Rajan Bhambroo received his Bachelor’s Degree in Metallurgical Engineering from PEC University of Technology, followed by a Master of Technology (M.Tech.) Degree in Corrosion Science Engineering from The Indian Institute of Technology Bombay. After working for a chemical company in Japan, he came to the U.S. and obtained another Masters Degree in Materials Science and Engineering from The University of Michigan Ann Arbor. Currently, he works as a Materials Engineer at Tenneco Inc., with a strong emphasis on material characterization and corrosion testing of components which are formed from a variety of materials such as stainless steels, aluminum alloys, cast irons, and alloy steels. Stainless Steel World Americas asked the expert several questions to gain insight on the role of material characterization in terms of testing, corrosion, and more. Readers are encouraged to send their questions to the editor to be featured in an upcoming Q & A article.
By Sara Mathov
Armstrong has been working in the procurement industry for several years. She joined the Joule Processing team in 2018 and has had a primary focus on procuring materials and applications such as stainless steel and heat exchangers, for midstream applications involving natural gas.
Since working at Joule, Armstrong progressed from her initial position as a Project Coordinator to Procurement Lead, before taking on her current position as a Projects Control Manager. Although her role as a project control manager focuses more on project management than procurement, Armstrong’s multiple years as a procurement lead has made her an expert on the current ins and outs of the procurement industry.
Q: What are some of the things you oversee in your role?
A: I am a part of the centralized analytical research group which is responsible for material analysis and characterization support to various business units within the company portfolio. The background of the projects that I work on varies quite a bit based on the business units and the larger program that the work comes from. Sometimes, I am working on material characterization for new product developments, while at other times the project might involve material characterization for process validations at the plant level or failure analysis or inspection from component testing at the customer facilities. Another major aspect is the failure analysis work on parts from in-service failure to understand why the failure occurred and providing root-cause analysis and feedback on how to improve the products from a materials engineering standpoint. These component may be made from a wide variety of materials such as ceramics, stainless steels, to basic steels, and cast iron. These components might also have a functional coating which helps improve the performance of the component in the application.
Q: Why is stainless steel used in the projects you are involved in, and how is it used?
A: Stainless steels are generally used where we want a combination of good mechanical properties, corrosion resistance, and good manufacturability. Different applications require different grades of stainless steels in varying shape and forms. Stainless steels are used in gaskets, gasket assemblies, and where the temperatures are high and the material gets exposed to oxidation conditions.
These components may have stainless steel coupled with a coating which may be organic or inorganic in nature and is required for functional properties. My work is based on material characterization of components, whether it is the substrate or the coating, depending on the nature of the issue faced by different business units.
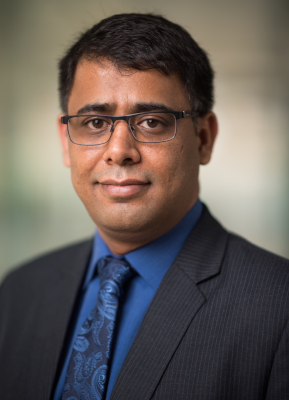
Q: What kinds of grades and alloys do you use?
A: The grade of stainless steels and other alloys used is highly dependent on the application since the material properties required will depend on the mechanical properties and corrosion resistance required to perform in the service environment. Generally, austenitic stainless steels are used but the exact grade of material varies depending of the application. Components are made from 302, 304, 316 grade stainless steels but some components might have different compositions which have been developed in-house for certain applications. In other applications, sometimes high strength materials are required, so martensitic stainless steels such as 400 grade or precipitation hardenable stainless steels may be used. The exact grade depends on the applications requirements.
Q: What types of testing do you perform?
A: There is no ‘one size fits all’ kind of test.
The nature of characterization technique or material testing depends on the kind of information required to establish structure-property correlation for product development or resolve an issue faced at the plant or customer level. There are times when it is needed to simply analyze the microstructure of the material and relate it with the mechanical properties observed for the components. At other times, as a consequence of the various processes such as welding, rolling, forging, etc., the microstructure of the material might change, making it necessary to establish variation of the mechanical properties as a function of the microstructural changes in the material.
Generally, we start with the visual/optical examination of the parts to determine what we need to examine and create a roadmap to conduct various tests and analysis for material characterization. For microstructural characterization, Optical Microscopy, Scanning Electron Microscopy (SEM) coupled with Energy Dispersive Spectroscopy (EDS), X-Ray Diffraction (XRD), and X-Ray Photoelectron Spectroscopy (XPS) are used to characterize materials. This does not mean that all of these techniques are used on each and every stainless steel sample generated.
