What are some of the stainless steels and other corrosion-resistant alloys (CRAs) that you have worked with?
Let me first clarify what the CRAs are. The definition of a CRA, as per NACE (NACE PUBLICATION 1F192®) is as follows: “Corrosion-resistant alloy (CRA)” is commonly defined as an alloy with an inherently low corrosion rate in the operating environment of interest, typically much lower than carbon and low alloy steels (e.g. 1–2 orders of magnitude less). However, in cases (based on the service environments) they may be subjected to localized corrosion (crevice and pitting corrosion) or environmentally assisted cracking (such as Stress Corrosion Cracking).
Often service environment and process and design parameters determines the envelope of application of the CRAs. Corrosion resistance of the CRAs is significantly affected by the manufacturing process (cast or forged or wrought product) and welding practices.
Personally, I’ve worked with many CRAs as listed here:
a) Austenitic stainless steels including super austenitic stainless steels, such as 254 SMO.
b) Duplex & super duplex stainless steels such as 2205, UNS 31803, 2507, and Zeron 100.
c) Incoloy® 800, 800HT for reformers in fertilizer, petrochemical, and refining plants.
d) Alloy 625, solid and clad lined constriction for offshore environments.
e) Various other nickel-based alloys, Monel®, Inconel®, Incoloy®, Hastelloy® in fertilizer, petrochemical, and refinery plant applications.
The positive things with these alloys are they’re the best alloys for the intended service. One has to know the design requirements, limitations, as well as the performance of these alloys for an intended service (from an industry handbook or best practice guides, etc.). If the right and best alloy is chosen for the intended service, they may last or outlast the life of the plant.
It’s true for a specific design environment, these could be the choice of using multiple alloys, the designer has to go for the best and optimum choice based on Life Cycle Analysis, cost factor, such as cost of procurement, fabrication, etc. I do not see any major technical drawbacks with these CRAs. When chosen judiciously, they are the best alloys for the chosen or the intended service.
However corrosion resistance of many CRAs at one temperature is not necessarily indicative of their corrosion resistance at other temperatures. Hence a thorough review of performance data is required. All of these alloys are always used for the most demanding services. Hence any failures could be major and serious. Metallurgy of these alloys is never straightforward; a high degree of alloying elements make welding and fabrication complex. For example while welding nickel based CRAs, weld metal segregation resulting in inferior corrosion resistance, chances of forming porosities resulting weld defects, and hot (solidification) crack propensities are common.
Uncontrolled heat input during welding can make duplex stainless grades prone to Sigma Phase Embrittlement. Inconel or higher nickel grades of alloys could be prone to solidification cracks due to the same reasons.
A Welding and Metallurgical Engineer (primarily) as well as the Design Engineer (to a certain extent) has to understand the complex metallurgies involved in these alloys (CRAs). Always CRAs should be fabricated in the correct way conforming to design and operational requirements.
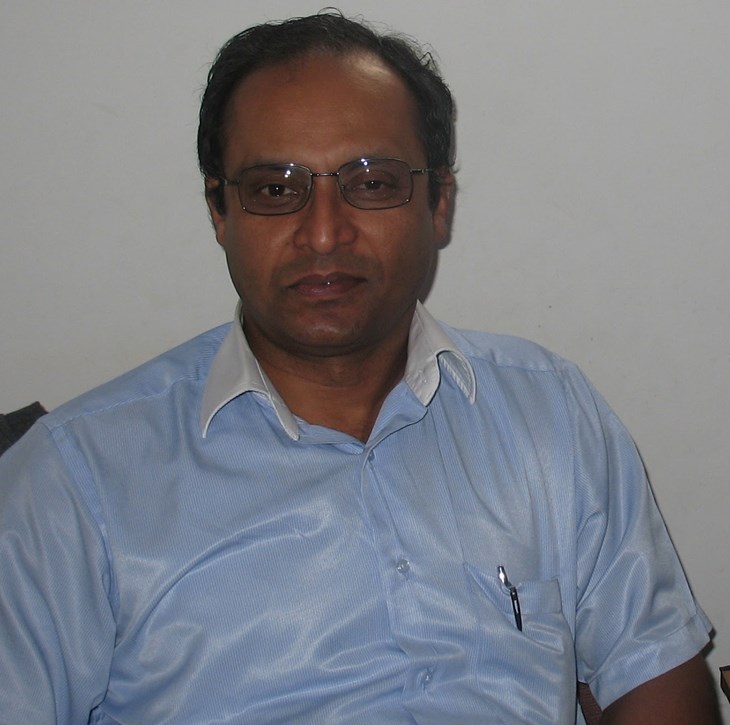
In the welding capacity of being a Welding & Metallurgical Specialist, is there anything in particular you always have to consider when working with stainless steels/CRAs?
