A typical working day
As her father owned an engineering company, Millen was introduced to the engineering world at a young age, so it is no wonder that she enjoys every aspect of her job, including working with clients, her coworkers, and her overall daily tasks.
Her day is routinely similar, beginning at 6 a.m. when she is given a set of piping engineering deliverables. With a few junior engineers working with her, Millen is very much in a leader position. She elaborates that working with junior engineers is refreshing, as they are very enthusiastic, and she enjoys mentoring and training people.
Millen says that the company she works for is doing a lot of workshare, with the project being split between four different offices: Baton Rouge, Louisiana; Mumbai, India; Vadodara, India; and the Houston, Texas office. “It is being divided by area. We are doing stress analysis and that is being done in our Indian office and the design is also being done in our Indian office. The key to success is working as a team, working together, checking each other’s work, and supporting each other. It does take a little longer because you have to consult and get everyone’s opinion. That is the hard part. Also, I find it challenging because there are different cultures and language differences.”
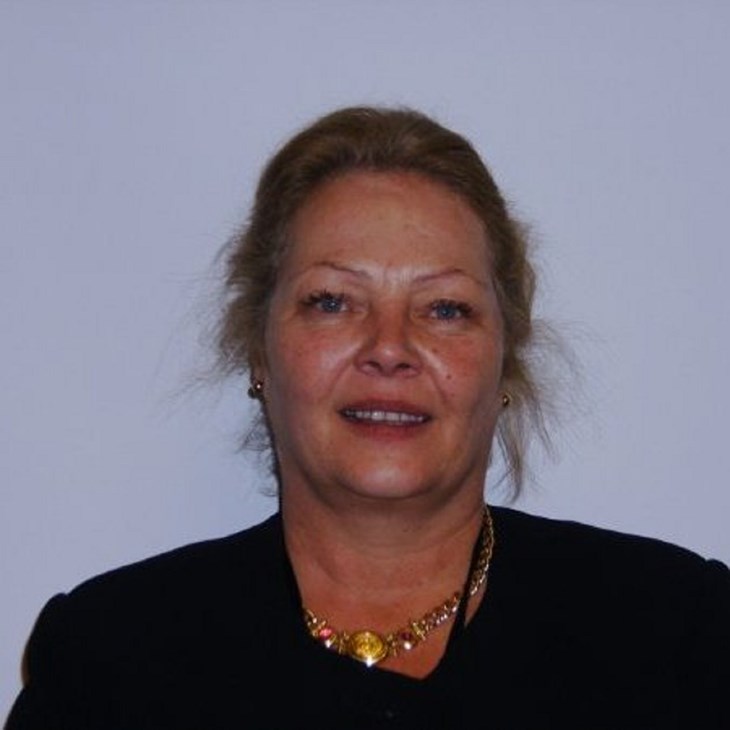
Working with exotic metals
Her team has a variety of duties, including collaborating with clients, manufacturers/ vendors, and looking at historical information when deciding what products and materials to use. Specifically, Millen highlights how exciting it is to work with some of the exotic metals that aren’t as common in the offshore industry. “We have got a lot of duplex, tantalum, titanium, and we even have hastalloy. We also have a lot of rubber-lined materials because what we are using is a very corrosive chemical, a pesticide, which is very interesting.”
Millen further explains that because these materials she is working with are so expensive, such as duplex and titanium, she has been looking at purchasing commodities like valves in a more cost effective manner. This is to ensure the quotes she is given meet the requirements. She adds that while researching more affordable methods, her team has discovered that with C22 alloys it is more economical to get a casting than a forging. “Forgings take longer than castings do. However, with castings you have additional testing to do because castings are prone to cracking. Therefore, we have to watch them carefully, especially in highly corrosive environments such as a chemical facility.”
For example, she explains that her team has worked with one specific valve that isover 12 inches in size and costs USD $5 million. Due to this high expense, Millen’s team cannot afford to make any errors. In addition, not only are the exotic metals expensive to buy, there are also longer lead times associated with them sometimes taking the upwards of 54 weeks. “It can actually be difficult to get some of the materials therefore we had looked at cladding and lining. We have found that in Europe no one clads anything from four inches and down, but four inches and above you can find people to clad for you. We looked at taking stainless steel and titanium and cladding them, which is often what is done on vessels.”
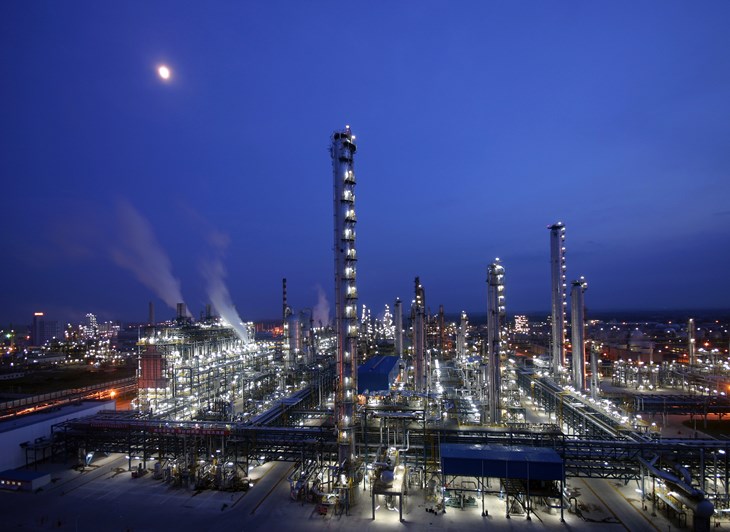
Chemical applications
When asked about chemical applications versus oil & gas applications, Millen discusses the effects of the market. She explains that due to the fact that the oil and gas industry is so non-buoyant at the moment, the chemical market is picking up. A lot of people in the chemical industry are investing while the prices are low. Millen does admit that she finds it is a big difference jumping from oil and gas offshore projects to chemical ones because even though the principles are the same, the schedule is much faster paced.
