Preventing pitting and crevice corrosion can save downtime and money. Identifying the type of corrosion affecting a system is the first step to eliminating it in the future.
By Michael Bestic, Senior Materials Engineer, Swagelok
Corrosion can occur on nearly any metal used in offshore and nearshore applications. Failure caused by corrosion is not inevitable and can cost companies billions of dollars each year. Companies who understand what type of corrosion is damaging their tubing systems can preemptively take precautions to reduce corrosion risks. Identifying the type of corrosion requires an intimate understanding of what causes specific types of corrosion. Exploring where to find corrosion is worth it, so risks can be minimized on oil rigs and refineries to help prevent significant profit loss and extended downtime.
How Corrosion Occurs
Corrosion, the loss of material on the metal surface, occurs when materials interact with the environment and result in a reduction in the wall thickness of components. This is especially true for components made from carbon or low alloy steels, making those components more susceptible to corrosion-related mechanical failure.
It is common to see metallic tubing systems in analytical and process instrumentation, hydraulic lines, and control and utility applications. The material most often used is stainless steel, containing at least 16% chromium. Chromium creates an oxide layer that offers protection to the metals from corrosion, though stainless steel corrosion can still occur. In offshore and nearshore applications, environmental conditions can cause the protective oxide layer to break down and leave even stainless steel components vulnerable.
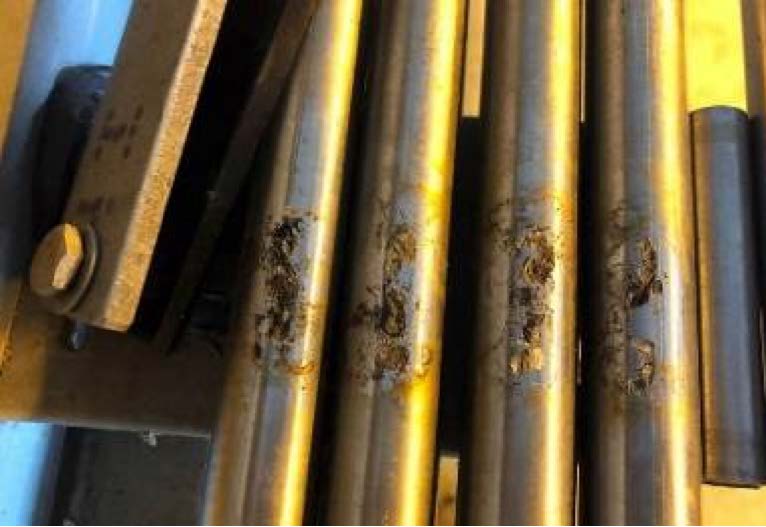
Crevice Corrosion
Like pitting corrosion, crevice corrosion (Figure 2) occurs when the protective oxide film on a component is broken. Crevice corrosion differentiates itself from pitting corrosion by occurring in crevices
rather than exposed metal surfaces. In most fluid systems, crevices are formed between tubing and tube supports or clamps, between adjacent tubing runs, and under dirt and deposits that naturally accumulate on the surfaces of components.They are virtually unavoidable during tubing installations and pose a significant danger to stainless steel integrity.
Once seawater diffuses into a crevice, there is often nowhere else for it to go. It remains trapped in the crevice and creates a chemically aggressive environment where crevice corrosion can occur (Figure 3). Since there is no way for the seawater to exit the crevice, corrosion can spread throughout the crevice’s surface, often quite quickly. Unfortunately, crevice corrosion is typically only discovered when a tubing clamp is removed from the tubing. It is also crucial to understand that crevice corrosion can occur at lower temperatures than pitting corrosion because there is sustained exposure to the corrosive solution. Therefore, it takes less effort to create the “pits” underneath the geometric device (e.g., the tubing clamp).
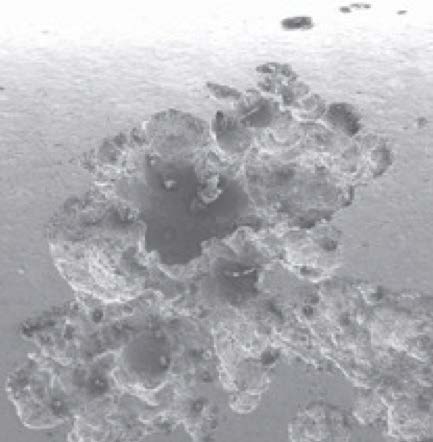
Identifying Common Types of Corrosion
Though corrosion comes in many forms and can destroy oil & gas installations if not well managed, it is important to choose the right material for the operating environment. Even when the proper material is chosen, however, localized corrosion can still happen. Identifying whether a system suffers from pitting corrosion or crevice corrosion is critical to creating an effective plan to combat it.
Pitting Corrosion
When the protective oxide layer on a stainless steel component is damaged by contact with a corrosive aqueous solution, the electrochemical reaction causes the unprotected metal to lose electrons through oxidation. The resulting electrochemical reaction causes
small cavities to form on the metal, commonly known as “pits” (Figure 1).
Typically, pitting corrosion can be seen on visual inspection, but the extent of the pits may not be initially obvious. Sometimes, the pits are so deep that they perforate the material in the components. In addition, pitting corrosion can make it easier for cracks to form in tensile-stressed components. Environments with high chloride concentrations, like oil & gas rigs surrounded by saltwater, can often create the perfect conditions for pitting corrosion of stainless steel material, particularly if the components are subject to high temperatures. Pitting corrosion can be detected by the visual cue of reddish-brown iron oxide deposits and the presence of pits that may have formed on the metal surface.

How to Prevent Corrosion
Material Selection: Consider the choice of materials for tubing applications,
from the tubing itself to tube supports and clamps. Type 316 stainless steel tubing works well in many installations so long as it is kept clean and temperatures are not excessively high. In warmer climates, especially in locations where salt deposits readily form and in installations where rust from carbon steel structural beams and floors accumulates on stainless steel surfaces, corrosion of type 316 stainless tubing is more readily observed.
For these situations, tubing from super austenitic (e.g., 6Mo or 6HN) or super duplex (e.g., 2507) stainless steel offers much better corrosion resistance. The higher yield and tensile strength of super duplex stainless steel also make it easier to build systems that must be rated to a higher maximum allowed working pressure (MAWP). If there is any doubt about what material will work best for an application, consult a supplier who can provide appropriate guidance on which materials will work best.
Placement and Design: Careful system practices are necessary for corrosion prevention to minimize the number of locations where crevice corrosion can occur. One way to diminish crevices in a system is to avoid placing components directly against walls or against each other. A supplier should be able to advise on the best way to ensure a system is using the most up-to-date corrosion-resistant alloys.
Corrosion and Materials Science Training:
While implementing these simple measures will help, it is imperative to make sure individuals are trained specifically on how to identify and remediate corrosion in its earliest stages. This should include regular and robust monitoring of potential corrosion sites. Seek out suppliers who can offer the materials science expertise to train everyone, from engineers to technical associates, and everyone else involved in selecting the materials for specific applications. This collaboration should allow companies to have the right corrosion-resistant alloys in place from the time a system is designed until the time it is in full operation. Understanding corrosion what it looks like, where it occurs, and why it is happening – will allow associates to fix problems before they become large enough to cause equipment failures, costly repairs, and lost revenues.