Dunn Heat Exchangers is a family-owned company with over 50 years of experience. Offering a wide variety of heat exchanger cleaning, repair, and fabrication, the company has made a name for itself in the industry, with the capacity to get equipment back in service quickly.
Stainless Steel World Americas spoke to Pete Dunn Jr., Dunn Heat Exchangers’ Director of Sales, to learn more about its commitment to being a quality service company, its safety promise, and its ability to efficiently clean industrial heat exchangers off-site.
By Sara Mathov
Family History – The Beginning of Dunn Heat Exchangers
Dunn Heat Exchangers goes back to 1936, when Pete’s great grandfather took out a loan for his father, to start a gas station in Galveston, TX. From there, he began to rent equipment, primarily to service a port, using a lot of large air compressors for ships, which were steam driven at the time. “When coming into port, the ships would shut their boilers down, however, they still needed something to power their pumps and other components,” explained Pete. “We started renting to them, and from there realized that chemical plants and refineries need a lot more air compressors than ships do. That is how we got into the industrial sector.”
From there, Pete’s grandfather saw heat exchangers passing by on trucks. After wondering what these were and learning they are being sent across the state to be repaired, he volunteered to help out. “He was able to start a business in building, servicing, and maintaining heat exchangers, over 54 years ago.”
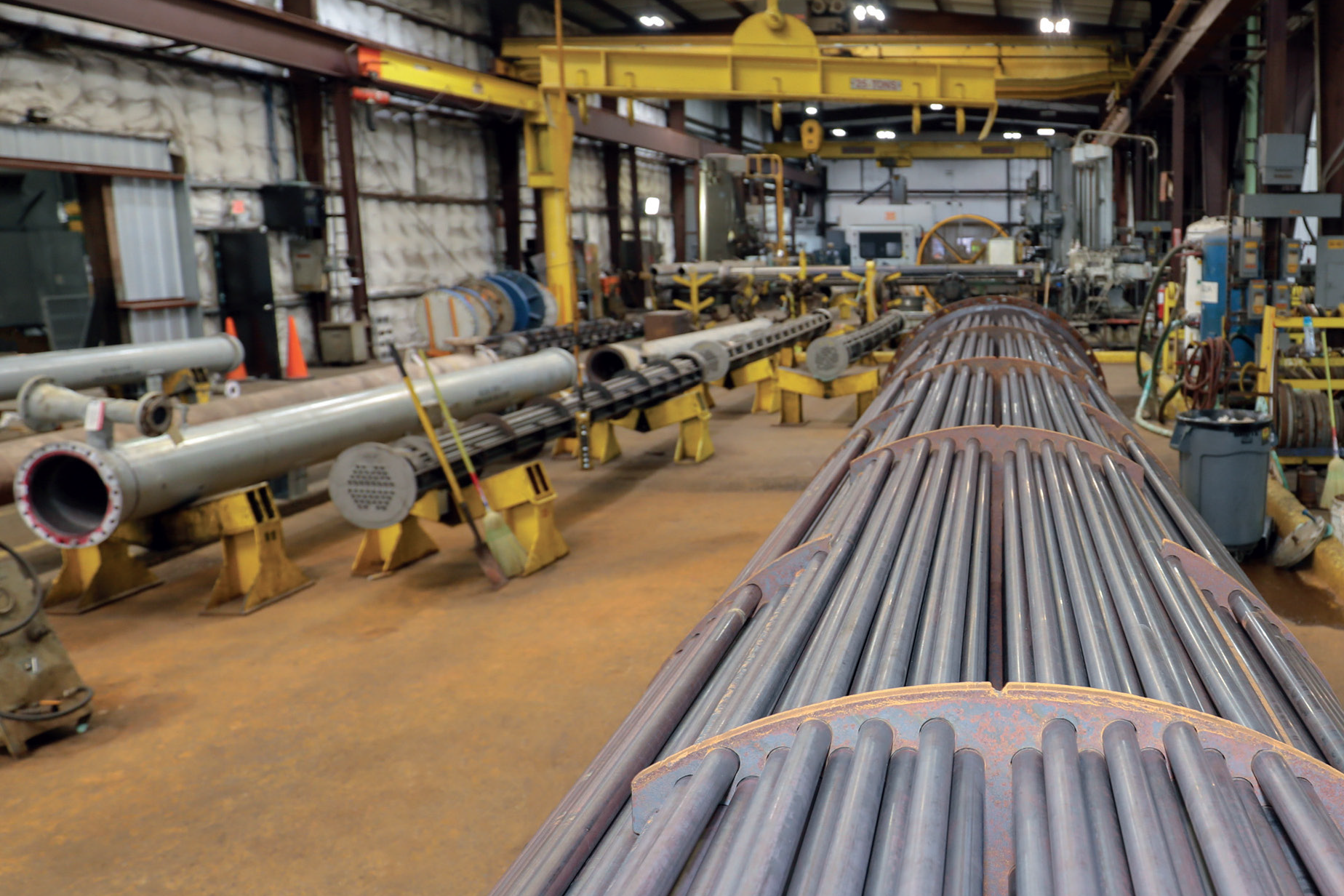
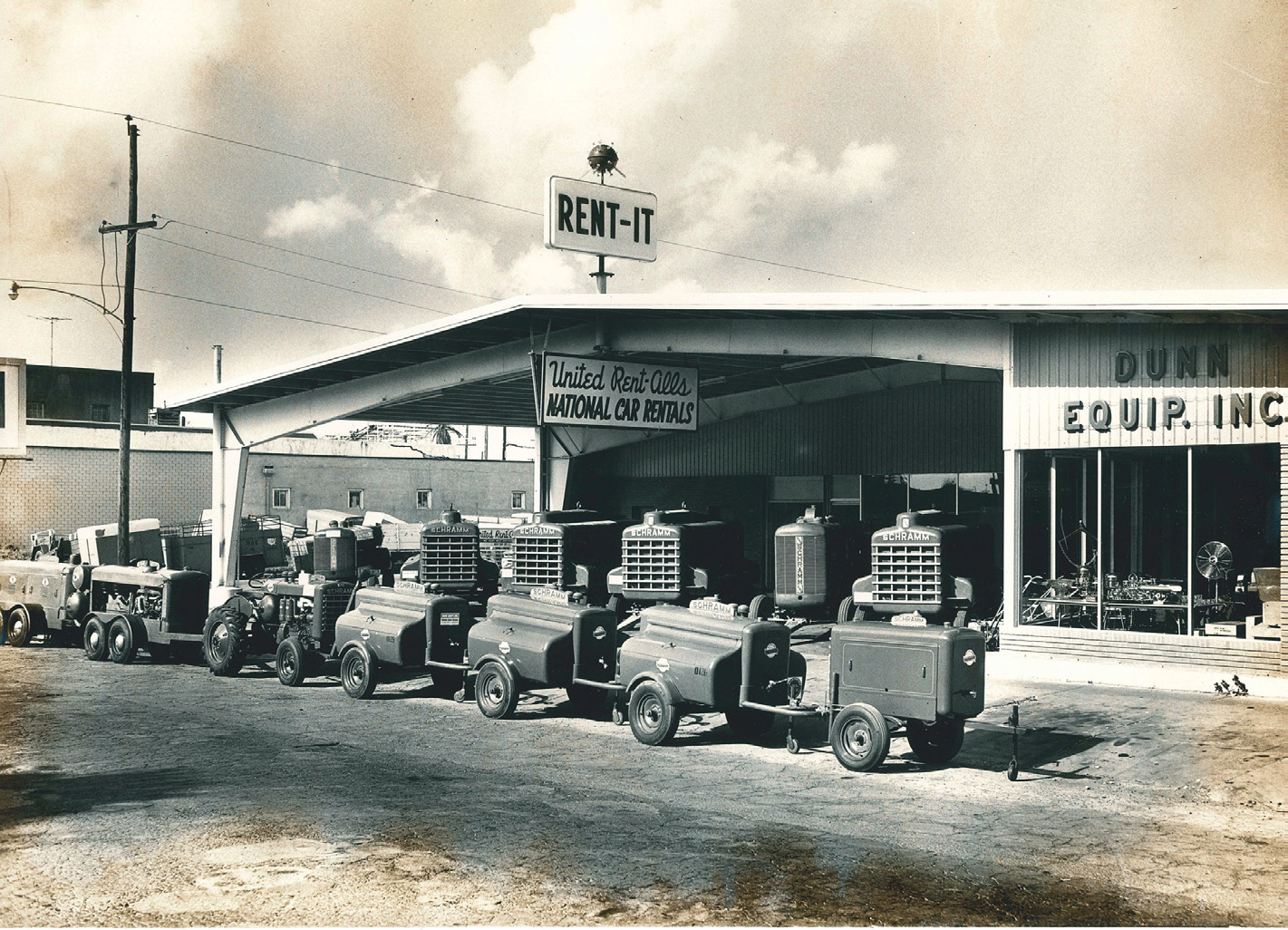
Originally, the company was an 11,000 sq ft shop in Texas City, which has now grown to 100,000 sq ft, and another large-scale facility in Bay City. “We service everything you can imagine when it comes to shell and tube heat exchangers, from new designs, including handling process conditions, thermal, and mechanical requirements, all the way through to final assembly,” asserted Pete. “We also offer cleaning and repair of heat exchangers.”
