The metals in stainless steels like to oxidize (when iron oxidizes, it is called rust). The chromium in stainless steel has a relatively high potential to oxidize, which is why it is used. This oxide forms a protective coating on the outer surface, preventing further oxidation of the material beneath the oxide layer. When welding, the metal experiences a liquid stage, and if oxidation of the liquid occurs, this oxide forms impurities within the weld. Furthermore, it depletes the weld of chromium, so that the outer protective coating may not form. In addition to oxygen, other elements like nitrogen and hydrogen can form impurities, and deplete the metal of alloying elements.
By Justin Bekker, Metallurgical & Welding Engineer, SGS Canada Inc.
Protection Comes in Different Forms
Protecting the molten metal from air is done by creating a safe atmosphere; in stainless steels, this is generally an inert atmosphere. Although CO2 can be used for carbon steels, it cannot be used for stainless steels in amounts greater than approximately 5%, as both the carbon and oxygen are detrimental. This inert atmosphere is formed by the burning of a flux, such as that found in the coating of shielded metal arc welding (SMAW) electrodes and the core of flux cored arc welding (FCAW) electrodes. Alternatively, a shielding gas can be flowed over the weld such as that found in gas metal arc welding (GMAW) and gas tungsten arc welding (GTAW). For stainless steel fabrication, welding processes requiring a shielding gas are typically used, and this shielding gas can be easily customized to suit the needs of the weld.
The shielding gases primarily used are argon or helium as the main constituents with small amounts of carbon dioxide (CO2), oxygen (O2), nitrogen (N2), hydrogen (H2), and nitrous oxide (NO). Argon and helium are both inert, so they do not react with the atmosphere or the molten metal, but they are also electrically conductive in their plasma state (plasma is superheated gas and the welding arc is hot enough to create plasma). Plasma is what allows the electricity to conduct between the electrode and the part being welded (the electrode and the molten metal of the weld do not actually touch, except for in short-circuit welding). Welding of stainless steels with pure argon or helium is possible and it will provide the necessary protective atmosphere, but small additions of other gases may improve it. Argon, compared to helium, has narrower penetration, cooler arc temperatures, slower travel speed, and decreased wettability, but is cheaper and a more stable arc. Helium, although more desirable in several aspects, is used less frequently due to its cost and somewhat sporadic supply shortages.
Different Processes Require Different Atmospheres
In terms of welding processes, short-circuit GMAW is a colder welding process, so a higher concentration of helium is typically used. Spray transfer GMAW can be used with primarily argon plus CO2 or O2 for arc stabilization, whereas pulsed GMAW can use 100% argon as the pulsing helps stabilize the arc. FCAW electrodes contain flux (similar to SMAW electrodes) within the core of the wire that produces both the shielding gas, as well as a protective slag (see Figure 1 for a modestly cleaned SMAW weld). There are several options to the flux that can be used, but generally they dictate the suitable position for the electrode or the power source (AC or DC), which is dictated by the arc stability. An additional shielding gas is generally flowed over FCAW applications, but due to the task already being partially completed by the flux, the shielding gas is usually argon with a higher concentration of CO2 (25 – 100%). In GTAW applications, 100% argon is often used as it is necessary to avoid oxidation of the tungsten electrode (Figure 2). Helium may be added, but generally GTAW is used for thinner material and the extra heat provided from helium is not necessary. A small amount of H2 may also be added for GTAW austenitic stainless steel applications for increased travel speeds. Submerged arc welds (SAW) can have their fluxes specially tailored to alter the chemistry of the weld in addition to protecting it from the atmosphere.
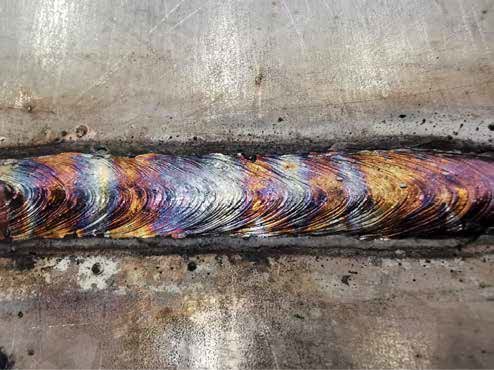


Trade-Offs in Gas Composition
Argon and helium gases create an unstable arc (helium more so than argon) allowing the arc to “dance” and promoting spatter, which are both a frustration to welders. Small additions of O2 and CO2 stabilize the arc, but as mentioned earlier, both of these gases can lead to detrimental effects – excess carbide and oxide formation. As a trade-off, O2 and CO2 may be added in amounts of 1-2% and 2-5%, respectively. Care must be taken in deciding the optimal mix as it will depend on the specific application of the weld. Unlike argon and helium, the diatomic gases (two atoms, such as O2) dissociate (into two separate atoms) in the heat of the welding arc and react with the molten metal, for good or for bad.
In austenitic stainless steel, the addition of H2 (2-15%) to argon improves the wettability and increases the penetration and travel speed. The presence of H2 can alleviate the oxidation effects when CO2 is also added. H2 is not recommended in ferritic or martensitic stainless steels due to the risk of hydrogen embrittlement. In duplex stainless steels, the addition of N2 (2-3%) promotes the austenite phase. This is a variable that can be used to fine tune the austenite/ferrite balance. NO is used less commonly, but its purpose is to both stabilize the arc and provide a health protection to the welder by reducing ozone production.
Position and Geometry
Another consideration is whether the back side of the weld is exposed to air, such as in an open root weld on a pipe. The shielding gas may have limited flow over the back side of the weld leaving it exposed while still semi-solidified. This scenario is common with GMAW and GTAW applications, which require a backing gas to be flowed from the back side (see Figure 3 for an example of a root that used 100% argon for the shielding and backing gas). For small diameter pipes it may be most efficient to fill the ID of the pipe with shielding gas (typically 100% argon), or a removable dam may be built around the back side of the weld and this space flowed with shielding gas. If a backing gas is not used in these applications, the result may be oxidation of the surface, termed sugaring. This oxidation is both aesthetically unfavorable and less corrosion resistant.
Position of the welding should also be taken into account. Since helium is lighter than air, it may be more applicable to weld in the overhead position with a higher helium concentration, and in the flat position with a higher argon (heavier than air) concentration.
Conclusion
Choosing the optimal gas mixture is not simple and requires consideration of the base metal chemistry, filler metal chemistry, degree of corrosion resistance required, welding parameters, desired aesthetics of the weld, and availability of gases. Past experience can go a long way to making good decisions, but sometimes something new comes up and additional consideration may be necessary to optimize results.
Keep in mind that changing shielding gas usually requires qualifying a new welding procedure, but if there are numerous parts to be fabricated the cost of a new procedure qualification may be well worth the improved weld quality and/or efficiency.