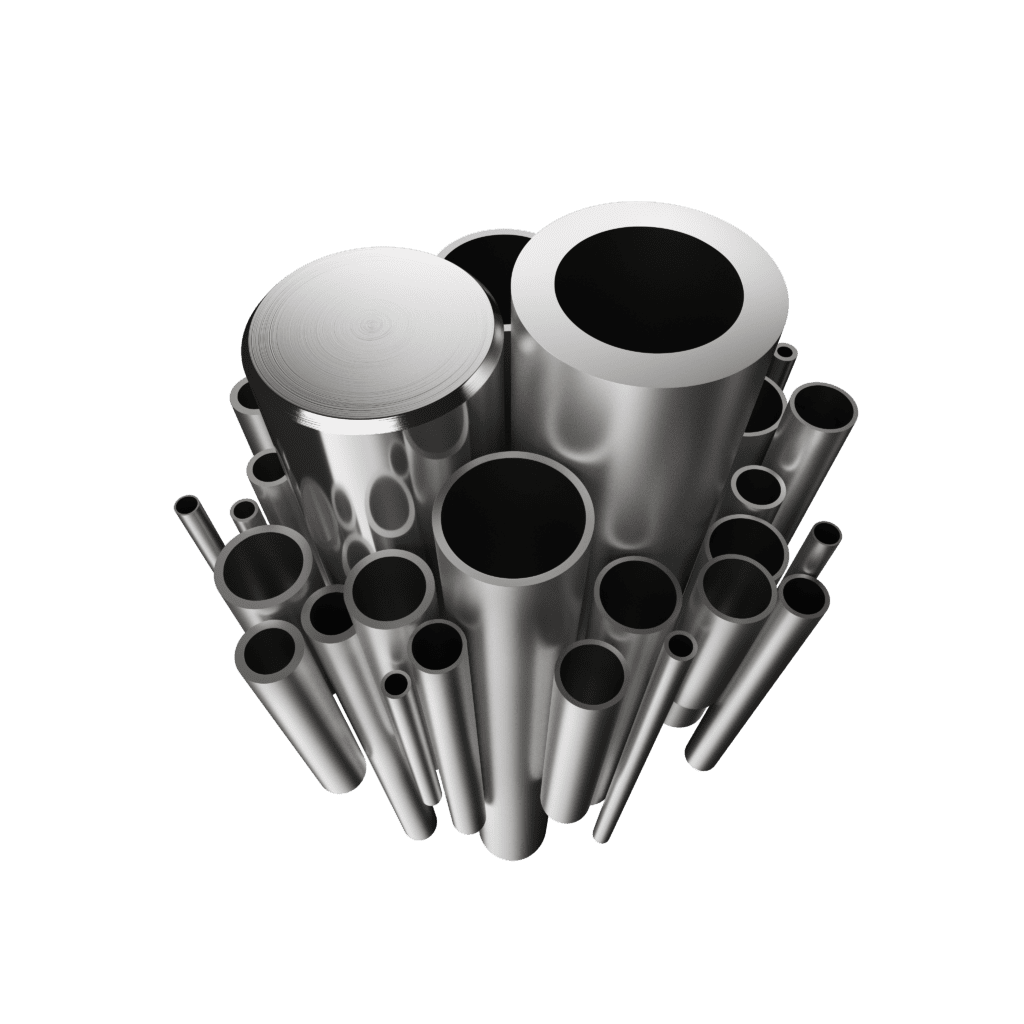
Machinability Defined
Simply stated, machinability is the ease with which a metal can be cut, permitting the removal of material with a satisfactory finish, at low cost. The challenge is that this can be a bit hard to predict due to wide-ranging variables, such as the condition of the work material or physical properties. Not to mention the type of CNC machine being used, cutting tool materials and geometries, speeds, temperatures, lubricants, and other factors. As a result, machinability gains are often evaluated on a case-by-case basis, depending on a specific manufacturing process.