Traditionally general corrosion control philosophy had been through good design, for example, adding thicker metals, more corrosion allowances, by adopting appropriate inspection methods, use of protective coatings or corrosion inhibitors, or by the selection of CRAs.
As evidenced, starting in the 1980s, many new oil and gas production environments became too aggressive with respect to the operating environments (deep sea, extremely sour crude and gas) and due to these environmental factors the use of CRAs has increased. According to NACE PUBLICATION 1F192® referred previously, use of CRAs as a corrosion-control method in aggressive oil and gas production environments are now very well established. However, the complexity of the corrosion effects associated with these severe conditions are ever increasing and the metallurgical complexities of the many alloys involved have resulted in challenging materials selection problems for the Metallurgical and Welding Engineer.
Further consideration is also given to the performance of the materials in the welded condition for many applications, as weldments sometimes do not retain the same corrosion resistance as parent materials.
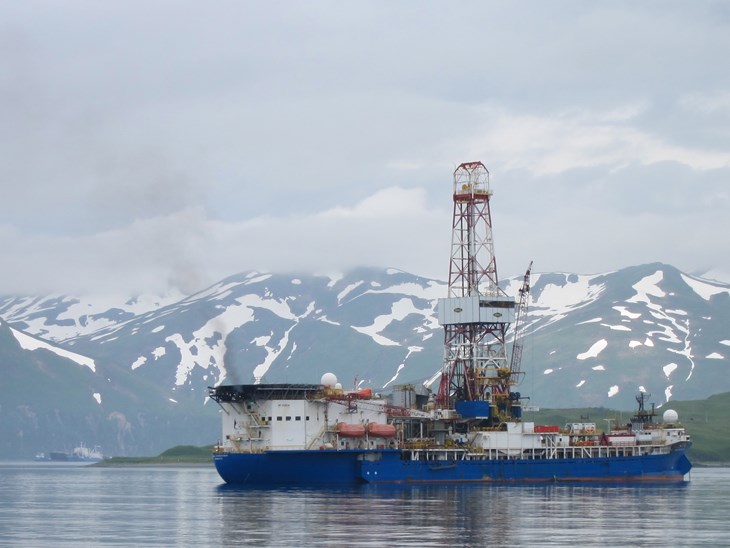
Are there any new grades of stainless steel/CRAs that you have recently started working with or recommending?
Hyper duplex stainless steels are one of the interesting recent developments within the modern duplex family. These duplex stainless steels exhibit both the highest levels of corrosion pitting resistance as well as mechanical strength. Two newly developed grades are Sandvik SAF 2707 HD® and Sandvik SAF 3207 HD®. Hyper duplex SAF 2707 HD (UNS S32707) was accepted and introduced in API-TR-938C, 2015 edition, titled Use of Duplex Stainless Steels in the Oil Refining Industry.
UNS S32654 (654SMO) is another grade of super austenitic stainless steel for demanding offshore applications, which had been in the market introduced some time ago. These grade of alloys are almost competitors to each other in deep sea drilling, exploration, as well as refinery services, though hyper duplex grades may outscore the 654SMO with respect to the higher critical pitting temperature, however welding and fabrication of these alloys are always problematic.
In a few instances, I have come across welding and metallurgical issues related to hyper duplex SAF 2707 and 654SMO. Both alloys require meticulous welding and metallurgical considerations for successful service applications.
Is there anything that you have specifically learned from being a welding engineer that has helped you become a better engineer overall?
One has to understand the basics and has to do an in-depth analysis while dealing with such varied and widely different alloys, design codes, client, and/or project specifications. I’ve learned many such tricks by always keeping up to date in my areas of specialty.
