As hydrogen becomes a more popular mobility solution, selecting the proper valves in vehicles and refueling stations becomes crucial.
By Chuck Hayes, Global Technology Lead, Clean Energy, Swagelok
Shifting attitudes toward fossil fuel-driven vehicles has put hydrogen in the spotlight as a potential replacement. In addition to being cost-competitive with other alternative fuels, hydrogen has a proven safety record and can be produced sustainably. However, the key to a hydrogen-driven future is creating vehicles and refueling stations that can safely and effectively handle the gas.
High-quality materials must be used to build the infrastructure, especially the valves that control the flow of hydrogen into the vehicle or within the refueling station. The valves used in these applications must provide leak-tight performance over a long period of time. Hydrogen presents a particular set of challenges that could overwhelm lower-quality valves, so providers must adhere to the highest standards possible to make the system work effectively.
Choosing the right valves for hydrogen fuel applications is critical to ensuring the system does not put consumers at risk through faulty valve performance. To ensure the best choice is made, it is important to properly identify challenges within an application, as well as research the different types of hydrogen valves available, and where each is most effectively used in the mobility industry.

Specific Challenges Posed by Hydrogen
Containing hydrogen molecules can be challenging even under the best of circumstances. In addition to being among the smallest elemental molecules, once pressurized they create an even greater challenge. That is why all connection points – and particularly the valves – must be leak-tight.
The size of hydrogen molecules also poses a threat to lower-quality stainless steels because the molecules can diffuse into the material and cause it to weaken through a process called hydrogen embrittlement. When the stainless steel becomes weaker and is subjected to the high pressures necessary to use the fuel, it can cause cracks to occur in the valves, resulting in unsafe conditions.
That is why the valves in hydrogen fuel systems must be chosen carefully, with four specific considerations in mind:
- Pressures – To achieve desired den-sity, H2 must be stored in on-vehicle tanks at 350-700 bar.
- Stress and Vibration – Systems must be able to withstand fast speeds, bumpy roads, and inclement weather conditions.
- Safety – Refueling stations must be safe-ly operable by the average consumer.
- Maintenance – On all valves it should be easy to recreate leak-tight joints during servicing.
No matter what the application, hydrogen valves must perform with those attributes in mind. All connection points must be leak-tight and should be able to withstand the stresses put on them in mobility operations. The following are examples of types of valves that can be chosen.
Hydrogen Ball Valves
The most common valves in hydrogen systems are ball valves, which provide users with the ability to stop and start the flow of hydrogen quickly (Figure 1). If this valve is chosen, examine the stem seal carefully because it must be able to cope with challenging conditions. It may make sense to use a trunnion-style ball with a direct-load design, which can easily provide leak-tight performance as the valve opens and closes. Additionally, using a bottom-loaded stem design may enhance the safety of the valve by limiting the chances of stem blowout.
If there is any question about which ball valve to use, a supplier should be able to advise on which one is best for a specific application. Within the ball valve category, there are many options, including two- or three-way functionality, different mounting options, and multiple flow coefficient ratings that can be tailored to fit your system. Hydrogen ball valves should also be compatible with the appropriate fittings so leaks do not occur.

Hydrogen Needle Valves
If an application requires a more precise adjustment in hydrogen flow, needle valves may be the most effective option (Figure 2). Specifying needle valves in hydrogen systems means additional considerations must be made. For example, needle valves often require significant force to seal correctly because they are usually all-metal construction. Though necessary, the applied force also has the potential to damage the needle and possibly the seat. Leaks could lead to potential fire hazards, resulting in costly maintenance. In addition, large air actuators may be required to open and close needle valves in hydrogen applications, which could delay the opening or closing by up to two minutes.
Choosing needle valves made from high-quality 316 stainless steel is a best practice to ensure the metal is not easily damaged over time by the process of hydrogen embrittlement. The needle valves must also be properly pressure rated to deal with the high pressures (350-700 bar) that occur in most hydrogen applications. Finally, the needle valves should be compatible with hydrogen-qualified fittings just like the ball valves.
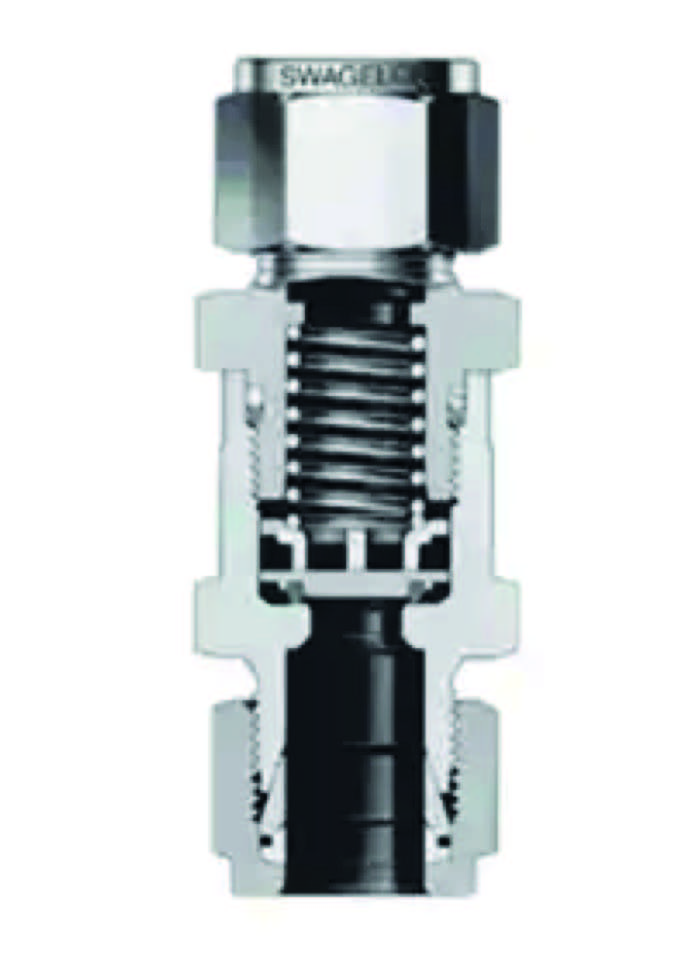
Hydrogen Check Valves
Check valves prevent backflow in hydrogen refueling systems, allowing consumers to use them safely (Figure 3). Even if one understands check valves in other industrial applications, those used in hydrogen refueling stations must contend with hydrogen-specific conditions.
Once again, the steel matters. Most check valves have springs and are usually constructed with strain-hardened material, which is more susceptible to hydrogen embrittlement. Check valves used in hydrogen systems should be manufactured with high-quality 316 stainless steel to avoid these problems. In hydrogen refueling applications, check valves undergo rapid, severe changes in temperature and pressure, which can lead to damage of the valve’s elastomer seals. Ball check valves are the better option for hydrogen compressors for that reason, and they should also be compatible with other hydrogen system components.
As the world begins to view hydrogen as a viable alternative to fossil fuels over the long term, the safety, reliability, and durability of its corresponding infrastructure must meet high-performance standards. Working with a reliable valve supplier who can help choose the proper components for whatever hydrogen system is being built will help secure its long-term future.