The stakes for leak-free operation in the offshore oil & gas market have never been higher. Operators are looking for methods to keep their facilities safe and reduce potential environmental hazards while maintaining maximum profitability. Therefore, working with trainers who understand the operator’s specific conditions is paramount.
By Joel Martin, Manager, Marketing Training & Services, Swagelok Company
Over the years, circumstances surrounding oil & gas operations have changed significantly, and keeping fluid systems and their basic components in peak working order has become increasingly important. As operational costs continue to rise and labor is in short supply, more platform operators are focused on the goal of finding well-built components that last longer and perform at a high level over their lifetimes.
Additionally, platforms are becoming less accessible as they move farther offshore, and therefore, changeouts of equipment are getting more costly. Finally, drilling operations are going deeper than at any time in history, so components must be rated to accommodate the increased pressures that occur at those depths.
Offshore Drilling
Offshore drilling platforms are complex operations. Between the instrumentation lines, hydraulic power, chemical injection deluge systems, and numerous other components, platforms often consist of nearly 50,000 feet of tubing, more than 20,000 fluid system components, no less than 10,000 fittings, and up to 8,000 mechanical connections. Maintaining such a system safely and reliably can be challenging. Choosing the proper components and materials is crucial to keeping drilling platforms operating and avoiding pitting, see Figure 1, and crevice corrosion, see Figure 2, which are more likely to occur on drilling platforms than in other applications.
To understand how these components will perform, oil & gas instrumentation engineers should equip themselves with the knowledge and training necessary in metallurgy and materials science. Working with reliable suppliers who can help train engineers on these important elements of component selection is vital. The best training programs focus on materials science to aid professionals in understanding how to obtain the best field service results.
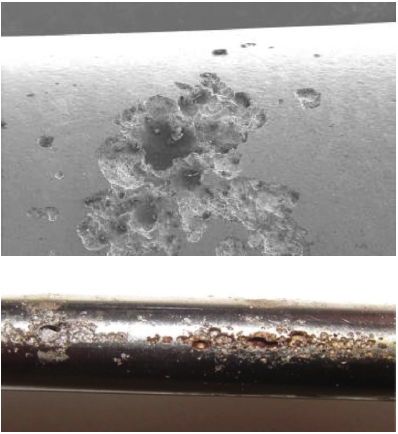
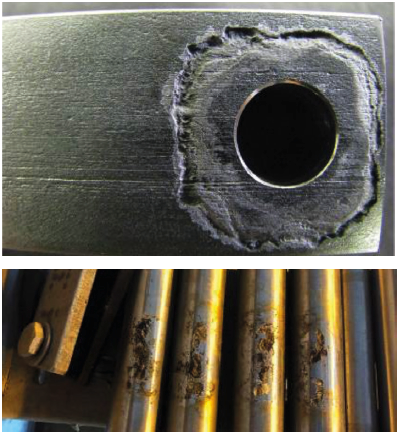
Alloy Evolution and Why Training Matters
Harsh oceanic conditions often lead to corrosion, see Figure 3, which will negatively affect a platform long before it ceases operations, but replacing components on an ongoing basis is costly and risky. Therefore, the goal is to extend component lives as long as possible. Yet, deciding which materials to select and specify is not an easy task, see Figure 4. The answer depends on what the individual is trying to accomplish and what the specific application is.
In the past, 316 stainless steel tubing – which forms a passive, chromium-rich oxide layer on its surface to inhibit corrosion– was the primary choice for oil & gas applications. Its time-tested performance met the needs of most applications, and under the right conditions, can still do so, Figure 5. With the evolution of the oil & gas industry and the increasing complexity of operations, higher-performing tubes and fittings are now required – and 316 stainless steel is not always up to the task.
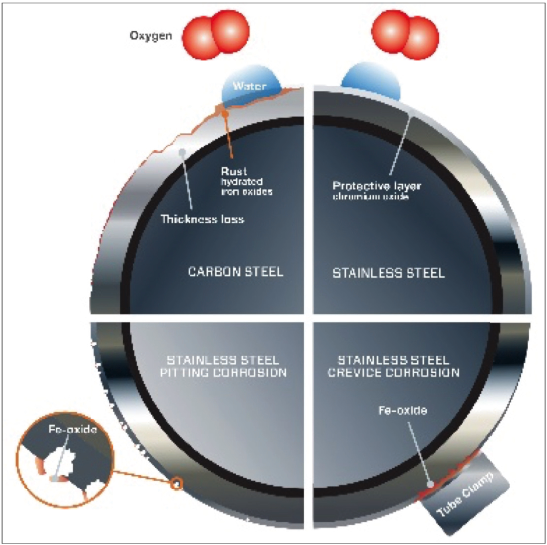
Fortunately, other alloys are available that resist corrosion, including super duplex stainless steel and 6-moly stainless steel. Although these alloys often perform better than traditional 316 stainless steel, they may not be the answer for every application on an off-shore drilling platform.
Each situation demands its own evaluation, and factors like environmental conditions, required performance, and cost should be considered. Though operators often like to use one material throughout the platform, it may not be economical to do so.
