Austenitic stainless steels are the most popular grades of stainless steels due to their excellent corrosion resistance, high formability and weldability. However, the tribological behavior of this material class is characterized by a high coefficient of friction and poor wear behavior, which severely limits the technical application possibilities and the service life. Low-temperature surface hardening processes using carbon and/or nitrogen can increase the wear resistance while maintaining the corrosion resistance. However, nitrogen-based processes are unsuitable, since nitrogen tends to recombine in its gaseous phase at temperatures around 300°C. This is why the use of nitrogen-based processes is not recommended. S³P, featuring Kolsterising®, a proprietary Bodycote process, is a carbon-based low temperature surface hardening treatment which produces a much higher thermal stability in the hardened condition, allowing both high wear resistance and subsequent welding.
By Susanne Gerritsen, Application and Development Engineer, Bodycote S3P
Low-Temperature Surface Hardening Processes
The corrosion resistance of austenitic stainless steels is based on the formation of a protective chromium oxide layer. Unfortunately, chromium tends to form nitrides and carbides at elevated temperatures (>500 °C). If the chromium content locally drops below a certain limit CrRe (dashed line in Figure 1) at which the steel is corrosion resistant, pitting or crevice corrosion will easily occur. In order to enhance the mechanical performance of austenitic stainless steels while preventing the chromium depletion, low temperature carburizing (LTC) / nitriding (LTN) and nitrocarburizing (LTNC) below 500 °C – at which the incubation time for precipitations, mostly carbides/nitrides, is longer than the treatment time – can be applied. 1 – 4
The hardening principle is based on thermochemical diffusion of carbon and/or nitrogen to form a diffusion zone, also known as ‘expanded austenite’ or ‘S-Phase’. The interstitial embedded atoms generate high residual compressive stresses in the diffusion zone (see Figure 2). These stresses increase the surface hardness, by which the wear resistance increased. The diffusion-based hardening method results in a gradual hardness progression, which maintains the material ductility.
Nitrogen expanded austenite generates residual stresses up to 5-8 GPa compared to ~2 GPa for the carbon expanded austenite, leading to a slightly higher surface hardness, but is also associated with significantly more brittle behavior compared to low temperature carburizing (LTC). Low temperature nitrocarburizing (LTCN) combines a hard surface hardness value with a relatively good ductility. However, LTC is preferred when high fatigue strength and ductility is necessary. 5 –
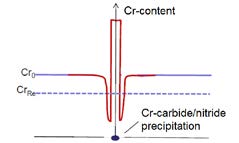
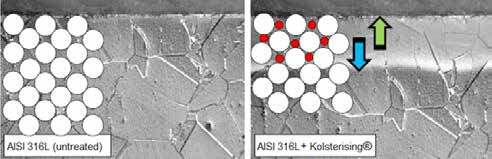
Welding In Combination With Low Temperature Surface Hardening
Welding is a major process to join components or groups of components permanently and therefore plays an essential role in component production. During welding a material-closed solid connection is created by using temperatures above the melting point and fuse materials together. Welding is possible with and without a filling material. When using welding with filling material, similar corrosion properties of the part to be welded and the filling material must be considered to prevent galvanic corrosion. One technique to weld stainless steels is by electrode welding, including Metal Inert Gas (MIG), Metal Active Gas (MAG) and Tungsten Inert Gas (TIG) welding. Another method is laser welding, which has the advantage of lower heat influence and a narrower heat affected zone. 9,10
Welding Before LTC
As mentioned in the previous section, welding introduces additional heat into the material, which usually leads to a change in the base material structure, depending on the chemical composition of the stainless steel and the welding parameters. For steel grades with high amounts of ferrite-forming elements like chromium and molybdenum, delta ferrite can form rapidly and a loss of ductility can occur. Additionally, a too slow cooling rate can lead to chromium precipitations and thus a reduction of corrosion resistance. Both reduce or prevent carbon diffusion during S³P Kolsterising® and therefore no satisfying result can be achieved. Furthermore, due to the low thermal conductivity of stainless steels and the high coefficient of thermal expansion, higher residual stresses may occur and lead to distortion during the heat treatment process. To minimize the challenges of austenitic welding, accelerated cooling techniques as with liquid CO2 or solution annealing can be applied. To avoid chromium precipitations, a low carbon content in the base material is recommended. Additions of titanium or niobium (TiC, NbC) are also advisable since they have a greater affinity to carbon than chromium. Examples of this are material grades out of the AISI 300 series with an L, like AISI 316L (1.4404) or with Ti/Nb such as the grade AISI 316Ti (1.4571) with titanium as the carbide former. To avoid distortion during heat treatment, the thermal stresses after welding can be reduced by solution annealing (> 1000 °C). Also, electropolishing is recommended to minimize the internal stresses in the outermost surface of the component, and additionally a flat and homogenous surface will be achieved which increases the corrosion resistance.