The main customer base of Dunn Heat Exchangers is midstream and downstream oil & gas, followed by power generation.
Quality Services and Safety: A One-Stop-Shop
The company has had many major milestones over the years, one most notably being the ability to clean heat exchangers off-site. “In the past, heat exchangers have always had to be serviced and cleaned on-site. Large pumps and equipment would have to be brought inside the plant, and then be manually operated. This was a very high source of accidents and fatalities, because of dealing with high-pressure water,” said Pete. “We saw that it was necessary to start cleaning off-site. We developed our own equipment, ways to transport the dirty equipment without leaking the contaminants, and create a way to clean which is easier, faster, cheaper, and most importantly, safer.”
When cleaning a heat exchanger, 40,000 psi is used, which is very dangerous. Dunn Heat Exchangers changed its safety reporting protocol and model to directly address this issue. “We do not want anyone manually using this, we want all of our employees outside of the line of fire. We have switched to a behavior-based safety model. Before, we would celebrate milestones without reportable incidents, but what some did not realize is this encouraged people not to report. This new model rewards individuals for good safety practices, which is what we are all about. We have seen really positive changes, and every single person in the company is thinking about safety.”
After cleaning an exchanger, there are often issues that need to be addressed and repairs that need to be made. “The machining is precise, and even the welding processes must be overseen for heat exchangers. It takes specialized tools to do so, therefore, a lot of the things we use in our fabrication process, we also use in the repair,” said Pete. “This is very convenient for customers, because immediately after cleaning, we can begin inspection, repair, put them back together, and get them back inside the plant quickly. This saves time and prevents the client from having to source several contractors; we are essentially a one-stop-shop.”