“The materials and services are a lot different, but I find it very interesting to be able to better understand the soft seated materials used for valves. In oil & gas we would use carbon steel, stainless steel, or duplex, but on the chemical side we tend to use a lot of corrosive materials like tantalum, Hastelloys, alloy 20. There is some carbon steel that we use in utilities, but the rest is all exotic.”
Adding to this, Millen states that it is very important to have a paper trail for all materials and valves, etc. It does not matter if it is offshore or chemicals as she believes nowadays everybody is safety conscious. “Some things are more stringent offshore, but then some things are more stringent on the chemical side of things,” she says.
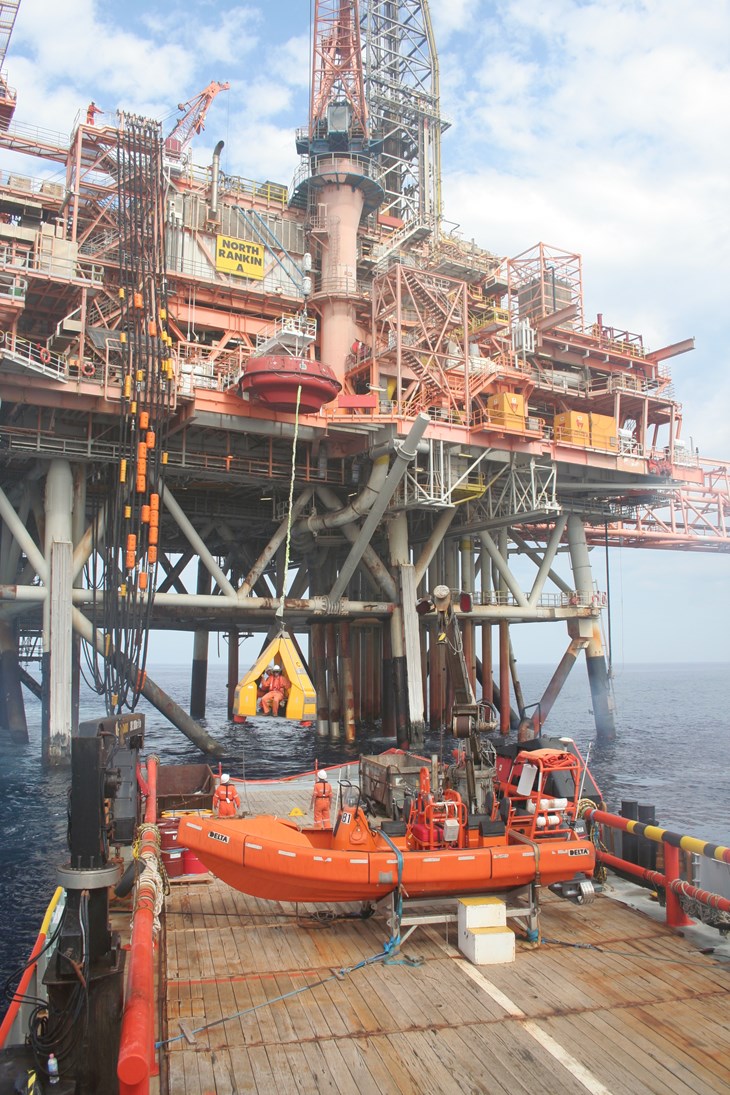
Avoiding fugitive emissions
It is clear that Millen has a vast amount of experience in her field and this is exemplified even more when she discusses her knowledge of, and dealings with, fugitive emissions, a very significant topic in the industry right now. Not only do fugitive emissions damage the environment, when gases and other vapors leak, they are also costing the company money. Hence, preventing fugitive emissions is a key aspect of Millen’s job. Due to the corrosiveness of the chemicals she deals with, her valves need to meet the standards to ensure leaks do not occur. Further expanding on the topic of fugitive emissions, Millen talks about imports and having to be careful when sourcing from abroad. While she will get a couple of valves from overseas for the project she is currently working on, she has to be certain they have the ISO 9001 accreditation.
“We tend to stick with the manufacturers that have the accreditation. You know they are following the required processes to ensure the quality is coming out perfect.”

Training the next generation
Millen ends our interview by discussing her involvement with the Valve World Americas Conference and Expo steering committee and explains the significance of attending industry events. She believes that if you do not attend conferences you will not move with the changing times.
“I am a big fan of conferences and training the youngsters,” she says. “You will find nowadays that young engineers are extremely good using computer software but when it comes to the technical knowledge, the information is not being passed on quick enough.” To conclude, Millen gives an insightful view on the future of the industry, believing that it often goes through a difficult time but will pick up again. She sees it as a continuous fluctuation from high to low; an optimistic attitude to have during the current industry downturn.