Physical and Mechanical Considerations
Even within the given American Iron and Steel Institute (AISI) standards, the condition of the core material can vary – a clear signal that manufacturers would do well to evaluate whether their steelmaking supplier has full control of all quality steps in production. Do they run an integrated steelmaking process to ensure consistency of material, from batch to batch, and from melt to final product? Sandvik cites eight key factors when it comes to physical properties, including:
- Microstructure – ensuring it is even throughout the material.
- Grain size – should be fine and even. Heat treatment – controlled and short time to quench.
- Chemical composition – kept tight to ensure repeatability from batch to batch.
- Fabrication – qualified and audited by third parties.
- Hardness – in line with NACE requirements.
- Impact strength – sufficient to cope with higher demands for critical components.
- Tensile strength – high ductility to meet end user demands.
On top of this, and relating to individual material groups, mechanical factors need to be considered, including:
- Modulus of elasticity
- Thermal conductivity
- Thermal expansion
- Work hardening
Stainless Machining Challenges
Several of these factors, such as work hardening, are of particular concern when machining high alloy stainless steels. Stainless steels are generally more challenging to machine, compared to regular carbon steels, as they are often tougher, gummier, and tend to work harden very rapidly. Such machining challenges are also closely related to the presence of higher nickel content and other tough alloying elements – the very elements that make these high-alloy steels so attractive for challenging corrosive, high-stress applications in the first place.
Work hardening means that as the material is machined, the surface strengthens, making it progressively harder to machine and dulling the cutting tools faster. Yet another key consideration is achieving appropriate chip breakage to avoid entanglement in the machinery.
Setting a Baseline for Machineability
So how can fabricators compare the relative ease (or hardness) of machining components using various stainless grades? Fortunately, AISI has developed a baseline standard based on a weighted average for a wide range of steel grades, including high-alloy stainless steels. They determined this by running turning tests at 180 surface ft/min (sfpm). The AISI then arbitrarily assigned 160 Brinell B-1112 (a cold-drawn EN19 steel) a machinability rating of 100% (see bar diagram).
Comparative Machinability Ratings
Consequently, steel grades with a material rating of less than 100% would be more difficult to machine than B-1112, while those with a higher value than 100% would be easier. Based on this rating system, AISI grades such as 303 and 304 are easier to machine than say a duplex like 2205, a 316L grade (not shown) or higher nickel alloys. All steels are then assigned a numerical rating that is a percentage of relative speed based on B-1112 as being 100%.
Average Tool Life: 7-10 Min
For stainless steels, a tool life of approximately 7 to 10 minutes. Naturally, any clever means of further extending this lifetime, by modifying the chemical composition within standards or other means, is of keen interest.
Making Stainless Steel More Machinable
Against this backdrop, it is not surprising that steel producers (and their customers) are increasingly on the look-out for better ways to make stainless steel more machinable. The ability to extend tool life, reduce complications, and produce more components at a lower price can give a fabricator a significant competitive advantage.
An Age-Old Quest
“The quest to make stainless steel more machinable has been going on for many years,” says Vinicius Martins, Business Development at Sandvik Materials Technology. “Back in the mid-20th century, metallurgists discovered adding small amounts of sulfur to the chemical composition had the effect of forming a lubrication layer on top of the cutting tool, reducing friction, and extending tool life. The impact was so favorable that many specialty steelmakers started making additions of sulfur and even sometimes phosphorous to grades like 303, 416, and 420.”
“Soon a problem arose,” continued Martins. “While sulfur and phosphorous had certain advantages, they also adversely impacted many of the positive properties of the stainless steel itself. For example, sulfur lowers the mechanical and corrosion properties and affects the microstructure in such a way that leads to brittleness during welding.”
Consequently, this metallurgical dilemma remained for many years – how does one produce a stainless steel with high corrosion resistance, superior mechanical strength, and good weldability, while also offering world-class machinability? In fact, it became something of the “Holy Grail” for R&D metallurgists in the last half of the 20th century, according to Martins.