After all, 316 stainless steel offers good ductility, which allows for easier forming and welding at a lower price point. For many oil & gas fluid systems, 316 stainless steel remains the top choice, particularly if they are shielded from external factors like sun and salt spray. It is, however, important to understand that not all 316 stainless steel formulations are created equal. Some have higher concentrations of nickel and chromium than are required by ASTM, which means they are less susceptible to corrosion and are more reliable.
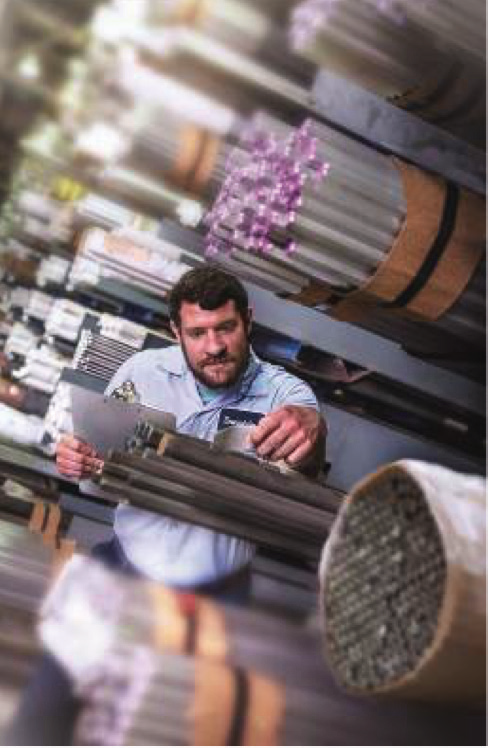
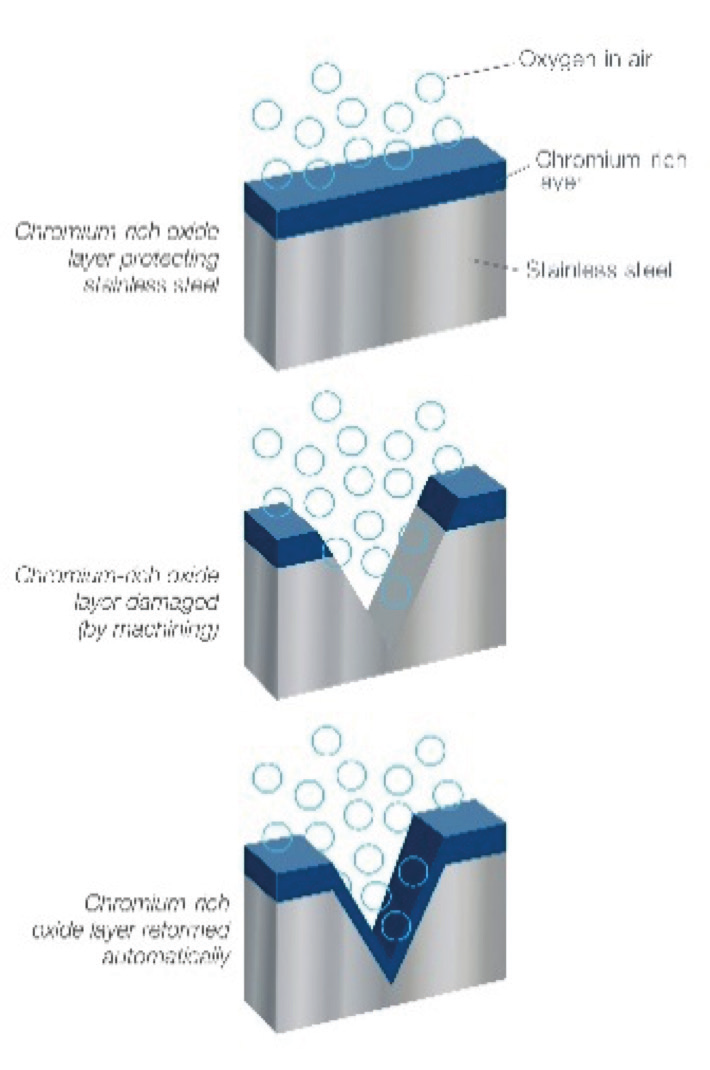
Alternatives
In contrast, fluid systems that handle sour gas require much more significant corrosion protection. Such systems are more likely to suffer from sour gas cracking or sulfide stress cracking (SSC), Figure 6. SSC occurs when the metal corrodes through contact with hydrogen sulfide and moisture, which is common on offshore platforms and is becoming a more significant problem as sour reservoirs are developed worldwide.
Under such conditions, metal becomes brittle, and cracks more frequently as tensile stress and corrosion combine. That is why more advanced alloys like Alloy 825, Alloy 625, and others should be used in such conditions to ensure the system’s safety and durability. These requirements are specified by the NACE MR0175/ISO 15156 standard.
