Playing a pivotal role across the board, from the oil and gas industry to chemical manufacturing to power generation, heat exchangers and heat transfer equipment efficiently transfer heat between fluids, enabling the reuse of thermal energy. Through enabling the recovery of heat, these components are known for reducing operational costs significantly, as well as enhancing energy efficiency. Follow Stainless Steel World Americas to learn more about the fundamental elements of heat exchangers, shell and tube configurations, material considerations, design, and more.
By Shopia Ketheeswararajah
Q: What Are Heat Exchangers and Why Are They Important in Industrial Applications?
A: Heat exchangers are specialized to the application that they are used in. Typically, the heat transfer equipment is designed to transfer heat between two or more fluids, without mixing. The role the heat exchanger plays in industrial processes involves optimizing thermal energy use. For example, heat exchangers recover heat from hot process streams and use it to preheat incoming fluids. This process is known for reducing operational costs significantly and promoting energy efficiency.
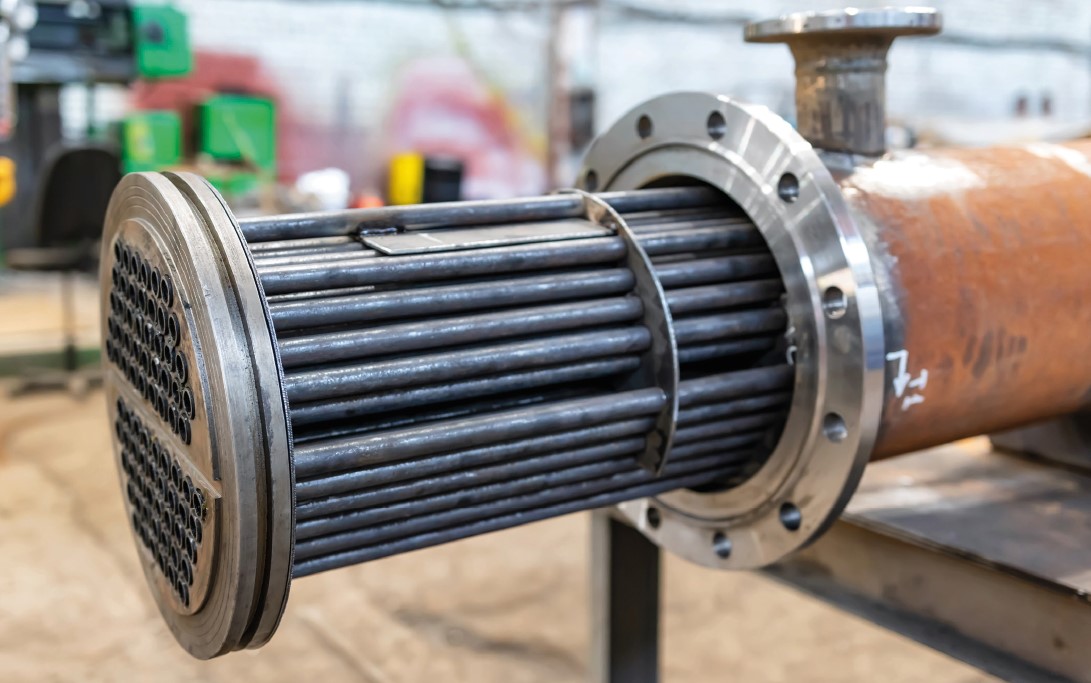
Q: What Are the Main Types of Heat Exchangers Used in the Oil & Gas Industry?
A: There are a variety of heat exchangers used in the oil and gas industry. Shell and tube heat exchangers are most likely to be found in plants and are used mostly for their robustness and ability to handle high pressures and temperatures. This type of heat transfer equipment contains a bundle of tubes within a cylindrical shell.
One type of fluid flows through the tubes and another fluid flows around the tubes within the shell; this creates heat transfer. The second variation of heat exchangers that are most commonly found in the field are called plate heat exchangers. They are known for their compact and flexible design, making them ideal for tight spaces. Plate heat exchangers use corrugated plates to create turbulence which enhances the heat transfer process.
Air cooled heat exchangers utilize air to cool process fluids and are essential in environments where water is not easily accessible. Lastly, double-pipe heat exchangers typically have a simpler design with one pipe inside another. This allows for the heat transfer between fluids in the inner and outer pipes.1
Q: How Does a Shell and Tube Heat Exchanger Work?
A: As mentioned previously, shell and tube heat exchangers typically allow for the flow of two fluids without having them mix with one another. The fluid inside the tubes transfers its heat to the fluid in the shell through the tube walls. These designs can create a large heat transfer area, especially in applications that are high-pressure and high temperature. In addition to this, shell and tube heat exchangers can utilize baffles within the shell to direct fluid flow and increase heat transfer by creating more turbulence. The flow process can be configured in several different ways, such as parallel flow, counter-flow, and cross-flow. Each unique configuration of flow is used to optimize heat transfer. In comparison to plate-type coolers, this type of heat exchanger is known for its benefit in cost-effectiveness. 2

Q: What Are the Advantages of Plate Heat Exchangers Compared To Other Types of Heat Transfer Equipment?