Optical microscopy is useful for getting information regarding the microstructure of wide area regions. It helps understand the general microstructure of the material whether it is austenitic, martensitic or ferritic. But the material may also contain different kinds of secondary phases such as precipitates, carbides, inclusions etc., which are generally smaller in size (less than a few μm in diameter) which can not be effectively observed using optical microscopy. In such cases, an electron microscope is utilized to observe microstructural features at a much higher magnification of upto 100k (or even higher), as compared to the magnification of 1k which is generally available on the optical microscope. Another benefit of electron microscope is that these instruments are generally equipped an energy dispersive spectroscopy (EDS) instrument which helps in chemical analysis of the precipitate, carbide being analyzed.
X-Ray Diffraction (XRD) techniques are utilized to understand the phase composition of the material. It is particularly helpful when there is small secondary phase present in the material which is chemically similar to the primary phase and thus cannot be easily distinguished by SEM-EDS. A good example of this is presence of austenite in martensite matrix for precipitation hardenable stainless steels. X-Ray Diffraction (XRD) analysis is used in such situations since this technique can distinguish based on the difference in the crystal structure of the two phases. As long as the secondary phase is more than a certain threshold (about 1 %), the technique can be used to identify the phases present in the material both qualitatively as well as quantitatively. In addition to applications for stainless steels, we use this technique extensively in phase identification since the presence of the correct phase at all stages (raw material, processing stage, final product) is critical in obtaining the desired performance in the product.
Another technique that I employ for material characterization, specifically surface characterization is X-Ray Photoelectron spectroscopy (XPS). When analyzing coatings, generally, the material is prepared along the cross-section and analyzed using SEM. However, SEM would provide us with information on the morphology or the layer structure of the coating present, whether it is single layer or multi-layered. To see the variation in the coating chemistry as a function of depth from the surface, XPS is utilized in our group where we analyze the first few atomic layers of the surface and then etch the surface to remove a known depth of coating and then analyzing the newly formed surface again to obtain the coating composition at that location. Progressively etching and measuring surface chemistry using XPS allows us to generate a depth profile which us utilized in understanding the coating composition, particularly in multi-layer coatings. This is of critical importance since the different layers in the coating perform specific functions and having the right chemistry in each individual layer is critical in getting the overall performance from the coating and thus the component.
In addition to these characterization techniques, other material testing such as mechanical testing, thermal testing, tribological testing is also performed as needed by our group.
Q: Are there specific types of corrosion testing performed?
A: There is no specific corrosion testing, as most of the work is from a material characterization/failure analysis point of view. If a component is returned to us for failure analysis and it shows sign of corrosion taking place, the first thing we do is identify the corrosion product that are formed on the surface of the metal to identify what type of corrosion products are formed during service. To this end, we use SEM-EDS and XPS to identify the surface chemistry of the corrosion products. Corrosion testing is carried out only if the business units want to understand the corrosion behavior of the material in a particular service environment.
Q: Are these types of tests destructive, or non-destructive?
A: It is most often a mix of both. If you are looking at the cross section, then you have to cut the samples, which is destructive. Just looking at the surface is non-destructive.
Q: Are there benefits to one type of testing over another?
A: Most of these analytical techniques for material characterization are complementary to each other. The selection of a particular technique or a set of techniques is dependent on what information we want to obtain. For microstructural analysis, Optical microscopy, SEM-EDS and X-Ray diffraction are used to identify the material. But if the area of interest is closer to the surface and analysis of phases and chemical composition is desired, for example in case of coatings, then X-Ray Diffraction and X-Ray Photoelectron Spectroscopy (XPS) in combination with SEM on the cross-section is better choice.
The functional properties of a component are dependent on the material used to fabricate the part. But the material properties are highly dependent on the chemical composition, fabrication process, and heat treatments that are given to the part. To obtain the optimum functional properties in a component, a good understanding of the material microstructure is critical which necessitates in depth material characterization.
Q: How is sustainability impacting operations?
A: From a sustainability point of view, several companies are working on streamlining their processes and reducing waste. Often, companies are working on getting the failure and reject rate as low as possible, to reduce waste of metal. From a metallurgy point of view, we do not want to waste precious metal, which can be used for other purposes.
Q: What are your thoughts on the future of the industry?
A: Renewable sources or cleaner sources of energy will become more prevalent in the coming years, and this development will require greater emphasis on the material characterization to understand the material behavior in these conditions. For example, development of hydrogen engines would need understanding of how the material behaves at high temperatures in a hydrogen environment. Hydrogen embrittlement is an issue in stainless steel components, so the stainless steels and other alloys which are currently in use in Internal combustion engines, will need to be evaluated for microstructural changes during long exposures to high temperature hydrogen environment.