That is, until an ingenious invention came along. Metallurgists at a leading global materials technology company found that by adding non-metallic inclusions to the material they could manipulate the grain boundaries in the microstructure to replace the high sulfur content and facilitate chip formation at a lower yield strength. In other words, they ended up with a material that had all the advantages of standard stainless steels, but with high machinability.
“The creation of this material was really a milestone for easier machining,” said Hillbom. “Quite simply, it was a smarter way to achieve high machinability by adding non-metallic inclusions. It has been around for a few decades now, but still plays an important role for the machining fabricators that are seeking to achieve the lowest cost per component.”
A Growing Trend
“This milestone by metallurgists opened the eyes to the whole industry and is just the start of a growing trend. Now the quest continues to optimize the machining properties across an even broader range of steel grades – from austenitic stainless steel to duplex and higher alloys,” said Hillbom. “Part of this focus is using non-metallic inclusions to ensure a fine grain and even microstructure throughout the material. This same thinking and some of the processes are now being used for both bar and hollow bar formats – an added plus.”
“The benefits to customers are pretty remarkable,” said Hillbom. “We have seen cases where customers had achieved both higher productivity, longer tool life, and better chip-breaking by using materials engineered with non-metallic inclusions!”
“In the future, I think we can expect to see a lot of innovative thinking in this area – new optimized grades across a broader and broader range of stainless-steel types,” he concluded.
About the Author
Henrik Zettergren is the Global Product Manager for Sandvik, based on interviews and independent research from Sandvik Materials Techno-logy and Sandvik Coromant. The holder of a Master’s Degree in Industrial Economy, Zettergren is an expert in logistics, organizational planning and strategic production. He joined Sandvik Materials Technology where he has spent more than 10 years in various key managerial and strategic roles. Currently, he is Global Product Manager for the Stainless Bar products where he oversees everything from sales, marketing and the product assortment to value-based selling, pricing, processes, and tools.
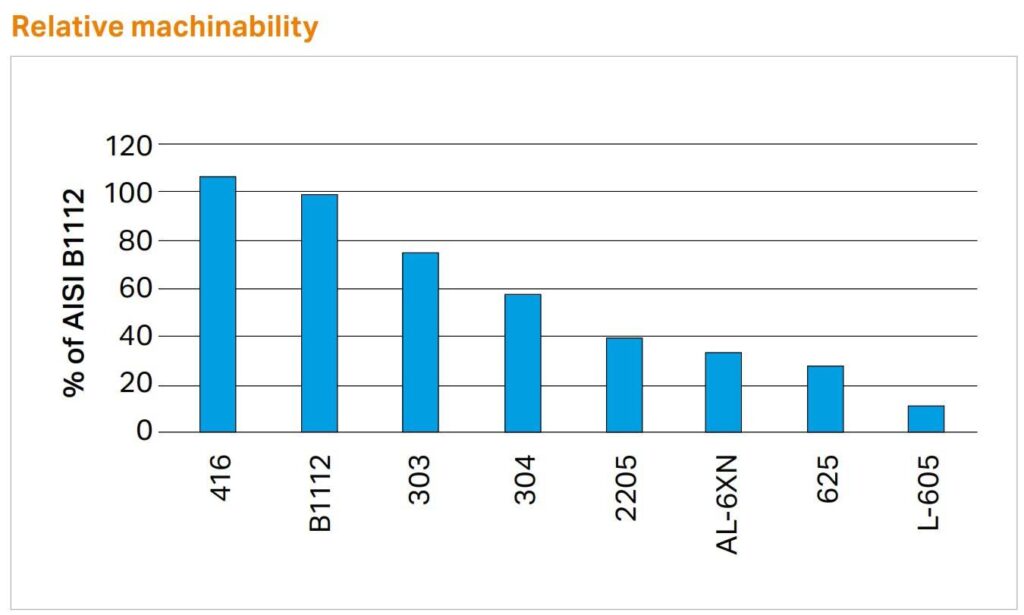