The current global consumption of materials is not sustainable; hence, the longevity of applications is crucial. Similarly, carefully designing the applications by utilizing higher strength material, resulting in less material used, is contributing to a lower consumption of resources and a reduced carbon footprint.
By Joachim von Schéele, Global Director Commercialization at Linde
The Green Transition
Stainless steel is furthering the transition towards sustainability in three different ways:
1) Applications with a long lifetime and a low carbon footprint over time
2) Production of fully recyclable applications with recycled materials
3) Stainless steel-produced solutions for a green transition and decarbonization
Accordingly, stainless steel is positioned to play an important role in the green transition; however, there is still a need to leverage its advantages in current applications by pursuing improvements throughout its production chain and to develop new uses aligned with the green transition.
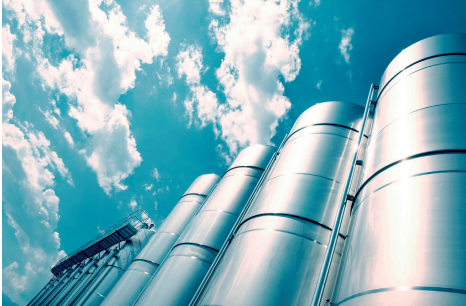
Choosing Green Inputs to Production
Naturally, a short-term approach to decarbonizing the production process would be a focus on improvements and minor alterations compared to mapping out longer-term options. There are immediate actions relating to procurement, operation practice, and use of proven technologies that can be implemented to reduce the carbon footprint.
Stainless steel’s carbon footprint can vary greatly based on the raw materials that are used during production, the percentage of scrap melted, use of carbon-free electricity, and so forth. Regardless of the route, the largest CO2 emissions in stainless steelmaking are found in Scope 3, which is associated with primary raw materials like chromium, nickel, molybdenum, lime, and so forth. These materials are needed for production and meet the alloying materials specifications.
Due to the increase in stainless steel production and consumption, there will be a need to use relatively pure iron units and primary alloys in the charge mix as forty to fifty years ago, there was less production of stainless steel. Stainless steel can now be recycled in the form of scrap; therefore, reconciliation of the balance will involve iron and primary alloys. This requires special attention concerning so-called Scope 3 emissions, i.e., emissions generated in the upstream production of these input materials. The greenhouse gas (GHG) emissions from primary alloys like nickel, molybdenum, and chromium could be substantial. Not only are these valuable alloying atoms traded in different forms like electrolytic nickel, iron-nickel (FeNi), nickel pig iron (NPI), ferro molybdenum (FeMo), molybdenum oxide (MoO), and so forth, but the impact of their respective production varies greatly.
There are many aspects to consider when it comes to the GHG inventory of primary alloys. This is not limited to the influence of the metallurgical extraction process where the alloy is produced from its ores but impacted also by the ore type, as well as the kind of energy used in the process from mining to alloying material ready to use in steelmaking operations. In steelmaking operations, besides the choice of raw materials, there are issues with efficiency, such as energy consumption, the consideration of yield, and how the operations are influenced by the process technology employed. Yet another key factor is the source of energy, such as fossil fuels or energy from renewable sources. These are some of the factors to consider when evaluating the GHG emissions from steelmaking operations, and therefore its sustainability. The reduction of GHG emissions will be an important consideration for many years to come.
Accordingly, it is very important that attention is paid to the carbon footprint when procuring alloys because those alloys could be a large contributor to the stainless steel product’s eventual carbon footprint. A study conducted at the Royal Institute of Technology in Sweden evaluated the impact of nickel supply and it showed that NPI, for example, carries a large carbon footprint – about five times that of the lowest CO2 emitting alternative for nickel supply. Accordingly, from this perspective, the NPI material should be avoided as much as possible. Some other observations on the carbon footprint relating to the choice of alloys include the use of nickel from sulfide ores instead of laterites, and, if possible, replacing nickel with manganese.
Using green power based on renewable energy sources is an obvious step that can be taken wherever possible. The biggest consumer of electricity is the electric arc furnace (EAF). Employing green power in the EAFs could decrease CO2 emissions across the Americas by 50-200 kg per ton of steel produced, depending on how the electricity is produced at the specific location. Naturally, green power should also be employed to produce the industrial gases used (oxygen, argon, and nitrogen).
Another action that instantaneously results in a reduced carbon footprint is the charging of more scrap. Scrap is defined as ‘carrying zero CO2’; however, all alloys ‘carry CO2’ from their upstream production. The recycling rate of stainless steel is usually quite high, largely driven by the intrinsic value of “end-of-life” stainless steel products. The collection of scrap and sorting according to alloy content is paramount in retaining the intrinsic value of the alloying elements. The obvious risk is that valuable alloy atoms are lost due to dilution if the categorization and sorting of scrap is not up to the task. This is naturally something that will require attention from all actors in the value chain, from collecting end-of-life scrap all the way to the melting furnaces.
Stainless steel producers are carefully looking into their inputs of raw materials and energy and are creating “green brands” as a result of that. One example is Outokumpu, which has introduced a low carbon footprint family under the name Outokumpu Circle Green where the Scope 1 and 2 emissions have been reduced by 95% and the overall footprint is up to 93% lower than the global average. The chart below shows the CO2 footprint of stainless steel produced in different parts of the world with various contents of recycled material.
