The industrial world is undergoing a fundamental metamorphosis that has been in the making for quite some time. As industrial productivity and efficiency plateaued in the early part of the previous decade, manufacturers started utilizing a variety of new technologies such as the Internet, wireless connectivity, pervasive sensing, and ubiquitous computing to improve operational efficiency. While at the start they were disparate new technologies, companies started to realize that the power of the technology lay in combining them. Thus, Industry 4.0 was born.
Industry 4.0, in the broadest sense, implied utilizing the confluence of various technologies. Moreover, Industry 4.0 is a platform that enables the unification of information amongst participants in the entire value chain–from product inception to design, manufacturing, services, and even refurbishment. The end result will be a grand system in which all processes are completely integrated and will exchange information in real time. This revolution will transform the manufacturing processes in sync with the speed of change in customer needs–which implies making the production process flexible without taking excess time.
As noted below, Industry 4.0 includes a variety of technology and, while the impact of Industry 4.0 is clear at the overall level, the impact at process and product level is still vague. Varying process requirements of end-users create the need for customized solutions. Each technology and itself attuned to a particular set of end-users.
Upstream oil and gas: predictive analytics
With oil prices still around USD $50 per barrel (August 2017), the oil and gas industry continues to face turmoil. As the oil price falls, there is an acute need to reduce operational cost. Oil and gas end-users are thus finding better ways to manage their assets. Pump jacks and Electronic Stability Programs (ESPs) form the majority of solutions used in oil and gas. It is paramount to ensure that they are working efficiently and, currently, maintenance personnel have to regularly visit all the pumps to ensure they are properly serviced and running. While they are visiting a perfectly working pump, some other pump might fail. This increases labor costs and leads to increased equipment downtime.
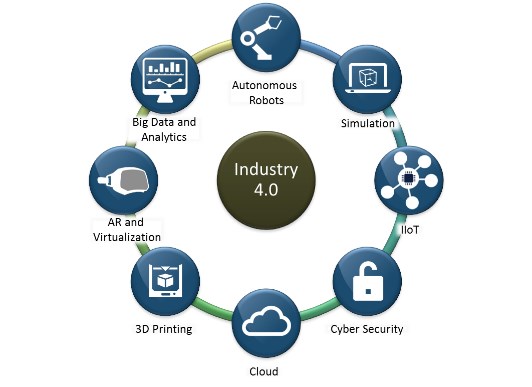
“In the new era of low oil price, it is pertinent that oil and gas operators are able to contain cost of operations,” opines Nav Dhunay, CEO of Ambyint. “Analytics could help oil and gas companies improve efficiency by 10% to 15%.” Nav and many other enterprising entrepreneurs have started using technology to solve challenges in oil and gas. Analytics is one of the areas that forward-thinking oil and gas companies are looking at as they seek to improve how they operate their businesses and deliver their capital projects.
Up to now, there has been no way to predict when and how a particular pump is going to fail. A better understanding of when a given pump might fail will allow maintenance personnel to ensure they are addressing the critical issues to drive pump uptime. Predicting how a well and the associated pump will perform has been considered impossible. “That’s where years of analysis comes into play,” quips Dhunay. “Based on the data collected, we can predict how a well is expected to perform. Based on a combination of various factors, we can predict when the pump or other equipment is expected to fail. This helps drive equipment uptime and end-users save on labor cost.”
For example, analytical systems optimize ESP’s pumping speed to enable the highest production. Based on the proprietary algorithm, these systems enable reduced mechanical loadings and higher efficiency leading to over 30% reduction in energy cost. In the next few years, more and more companies will be deploying predictive analytics to optimize every facet of their enterprise.
Oil and gas refineries: IIoT and predictive maintenance
A smart world of connected things, devices and users exchanging information in real time to perform assigned tasks is already a reality in the industrial space. Industrial Internet of Things (IIoT) enables the unification of information amongst participants in the entire value chain. The end result will be a grand system in which all processes are completely integrated and will exchange information in real time.
“The biggest challenge to IIoT is the effective aggregation of data. Engineers are spending too much time extracting and aligning data from various sources,” said Ben Blanchette, Director of Product Marketing of Honeywell Process Solutions’ Digital Transformation business. “Paramount for successful IIoT implementation is a smart and secure collaboration system that can provide you with secure access to data that is being collected. Once you aggregate the data and analyze it, then domain experts such as Flowserve can plug-in, bench-mark the equipment data, and provide performance tools.”
Honeywell, a leader in the global automation market for process industries, is able to collect and analyze the data through its Distributed Control System (DCS) infrastructure. Flowserve, a leader in flow control solutions, is able to provide actionable insights through transformative service capabilities that lead to more powerful decision-making and process optimization. Ultimately, through collaborations, companies will leverage the IIoT to help customers minimize unplanned shutdowns, maximize output, minimize safety risk, and optimize supply chain strategies. “The success lies in collaboration. That is how customers can get better performance and lifecycle out of their equipment,” says Ben.
