Stainless Steel World Americas had the chance to speak with Hoefig about his role as a Welding Engineer, the types of materials he uses for highly corrosive applications, how to deal with aging infrastructure, and what wisdom he would share with the future generation of welders.
By Brittani Schroeder
Scott Hoefig did not always know he wanted to be an engineer. After being accepted into two programs at the University of Waterloo, in Ontario, Canada, he had to decide between Computer Science and Mechanical Engineering. A week before the deadline, Hoefig chose Mechanical Engineering, and he has never regretted his decision. “When I made that decision, I knew I was making a decision about the kind of life I wanted, and I knew that I did not want to sit at a desk with a computer every day. Mechanical Engineering was more hands-on, and I got the opportunity to see things being built, and that is what I wanted,” says Hoefig.
Once he was in the program and started his co-op placements, Hoefig realized he particularly liked the materials side of engineering, and really found his niche in welding. “I specialized in welding and joining materials, and did many co-op placements during my undergrad studies,” he relays. “After I finished my degree, I went back to one of the companies I co-oped at and applied for a full-time position. I have been there ever since.”
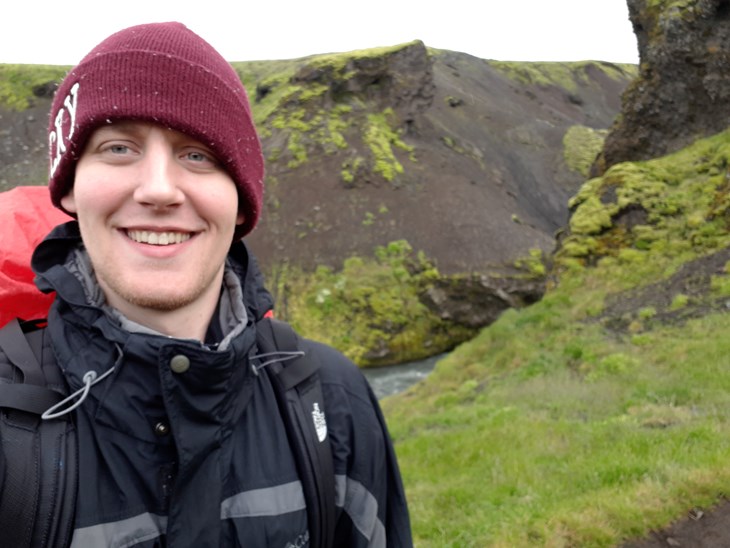
The role of a welding engineer
Hoefig is a Welding Engineer at Chemetics, Inc., located in Pickering, ON, Canada. As a Welding Engineer, he completes all of the welding procedures, maintains and updates the welding practices, helps find solutions to new applications, and troubleshoots all types of situations. “I help resolve anything that is considered non-conformance, from minor to major defects,” he explains. “I also do a bit of fabrication and industrial engineering, R&D, and I support multiple engineering teams and my manager. Any technical welding questions are answered by me.” Hoefig also works with different suppliers and qualifies new vendors. When the team is working on a new bid or proposal, he completes specification reviews and cost impact reports. “I also review procedures with the suppliers as well to make sure they are at the level of quality that our company requires. Sometimes I also visit the project sites domestically and internationally if a client needs assistance,” he says.
With the large number of responsibilities included in his role, Hoefig does not have a typical working day. “I would say I have a typical working month, because every day I am doing something different,” he relays. “It really goes in cycles. I will spend a few days developing new procedures, a couple days working with a client, another couple of days reviewing documents, some time spent planning for upcoming projects, then time spent on upcoming bids, proposals and special projects. When I look at my schedule a few months at a time, it is repetitive in that way, but every day brings something new.”
There are many aspects of his role that Hoefig enjoys. “I think being able to work with leading edge technologies, new exotic alloys, and being able to solve the problems is what I enjoy most,” he says. “When you are in university, you do not expect to use what you learn throughout your career. I personally rely on it, and I pull out my notebooks all the time to refer to what I learned years before. I love being able to put that knowledge to good use.”