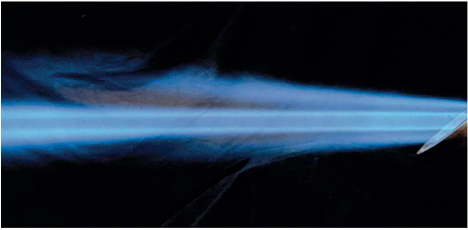
Towards a Greener Production
Short-term approaches to decarbonization are focused on improvements and minor alterations. However, any technology change today should take the future into account, like being ready for the use of hydrogen for example. Increasing energy efficiency immediately reduces the carbon footprint. There are four processes to address: (1) the EAF, (2) the argon oxygen decarburization (AOD) converter, (3) ladle preheating, and (4) reheating and annealing.
EAFs are the biggest consumer of electricity. However, there is also additional energy input to consider, which supports melting and refining using oxyfuel burners and injection lances. CoJet technology has revolutionized EAF operation. Today, more than 170 EAFs use CoJet. The AOD process is used today for more than 75% of the world’s stainless steel production. However, to be efficient it requires a sophisticated control system, such as the Intelligent Refining System (IRS), which was introduced in 1995 and is successfully in operation at more than 100 AOD converters, ranging from three tons to 120 tons and found across 12 countries. The improvement in AOD process efficiency and productivity results in a lower tap-to-tap time and a lower carbon footprint.
To achieve preheating and reheating with a low carbon footprint – and ultimately bring it to zero – the first step involves increasing the energy efficiency. Flameless oxyfuel has demonstrated the ability to reduce the fossil fuel consumption in ladle preheating and reheat furnaces by 20-60%; it is a well-established solution that has led already to considerable decarbonization. Ladle preheating using flameless oxyfuel achieves shorter heating times, lower NOx emissions, more uniformly heated ladles, longer ladle life, and, if desired, higher preheating temperatures. Partial or full conversion of reheat furnaces from air-fuel to flameless oxyfuel combustion is not only a relatively easy first step to decarbonization, it also prepares the furnace for subsequent hydrogen fuels.
The world’s first heating of steel with 100% hydrogen as fuel was carried out in Sweden in March 2020 with 25 tonnes of ball-bearing steel ingots heated in a pit furnace fired with hydrogen oxyfuel using REBOX Hyox technology. After heating and soaking, the ingots were successfully rolled to bars in the rolling mill. A thorough inspection and analysis of the rolled bars showed that heating using hydrogen as fuel does not impact the quality. Based on this success, a permanent full-scale installation of REBOX Hyox at Ovako’s Hofors mill was commissioned in early 2024 in a total of 24 pit furnaces, where both the oxygen and the hydrogen are produced using renewable energy.
In parallel, several similar full-scale tests have been carried out with REBOX Hyox on stainless steel ingots. These tests were successful, and no negative impact on the material was identified. Another example of early use of hydrogen is in the cutting operation at continuous casting. Full-scale tests have successfully confirmed the advantages of using hydrogen-oxyfuel at the cutting. Excellent results included the ability to cut with twice the speed when using only half the power. Accordingly, using hydrogen could not only support decarbonization but also improve the operation.

A Sustainable Material with Green Applications
Stainless steel is a superior, durable material that requires low maintenance. The carbon footprint from applications can be reduced due to lack of surface treatments and repairs over its life cycle, but the carbon footprint can be low from the start depending on how it is made.
Stainless steel has inherent properties that make it suitable in structural and infrastructural applications. Corrosion properties have historically been the main driver behind the use of stainless steel, along with hygienic and esthetical properties. In dynamic applications like transport tanks, maintenance and other corrosion-related properties are important, as well as the mechanical properties that allow for lighter construction, and thus higher payloads. In this type of application, the fuel consumption in use is a factor that contributes to the competitiveness of stainless steel from a sustainability and life cycle analysis perspective. In “static” applications like buildings, bridges, and storage tanks, the maintenance cost is typically one of the drivers behind using stainless steel along with the mechanical properties that allow for weight reduction. Thus, stainless steel uses less material to achieve the same functionality as alternative materials. The maintenance costs usually relate to the corrosion properties, i.e., less need for corrosion protection and longer service time. The energy consumption in use is normally not influenced by using stainless steel in these applications.
Conclusion
Today, we already see applications that have the potential to exploit the benefits of stainless steel. In the automotive industry, the transformation to battery electric vehicles will provide opportunities for an increased use of stainless steel due to their mechanical properties and tensile strength. Lately, the importance of fire resistance has been pronounced. Stainless steel is particularly well suited for the battery compartments that house lithium-ion batteries; crash safety and weight saving are important, but an even ore critical role that stainless steel plays is the heat resistance in case of fire. Cathode material for fuel cells is already being produced from stainless steel and could very well increase the demand for stainless steel in the future. Moreover, to produce the hydrogen needed for fuel cells, stainless steel will be an important construction material in the design of electrolyzers, where high temperature stainless steel could also be of interest. And in the fuel cells themselves – cars or stationary systems – stainless steel precision strips are being increasingly used.
From a life-cycle perspective, stainless steel can often be considered a preferred option compared to competing materials. But there are large opportunities to strengthen the position further by carefully selecting input materials, using green power, improving its production, and so forth. Moreover, due to its superior sustainability properties, stainless steel also can be further leveraged in current applications. It has a bright future in new uses aligned with the green transition.