Reduction of overall maintenance costs for critical equipment has been the need of the hour with many high temperature applications. The service conditions seen in many high-temperature applications are extremely aggressive. The life for a high-temperature component is often relatively short compared to applications at ‘normal’ temperatures. Replacement of high-temperature components is therefore often necessary during expensive planned maintenance breaks. Unplanned maintenance breaks that are required when a component failure occurs are increasingly costly to implement. Specially designed high temperature grades can increase the service life of many components and improve the overall productivity of the equipment.
Venkat Ramesh, Global Product Manager (Heat Exchanger tubing) and Shabareesh Nair, Director (Technical Marketing Asia) Tubacex Group, Spain
Obstacles in High Temperature Applications
Some of the common obstacles in high temperature applications include cracking of tubes in the application, the wall thickness of the tubes tends to reduce in size, sometimes the surfaces develop scaling and lastly these components can also demonstrate erosion and corrosion. These obstacles typically occur when the production produces solids from the process and erosion occurs due to solid particles from the process. Hot corrosion often causes oxidization, carburization, sulfidation, and nitriding. Low creep resistance of the tubes is also an obstacle users experience.
Hot corrosion occurs when service conditions become more aggressive and effect the tubes at temperatures above 400º C. Apart from this, the creep strength of the material becomes a de-sign factor and may not yield the needed strength. Normal temperatures and structural stability of the material become very important.
For example, Tubacex high temperature grade (Tubacex TX 253 MA®) is suitable for many high-temperature conditions. These tubes can provide substantial savings by increasing the service life of many components as compared to other standard stainless-steel grades.
Tubacex TX 253 MA® is an austenitic 20Cr 10Ni + Si type of alloy with very well-defined contents of rare earth metals (REM) and nitrogen.
The REM in combination with the silicon contribute to the alloy high oxidation resistance and the nitrogen to its high creep strength and structural stability up to high temperatures. Maximum service temperature reaches 1150°C.
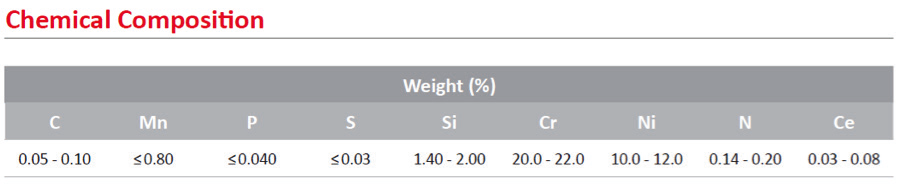

The material has silicon in its chemical composition which helps in formation of Silicon oxide layer (SiO2) in addition to the already existing protective oxide layer (Cr2O3). This prevents the diffusion of Oxygen; Carbon is present in the service condition and it prevents risk of oxidation and carburization.
Silicon (Si) is used for additional protection and acts as a silicon oxide layer, REM (Ce) provides a thinner, tougher, and more adherent oxide layer, and lastly Nitrogen (N) raises the strength and delays the precipitation of the sigma phase. The presence of micro-alloying elements like Cerium help the oxide layers remain integral to the tube in service conditions, creating optimal protection for the tube.
Creep Strength
The high carbon and nitrogen contents present are mainly responsible for the superior high creep strength in this grade compared to other high temperature grades (Figure 1). The high carbon and nitrogen contents result in the solution hardening effect and the precipitation hardening effect is generated by the precipitation of fine chromium carbides and nitrides.
Microstructure Stability
This type of material presents a fully austenitic matrix. Due to its lower chromium content and its higher nitrogen content, the alloy is much less sensitive to the sigma phase formation, as op- posed to other high temperature grades, such as AISI 309S, 310 and 310S. Sigma phase severely impairs toughness, ductility, and corrosion resistance.
High carbon and nitrogen can lead to the formation of chromium carbides and nitrides, which can reduce toughness and corrosion properties but with an effect less pronounced than sigma phase.
