Starting out in the industry
Ana began our discussion by explaining that she graduated as a Material Engineer in Venezuela and shortly after became enamoured with failure investigations. After receiving a full scholarship for the University of British Columbia, one of Ana’s mentors registered her to work on acoustic emis- sions for her Master’s Degree. She detailed that these types of emissions are elastic waves that occur as the cracks propagate or as materials deform, so she spent the next two years listening to the sounds emitting from cracks. Even though she graduated during a recession, she began working on marketing and developing industrial applications for acoustic emission as well as other specialized NDT techniques. Part of her job involved testing aerial devices until she was able to know almost everything about them just from driving behind them. At the time she just considered it a part-time job; she never for a moment thought it would become her career and lifelong passion.
“After that first position I moved on to work for a company that served the industry by performing failure analysis. From there, I was subcontracted by a good friend and mentor who worked at The Dow Chemical Company. The particular project was sup- posed to be just a part time job for approximately three months while a new ethylene facility was beginning operations,” she explained before continuing, “Several years later, my colleagues at Dow advised me to look into IRISNDT, the NDE company that Dow frequently used. That was 20 years ago! I was the very first engineer hired by IRISNDT. Since then, management has sup- ported me on projects which have entailed introducing novel emerging NDT technologies, linking failures, non-destructive examinations, and asset management projects to keep aging plants operating reliably.”
Her current role
Ana’s current role as Chief Engineer involves providing technical oversight as well as insight into the engineering component of IRISNDT’s services. The position re- quires her to always be on the lookout for novel and/or emerging NDT technologies and to determine if there is a way for these new methodologies to become part of the company’s service portfolio. She also, if required, works on tricky evaluations and failure analyses. One of her most import- ant duties, however, is ensuring that as a company everyone thoroughly understands what challenges the customers are facing and how those challenges can be successfully dealt with.
She said that despite what project she may be working on, she always tries to be the best communicator both inside and out- side of the company. Since oftentimes the industry working on pressure equipment integrity deals with such specialized and complex problems involving metallurgy and NDE, communicating the correct information to everyone involved, whether it is a co-worker or a client, is absolutely essential and something she is constantly working on.
A typical workday
An average working day for Ana depends a lot on the season, since her work has a significant seasonal component. During the winter, which is also known as “non-shut-down season” she reviews developments in engineered NDT technologies as well as promoting the company’s engineering and technical capabilities. This includes attending conferences that deal with emerging NDT technologies and/or equipment management. Sometimes she will even present the company’s work at these events. During the shutdown season, she is busiest reviewing and approving technical reports. She also works on di cult technical problems or collaborating with special new clients.
When asked about some of the challenges she is faced with in her role, she is quick to answer, “Making mistakes is a very painful experience for engineers. Yet, trying new technologies entails making mistakes, learning, and then moving-on. Being a nerd, I also have to work hard at understanding people. But with all that being said, I get a tremendous feeling of accomplishment when the team (with all its multiple disciplines) completes a large project or equipment repair. I also get a charge when our client succeeds because of the outcome of our projects. One of my favorite parts of the job though is acquiring new knowledge that fits and fills gaps in the puzzle of materials engineering.”
Working with stainless steels
In her role as Chief Engineer for an NDT company, Ana works with both stain- less steels and CRAs continuously. For in- stance, she cites AISI 304 and AISI 316 as the most common stainless steels she sees but she has also worked extensively with the 6Mo stainless steel alloys, Alloy 20 as well as high temperature nickel castings and wrought materials. She has lots of experience working on ethylene furnaces and with that type of project stainless steels with high nickel contents are considered the “regular workhorses.” For corrosive services (with a pH below fivve or greater than nine) at temperatures greater than 200 oF and pressures greater than 200 psi, she sees stainless alloys as “powerful allies” to help keep equipment operating safely. In flow related corrosion losses, parts constructed out of stainless steel have a much better service life than low alloy steels.
