It can be easy to underestimate the role of a fastener. Oftentimes, an engineer’s main focus is on an application itself, such as a valve or hose. The fastener is, however, a crucial component because it connects and holds everything together. Ensuring that a fastener is meeting the quality standard for a specified application and environment is important for avoiding hazardous and dangerous situations.
As the Technical Lead Engineer at Auge Industrial, Justinn General explains to Stainless Steel World Americas the important points to keep in mind when dealing with fasteners, how standards and specifications for applications in the oil and gas industry are improving, and the importance of encouraging the younger generation to join the oil and gas industry.
By Catarina Muia and Brittani Schroeder
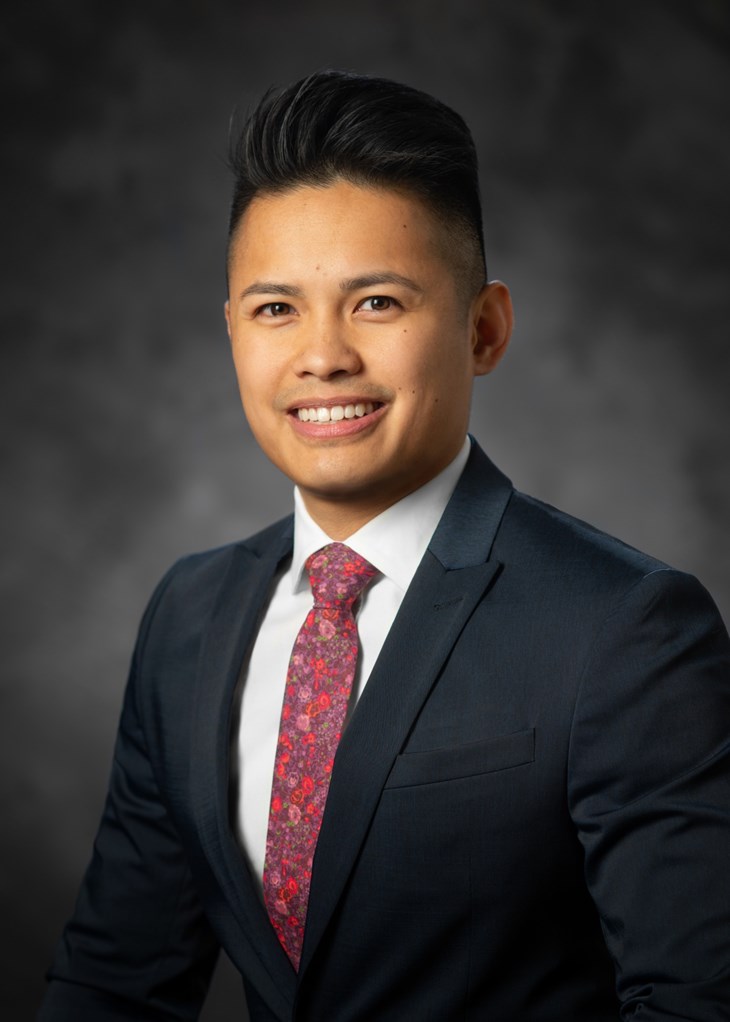
It all began when General first started college where he studied nuclear engineering. In his senior year, the Fukushima Daiichi nuclear disaster occurred, “it was a huge catastrophe in the industry; companies were not looking to hire nuclear engineers. Luckily for me, I was actually working at a material science laboratory, where I had the pleasure of working with one of my professors, who took me under his wing to become one of his students in the graduate program,” General recalls. Upon the completion of his Nuclear Engineering degree at Texas A&M in 2011, General continued to study Material Science, and obtained his second degree in 2013.
Fresh out of college, General began working at Rolled Alloys as the company’s Regional Metallurgist. The company specialized in the nickel and high-end alloys, which is why one of General’s specialties is looking into super-duplex and duplex lines. In this role, General would assist engineers. “If the engineers had any questions, they would refer to me. They would ask me how to procure a specific material, or where the best mills are, and it gave me a chance to gain technical experience.”
At the downturn of the oil and gas industry, General was laid off, but since he was engaged in the industry itself, he obtained a new position through one of the biggest organizations in Houston for metallurgist; the American Society for Metals (ASM). Currently, General is the Chair for of the organization. “One of my contacts from ASM, Dwight Janhoff with BP, was able to recommend me to Auge Industrial, which manufactures critical fasteners, and similar products,” General explains. “In my current role, I interact with many original equipment manufacturers (OEMs) and end-users regarding fasteners used in the oil and gas industry.”
