Keeping up with guidelines and preventative testing is vital to the success of any petrochemical company, and aiming to keep corrosion to a minimum goes hand in hand with the goal of reducing emissions at any facility.
Stainless Steel World Americas had the pleasure of speaking with Jonathan Maddox, Specialty Aromatic Solvents Process Engineer from Nippon Chemical Texas Inc. (NCTIUS), about the effect of corrosive chemicals on various materials, the call for a carbon-neutral world, and the impact of changing regulations.
By KCI Editorial
Studying engineering often leads one to a path of continued growth and a wide variety of potential options for an occupation. This was the experience Maddox had as he began his career. He planned to become an engineer at an early age and after the persuasion of influential officers in his National Guard unit during his service, he decided to focus on chemical engineering. “The complexity of this industry makes for a very interesting work life,” chuckled Maddox. Working for the operations department, he handles many of the daily requirements at the plant, including technical support, loading equipment, and processing chemicals to produce final products.

Specializing in aromatics, Maddox also tackles project management and is responsible for monitoring the processes and overseeing improvement initiatives “I enjoy the intricacy of my role and what it brings,” said Maddox, “it is interesting to see how theory and scientific application collide with humanistic processes; the people and equipment make up the process.”
Corrosion Prevention in Stainless Steel
Due to the hazardous nature of working with petrochemicals, stainless steel is widely used throughout the Nippon Chemical Texas facility. “We often use duplex as a material due to its durability,” explained Maddox. “Alloy 304 is used in several applications, and 316 is used for control valves and lower-temperature applications, such as refrigeration. Using 316 in low temperatures helps mitigate the risk of potential cracking; its resilience is crucial when encountering intense environments.”
“From a financial standpoint, the use of carbon steel over any other material generally makes the most sense, as it will often have the best cost-benefit ratio,” he continued. Stainless steel is also often used in the fabrication of valves, hoses, tanks, and more at the Texas facility, provided the conditions for each asset are appropriate.
When asked about corrosion, Maddox said, “it will always be a point of concern at a plant such as ours. It will always occur to an extent. What matters is how we attempt to mitigate the degree of damage.”
Mechanical integrity programs are in place to try and certify the integrity of the equipment, to protect against corrosion as well as metal fatigue and other potential issues. “We are constantly on the lookout for any and all forms of corrosion and how to prevent it.”
Following the process safety management (PSM) guidelines, the mechanical integrity program completes non-destructive testing (NDT) to assess the strength of materials against specific chemicals. “It is a process; following the guidelines, figuring out the best practices as well as what types of testing should be completed.” The tests are often completed every three to five years, with each piece of equipment being properly inspected and documented, keeping records in case of potential issues. “As new issues arise, we come up with a solution, such as changing the metallurgy,” said Maddox.
When corrosion causes an asset to fail, a sample of the corrosion will be cut out. “If it is clear that a specific chemical is the cause, we may be able to handle the situation ourselves. If not, the sample is sent to a lab for evaluation and testing where specialists determine the mechanism of corrosion,” said Maddox. “For example, we periodically receive material with free water. Over time and in the presence of free water, aromatic process fluids corrode the surface of steel through electrochemical corrosion, and therefore proactively deciphering how to solve the issue is the safest and most economical solution to maintaining the mechanical integrity of a production line.”


