Cryogenics
Please describe the basic concept of what “cryogenics” is.
The word comes from the Greek word meaning cryo, which means ‘cold,’ and genic, which means ‘producing.’ It is the science that studies very low temperatures, generally temperatures below -150°C. (It is not well-defined what the cryogenic point on the temperature scale exactly is, but it is usually believed to be -150°C when we are talking about valves.)
The Standard MSS-SP134/2012 considers cryogenic fluid to be a gas that can be changed to a liquid by removal of heat by refrigeration methods to a temperature at -100°F (-73°C) or lower. That is, any fluid below -73°C is considered cryogenic service.
What are some of the end-use applications for cryogenic valves?
In the hospital sector, cryogenics is often implemented in the transportation of oxygen, whereas in the oil and gas industry, cryogenics is used in the transportation of Liquefied Natural Gas (LNG) and/or Liquefied Petroleum Gas (LPG).
Is there a big demand for cryogenic/valves?
No, only because the segment of cryogenic valves is very restricted, so it depends upon the few companies that operate it. The demand for these products often rises when there is a production plant that is being expanded or needs some repair or replacement of lines. The demand for cryogenic products is much lower than the demand for conventional valves.
How are cryogenic valves different from standard valves?
Cryogenic valves have a body/bonnet extension integrally cast/forged or consisting of a pipe or non-standard wall tube that distances the stem packing and valve operating mechanism from the cryogenic fluid in the valve body/bonnet.
Materials in contact with cryogenic fluid or exposed to cryogenic temperatures must be suitable for use at the minimum temperature specified by the purchase order. The pressure tests are made at temperatures -196°C.
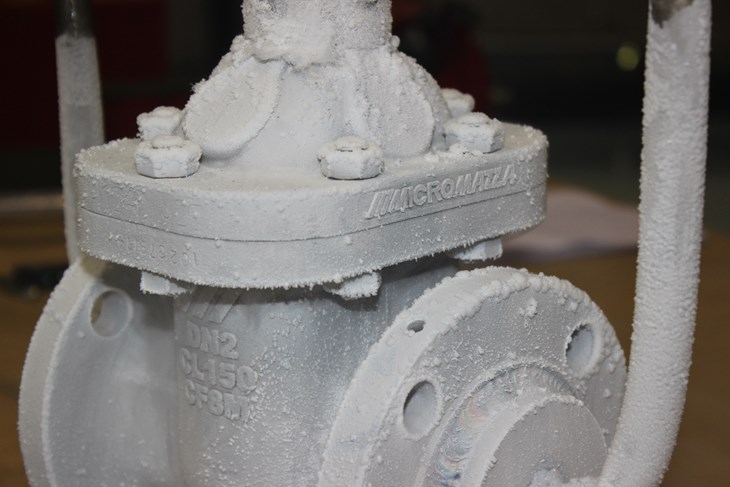
a) What type of environments do they have to withstand?
It depends on the application and what is specified by the purchase order, but to approve a cryogenic valve, it need be tested according to standards like the MSS-SP134 or BS6364. Both standards are very rigorous and request pressure tests with room temperature at -196°C.
b) Do they have to be cast out of a specific material?
Yes, they do. The cryogenic valves usually are cast or forged out of stainless steel series 300 material (such as the grades 316, 304, 321, 347), but other possible materials can be found in the standard ASME B31.3.
What is the production process like for cryogenic valves?
The production process for cryogenic valves is a very specific and thorough process. It needs to be run in a clean room and the parts need be free of any grease and/or oil. Besides the production pressure test (which is for all valves), the valve needs to be approved in a severe cryogenic testing lab where the test fluid generally is helium gas.
a) Are there any special considerations?
All the valves that need to be tested have to be free of water, grease, and/or oil, and if they aren’t, there is a large likelihood that the test could fail because the low temperature transforms any contaminant in something like stone and can stop the valve drive or damage the seat.
b) Do they require different testing?
Yes, they do. The testing is done in a tank where the valve is submersed in liquid nitrogen, which reaches a temperature of -196°C.
Are there any particular challenges with cryogenic valves?
Yes, there are. Packing and gasket materials in direct contact with the service fluid have to be capable of operating at temperatures from positive (warm) temperatures to the lowest cryogenic temperatures. The valves need to have a bonnet extension that distances the stem packing and valve operating mechanism from the cryogenic fluid that might otherwise damage or impair the function of these items. The bonnet extension shall be of sufficient length to provide an insulating gas column that prevents the packing area and operating mechanism from freezing.
How are these challenges dealt with?
These challenges are treated very seriously by a strong engineering team that is dedicated in producing the best-possible product. It also helps to have access to a laboratory with all the necessary resources to perform all the complex tests.
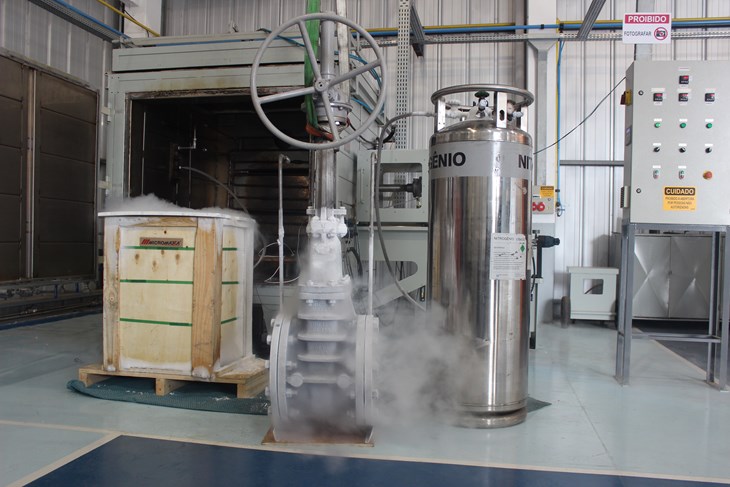
What are some of the different alloys used for cryogenic valves?
