By 2030 there will be over 200 million tons of hydrogen produced under the Net Zero climate change program. Hydrogen sales will generate revenues of over $400 billion USD, and also generate stainless steel sales for hydrogen production.
By Bob McIlvaine, The McIlvaine Company
The IEA forecast for 2030 projects electrolysis as the largest production mode followed by fossil fuels, mostly natural gas, and without carbon capture. An equal amount will be produced with carbon capture and sequestration. A relatively small amount will be produced with carbon capture and beneficial utilization.
McIlvaine believes that biomass including waste can be a significant source of hydrogen. An analysis has been prepared based on 20 million tons of biomass based hydrogen by 2030.
Stainless steel for tanks, piping, pumps, valves, piping scrubbers, and electrolyzers could account for $2 billion USD in stainless revenues per year by 2030. One variable is the mix of technologies. The relative stainless steel revenues per ton of hydrogen for electrolyzers is tiny compared to fossil with CCS. Electrolyzers will not be a significant source of stainless steel revenue compared to the other production sources.
The stainless steel market will be a function of the production technology choices. Relative stainless purchases have been compared for production, carbon capture and sequestration, transportation including liquefaction and storage.
Stainless purchases for the production of electricity using solar energy and electrolyzer technology are rated as the base number. Since ten times more is spent on the transportation and storage, there is no need for carbon capture. The total stainless purchases are 11 times the purchases just for production.
Most renewable technologies, other than biomass, have no need for carbon capture and sequestration. Biomass has the highest total investment in stainless but it is carbon negative. In terms of the total stainless market to meet net zero BECCS results in less stainless needed.
Ammonia is a special case. Production costs are high but carbon capture and sequestration costs are relatively low. Transportation and storage costs are also relatively low due the avoidance of liquefaction and other challenges moving hydrogen.
The forecast of $2 billion USD in stainless sales is based on the mix creating a relative stainless investment of 20 in 2030. Since the potential total ranges from 11 to 40, the production choice will be a big variable. Likely yearly stainless sales could be as low as $1.8 billion USD to as high as $2.4 billion USD. The extremes would be a low of $1.1 billion and a high of $4 billion USD.1
It is difficult for purchasers to select the best materials for these applications due to the lack of experience in this field. There is a hierarchy in the value of the type of cost factor which can be communicated. The following is a list from lowest to highest:
- General cost factors: The evaluated life is one example. Since the life of a specific stainless steel depends on the alloy percentages, this factor is important in the selection.
- Specific process cost factors: Fluctuations in temperature and time interval between repair or cleaning opportunities is important in product selection and cost.
- Product task cost factors: At the next highest level there are factors associated with the product task e.g. larger sized couplings, pumps, and valves needed due to the nature of the hydrogen gas. There are selection challenges for the very low temperatures of cryogenic hydrogen. Where should metal be selected over composite materials?
- New unresolved cost actors: Most of the factors regarding materials of construction, and sizing are unresolved because of the fact that many of the applications are new. You can not necessarily assume that the factors long established relative to refinery hydrogen are applicable to these new applications.
