What lead you to pursue a career in welding?
I was at Ohio State University for an engineering major and I found out Ohio State was one of the only schools with a welding engineer- ing program. I was familiar with welding because my father did a lot of it and I ended up becoming a welding engineer.
I’m actually an engineer, but I’m qualified to do welding. If I go into the field to help clients they aren’t going to listen to me unless I can be a good welder. When I first started at Lincoln Electric, six years ago, I had to go through the 16-week Welding School program. All of our internal engineers or technical sales representatives, who are also typically engineers, have to go through the same program. Even the marketing department will take part in welding seminars so they are familiar with the products Lincoln Electric manufactures.
What are some of the lessons taught during the school?
The materials I focus on today because Lincoln Electric, through R & D as well as acquisitions, is moving into the development and manufacture of high alloy consumables.
A lot of it is hands-on, but the important part is the knowledge. Learning why you do certain things, why you use one material to weld another material, what happens when things get hot and what happens when you cool things down too fast, basically knowing what happens to the materials when we weld them.
This is especially important when it comes to welding stainless steels because there are so many different materials, filler metals and electrodes to choose from. It is important to make sure it is welded correctly. Newer materials are always being developed.
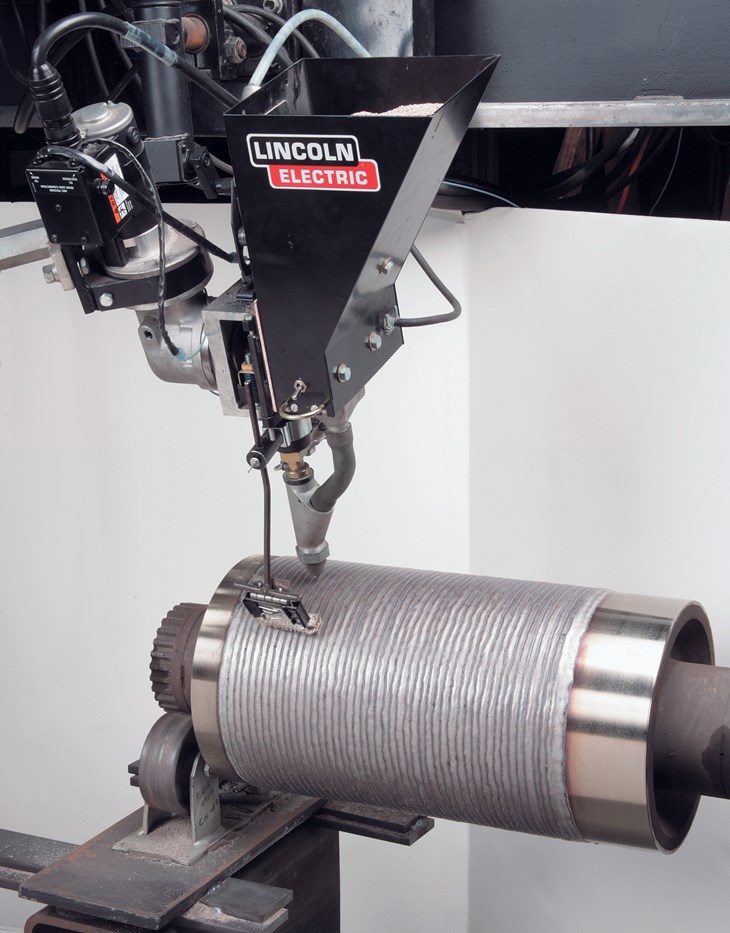
Lincoln Electric
What are some of your departmental duties?
We offer assistance to customers with welding procedure questions. If they are having problems with filler metal selections, weld cracking issues, or meeting specific welding requirements we will help find solutions to their problems. If they want to make a part faster or reduce the amount of welds we’d work with them on that as well.