Dunn Heat Exchangers is a TEMA (Tubular Exchanger Manufacturer Association) shop. “Many TEMA shops will produce similar quality, as they are following the same standards,” said Pete. But what sets Dunn Heat Exchangers apart is the overall quality package: “We are the only company that has offered off-site services continuously since 1960. We are a very large company, and we are also the only site that does not recycle process water.”
This can be a big quality issue for plants. When building with stainless steels, they are looking for hydrotests with water. “A lot of people do not realize that when cleaning a heat exchanger, the same level of purity in water is needed. A high chloride water could cause the same problems that one is trying to prevent,” said Pete. “We make our own demineralized water here, with our own units to take chlorides out. When recycling process water, most things coming out of plants will be slightly acidic or basic. Neutralizing those PHs essentially creates salts, and there is no way to filter this out when recycling the water. Using this water to clean may cause corrosion and unintended consequences. At Dunn Heat Exchangers, there is no need to worry about poor water quality and the associated damages when cleaning heat exchangers.”
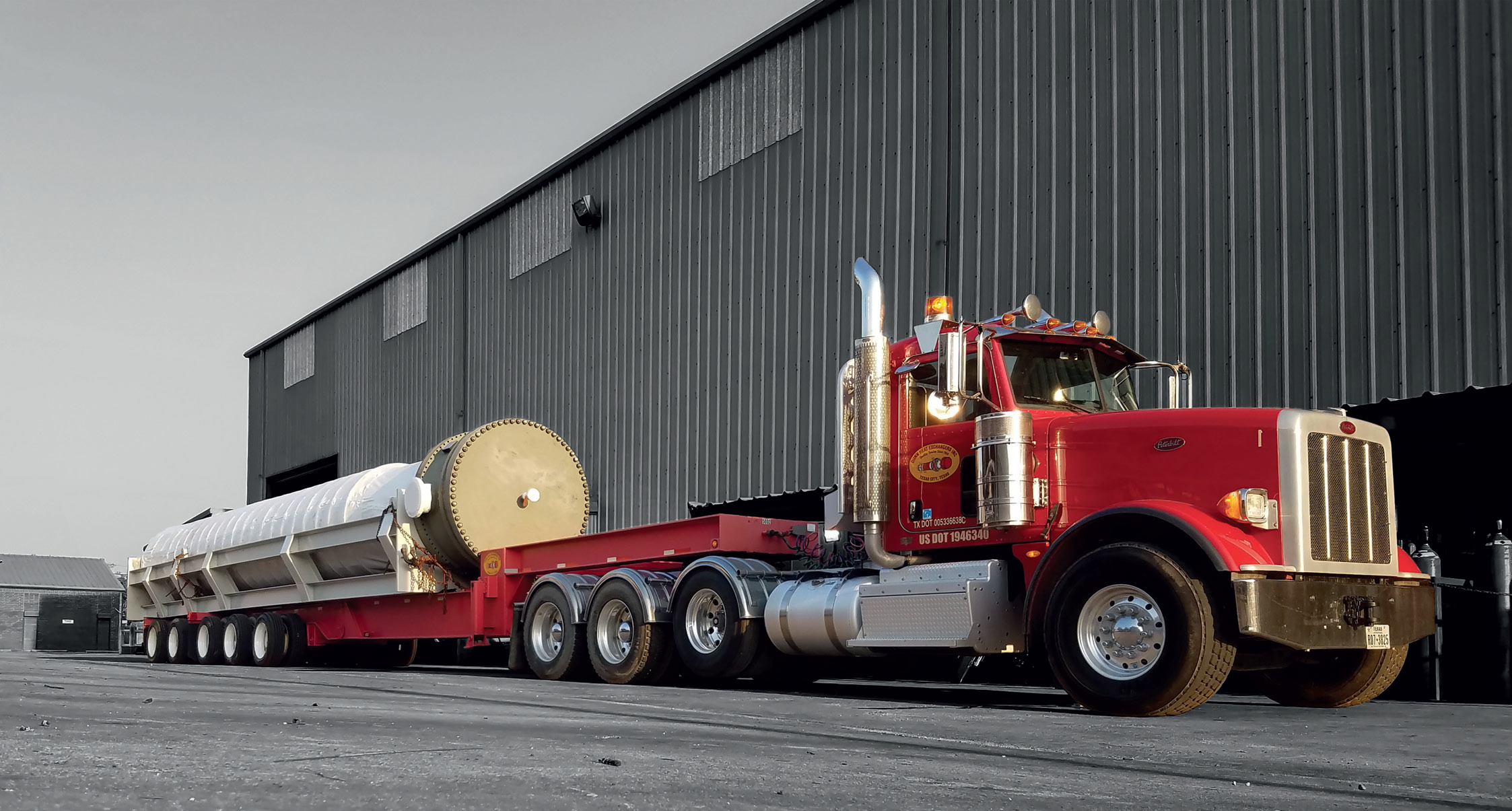
“The best way we have grown is honoring our commitments, and doing everything we can to provide good service to our customers.”
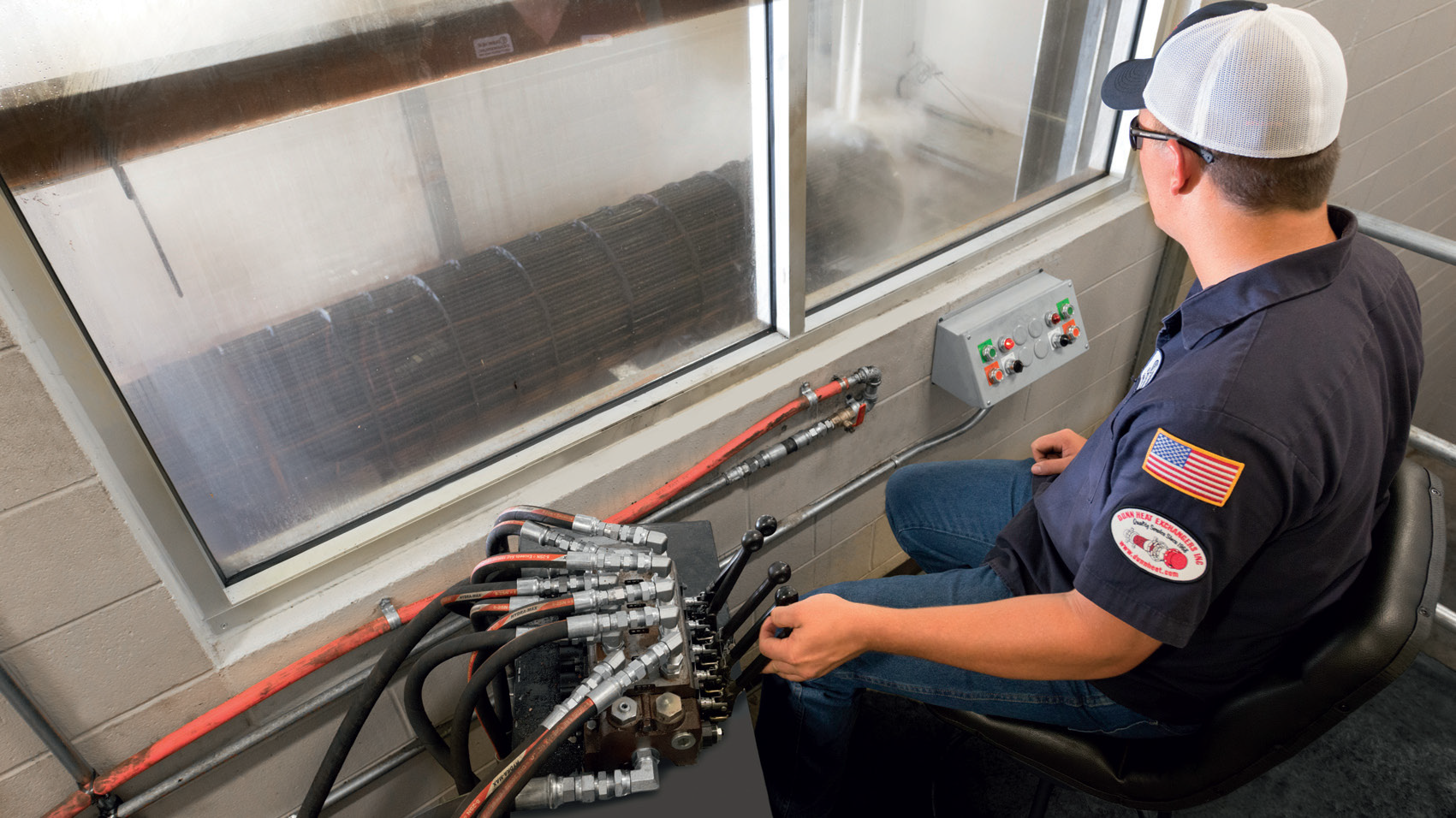
Improving Processes
A big change that the company implemented six years ago is an in-depth online tracker. Similar to the convenience of Amazon, the purpose of this tracker is for the customer to know how delivery is going. “It is also a centralized place for all inspection reports, all testing reports, and any EWA’s that they have. This is all accessible 24 hours a day, without having to speak to an employee, and updated in real-time,” said Pete. “Customers can log in and see all of the heat exchanger data as it sits at Dunn Heat Exchangers.”
