The steel industry ranks amongst the top three CO2 (carbon dioxide) emitters from the industrial segment, and many steelmakers have set carbon neutral goals for the 2030-2050 timeframe. In general, stainless steel producers have a smaller carbon footprint than most carbon steel producers — on average about half — yet many have focused on investigating and implementing various available decarbonization approaches.
Naturally, a short-term approach for decarbonization would be focused on improvements and minor alterations in parallel to mapping out longer-term options. There are immediate actions relating to procurement, operation practice, and use of proven technologies, that can be implemented to reduce the carbon footprint.
By Joachim von Schéele, Global Director Commercialization, Linde plc
Procure Greener
Using green power – based on renewable energy sources – is an obvious step that can be taken wherever possible. The biggest consumer of electricity is the Electric Arc Furnace (EAF). Employing green power in the EAFs could decrease CO2 emissions across the Americas by 50-200 kg per tonne of steel produced, depending on how the electricity is produced at the specific location. Naturally, green power should also be used to produce the industrial gases used (oxygen, argon, and nitrogen).
Another action that instantaneously results in a reduced carbon footprint, is charging of more scrap. Scrap is defined as ‘carrying zero CO2’; however, all alloys do ‘carry CO2’ from their upstream production. Accordingly, it is very important that attention is paid to the carbon footprint when procuring alloys, because those alloys could be a large contributor to the final carbon footprint of the stainless steel product.
A recent study was conducted at the Royal Institute of Technology in Sweden, where the impact of nickel supply was evaluated. The study showed that Nickel Pig Iron (NPI), for example, carries a large carbon footprint—about five times that of the lowest CO2 emitting alternative for nickel supply. Accordingly, from this perspective, the NPI material should be avoided as much as possible. Some other observations on the carbon footprint relating to the choice of alloys include the use of nickel from sulfide ores instead of laterites, and, if possible, replacing nickel with manganese.
Oxyfuel Combustion Drives Energy Efficiency
Many unit operations in a steel mill use air for the combustion of fuel, which carries 79% ballast (almost all of it nitrogen). This nitrogen is heated up in the furnace and emitted in the flue gas, resulting in wasted energy, higher fuel consumption, and CO2 emissions. Moreover, it hampers the radiative heat transfer from the products of combustion. The use of oxygen instead of air, called oxyfuel combustion, eliminates this nitrogen ballast, and results in:
- Up to 50% fuel and CO2 savings,
- An 80% reduction in flue-gas volume,
- Up to 90% NOx (nitrogen oxides) reduction,
- On-demand production increase, and
- The ability to use of low calorific gases in heating and reheating operations.
Oxyfuel combustion has been successfully applied to several steel mill operations including blast furnace stoves, pelletizing/sintering furnaces, ladle preheating (40-60% fuel savings), reheat furnaces (batch and continuous), and heat treatment furnaces.
The economics of oxyfuel combustion are typically driven by fuel price, but as steel mills adopt green hydrogen fuel to decarbonize their footprint, oxyfuel combustion will become economically necessary. This is because hydrogen prices are expected to drop down to around USD$2/kg, which is equivalent to USD$15/GJ (i.e., hydrogen will always be a relatively expensive fuel). Accordingly, oxyfuel combustion is required to minimize the use of hydrogen. Therefore, the recommendation for steel mills is to convert to oxyfuel combustion now to achieve 20-50% CO2 reduction and be prepared to blend green H2 when it becomes available, to achieve full decarbonization in the future.
In addition, in stainless steel production, the annealing lines can be converted to a flameless oxyfuel operation.
