To sustain world growth, energy use must increase. However, if increased energy use is not accompanied by energy conservation, the increased energy use may create environmental problems.
Part Two of this two-part article examines experimental results of condensation heat transfer enhancement using hydrophobic stainless steel tubes. It includes an evaluation of the effect of hydrophobicity for tube-side condensation heat transfer. This is accomplished by comparing the performance of the enhanced hydrophobic (HYD) tube to a smooth tube.
By David Kukulka, Director of Engineering Development, Rigidized Metals Corporation
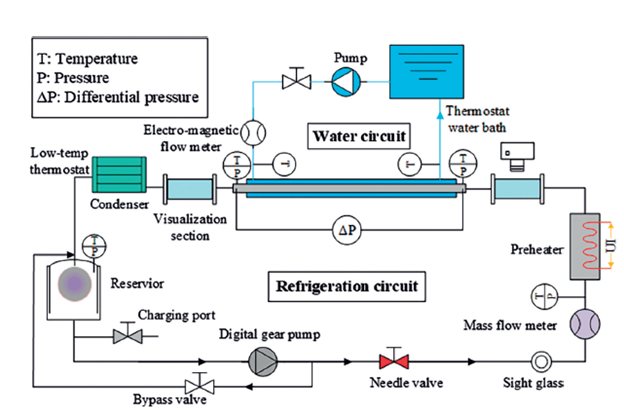
Experimental Details
Figure 1 details the experimental apparatus used in this study. An image of the hydrophobic enhanced surface studied here is presented in Figure 2 with surface scans of the hydrophobic surface shown in Figure 3. When tube-side condensation is studied, the test section (as can be seen in Figure 1) of the apparatus is composed of a horizontal counter-flow heat exchanger. Refrigerant flows in the enhanced tube being evaluated, and cooling water is flowing in the external annulus around the enhanced tube.
After the test section, the flowrate of the cooling water is measured using a mass flowmeter and the water is returned to the constant temperature water tank. The temperature here is measured using a Pt100 platinum resistance temperature sensor. The refrigerant is heated to a predetermined temperature and quality before it enters the test section. In the condenser, the refrigerant flowing from the test section is completely condensed and subcooled. Additional details regarding the experimental setup and procedure are found in Li et al. (2021).1
The purpose of this study was to investigate the impact of hydrophobicity on heat transfer tubes. This study utilized R32 refrigerant to study an enhanced hydrophobic heat transfer tube (HYD) and compared performance to a smooth tube (ST). This lays the foundation for the development of enhanced hydrophobic surfaces that are used in heat transfer applications.
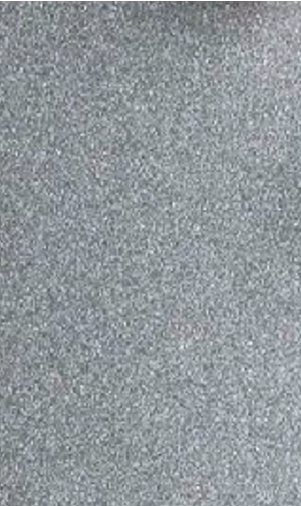
Tube Details
This study examines the impact of hydrophobicity on the surface of a condensation heat transfer tube and includes a comparison of a smooth tube (ST) and a hydrophobic (HYD) tube. It is important to note that the HYD surface used in this study is not a coating, but it is mechanically produced on the surface of the tube. The sessile drop method is used to optically determine the contact angle between the liquid and a solid surface; contact angles (see Figure 4) of 107.35° are found for the HYD tubes and 79.06° for the smooth tube. All of the tubes are constructed from stainless steel, with an outer diameter of 12.7 mm and inner diameter of 11.5 mm.

Effect of Subcooling on Hydrophobicity
Figure 5 illustrates the variation of the heat transfer coefficient with flowrate (G) for the ST and HYD tubes. In general, as the subcooling temperature difference increases, the growth trend of the heat transfer coefficient gradually slows down. This trend is more pronounced at the saturation temperature of 45℃.
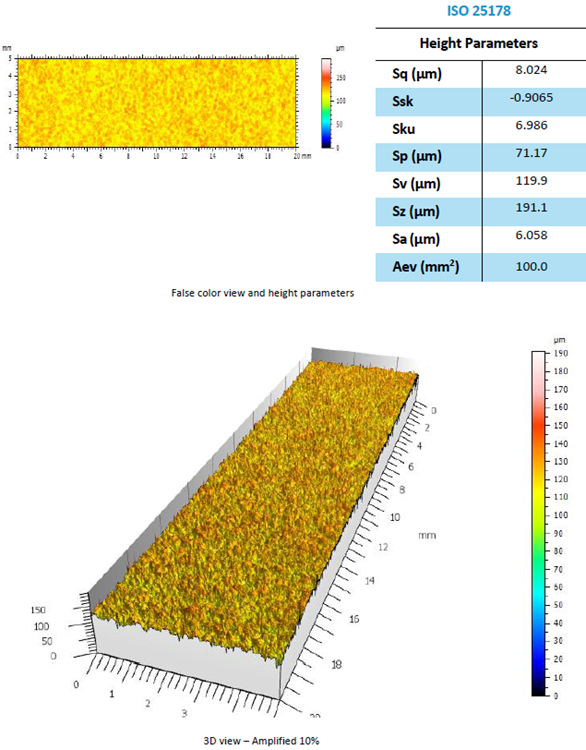
This demonstrates that an increase in subcooling temperature (i) impacts the detachment rate of the liquid, (ii) increases droplet accumulation, (iii) leads to thicker liquid film, (iv) increases thermal resistance of the upper wall surface in the microchannel, and (v) weakens the heat transfer effect. The saturation temperature of the ST at 35°℃ shows the opposite trend. This is due to the smooth surface of the ST, which lacks an enhanced surface and is less affected by the supercooling temperature.