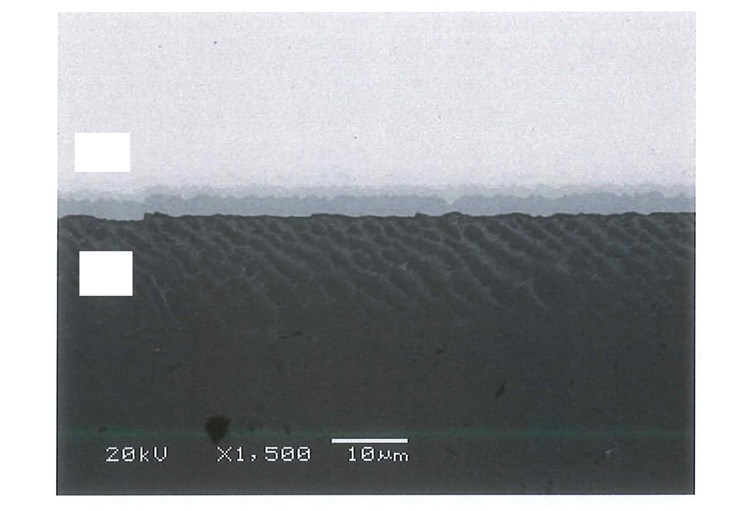
A range of materials
Within Hoefig’s role, he has had the opportunity to work with a wide range of materials. “We use a variety of metals, including all the plain austenitic stainless steels, the 304, 310, 316, along with the 6 Moly (molybdenum), high silicon stainless steels, Inconel, Hastelloy, and titanium,” he says. “When we are working in highly corrosive environments, such as sulfuric acid, corrosion resistance is of the utmost importance, and that means we need high quality materials.”
Part of Hoefig’s responsibilities include resolving difficult welding situations and stringent acceptance standards for defects. “With welding, we are implementing a lot of automated machines these days, so we always need to make sure the work is done properly. We are continually checking for imperfections developing in the welds,” Hoefig explains. “I obviously do not want there to be any defects, but I do enjoy the opportunity to solve a problem when one occurs. There is a little bit of investigation that needs to be done, and finding the correct solution is quite satisfying.”
Hoefig likes to think of some welding challenges as an abstract problem. Is the geometry off, and the gas is flowing in a certain way that is resulting in a defect? Are certain components compounding in a weird way that is causing the issues? Is an automated machine out of calibration? “If there is a problem, you just have to work through it systematically and you will find a way to solve it,” Hoefig says.
While in the process of welding, there are a few things that Scott Hoefig looks out for. “To start, you need to make sure you are getting your welding consumables, filler metals, etc., from reputable sources. You need to make sure you watch the amount of heat you are applying to the metals while welding – interpass temperature is critical for high performance alloys. You also need to properly clean your base metal and maintain your welding equipment,” explains Hoefig. “There are also issues that come from new equipment that arrives with slight differences from the specifications. You need to be very precise when ordering new parts and equipment, and verify them as they arrive to make sure everything is up to spec.”