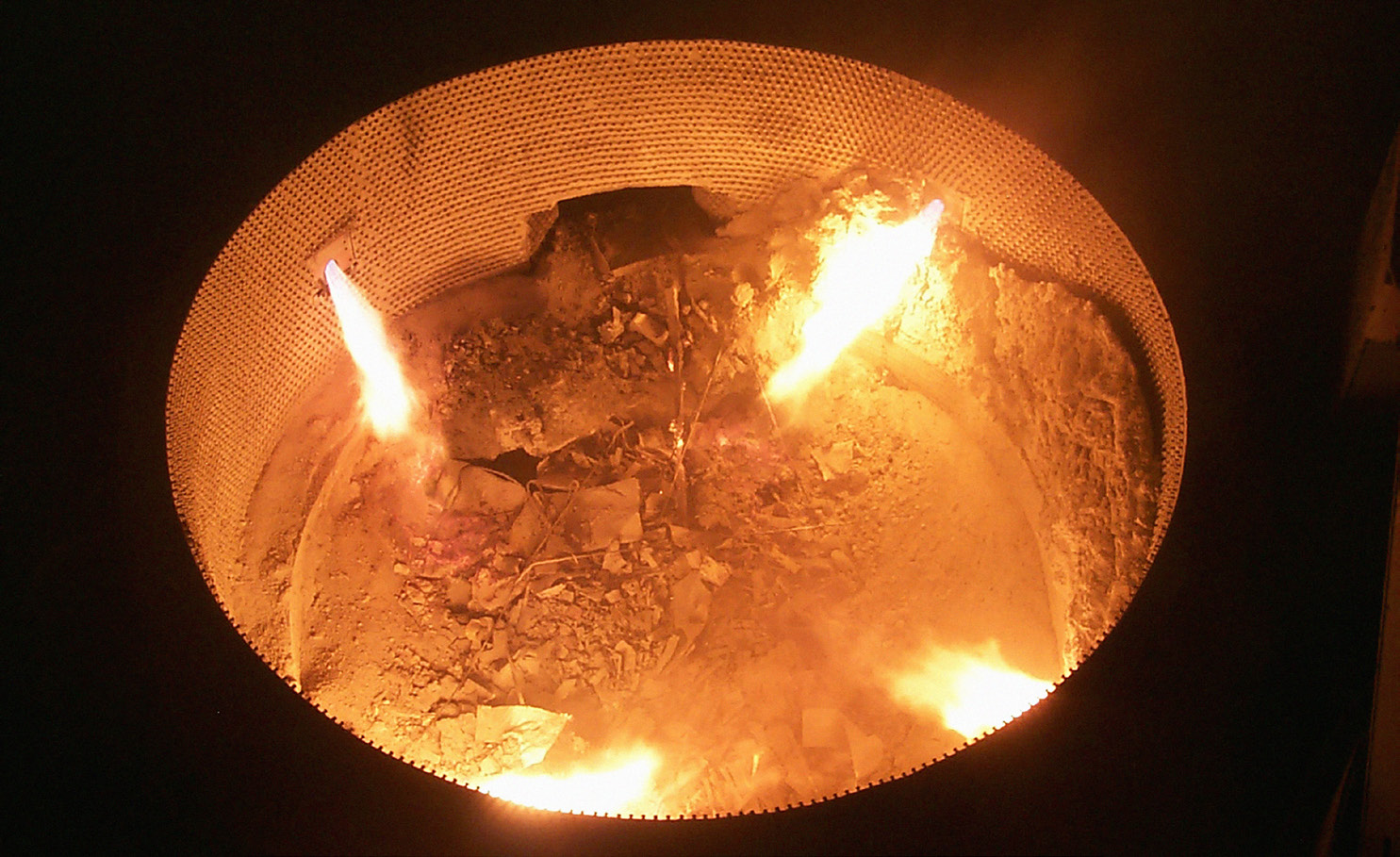
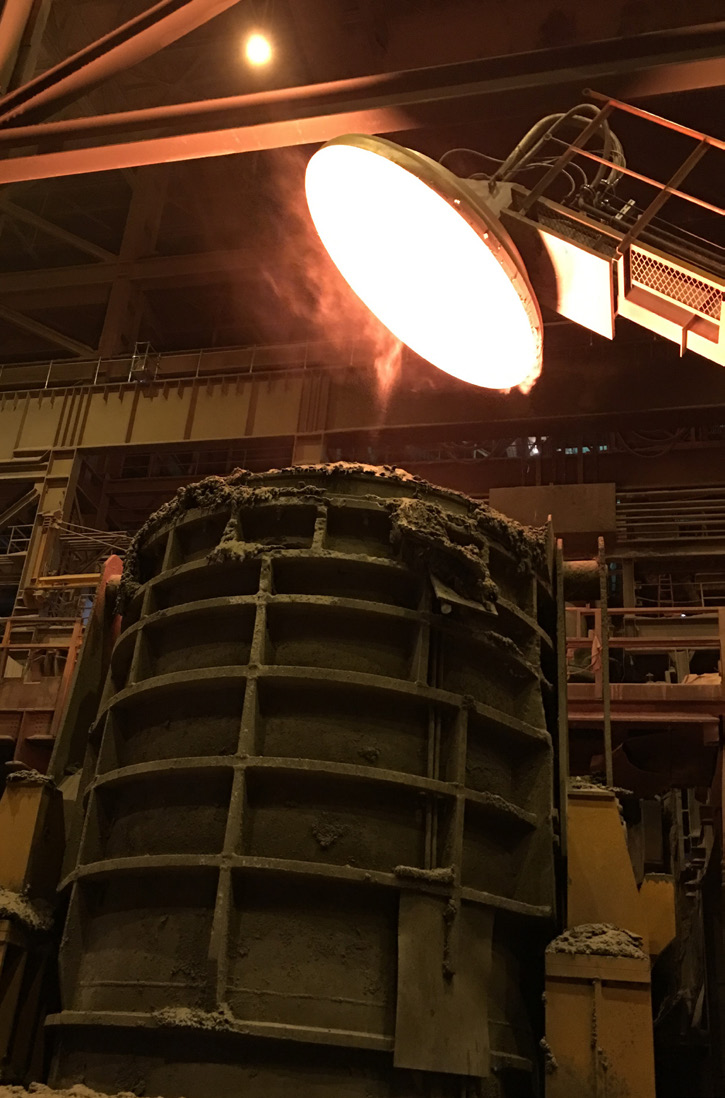


Flameless Oxyfuel Solutions
Increasingly stricter regulations on NOx emissions, combined with ongoing efforts to decrease the carbon footprint, demand the steel industry to use further enhanced processes. The successful development and use of flameless oxyfuel was originally triggered by the need for reduced NOx emissions. Since its full-scale introduction at Outokumpu in 2003, hundreds of installations have been completed using flameless oxyfuel in all kinds of steel reheating and annealing furnaces, aluminium and copper melting furnaces, and ladle and other vessel preheating systems.
In flameless oxyfuel, the mixture of fuel and oxidant reacts uniformly through the flame volume, with the rate controlled by partial pressures of reactants and their temperature. Fundamentally here, using burners or lances or a combination of the two, is the matter of utilizing velocity in a beneficial way when at same time separating the injection points of the fuel and the oxidant, leaving the traditional design of a burner. In flameless oxyfuel, the combustion gases are effectively dispersed throughout the furnace or vessel, ensuring a more effective and uniform heating of materials even with a limited number of burners installed. Although the first installations took place in reheating and annealing, flameless oxyfuel was quickly adopted for preheating of ladles and converters. The lower flame temperature substantially reduces the NOx formation.
At stainless steel production plants such as Acerinox, Outokumpu, and Sandvik, flameless oxyfuel systems are used for the preheating of ladles and converters. Typical results include 50% fuel (and CO2) savings, shorter heating cycle, and higher final preheating temperature.
Focus on Reheating and Annealing
Reheat furnaces typically consume 1.2-1.6 GJ/t of steel, and oxyfuel solutions can reduce fuel and CO2 emissions from reheat furnaces by up to 50%. An example of one such solution is Linde’s REBOX® oxyfuel solutions that have been installed on more than 180 batch and continuous reheat furnaces and annealing lines, with production up to 300 t/h and covering a wide range of steel grades. This has already contributed to decarbonization as the installations decreased the consumption of fossil fuel by 20% to 50%. Partial or full conversion of reheat furnaces from air-fuel to oxyfuel combustion is not only an easy first step to decarbonization, but it also prepares the furnace for subsequent hydrogen fuels. Indeed, oxyfuel combustion will be necessary with hydrogen fuels. For 20 years, flameless oxyfuel has been applied to improve temperature uniformity and secure reduction of NOx emissions – a matter particularly important going forward, including the use of H2. More than 40 REBOX installations have taken place at stainless steel producers. Some examples of those installations are briefly discussed below.