Figure 5 presents the variation of the heat transfer coefficient (HTC) with mass flow rate for the tubes studied here. The HTC’s of the tubes studied perform about 10% better at Tsat =35 °C than at Tsat = 45 °C. The physical properties of refrigerant R32 perform better at a saturation temperature of 35 °C than at 45 °C. Specifically, at Tsat 35 °C, the liquid phase density of refrigerant R32 is higher than at 45 °C, enabling the refrigerant to counteract the effects of gravity, particularly at high mass flow rates. This leads to an increased flow rate of the refrigerant within the tube, producing sufficient heat transfer and consequently enhancing the heat transfer coefficient. Moreover, the thermal conductivity of refrigerant R32 at a saturation temperature of 35 °C exceeds the thermal conductivity at 45 °C. This further enhances the heat transfer rate of the refrigerant.
Figure 6 shows the variation of pressure drop (DP) as a function of flow rate (G). This shows that there is no increase in pressure drop in the HYD tube.
To analyze the effect of hydrophobicity, the variation of the HTC with mass flow rate for ST tubes is compared to HYD tubes. Over the range of conditions considered here, the HTC of the HYD tube is approximately 20% higher than that of the ST tube. The hydrophobic structure enhances the upper wall surface of the tube with a lower surface free energy, preventing the refrigerant from generating a liquid film on the upper wall surface. Due to the increase in contact angle, the upper wall surface of the tube forms large and small droplets, resulting in a droplet condensation flow pattern.
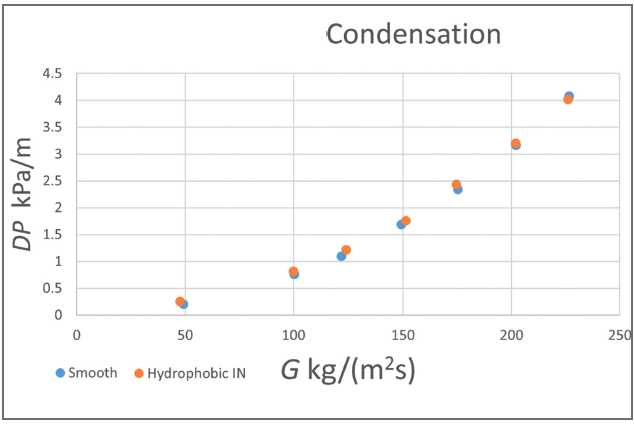
Conclusions
To assess the impact of the hydrophobic structure on tube-side condensation heat transfer, an experiment was performed that collected data over various scenarios (using refrigerant R32). Conditions included saturation temperatures being set at Tsat=35 °C and Tsat =45 °C, with mass flow rates of 100 kg m2 s-1 and 150 kg m-2 s-1. Specific conclusions derived from this analysis are as follows:
- Over the range of conditions considered here, the heat transfer coefficient of the HYD tube is approximately 20% higher than that of the ST tube. The hydrophobic structure enhances the upper wall surface of the tube with a lower surface free energy. This prevents the refrigerant from generating a liquid film on the upper wall surface.
- The physical characteristics of refrigerant R32 exhibit superior performance at Tsat=35 °C when compared to the performance at Tsat=45 °C. Consequently, both tubes demonstrate an enhancement of approximately 15% at Tsat=35 °C when compared to Tsat=45 °C. Moreover, as the mass flow rate increases, the heat transfer coefficient of the HYD tube increases by approximately 20% (when compared to a smooth tube). This enhancement is attributed to the hydrophobic structure, which promotes droplet condensation on the inner surface of the tube, increasing the droplet detachment rate and the heat transfer efficiency.
- Performance of the HYD tube shows a clear trend as the vapor mass rises. This occurs when the refrigerant gas phase dominates over the liquid phase, preventing the formation of a liquid film from the large droplets produced by the hydrophobic structure. As a result, there is a significant increase at an average vapor mass of 0.5.
- Future hydrophobic surfaces are being developed and tested; these will be the subject of another publication.
The hydrophobic tube offers a clear advantage over the smooth tube for various heat transfer applications and should be considered as a means to enhance heat transfer.
About the Author
David Kukulka has been the Director of Engineering Development at Rigidized Metals Corporation for approximately 16 years. He is responsible for the development of the patented process to produce Enhanced Heat Transfer Surfaces for the Vipertex Division of Rigidized Metals. He is a registered Professional Engineer and also has a PhD in Mechanical Engineering with a specialty in Heat Transfer. He has more than 40 years of experience in heat exchanger design and enhanced heat transfer development.