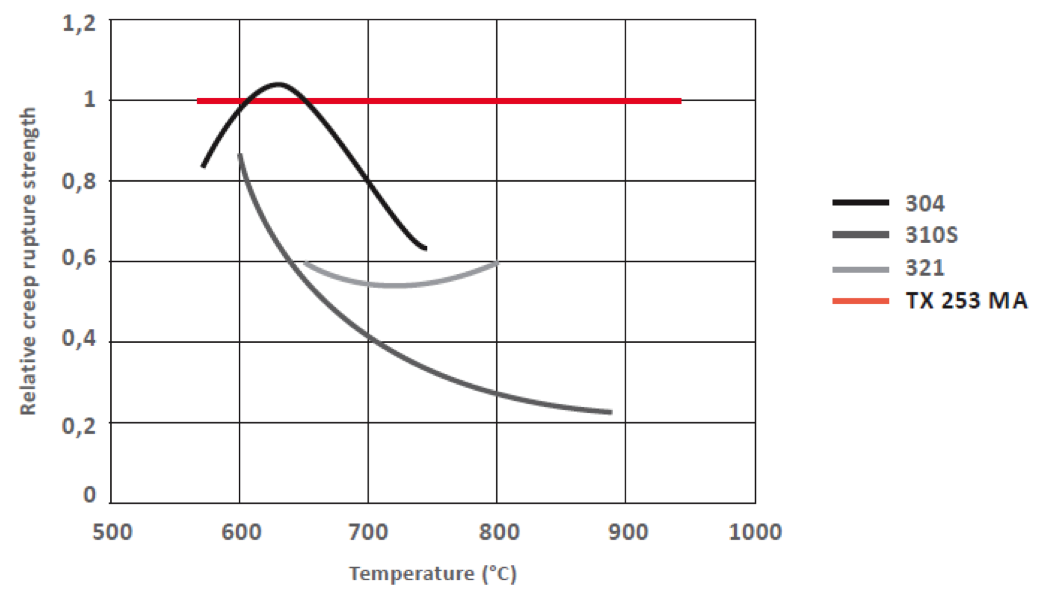
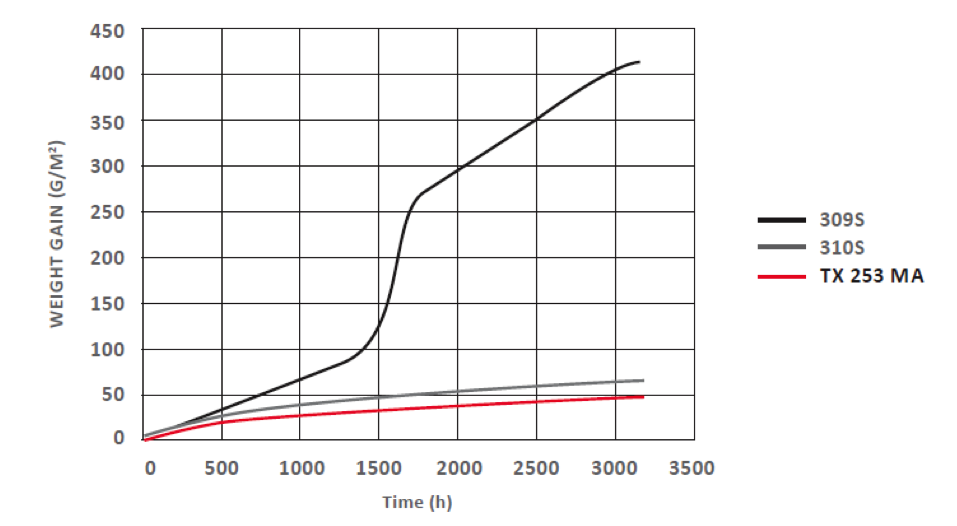
Corrosion Resistance
Oxidation
This material also has an extraordinary resistance to oxidation. The well-defined composition of chromium, silicon and micro-alloying with REM produces a strong adherent to tough complex oxide film of SiO2.Cr2O3. The oxide film of silicon and chromium provides a low diffusion rate for oxygen and metal ions, which affects the oxide growth and creates a high oxidation resistance to the alloy.
Micro-alloying assists in anchoring the oxide to the matrix which prevents oxide rupture and scaling. All this is particularly beneficial under rapid fluctuations of temperature (cyclic oxidation conditions). As shown in Figure 2, there is better cyclic oxidation response than 309S and 310S steel grades.
Sulfidation
Sulfur has a very negative effect on the service life of the exposed components. Sulfides, especially low-melting point Ni-bearing sulfides, can form and attack the underlying metal through cracks or pores present on the protective oxide layer. This tube is very resistant to sulfur containing atmospheres (superior to AISI 309, 310 and the nickel alloys) mainly for two reasons. It can form a thin, tough, and adherent oxide layer, so that sulfur diffusion is mitigated through the layer. Rare Earth Metals can form oxysulfide which prevents the formation of other harmful sulfides that would attack the underlying metal. In highly reducing conditions, when the formation of the protective oxide layer is difficult, steel grades with higher chromium content and minimal nickel content are more appropriate.
Nitridation
The risk of using nitrogen-containing atmospheres is that, when nitrogen diffuses into the underlying metal, chromium nitrides can be formed. Chromium nitrides have an embrittling effect and also, due to their high chromium content, produce a chromium depletion in the adjacent areas that impairs the corrosion resistance of the material. To avoid this, a dense protective oxide layer is needed. Ni content is also important as this element does not react to form nitrides.
Provided that traces of oxygen are present, material such as TX 253 MA® has very good nitriding resistance (better than AISI 309 and 310) due to the nature of its protective layer (thin, tough and adherent).
In atmospheres with no or very little oxygen, such as cracked ammonia gas, grades with higher nickel (AISI 314, 310, Alloy 800H) show superior resistance.
Carburization
Carburization produces embrittlement and damages the corrosion resistance of stainless steel. In order to prevent this, the most effective protection is a solid oxide layer. The addition of REM and silicon help develop an improved scale (thin, tough, and adherent) that makes this grade highly resistant to carburization compared with other grades such as AISI 310 and Alloy 800H.
When the atmosphere is alternately oxidizing and carburizing, the protective scale tends to grow with exposure, and it may break. In such a case, carburization can progress through the damaged oxide layer. Under these conditions, the material is less resistant than grades with higher chromium and nickel (AISI 314, 310, Alloy 800H).
Final Words
Gas to gas heat exchangers are going to play a crucial role in industry towards heat recovery solutions, improving energy efficiency and contributing to Net Zero goals. The flue gas transfers its heat to incoming gases which are reused in the system. The flue gas- es depending on source can lead to corrosion of tubes. Materials such as this one play a significant role in resistance to high temperature (often > 700 degree C) and corrosion caused by ox- ides, sulfides and so on, depending on source of flue gas.
With its improved properties for cyclic oxidation, excellent creep strength and structural stability at temperatures up to 1150°C, materials such as this can be a good alternate solution to high alloy materials such as 25Cr/20Ni grades and Alloy 800H.