Smart field services
In North America, there are millions of business fleet vehicles, remote field workers, and pieces of remotely-placed portable equipment operating outside of a company’s four walls and invisible to management. Integrating such products with Internet of Things (IoT) remote monitoring capabilities allows service organizations to leverage real-time data provided by their field assets. The data from connected de- vices/equipment will move field service departments from a reactive break/fix model to a proactive—even preventative— level of service delivery. IoT integration adds sensors and remote monitoring to take the place of customers’ eyes and ears, identifying issues before a serious equipment problem occurs and escalates. Potential benefits include lower labor costs (quicker time to first fix), greater customer satisfaction and retention, and increased revenues via new service offerings.
When a service technician does need to be deployed, wearables can help increase that technician’s productivity by providing easy access to needed information. Some service organizations may choose to engage in the custom integration work required to provide an Augmented Reality solution to their field service teams. Organizations that have already deployed tablets, or other mobile computing, to their service teams may prefer adding a secondary head-mounted display instead. These solutions can be deployed immediately to any existing solutions using a standard connection, such as High-Definition Multimedia Interface (HDMI). “Having access to the necessary diagnostic information and schematics through mobile computing is already transforming field service,” said Josh Hardt, Sr. Director of Strategic Planning at Brother International Corporation. “The next leap is to use a head-mounted display to place this information in front of your eye. If you don’t have to turn away from your task to consult reference materials you can be more efficient and deliver a higher quality outcome for the customer.”
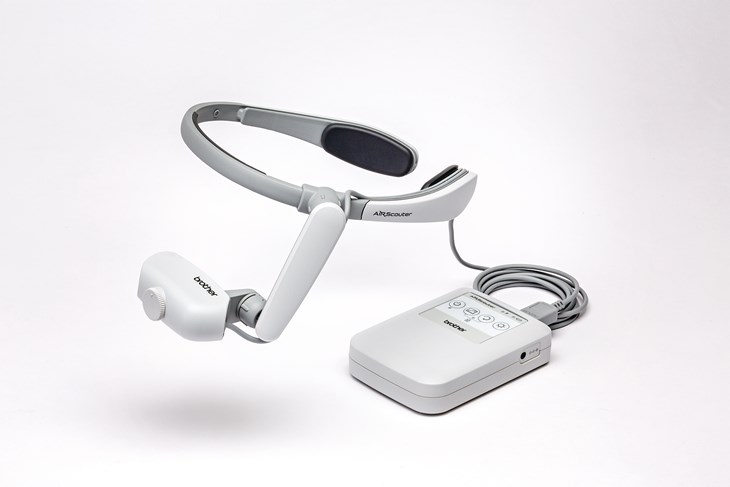
Process industries: simulation, Augmented Reality (AR) and Virtual Reality (VR)
The process industries, such as oil and gas and power industries, are a high growth segment in the simulation market. While these industries face an issue of shortfall in capacity, they must also grapple with the aging workforce factor. Recent statistics compiled by the Bureau of Labor highlight the broadening gap between the retiring and newer workforce. This gap is expected to widen at a faster pace in the coming years. As a result, there is a shortage of trained process operators, engineering, and maintenance crews. This shortage is driving the increased adoption of simulation solutions for the process industry. “Hands-on-training is a luxury that many industries can’t afford, as it is cost prohibitive to shut down a production process or take one of the equipment of offline,” suggests Mark Cheben, Global Marketing Director at EON Reality. “On the other hand, most critical equipment are too expensive to be dedicated solely for training purposes.”
Another key area of focus is process simulation. Recent developments in low cost processing power and reductions in software development costs mean that simulation solutions are being increasingly used in improving plant profitability. Although there is a demand for simulation solutions for process optimization and improving the bottom line, many simulation solutions and providers do not supply the necessary attributes end-users require, offering just the software and leaving end-users to struggle with optimizing the software and their processes.
EON Reality created a system, the AIRNET Industrial Planner, for a leading compressor manufacturer. The company needed its salesperson to select, plan, and optimize a compressor installation in real-time to shorten the sales cycle. The sys- tem was able to analyze thousands of catalog product and multiple data points (such as various critical design parameters), and optimize the layout to evaluate the technical performance and create a full-customized quotation.
Next stage in the technology evolution
There are multiple challenges in implementation, not just that the technology adoption in process equipment (especially pumps) is slow but in addition, the fragmented vendor landscape and lack of unified standards is affecting implementation. Evolution of a unified standard is essential to success. Security always seems to be an after-thought in industrial applications. Given the recent cyber-attacks, both individual and state sponsored, it is critical to build a secure and robust infra- structure. Finally, the aging workforce and talent crunch may bottleneck the adoption curve.
There has been much progress on developing new technologies and enterprising entrepreneurs are finding new solutions to solve tomorrow’s problem. Nav aptly summed it up, saying: “The process equipment industry is being disrupted daily. Buzzwords are changing constantly. In the next few years, there will be several revolutionary ideas and it is very exciting to be on the cusp of change.”
About the author
About the author
Anand M. Gnanamoorthy is the Industry Manager for Frost & Sullivan’s Process Equipment team, analyzing new trends and disruptions within the pump industry. He can be reached at anandg@frost.com.