We also work closely with our sales team of approximately 200 people. We’re their technical support if they come across something they aren’t familiar with material wise or if they need a specific welding procedure to help a customer. We also evaluate the new Lincoln Electric products. After the design is done they’ll have us test the equipment. If it’s a filler metal, they’ll have us weld with electrodes to determine if it’s better than what we currently have.developed, higher-alloy stainless steels, nickel alloys, cobalt alloys and others. These are I do a lot of demonstrations too. This afternoon I have customers coming in with one of our sales representatives and we’re doing a comparison between different types of stainless steel shielding gases for MIG (metal inert gas) welding. They sent in some gases and we have some shielding gases here; they want to weld with all of them to determine which one is best for their application. Other times customers come and see us weld on their parts. We even have a department where clients send parts and we’ll design a robotic system for them and they can watch the parts being welded. It’s called a “run-off.” This way they get to see everything before they buy it.
Can you describe a typical working day?
It varies, but that is the good thing about the job. There is always something different. The day depends on who is calling or which customers are visiting. It could be someone building trailers for trucks, or someone building power plants.
During the week we have a 1-800 hotline people call with their welding questions. Each half-day, all the engineers take turns answering the hotline and we talk about welding all day. We could get a phone call from a guy that bought a small machine from a retail store and is welding on his car in his garage or from a PHD researcher in a lab doing material testing. It is such a wide range of questions and it varies so much on who calls the number.
What are some specific welding problems you help with?
A part could crack during fabrication so we would look into it and perhaps discover they weren’t heating up the part hot enough before they started welding. Some materials we have to heat up, either with a torch or by putting it in an oven, to get it hot before we weld on it because it could crack. Or maybe a part in service isn’t lasting as long as it should because the right material isn’t being used. Many times people will select materials for what they want to make and afterwards have to figure out how to weld it. We do filler met- al and process recommendations. The main processes we support are flux cored, MIG (metal inert gas), submerged arc, TIG (tungsten inert gas) and stick welding.
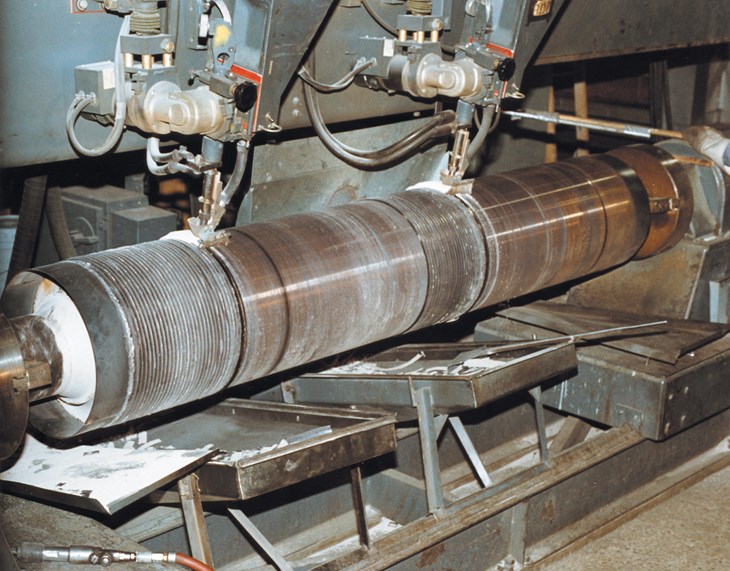
What are some challenges working with stainless steel?
When dealing with stainless steels and nickel alloys, higher-end alloys, it starts to get tricky when you have dissimilar materials to join and different service environments that can be tough on materials. A part of my job is gathering knowledge on all the different alloys out there because there are so many. For example, with stainless steels, the most common is 304L, and it is often used in power plants, food processing and the oil and gas industry. There are so many welding codes and rules to know just for one material, so I do a lot of read- ing and research using codebooks written by different organizations like the American Welding Society (AWS) or the American Society of Mechanical Engineers (ASME). We also have people in my department in charge of specific industries, like pipelines or power generation, so they are helpful.
Stainless steels also weld differently than carbon steel. The majority of people weld with carbon steel and once you start welding stain- less or the nickel alloys it’s not the same. The weld puddle moves differently, the procedures and the settings are different.
Do you have to weld stainless steel with other metals?
Yes, welding dissimilar metals is another challenge. Trying to weld different materials together, like stainless steel and low alloy steel can be difficult. Sometimes we have to do a three-step process where we have to weld a thin layer on the low alloy steel or we build it up, which is called a “butter layer,” then we put that in a heat treatment and after that’s complete we weld it to the stainless part. So it’s a multi-step process, where you actually have to do some thinking and planning to make sure you get good results.