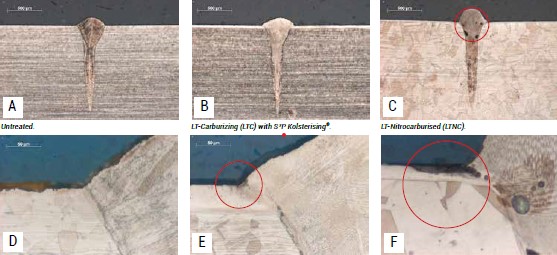
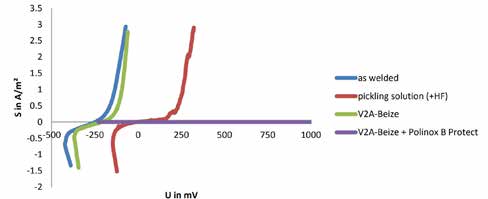
Post-Treatment And Corrosion Resistance
Post-welding of S³P hardened surfaces can lead to the formation of light chromium carbides as well as heat tint and/or slag. By suitable mechanical or chemical processes, such as pickling and post passivation, the corrosion resistance can be raised again to the value of the base material. This is illustrated in the pitting potential curves in Figure 4. The higher the voltage at the point of the curve rise, the higher the corrosion resistance. The best results can be achieved when using a combination out of Stain (HCL+HNO3) and post passivation.
Conclusion
S³P Kolsterising®, a low temperature surface hardening processes, increases the wear resistance of austenitic stainless steel grades. Welding, a thermal joining technology with a very high temperature impact, plays a major role for austenitic component production. The combination of welding and low temperature surface hardening is possible, taking into account essential aspects:
- If feasible, it is recommended to weld components before low temperature surface hardening.
- If welding is only viable after surface hardening, a process with the lowest possible and focused heat input should be selected, e.g., laser beam welding.
- Low-temperature hardening introduces large amounts of carbon and nitrogen, whose chemical behavior is temperature-dependent.
- Carbon-based diffusion should always be preferred to nitrogen-based diffusion if the components are to be welded after surface hardening. Carbon may recombine to solid precipitations to a certain extent, whereas nitrogen can additionally form pores, which negatively affects not only the corrosion properties, but even the mechanical properties.
- Welding joint should not contain any slag residues or oxides, such as temper colors, to remain the corrosion resistance. Mechanical or pickling processes in combination with additional passivation are recommended to restore the corrosion properties.
References
1. Inoue Y.; Kikuchi M.: Present and Future Trends of Stainless Steel for Automotive Exhaust System, Nippon Steel Technical Report No. 88, 2003
2. Mittermeijer, E. J.; Somers, M. A. J.: Thermochemical Surface Engineering of Steels. Woodhead Publishing, Kidlington, UK, 2015, pp. 581–614. – ISBN: 978-0- 85709-592-3
3. Bell, T.: Low Temperature Nitriding and Carburizing, Advanced Materials& Processes, June, 2002
4. Müller, D.: Die Wärmebehandlung metallischer Werkstoffe. Vorlesungsmanuskript, University Bayreuth, 2013
5. Berns, H.; Zaugg, R. Anwendung des Randaufstickens für nichtrostende Bauteile. In: HTM Z. Werkst. Waermebeh. Fertigung, 57 (2002) 6, S. 377-382
6. A.H. Heuer et al., Interstitial Defects in 316L Austenitic Stainless Steel Containing “Colossal” Carbon Concentrations: an Internal Friction Study, Scripta Mater, 56(12) 1067-1070 (2007)
7.Berns, H.; Pyzalla, A.: Microstructure and residual stresses of stainless steels case hardened with nitrogen. Surf. Eng. 20 (2004) 6, pp. 459–463, DOI:10.1179/174329404X7108
8.Miki, Y.; Nishimoto, A.; Tamiya, T.: X-Ray Residual Stress in the S-Phase of Stainless Steel Nitrided by a Plasma Nitriding Method and Residual Stress Measurement of a DLC Film Deposited on the S-Phase. J. Soc. of Mater. Sci. 65 (2016) 7, pp. 517–524, DOI:10.2472/jsms.65.517
9. Parvan Chavdarov: Electron Beam Welding of Superduplex Stainless Steel S32750, Stainless Steel World 2007 Conference, Maastricht, the Netherlands
10. E. Capello, P. Chiarello, B. Previtali, M. Vedani: Laser welding and surface treatment of a 22Cr 5Ni 3Mo duplex stainless steel, Materials Science and Engineering A351 (2003) 334-343
11. Gene Mathers, TWI: Welding of Austenitic Stainless Steel -TWI (twi-global.com), accessed: 04/22
12. Gene Mathers, TWI: Welding of Austenitic Stainless Steel – Part 2 – TWI (twi-global.com), accessed: 04/22
13. R. Bozart, G. Meinken, T. Kamps, C. Gülcan, Fachinfos zum Schweißen von warmfesten Stählen, Teil 2 (anleitung-zum-schweissen.de), Artdefects Media Verlag, accessed: 04/22
14. John C. Lippold, Damian J. Kotecki: welding metallurgy and weldability of stainless steels, 1. Steel, Stainless-Welding, 2005, pp. 230-259 ISBN: 0-471-47379-0
15. J. Pekkarinena, V. Kujanpää: The effects of laser welding parameters on the microstructure of ferritic and duplex stainless steels welds, Lappeenranta University of Technology, Physics Procedia 5 (2010) 517–523