While interacting with OEMs and end-users who are primarily in the upstream sector of the oil and gas industry, General’s main purpose is to be the technical front for Auge Industrial’s manufacturing and quality. “I am there to review customers’ specifications and projects, then communicate my findings to our manufacturing plant in order to meet the customer’s standards.”

Walking through General’s day
As a Technical Lead Engineer at Auge Industrial, General has plenty of responsibilities to keep him busy throughout the day. “My day can be broken down into two portions; the first is to be process centric, the second is manufacturing,” he explains. “In terms of being process centric, orders need to be processed and moved forward, and with so much going on, it is normal for issues and questions to arise. It is my responsibility to resolve specification issues, process new orders, determine which heat treatment to use for a specific product.
In regard to manufacturing, General needs to maintain great communication with the quality and engineering teams in order to maintain a functional relationship with his customer. “If there are any major quality dispositions, or if there is something wrong with the quality process, I am one of the first people to review it and give that disposition. I then have to decide whether or not we have to inform the customer, based on its impact on quality and delivery.”
Since General deals with high-pressure situations on a day-to-day basis, it is important for him to work well under stress. “I have a weird, love-hate relationship with stress. I think I need to be stressed out in order to say, ‘Hey, I have to get this done’; it is just how I am structured. In a strange way, the stress is my favorite part about the job,” he recalls smiling. “The stress proves to me that I really care about what I am doing.” As he oversees the engineering and quality of these fasteners that will be used in subsea projects, General knows there is no room for failure. “You have to either be perfect, or you fail. I will do everything I have to in order to ensure the items will be perfect. I have to be confident at the end of the day, when I make decisions for projects, I determine if an item passes or fails, then sign off on it.”
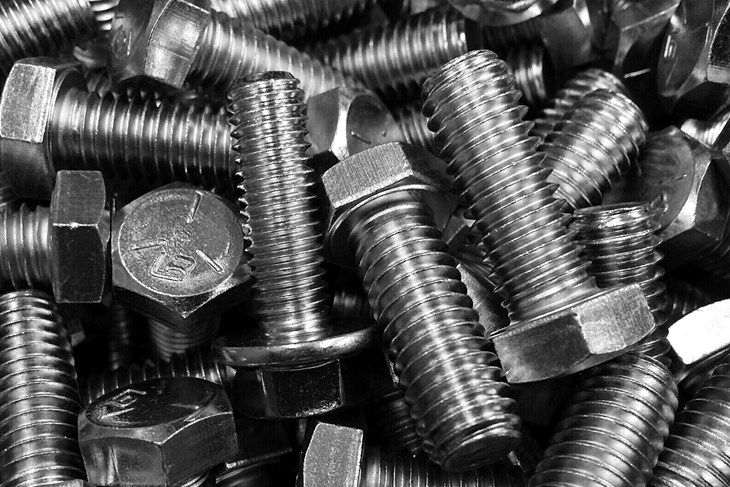
Testing for safety
Ensuring a fastener has been manufactured correctly for an application going through a specific process and environment is crucial. One problem General warns about is the inconsistency in quality when it comes to purchasing and using certain fasteners. A portion of oil and gas equipment uses fasteners in a subsea environment. If a leak is to occur and there is a loss of containment, there is both the environmental and safety aspect to deal with. Therefore, General stresses that each fastener must meet the proper specifications and quality standards to maintain safe operation in their respected environment.
In order to improve the quality of fasteners and further avoid containment issues, General explains that currently, Auge Industrial is working with the American Petroleum Institute (API) 20 committee. “The API has a multi-segment task group that is in charge of looking into different aspects of bolting, which is a topic that has seen a renewed interest,” General states.
The project can be broken into five major segments. “The first project, ‘Recommended Practice for Fasteners’, is to create an overall document tying together what we know, and what the industry understands. For example, what are the different grades we can use to make fasteners, and what are the specifications for each? This information then gives the industry a recommended practice of how to use each fastener with the appropriate application. In order to do this, the rest of the API committee is continually studying specific challenges that the fastener industry has faced,” General explains.
