A new zinc chloride-based solder paste that works on hard-to-solder 316 stainless steel alloy has been developed. The paste consists of powdered solder alloy suspended in flux paste with binders. The solder paste can be heated rapidly by torch yet is stable enough to be heated for long periods of time in an oven. The bond strength of the soldered connection is very strong and, in some cases, exceeds the strength of the underlying steel.
By William F Avery, Dr. Y. Baskin & Rebecca Zronek — Superior Flux & Mfg. Co., USA
A stable stainless steel soldering paste has been needed for some time. While there is great liquid and paste fluxes for soldering stainless steel, there has not been stable and sufficiently strong solder paste products to do this work. There are several considerations regarding this:
- Simple conversion of flux in paste form to solder paste does not work because the chemistry of these fluxes will often result in the flux attacking the solder powder owing to the activity of the flux.
- An ideal stainless steel soldering paste can be heated rapidly by torch.
- An ideal stainless steel soldering paste can be heated in long heating processes such as in ovens and be able to solder connections after long heating periods.
- The stainless steel used in this test was 316 stainless.
- The solder used for evaluation was 96.5/3.5 tin-silver, often used for stainless steel connections.
- The completion of this test compares the resultant new proposed solder paste to the best liquid flux we have for stainless steel soldering, and to another alternate zinc chloride-free stainless steel soldering paste.

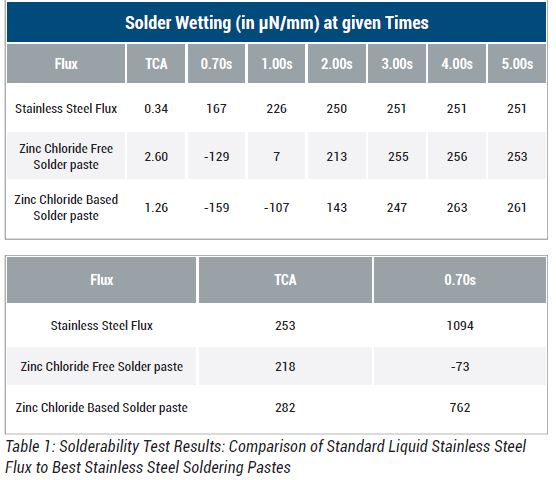
New Development Work
Deciding on an Activator Package
Step 1: Development was concentrated on improving soldering to stainless steel. Several formulations were developed to determine the best mixture of ingredients (particularly activators beyond the zinc chloride) to maximize the mixture as a paste. One mixture was found to be stable with the solder powder.
Step 2: None of the formulations, when made into solder paste, were capable of soldering stainless steel, suggesting that other chemical activation schemes were needed.
Step 3: The next test looked at altering the activating scheme and changing the paste consistency. A different acid choice was used along with other activators. The paste chemistry was altered to make a more fluid flux paste formulation. Figure 1 shows how the pastes looked when soldered to stainless steel using hot plate heating at 350°C. The results were quite dramatic; see Figure 1 (A)-(D).
Reducing Solder Paste Splattering
Because of the chemistry used with this solder paste, it was necessary for some water to be present. Pastes made in the previous section had intentionally too much water added, simply to ease the creation process. The series of successful fluxes created in this round were then tested via the solderability tester to measure their viability. The best visual (the least amount of splattering) and mixing result (went into solution the easiest) was found to be the new solder paste shown in Figure 2.
Testing the New Soldering Paste
The new soldering paste has been tested, as described previously, by a simple tensile test and by solderability testing. The test results are shown in Figure 3.

Tensile Strength
A simple tensile strength test was carried out to measure the overall strength of the solder bonds with the new stainless steel soldering paste. An interference joint was created by soldering one strip of stainless to another using the solder paste and torch heating. The tensile tester was used to pull on the parts until there was a break in the solder connection, or a break in the base metal strip.
Solderability Tester
The solderability tester measures the interfacial force between molten solder and the specimen being soldered, in essence, measuring the ability of the solder to flow on a surface. A common definition of solderability is “the ability of a metal to be wetted by molten solder”. The solderability test is unique in that it permits the simultaneous evaluation of base metal, solder, flux, and temperature to determine the effect of these factors in the soldering process. Three of these factors are held constant, while the fourth is the measured variable.
In the test, a fluxed metal strip specimen is held above the molten solder and connected to a load cell. The solder pot is raised to immerse the specimen to a preset depth below the solder for a set period of time. The load cell measures the weight change as solder draws up the test specimen. The weight difference is converted to wetting force by an online computer analysis. The solder pot then is lowered at the end of the immersion cycle, pulling the specimen out of the solder.


To evaluate the results, the height of the curve within the immersion time of the solderability test dip is measured in terms of wetting force. The wetting force is a measure of the extent of solder flow. Greater solder flow will result in better soldering.
Solderability Test Terms
Time To Cross Axis (TCA) – Time, in seconds, needed to achieve positive solder wetting. This is the measure of how fast the solder will start to spread on a surface.
Solder Wetting (in μN/mm) at Given Times – Wetting force expressed in micronewtons / millimeter (μN/mm) at the time indicated in the solderability curve.
Maximum Wetting (MW) – Maximum force; expressed in micronewtons/millimeter (μN/mm), in the positive solder wetting region of the solderability curve. This is a measure of how far the solder will spread on a surface.
Integrated Area Under the Curve (IA) – The area between the curve and the x-axis during the entire immersion cycle. The area is recorded in units of micronewtons/ millimeter-seconds (μN/mm-sec). This measure combines the effects of both maximum wetting and time to cross axis to give a single performance value.

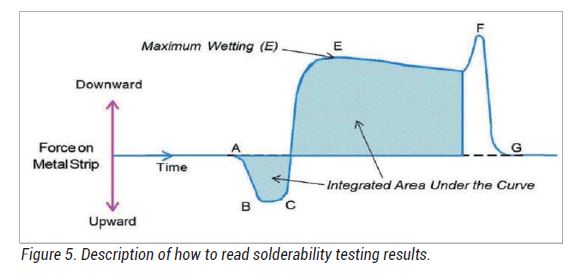

Conclusions
As a result of the testing described in this article there is now a better soldering paste for soldering stainless steel available. The new zinc chloride-based solder paste Has faster positive solderability than the previous zinc chloride-free solder paste used for this application, and, equally impressively, the new solder paste has maximum wetting like that of the strong stainless steel liquid flux.
The new zinc chloride-based solder paste has the advantage of being much more like the highly active corrosive liquid fluxes typical of this application. Unlike the earlier zinc chloride-free solder paste used for this application, this new soldering paste can withstand torch heating and long oven heating processing. This new solder paste works on 316 stainless steel and all other easier to solder steels and metals.