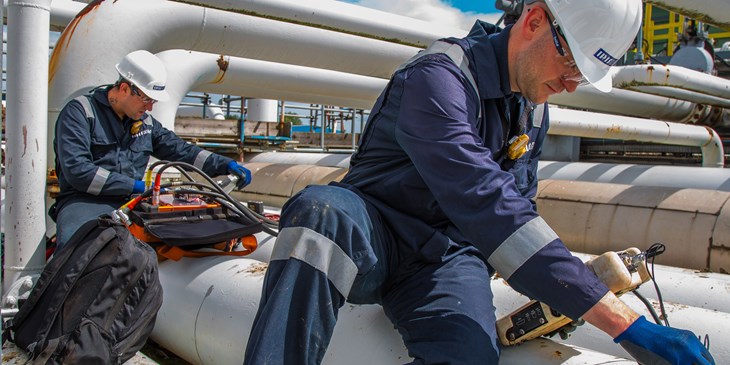
Photo: IRISNDT
NDT methods
She elaborated, “Regarding specific NDT methods, I think that electromagnetic techniques are extremely valuable for evaluating stainless steels. We are used to austenitic alloys having little magnetism, but this little bit of magnetism changes as they age/ corrode at high temperature or as some phases are attacked preferentially. Eddy current inspections of austenitic stainless steel tubes give valuable information as to losses and cracking. In the past, ultrasound inspections of stainless alloys have had limited applications until only recently. New probes have been developed specifically for austenitic and CRA weld inspection and I think we will know just how effective they are soon. Positive Material Identification (PMI) for validation of the materials placed in service is absolutely essential.”
Challenges & benefits
Ana says that one of the challenges associated with testing stainless steels and CRAs for flaws is that with some of the larger austenitic stainless steel grains it can be difficult to use ultrasonic inspection for welds and castings. Another challenge involves phase related embrittlement, which can happen a lot in duplex alloys. This phenomena cannot be identified with conventional radiographic (RT) and ultrasonic (UT) testing methods, which can be troublesome. However, Ana mitigates this by complementing RT and UT examinations with destructive examinations, especially when she is dealing with welds. Experience has also shown her that while working in the field, metallographic replication and magnetic measurements often provide valuable information to help solve a problem. Despite some of these challenges, what Ana really appreciates about testing stainless steels and CRAs is their unique response to corrosive conditions. In particular, she finds the attack of specific phases really fascinating as well as microstructures (both when they are new and as they age) really interesting.
Experience with aging facilities
Another aspect of her job that she finds very interesting, and comes across a lot in her 20 years on the job, is aging facilities. She has worked for several older facilities, such as nickel refineries and plants with gas and chemical reform furnaces, but the most fascinating projects she has worked on involve actually refurbishing and repairing older equipment. In her experience, she has found that the modes of damage in CRAs in aging plants are often very specific. This is why Ana maintains that in order to work on tackling the problem of aging plants and equipment one has to thoroughly understand the service and history to assess the condition of older equipment. Even then, repairs of aged materials can be extremely challenging.
In terms of using materials to help prevent or avoid problems it is important to ensure that parts have an acceptable replacement interval. But even more so than that, Ana stresses that it is crucial for operating personnel to have a clear understanding of the location and type of damage that has occurred over time. Especially in the chemical and petrochemical process industries, stainless steels and CRAs are indispensable. Ana’s best advice for dealing with aging facilities from the NDT perspective is to keep in mind that as equipment ages, more and more maintenance and regular checks are required; diligence is definitely key. It’s also important to be open to how new technologies can help to keep equipment reliably running.
The future of NDT
She also stated that she has had to keep an open mind in her career as NDT has been going through a “never-ending evolution” since she first started in the industry. She elaborated that computers first allowed engineers to evaluate much more data than ever before. Currently, Ana and her co-workers are able to obtain images that provide the best and most prompt descriptions of damage. In addition, even historical information can be examined and compared, which wasn’t easily accomplished before current technological advancements.
Ana ended our discussion by stressing that even though we live in a technological age that allows NDT to go places it never could previously, “Testing personnel still have a key responsibility with the digital data that is allowing us to communicate more easily. I specifically have in mind the amazing images that we get from digital detector array technology on the integrity of piping components. Also, the clear aw boundaries now outlined by Total Focus Method Phased Array UT technology promise to help us to ‘see’ flaws and metal losses more clearly with images instead of with words. NDE technologies change very quickly, but I look forward to seeing what is next.”