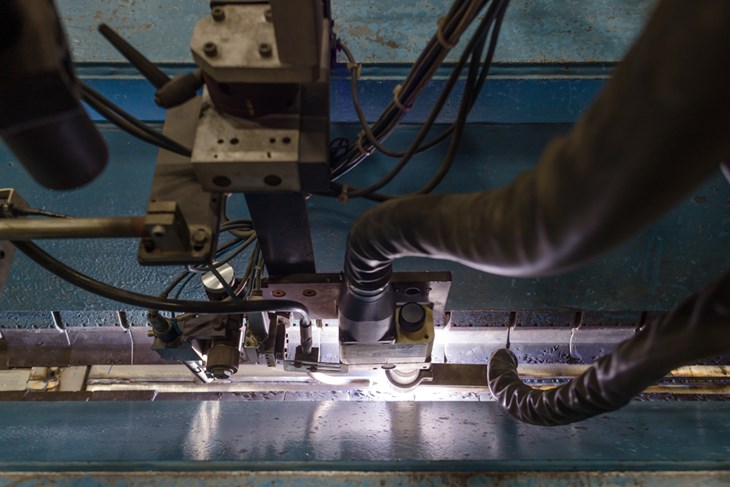
Working with aging infrastructure
Most of the projects that Hoefig works on deal with highly corrosive fluids, such as sulfuric acid. Due to the high corrosion potential, sulfuric acid plant operators need to monitor their equipment and infrastructure closely to make sure their plants are not aging too quickly. “All the parts need to be maintained and then replaced over a period of time—there is no way to avoid that in a sulfuric acid plant,” he explains. “Everything will corrode in sulfuric acid, even the most expensive exotic alloys. So we are familiar with replacing what we have installed long ago. Sometimes the materials will last 20 to 40 years, sometimes it will be shorter than that. The great thing about advancing technologies is that we are able to replace the older materials with new exotic alloys that may have an even stronger resistance to corrosion, which means it should last even longer in a sulfuric acid environment.”
Learning from the older generation
One of the reasons Hoefig enjoys his work so much is being able to work alongside some very knowledgeable people in the industry. “Everyone I have had the pleasure to work with has been able to teach me something new and interesting. I carry around notebooks so I can write down what I learn, and I constantly refer to them when I need a refresher,” Hoefig relays. “When I have a question, I have people I can go to for advice on a certain issue or situation. What I find most is that if you are willing to listen, people are willing to share their knowledge and experiences with you.”
The knowledge Hoefig gained from his supervisors gave him insight into industrial manufacturing and management, how to keep quality high, and how to put new processes and producers in place. “I definitely brought that knowledge to my current role,” says Hoefig, “and when I am creating new processes or implementing new procedures, I can rely on that knowledge.”
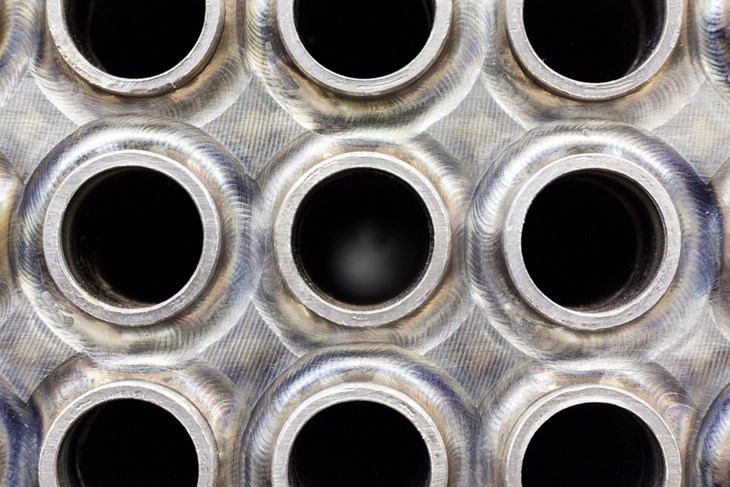
Words of wisdom
When Hoefig thinks about the future of the industry, he sees it continuing to grow and attract new talent. “There are always going to be new technological advances in metals and welding, and there will be new ways to deliver products quicker while also keeping the price down—especially if that is what the clients are looking for,” he says. “New materials will replace old and obsolete materials, and automation will really take over a lot of processes that are currently done manually. But I think there will always be a need for welders and skilled tradespeople.”
If Hoefig could give a few words of wisdom to graduating engineers and welders, he would say to always listen and be open to learning. “You cannot learn everything about the industry in school—so you need to know that your education does not end when you graduate. Listen to what the older, experienced engineers, welders, metallurgists, etc., have to say, because they have so much knowledge to share,” Hoefig relays. “These people are artists in their own way, and they want to teach you their craft. They will show you a whole different side of the industry; you just need to be ready with a pen and paper to capture and remember what you can.”