Sandvik uses full flameless oxyfuel converted continuous reheating for its production with excellent results. It is interesting to note that Sandvik’s operations include production of very high alloyed materials (e.g., for rock drills). This clearly demonstrates that flameless oxyfuel has no negative impact when heating even very high alloyed steel grades. Sandvik also has installations using an add-on system that combines air-fuel with oxyfuel to achieve a semi-flameless oxyfuel regime.
Dongbei Steel uses full flameless oxyfuel for a 70 t/h continuous annealing of stainless steel wire rod, a process called Direct Solution Treatment (DST). The fuel used is gasified coal with a calorific value at 2 kWh/m3. Another such DST installation is found at Yongxing, where the fuel is natural gas. This 60 t/h production is the most energy efficient stainless wire rod annealing line in the world, with a total fuel consumption including idling time, etc., at <70 kWh/t.
A Study on Hydrogen in Reheating
Hydrogen combustion results in a 100% H2O atmosphere in the furnace. After Linde performed pilot tests to develop hydrogen flameless oxyfuel burners and to assess the impact of hydrogen reheating on steel quality, capacity, and uniformity in the reheating process, NOx emissions, safety issues, scaling, it was determined that all results were encouraging, and no negative impacts could be identified.
Based on the positive outcome from those pilot tests, engineering steel producer Ovako and Linde decided to under-take full-scale O2-H2 steel reheating in one of the soaking pit furnaces at an Ovako mill that is supplied with green electricity and green oxygen. The full-scale demonstration was carried out last year when 100 tonnes of ball-bearing steel ingots were charged into four soaking pit furnaces, all equipped with flameless oxyfuel. One pit was fired with hydrogen-oxyfuel using REBOX Hyox, whilst the other three operated with their normal LPG-Oxyfuel. After heating and soaking, the ingots were successfully rolled to bars in the rolling mill. A thorough inspection and analy-sis of the final bars showed that heating using hydrogen as fuel does not impact the quality. Göran Nyström, EVP, Head of Technology and Marketing at Ovako, summarized the results: “Hydrogen can be used simply and flexibly, with no impact on steel quality, which would mean a very large reduction in the carbon footprint.”
Conclusions
At most places, use of hydrogen is not yet viable, however, there are actions that can be taken immediately to reduce the carbon footprint of stainless steel production. Areas to focus on are the types of power, potential to increase the scrap charge, and the alloys selected.
Another area to focus on is increased energy efficiency, which can take place without cost penalty and alteration of the existing processes. Use of oxyfuel solutions in the EAF, ladle preheating, reheating and annealing processes, are well proven solutions. Not only would oxyfuel decrease the fuel consumption today, but also – as these solutions are hydrogen-ready – decrease the need for hydrogen going forward.
Achieving carbon neutral stainless steel production is a journey. However, procurement choices and proven technologies are available to implement immediately, which could provide large reduction of the carbon footprint.
References
1. Wei, W. et al., Energies 2020, 13, 5664.
About the Author
Joachim von Schéele received his MSc in Process Metallurgy and PhD in Production Engineering from Royal Institute of Technology (KTH), Stockholm, Sweden, in 1987 and 1992, respectively. Joachim von Schéele has served in many different technical and commercial management roles at AGA, BOC and Linde, and been actively doing business in more than 40 countries around the world. Joachim von Schéele is a well-known speaker and has published more than 200 papers on energy and emission conservation, recycling, and production. He has served as a member of more than 30 boards of companies, associations, and research and education organizations, and as session chairman at many conferences. Joachim von Schéele holds six patents related to combustion and recycling, and is based in Munich, Germany.