In between the two extremes, other opportunities exist to use specific metals that best align with the goals of an application. In some systems, for example, advanced alloys may only be necessary for tubing, while 316 stainless steel can be used for tube fittings. If oil & gas professionals have a more complete un- understanding of the science behind specifying these materials, they can make smarter decisions about what alloys will improve the safety of their platform while maintaining profitability.
How Materials Science Training Can Help
To ensure oil & gas operators receive the right training in metallurgy and materials science, it is important to choose programs that employ trainers with re- al-world experience and who have been thoroughly trained themselves.
The right training program addresses the specific challenges the facility faces, in- stead of instead of using general knowledge and understanding. Trainers should also be intimately familiar with local circumstances, regulations, and other geographic-specific situations that inform the facility’s particular needs, Figure 7. For example, there are different regulations for oil & gas activity in the Gulf of Mexico than those in the northern United Kingdom. A trainer should understand the difference.
Another important factor of evaluating a training program is how well trainers understand the local workforce. The more trainers understand what knowledge is necessary for specific workers, the better they can connect with their training needs. For example, in some areas of the world, workers need more materials science and corrosion training, and the workers are particularly receptive to receiving it. In those instances, trainers can tailor metallurgy and materials science training to improve their overall knowledge and take it to higher levels.
In the case of oil & gas professionals, trainers should also be able to address the specific alloys used in the applications. Understanding the needs of oil and gas problems is crucial because the conditions on any platform can affect materials selection. For example, it is important to understand how most tubing and fittings are installed, how systems are kept clean, or whether they can be protected from outside irritants.
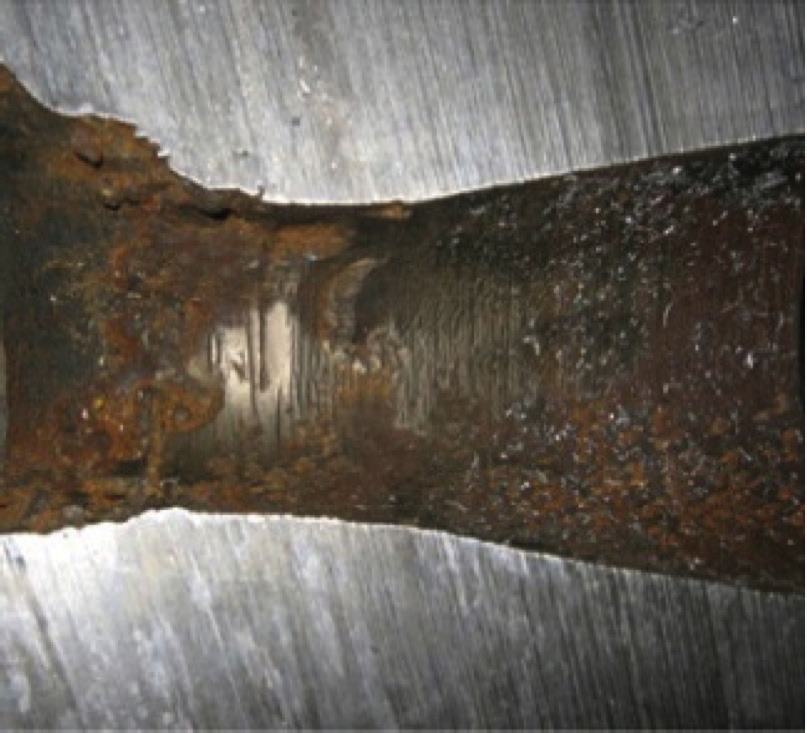
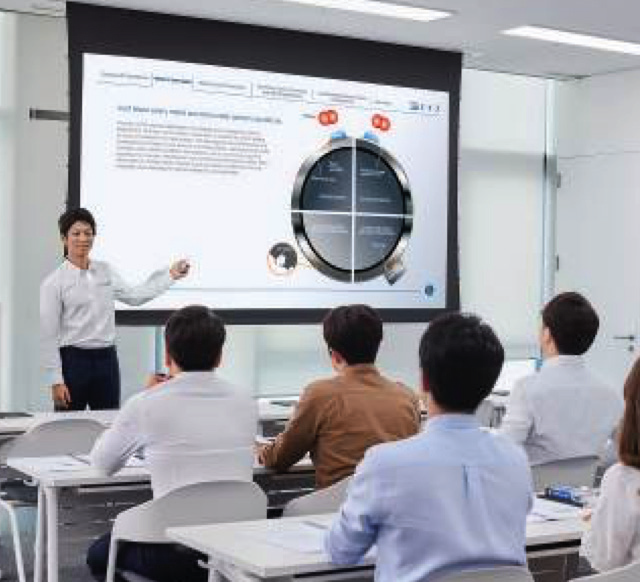
Final Thoughts
Reliable suppliers should be able to have in-depth conversations with a team leader to decide what kind of materials science training the team needs. They should also be able to guide them in their selection of materials that will meet the needs of the platform applications.
In the end, choose trainers who can be as local as possible, so they understand the conditions, markets, and needs of the team. Such training will elevate the performance of the platform and improve safety and profitability for years to come.
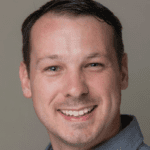