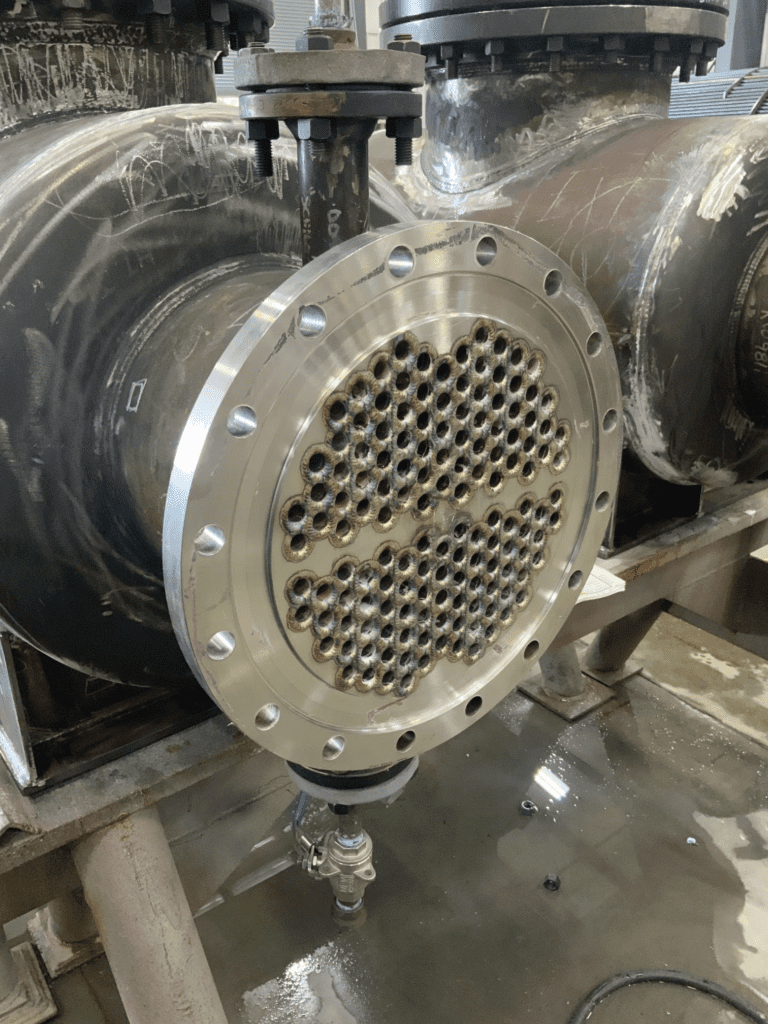
“We are constantly on the lookout for any and all forms of corrosion and how to prevent it.”
The Urgency of Emission Reductions
Corrosion prevention and potential loss of containment fall hand in hand with emission reduction. In Maddox’s position, meeting the emission goals is of high importance. One way to potentially reduce emissions alongside corrosion prevention is to change manual adjustments to automated controls. “We are upgrading the controls to one of our larger process heaters, making the controls automatic instead of manual,” Maddox explained. This will allow a much tighter control of emissions. “Much like our strategy that controls distillation columns, we are looking at a measurement and then making an adjustment to the flow rate to automate the controls, and therefore reducing the produced emissions.”
“There is a huge push to go carbon neutral,” said Maddox. “We want to reduce emissions and meet the global goals, as well as get ahead of the potential regulations that may be put in place so we do not put undue pressure on the operators or operations department.” The push for a carbon neutral environment has been a global phenomenon that continues to gain traction as new regulations arise.
The Effects on Storage Tanks
In order to ensure that the integrity of the facility is maintained, all of its equipment and assets are subject to updates, including storage tanks. As a petrochemical facility, there are many storage tanks in place, that must meet the API codes and standards. “With each update, the standards tend to become more conservative and restrictive, and as a company, we need to stay on top of the changes,” said Maddox. Tanks designed under older, less constricting codes have potentially inadequate safety systems that require assessing. “We need to ensure there is no risk of failure and that employees, as well as the surrounding environment, are not put in high-risk situations.”



For example, an older design of a pro- cess water storage tank ran into problems when accidentally overfilled. The overfill mechanism was not designed for the scenario at hand, and subsequently, damage occurred to the roof of the unit. “In this scenario, we had to understand exactly what had happened, as the safety devices failed unexpectedly,” explained Maddox. “In this circumstance, it is best to check the changing industry standards and ad- just accordingly to reduce said risk and the subsequent risk of harmful emissions being produced into the environment.”
Looking Forward
When looking to the future of the industry, Maddox believes a more humanistic and personal approach will be considered. “Humanizing the technical aspects of the industry and putting yourself in the position of others goes a long way,” said Maddox. “I believe that behavior-based safety and neuroscience will play a role moving forward and that it will take into consideration the welfare of the individual and how that can affect the process. This approach more accurately presents how we create and configure equipment, and how we make decisions from a human perspective, instead of only looking at technical information,” said Maddox.
Continuing the conversation surrounding a more personal aspect to the industry, Maddox advised newcomers to the industry: “take the time to get to know your values and personal boundaries. There are a lot of different paths in this field, and it is important to understand where you want to go. Take opportunities to learn, become a better presenter and communicator, and find your place.”