As the Senior Advisor of Subsea Control Systems at Chevron, Tanju splits his time between his office in Houston, Texas and being offshore. “Subsea is so fascinating because you can’t just go there and touch the equipment since it’s thousands of feet under the water,” says Tanju.
Protecting the pumps
Deep water pumps rely on a subsea control system to keep them operating. “Controls is very important because without the control system, a subsea pump is basically a big anchor,” explains Tanju. “The control system is what makes them work. As a controls engineer it is necessary to understand all types of pumps: Multiphase, single phase and gas compressor. Everything has to work with each other like a Swiss watch. Otherwise, you may lose your pump and retrieving a pump from deep water is very expensive because of the mobilization of the large intervention vessels.”
Because of the heavy costs associated with physically removing a pump from thousands of feet underwater, subsea operators take extra precautions to protect the subsea equipment. In order to avoid damage to the pump, there are several methods used. First, the pump controls system is designed so that there is minimal human interface.
“Up until now, the Human Machine Interface (HMI) would indicate an issue (alarm) and await operator action,” says Tanju. “However, when it comes to pumps, you do not have time. So now, the software takes immediate action in order to protect the pump, and then it tells you what it did after.”
“Up until now, the Human Machine Interface (HMI) would indicate an issue (alarm) and await operator action,” says Tanju. “However, when it comes to pumps, you do not have time. So now, the software takes immediate action in order to protect the pump, and then it tells you what it did after.”
Unique challenges of the subsea environment
Tanju lists time frames as one of the challenges when working on projects. For example, while he was working on a project in the Gulf of Mexico, there were several areas being developed at once, including the platform hull, subsea systems and topsides facilities. “At the end of two or three years, everything must come together. There is one target date that everyone is working towards, but that can be a challenge because until you get into a project, you do not know all the details. Not just for pumps, but for the system controlling the pumps.”
He has worked on another project that involved dual gradient drilling, where mud had to be pumped up from the seabed floor. He shares that one of the most challenging aspects in deep water was mitigating effects of hydrostatic pressure due to the seawater.
When pumping hydrocarbons in deep water, the low permeability of the reservoir causes pressure to fluctuate drastically. Pressure increases rapidly when you stop the pump or production, but decreases when you start the pump again. You are left with a wide range of pressure that the system must accommodate.
“We especially see these fluctuations at production start-up. When you isolate you have high pressure if you are not producing. However, once you do start production, the pressure goes down and there is rapid relief, but when you stop again it builds up.” It can therefore be challenging to design a pumping system that can handle the wide range of pressures. Tanju further explains that towards the end of field life, reservoir pressure naturally declines.
“We have tricks to increase the pressure. For example, you can inject water. Another method to help increase pressure in the deep water reservoir is to pump fluid at the mud line to the reservoir. Instead of producing from the reservoir you are putting water into the reservoir. All around the reservoir they drill wells and then flood it with water to push the hydrocarbons into the center, and then we produce from there.”
Protecting people, the environment and equipment
“For Chevron, safety is the most important thing—not only for the environment, but for the workers as well. For our pump system we implemented a secondary control system that monitors and reacts independently of the primary system in order to ensure protection of both the pumps and the environment. ”
Tanju explains that the two systems are completely segregated, including the programmable logic controllers (PLCs), instruments and electronics. If a fault condition is detected by either system, the pumps will be shut down. “This is in excess of the requirements for a typical subsea controls system.”
“For example, if a boarding valve closes, the system automatically isolates the pump. We design our valve control to react faster than any transient reaching the pump. Another example, if the operator opens up a chemical injection valve by mistake, the system is capable of closing the valve if the pressure is increasing toward damaging levels. It predicts the problem ahead of time and it closes the valve.”
When it comes to qualifying products, Chevron doesn’t do internal testing, but they require vendors to do certain tests to demonstrate suitability for the application. Vendors themselves also need to be approved, along with any sub vendors. Chevron also requires a quality control (QC) witness be present for all testing.
“We qualify a lot of technologies for subsea. One of the important ones was a coupler for deep water which would not allow leakage out, but which also would not allow seawater into the circuit. It was not a new technology, but it was new for deep water.”