“The second part of the project was on ‘Coatings and Platings’ in specific environments, to understand whether or not being in these environments would cause an issue once in service.” The third project is ‘Hardness Limit’. “For hardness, you want to know how strong the material is because you need to understand what level of hardness is acceptable in certain environments,” General says. In a subsea environment certain levels of hardness can be susceptible to hydrogen cracking. “We need to know what the safety limit is for this material to operate at,” he continues. “It can be tricky though; if you punch hardness on a stud three times, you could get three different answers because of the variability in the hardness testing.” However, the fourth project focuses on the ‘Hardness Uncertainty’, which the committee is trying to fine-tune the hardness testing process. “When we do a hardness test, every time we punch it, we want the results to be pretty close. We want consistency.”
Finally, General explains the fifth project, which has the committee looking at how to better ‘Understand Nickel Alloys’, and the effect of thread rolling on the mechanical properties. “We roll thread nickel alloys to form them into the desired thread. To do so, we are adding cold work the material, which then makes it a lot harder. The problem we face is the lack of understanding for how much the cold work can affect a type of steel.”
The efforts made by the API committee, and companies such as Auge Industrial, are being implemented because the oil and gas industry does not want to continue to see failures. “The last thing you want to worry about is a fastener, and unfortunately, many people slot it as one of the lowest priorities because they believe it is a commodity. A fastener is not just a product that you can see and buy off the shelf, for this industry it is becoming an engineered product,” General urges. “We really want to change that perception. Each fastener needs to be made specifically with the correct quality controls, in order to ensure it will not fail.”
General and his colleague, Aldo Perez, Auge Industrial’s Business Development Director, predict these changes to the industry to take full effect in the next two to three years. “Currently, the testing is being done, and now people are beginning to use it, understand it, and are beginning to believe in it,” says Perez.
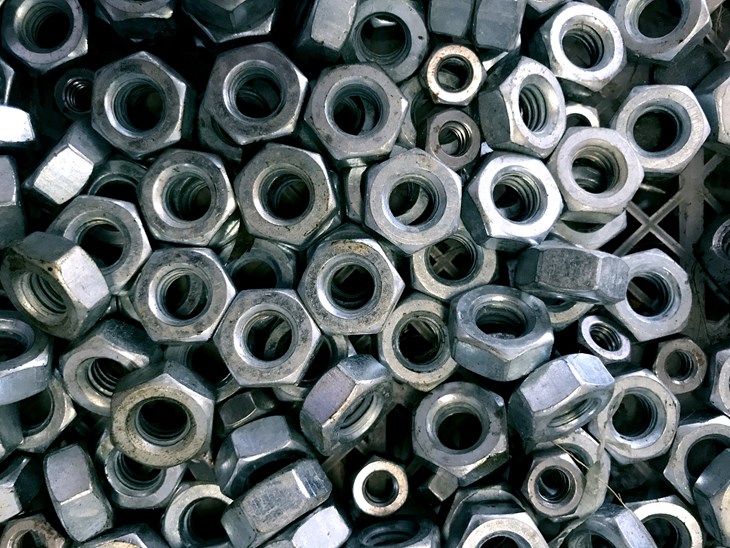
Materials and coating
While Auge Industrial typically uses alloy steels, General explains that the company will use the higher stainless and super-duplex stainless steels if a customer has requested it. “If someone has, for example, requested a 316 stainless steel valve, we have to ensure that the fastener will be made from the same, or similar metallics.” If metallics are mixed together that are dissimilar, the corrosion resistance can be affected. “Specifically, if you have a 625 Inconel valve, and then you pair it with carbon steel bolting, the studs and nuts are going to preferentially corrode.”
Once the materials have been selected, General explains that coating could be used to add protection to the application. Touching briefly on the topic, he says that the applications he deals with typically use Xylan® (fluoropolymer) or electroplated (i.e. zinc, zinc-nickel, etc.). “A zinc-nickel plating is used when the application needs to be more corrosion- resistant. While Xylan® adds some corrosion-resistance, it really helps with assembly. If you have ever heard Teflon or Xylan®, it is supposed to be ‘non-stick’. As this coating is non-stick and slippery, assembly is much easier. From there, it becomes simpler to dial exactly how much torque is needed on each specific bolt.”
Keeping the industry going
It is no secret that there is currently a wave of retirees in the oil and gas industry, and General believes that this movement will pose some challenges. “Being part of the API committees in the oil and gas industry, I see that between myself and others there is a pretty big age difference.”
Perez explains that currently, the biggest challenge is recruiting and keeping people in the oil and gas industry. “Nowadays it is close to impossible. What we need to start doing is show the younger generation that there is a huge opportunity for growth in a short amount of time,” he states. “If you have the ability to learn quickly, and you have an entrepreneurial spirit, this is the industry for you to take on leadership roles quickly.”