The main alloys that are used for cryogenic valves are the stainless steel 300-series (such as 316, 304 321, 347).
Why are these alloys used?
These alloys are largely used due to the lack of a clearly defined transition from ductile to brittle fracture in impact toughness testing.
What are some of the common types of cryogenic valves?
Often, they are the gate valves, but ball valves, globe valves, and check valves have also been used. For example,
Micromazza manufacturers cryogenic gate and ball valves.
Micromazza manufacturers cryogenic gate and ball valves.
Severe service
How do severe service valves differ from cryogenic valves? Or are cryogenic valves considered a severe service valve?
Cryogenic service is considered a severe service. Generally speaking, severe service that occurs with oscillation of temperatures between positive and negative temperature.
What are some end-use applications that would be considered severe service?
Materials for use in H2S-containing environments in oil and gas production.
What are some of the alloys that these types of valves are made of?
We can use carbon and low alloy steels, cast irons, duplex stainless steels, and austenitic stainless according to NACE MR0175.
Why are these alloys used?
They are used if all the requests mentioned in the NACE0175 standard are made. By doing this, we ensure that the valve will not fail due to cracking caused by sulfide stress corrosion cracking (SSC).
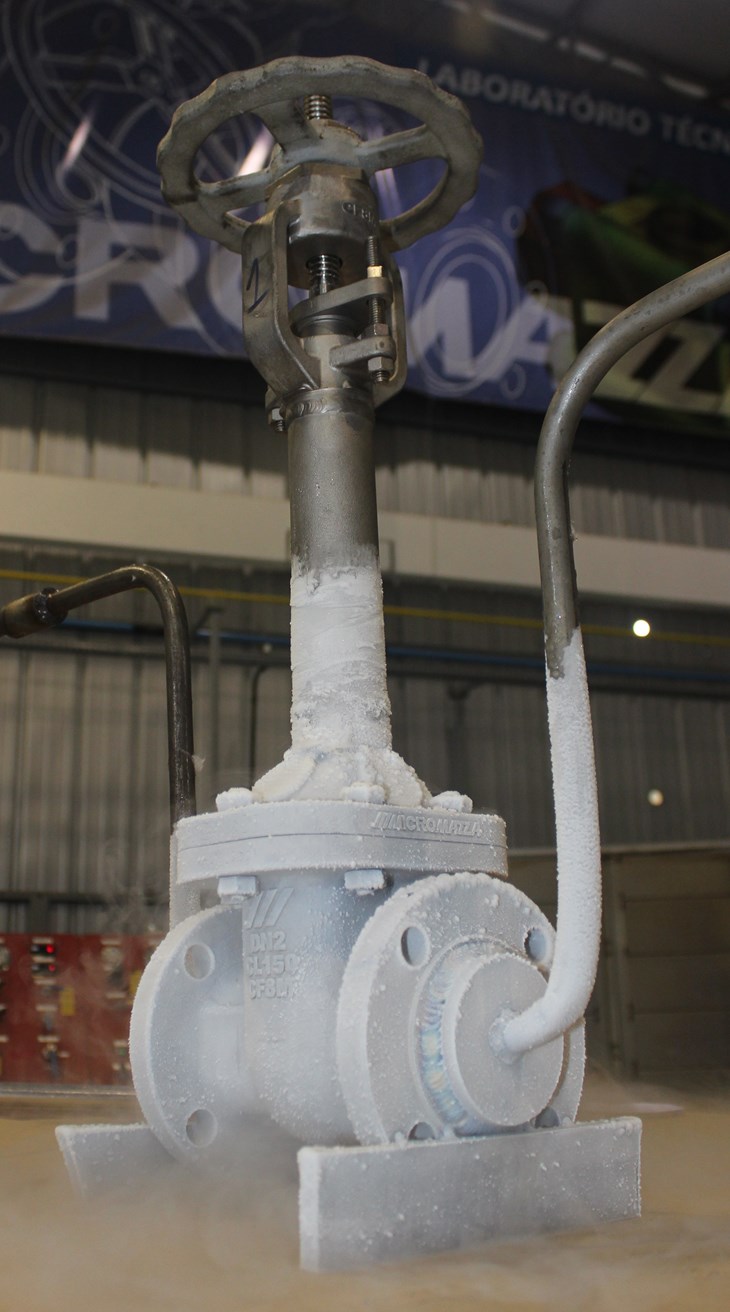
What are some of the challenges related to severe service valves?
The sour gas or hydrogen sulfide (H2S) gas, which is also known as sulfuretted hydrogen. It is considered the second-most deadly gas after carbon monoxide that man can encounter in the industrial environment.
Common in all sectors of the petroleum industry, this gas can be found in oil production and refining processes, sewage systems, the paper industry, groundwater, and a variety of industrial processes. The main challenge related to severe service valves working with H2S is to guarantee or prevent the material failing. Any type of failure in a production line containing H2S can be lethal.
How are these challenges dealt with?
The buyer must have a full understanding of the product. The standards must be applied in their entirety and the manufacturer must supply the product in compliance with all requested requirements. It must always be remembered that we are dealing with human lives and it is our duty to preserve the integrity of every person.
Is the production process different for valves that will be used in severe service?
Yes, it is. For severe services there are specific standards that have been created and improved over the years to improve the process and preserve lives.
Is the testing process any different?
Yes, for some severe services, from the selection of the material to the end of the manufacturing process, additional tests are carried out in order to guarantee the quality of the product. These tests range from the control of chemical composition, hardness, welding control, among other tests.