Another aspect of this system is the ability to help catch problems. “If a customer sees something that seems off with the estimated delivery, we can stop and pivot, and decide what we can do to improve that delivery. We do everything we can to get the best possible delivery and solution.”
Guaranteed Satisfaction
“We want to provide the customer with the best solution to what their problem is,” said Pete. “Whether it is cleaning services, repair, or new fabrication, we look at each problem and offer the best solution. We could cut corners to remove time or cost – but how much heat transfer could be lost in service? On our repair side, we work with our customers to be honest about what the best solution might be, perhaps a new product rather than continuing to spend money on repairs, even offering solutions with our competitors if they have more shop space available.”
Dunn Heat Exchangers maintains its core values as a family business. “We have been around a long time, and we intend to be around a lot longer,” said Pete. “Someone might get the job today, if they underbid or make false promises, but they would not get that job tomorrow. The best way we have grown is honoring our commitments, and doing everything we can to provide good service to our customers, so they come back to us for their next turnaround or fabrication.”
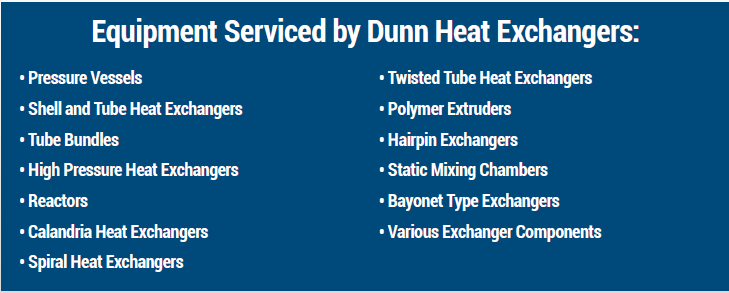
Looking Ahead
One of Dunn Heat Exchangers’ main goals at the moment is to increase speed throughout all of its processes. “Today, customers need specific timeframes that fit within their windows. Next year, it will need to be done even faster, so everything that we do, we will work on doing it in a timely manner. We always maintain quality, and safety, but are working on taking even less time than ever.”
It is obvious that refineries and gasoline will always be needed. However, with clean initiatives being pushed, including carbon capture, the need for heat exchangers is only increasing. “People in the industry have a lot of good reasons to be excited about the future. The need for new fabrication, design, and repair of heat exchangers will only grow over the next few decades. Dunn Heat Exchangers will continue to deliver what we have always delivered; quality service,” he concluded.