A: Plate heat exchangers usually consist of a large surface area that is supported by closely spaced plates. The turbulence created by the plate’s pattern offers users several technical advantages. This design improves heat transfer rates while also minimizing fouling. The design of this specific type of heat transfer equipment is modular, meaning it allows for easy expansion or modification to meet any changes made to the process. This type of equipment is said to be easier to disassemble and clean, reducing maintenance downtime and these features make plate heat exchangers beneficial in applications where space is limited.3
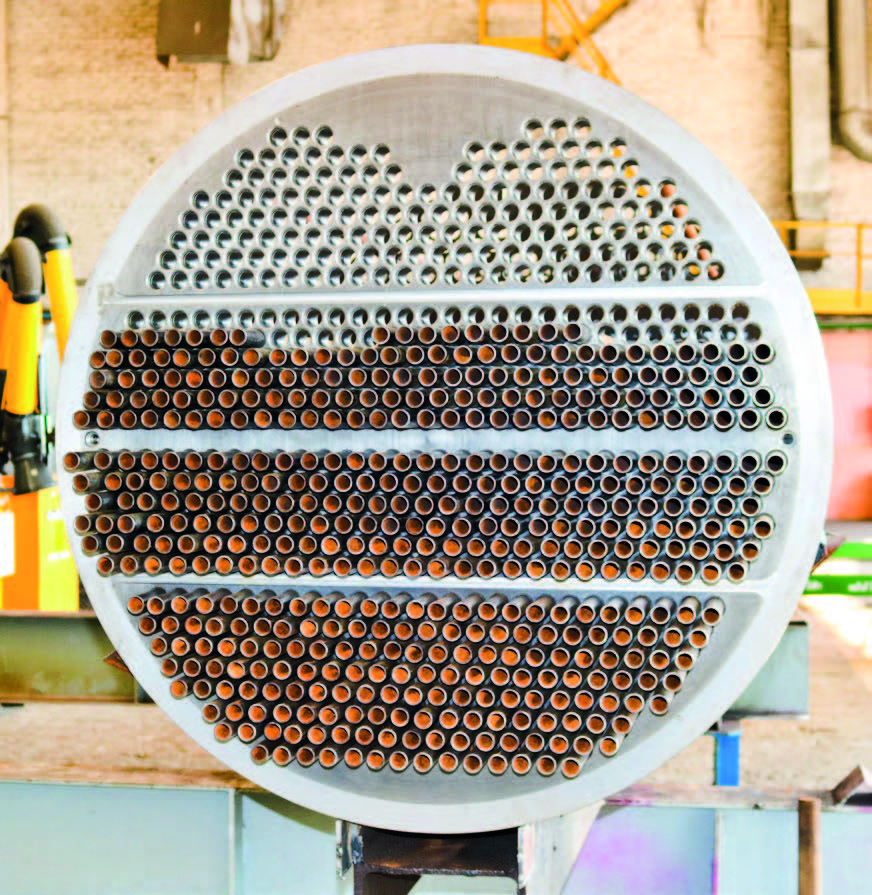
Q: What Factors Should Be Considered When Selecting Materials for Heat Exchangers?
A: Selecting the appropriate materials for heat exchangers consists of detailed assessments of key factors. Corrosion resistance is at the top of the list when it comes to material selection. This is because the material should be able to withstand the corrosive nature of fluid when it comes into contact with the equipment, especially when it is being used in the chemical and oil and gas industry.
Thermal conductivity is another factor that must be taken into consideration. Materials that are high in thermal conductivity aid in the overall efficiency of the heat transfer process. Mechanical properties of the materials aligning with the operational pressures and temperatures is also a critical factor that must be taken into account.
Lastly, cost consideration poses a significant factor; a balance between performance characteristics and economic feasibility should be at the forefront when determining the type of material that should be used in a heat exchanger’s design. Stainless steel, titanium, and various nickel alloys are chosen based on the requirements of the application that will be using the heat transfer equipment.4
Q: What Are Some Essential Maintenance Practices of Heat Exchangers?
A: Maintenance practices ensure the longevity of the heat exchanger, in addition to its performance. Regular cleaning is vital to prevent scaling and fouling, as these two challenges pose a risk to the overall efficiency of heat transfer. This involves a process that both chemically cleans to dissolve deposits and mechanical cleaning which aids in removing physical blockages of debris.
Routine inspections are critical to detect early signs of wear-and-tear, corrosion, and mechanical damage. Often, operators will perform leak testing to prevent the mixing or cross contamination of fluids. When fluids cross contaminate, there are potential hazards that will affect the process and compromise the equipment’s integrity.
Monitoring performance such as differing temperatures and pressure drops can be helpful to determine any decline in performance, prompting timely maintenance. Lastly, implementing a proactive maintenance schedule based on the equipment’s operation can extend the overall life expectancy of the heat exchanger.5