Are there any extra precautions you have to take with stainless?
Everything has to be clean, from the materials we use to the area we work in. If we have oil on the stainless it could cause cracking or porosity in the weld. If we have a stainless part and we clean it with a wire brush that isn’t stainless, the part will rust. Shielding gasses are also more important. When weld- ing a pipe with regular steel we can just weld it up. With a stainless pipe we sometimes have to fill the inside of it with argon gas to protect the backside of the pipe, and the backside of the weld metal, from coming in contact with oxygen because that can lower the corrosion resistance of the materials. This process is called purging.
What tools make stainless welding easier?
The biggest thing is using auto- mated systems. The more we can automate things the more repeatable, and faster, they will be. An example, besides a robot, is an Orbital TIG system. Instead of having someone sit and weld around a pipe, we can use a TIG system that clamps onto the pipe. A little mechanized system rides around and does the weld, but the operator still controls it with the start and stop button. He can adjust the current, but the movement of the welding arc is done automatically. It’s faster, easier on the operator and more repeatable than manual welding.
The other big thing is pulsed MIG processes, because we are able to adjust the output of the machine by tuning it to specific alloys using computer software. That has been helpful with some of these newer alloys, especially the nickel based ones. We can also tune our machine to some of the duplex stainless steels to ensure we get a stable welding arc out of it. That will make it easier for the welder to use.
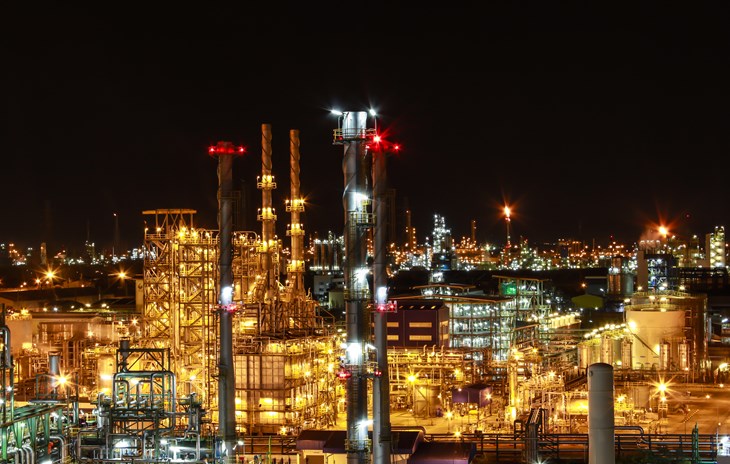
What trends are you noticing with stainless?
We’ve been getting lots of calls and visits from semi-trailer manufacturers making more components out of stainless, like tanker trailers. Also, we get a lot of requests regarding LNG (liquefied natural gas). We’re doing a lot of work helping with storage tanks and vessel fabrication. Those are made from 304L, 316L stainless steels and nickel steels. Some of the tanks can be as tall as 120 feet and up to 282 feet in diameter.
Process piping for chemical plants and refineries is always a big one. People are always replacing piping or they are building new facilities. Once again, there could be different materials, because someone might find one material does not last as long as they require. So they might try going to a higher alloy and we have to figure out how to weld it to the existing pipes in the plant.
As the vice chairman of AWS Cleveland section why do you think it’s important to join a professional association?
I do it because it’s helpful meeting other people in the industry. We have monthly meetings and we always have a topic that is discussed; often it’s a technical topic, so it’s a good opportunity to learn from others in the industry. If I’m giving a technical presentation, I think it’s a good opportunity to teach people and spread knowledge on welding.
The good thing about AWS is they write a lot of the codes and standards for welding and just being involved in that is very helpful. We could be talking about codes at one of the meetings and the next week I might come into work and have someone ask me the same thing. It’s always good to talk to other people, because it gives a
different perspective and I can find out different ways of doing things.
What advice would you give to someone starting out in the field?
Listen to other people. It’s always good to meet others in the industry and try to learn about what materials are used now and what materials may be used in the future. That’s why I have a job, because everything is always changing, from the materials to the way we weld. Everything changes and it’s important to keep on top of those changes.