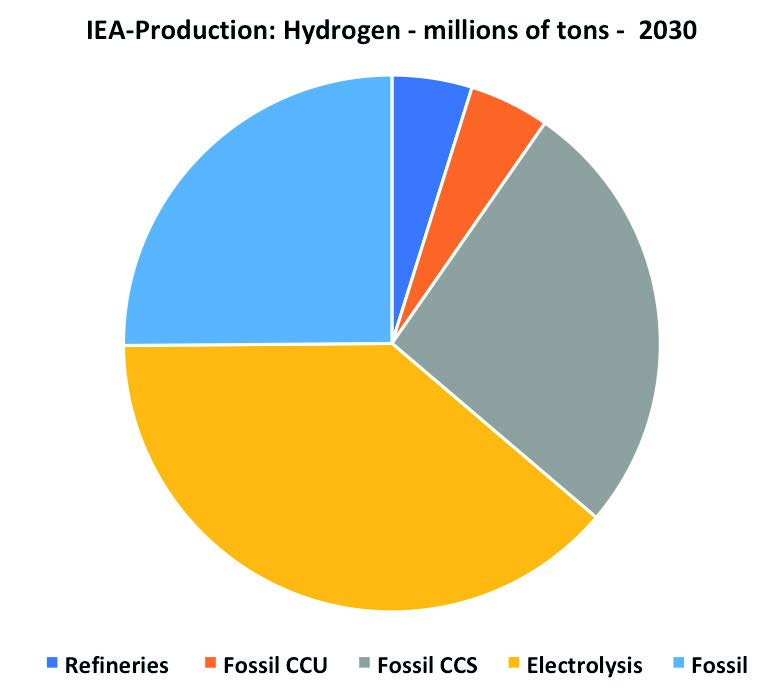
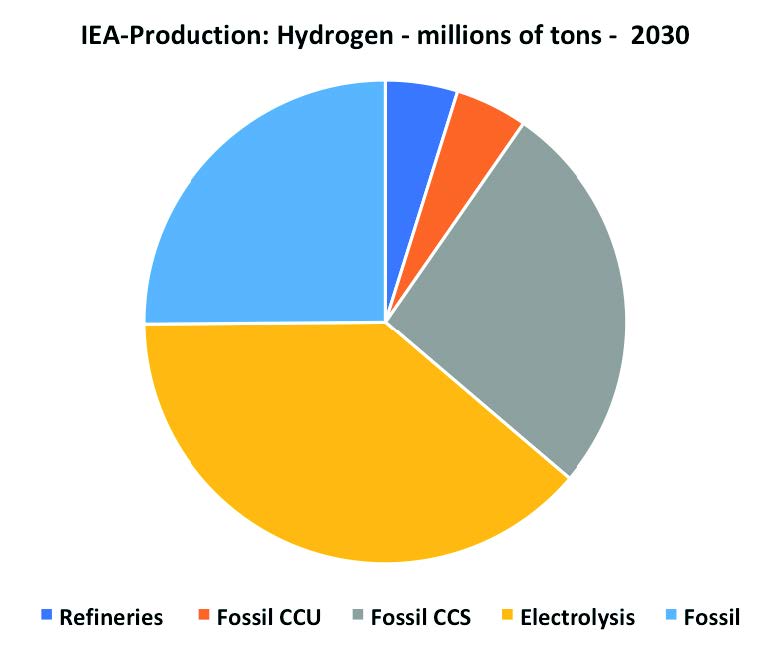
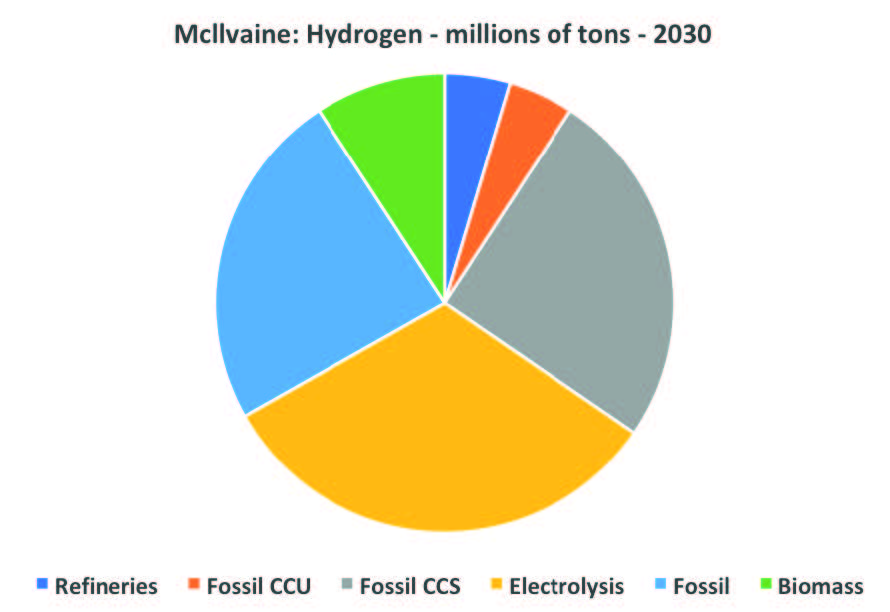
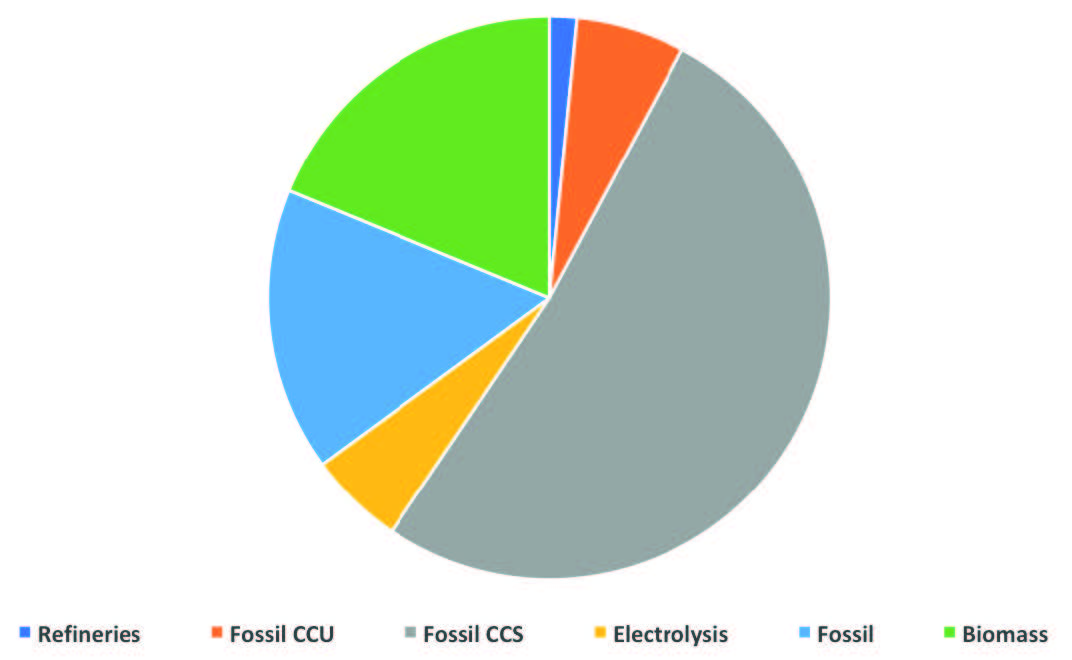
In the case of hydrogen from coal, it was found that in the SO2 scrubber alloy 2205 was adequate to resist acid corrosion in general. But with gypsum buildup on the scrubber walls concentrated acid was formed and resulted in crevice corrosion. Higher nickel alloys were then required.
- Disputed Factors: Generally acceptable materials for compressed hydrogen gas include austenitic stainless steels, aluminum alloys, copper, and copper alloys. In general nickel alloys are avoided because of embrittlement. The steel selection for a particular product such as a compressor creates a series of requirements. These result in disputed claims as to which combination has the lowest total cost of ownership.
Each supplier provides reasons why his product offers the lowest total cost of ownership. The purchaser is challenged to sort out which claims are most accurate. This challenge is best met by connecting the suppliers, users, consultants, and media in an organized way through the Industrial Internet of Wisdom. Future articles in Stainless Steel World Americas will focus on these disputed factors based on supplier and expert input.
References
1. Stainless Steel World Markets published by the McIlvaine Company.
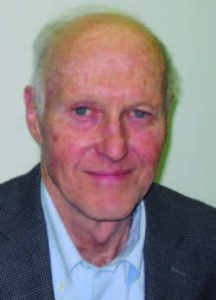