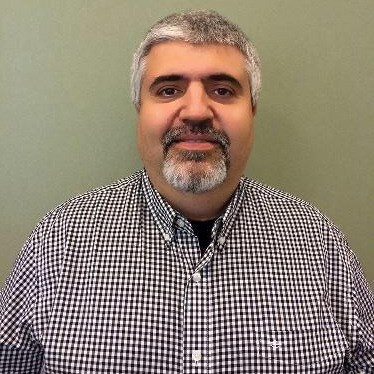
New barrier fluid technologies
Tanju is involved in developing new technologies for barrier fluid delivery and control, which is used to cool the motor and protect the mechanical seal. He explains it is very important to control barrier fluid pressure subsea to maintain it slightly higher than the production pressure. This is especially important for high pressure, deep water, long distance step out and low permeability reservoirs, because the wide range of operating pressures does not allow you to adequately regulate the topside barrier fluid power unit output fast enough. The rapid movement of fluid is limited due to the friction and umbilical length.
“You cannot allow production fluid to leak into the motor because it will contaminate mechanical seal surfaces, damaging it, and potentially lead to motor failure. That is why you maintain higher pressure on the barrier fluid system at the pump. When the pump is not operating, the pressure inside of the pump is high, but your barrier fluid pressure has to be slightly higher than that to leak into the production. Because of the low permeability of the deep water reservoirs, when you start the pump, the production pressure goes down. The barrier fluid control system must adjust the pressure inside of your motor to follow the decreasing production pressure, otherwise increased differential pressure may damage the mechanical seal.”
Harsh subsea environments require special materials for equipment
Chevron has material science subject matter experts within the company. “Welding, exotic materials and cathodic protection are all big areas for subsea material science that must be taken into account in designing and deploying technology subsea. Even though all the numbers are correct according to the specifications, with cathodic protection you have to consider shadowing effect, which is a big issue in subsea. Shadowing is when you put something in a can, for example, and put a lid on it—you are only protecting the outside of the material, not what’s inside. So with subsea, even though you put a bunch of anodes, it may be shadowed from the anodes.”
Tanju recalls an experience he had with drilling systems, where a high quality stainless steel was affected by shadowing. “When we took it out from the deep water, about 7,000 feet, inside the ring looked like it was eaten by a worm. At the time, I thought an animal must have done this. It looked really interesting. But really, that was the shadowing effect that had occurred because the ring inside didn’t get enough benefit from cathodic protection.”
Eventually we fixed the problem by inserting a small anode inside of the ring, which creates a positive charge so that the electrons aren’t removed from the surface of the metal, thus protecting the metal from corrosion.
Future of the pump industry
Tanju shares his thoughts about the future of subsea processing. “I’ve seen the technology evolve over the years. Right now we have subsea deep water single phase pumps. In the future, we will see applications for multi-phase pumps, as well as wet-gas compressors. Ultimately, I think that the industry is going towards subsea processing, moving more of the pumping, compression and separation equipment from the topside facility to the seabed.”
He mentions that this technology is not being used yet for deep water, but there are deployments in shallower water such as the North Sea. Several companies are developing equipment for deep water. “You separate out gas and water. Then, you can produce either oil or gas. Whatever you do not want to produce, water and/or gas, you inject back into the reservoir. It saves space on the topside. Smaller floating production units are key for the future.”
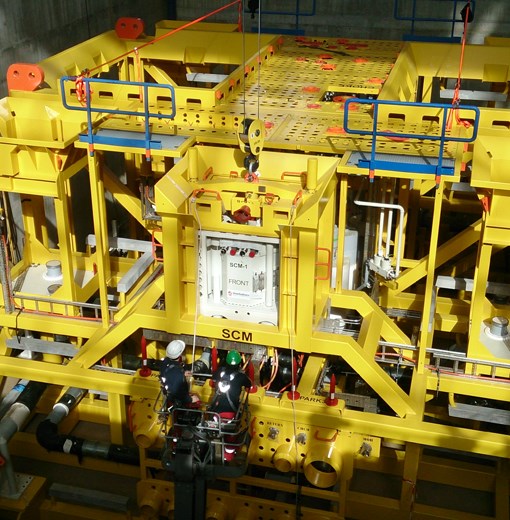
All photos: Courtesy of Schlumberger; © Copyright 2016 Schlumberger