For example, 304L austenitic stainless steel is the very frontline of the 300-series stainless family. This alloy meets Notch Toughness at Cryogenic, Liquid Nitrogen environments – 3200 F (- 1960 C) as well as corrosion resistance in sulfuric acid environments at ambient plus elevated temperatures, meeting requirements of ASTM A 262 Practice E. Corrosion is practically non-existent at the cryogenic temperature. Depending on the design or project requirements, this alloy maybe used both for extreme low temperature as well as for corrosive environments.
But unless one is familiar with the published reports/data sheets of this alloy, recommending this for the correct application would not be safe and advisable. The same rationales are applicable for duplex and super duplex stainless steels also involving various design conditions in upstream oil and gas production as well as the downstream refining and petrochemical industries. The knowledge gained from one type of industry is always transferable to the other type through application of thorough design principles. One only gains all this knowledge through exposure in various industries.
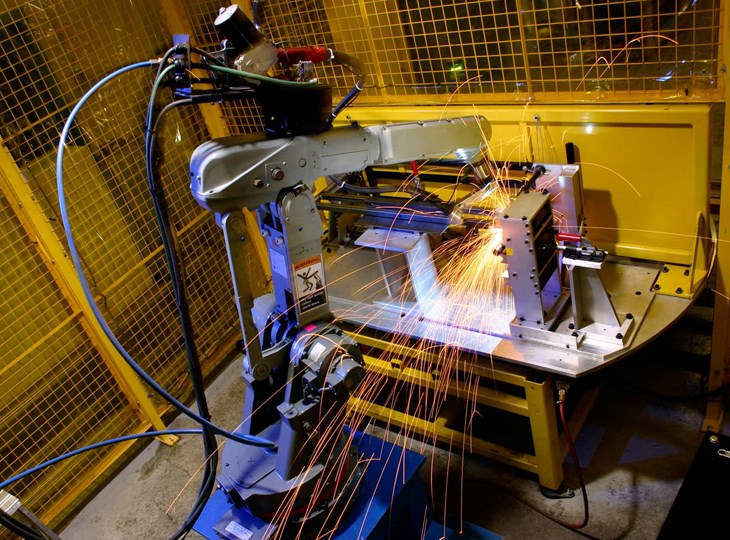
Are there any welding related trends that you have noticed recently?
There is a move towards automation such as robotic welding, etc. It’s good for the mass production industry, which often has less design intricacies. It still remains to be seen if such a trend will really pay off in scenarios where there are complex design conditions and/or metallurgy and welding issues involved.
What three pieces of advice would you give young people who want to become Welding & Metallurgical Specialists?
I would recommend:
1. Having a good understanding of metallurgy, welding, and corrosion engineering issues on various complex alloys that are used in different industries.
2. Having a thorough understanding of design codes and industry practices.
3. Making sure to practice due diligence, which is the most important of all
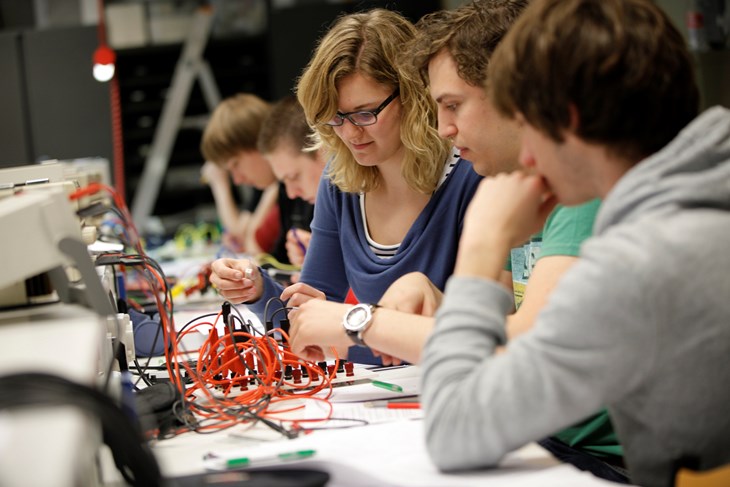