The global economy is finally rebounding from almost two years of COVID-19 restrictions and in these early days of a post-pandemic world, some signs of things to come appear to be seen. We are not talking about supply chain issues; for example, manufacturers, distributors, and end users fighting over trucks, containers, and ships to move their goods. This is blatantly a huge inconvenience, for sure, but a temporary one; not expected to last enough to change the major drive affecting the stainless steel market in the coming years: climate change.
By Davi Correia
Climate Change
Societies around the world, in varying grades of commitment, are demanding action on reducing CO2 emissions in order fight climate change. CO2, along with other greenhouses gases, accumulate on the planet’s atmosphere and entrap heat from the sun. The steady build-up of CO2 since the industrial revolution has made CO2 concentration move from 270 to 400 parts per million. Global temperatures have also been steadily rising and many scientists believe that they may be related to change in climate patterns and extreme weather events.
Reducing CO2 emissions requires a multi-pronged approach, as there is no single solution to tackle a problem involving different segments of the economy. For the steel and stainless steel market, three key factors are at play1:
1. Growing demand for sustainable steel products – Many end users have ambitious aims of eliminating carbon emissions from their supply chains.
2. Further tightening of carbon emission regulations – Steelmaking will require new technologies to comply with the more stringent targets.
3. Growing investor and public interest in sustainability – Investment firms worldwide are facing demands from large corporate clients, such as pension funds, to place increasing shares of their money in companies with strong Environmental, Social and Corporate Governance (ESG), policies. ESG reflects the commitment of a particular company with social and environmental factors.
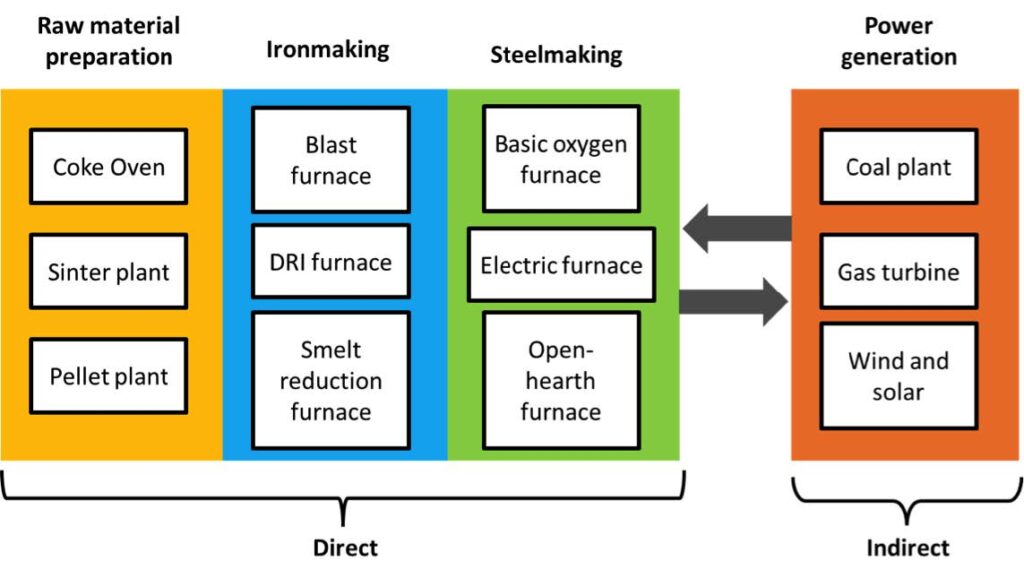

Steel Production: Ever Greener
Traditional steelmaking produces direct and indirect emissions (see Figure 1) and attempts to reduce both shall be part of the sustainable landscape of the up-coming future. “The sector is currently responsible for about 8% of global final energy demand and 7% of energy sector CO2 emissions (including process emissions). However, through innovation, low-carbon technology deployment and resource efficiency, iron and steel producers have a major opportunity to reduce energy consumption and greenhouse gas emissions, develop more sustainable products and enhance their competitiveness.”2
Steel makers use either of two routes to produce steel: integrated blast furnace (BF)/basic oxygen furnace (BOF) or electric arc furnace (EAF). “While integrated players produce steel from iron ore and need coal as a reductant, EAF producers use steel scrap or direct reduced iron (DRI) as their main raw material.”1 Within the current constraints of the technologies, some trends have started to consolidate. It seems that decarbonization for the sector will involve.3
- Maximize use of scrap and minimize use of hot metal in blast furnace/basic oxygen furnace (BF/BOF) steelmaking, currently the dominant technology for steel producers.
- Replace blast furnaces and basic oxygen furnaces with electric-arc furnace (EAF) technology.
- Replace BF iron produced from coke with direct-reduced iron (DRI) and/or increase the ratio of higher-grade iron ore products used in the steelmaking process.
- Replace the natural gas used to produce DRI and the coal used to generate electricity with renewable energy sources.
This is not a comprehensive list, as some other solutions are also being studied, but they are for the moment either limited in scale or technology. For example, biomass reductants are an example of the former. In this process, heated and dried sugar cane, or pyrolyzed eucalyptus, is used as an alternative reductant or fuel. This solution is largely geographic-dependent and hard to scale due to land requirements. As an example of the latter, we can name carbon capture and storage, which has been proven technologically sound only in power plants (post-combustion), but requiring a substantial extra cost to the process. As of now, for steelmaking, it is considered a technology still requiring further development.
Considering the current solutions, decarbonization will not be cheap. Some estimates point that cutting carbon dioxide emissions by 61% by 2050 would require the steelmaking industry to invest more than $1 trillion – and the iron ore industry a further $239 billion.3
What about hydrogen? This element has been touted as a possible solution for many applications that are fuel-intensive, including steelmaking. Hydrogen is a very small element; in fact, the lightest element on the periodic table. Being small and light means two things for industrial applications: that high pressures are required to achieve useful energy densities; and that it is prone to leaking due to its small size. Another problem with hydrogen is how to obtain it. Although it is the most abundant element in the universe, it is highly reactive, meaning that most of the hydrogen on Earth is found in more complex forms such as water or organic compounds. In order to retrieve useful hydrogen from these compounds, energy is required.
Today, the two most common feed-stocks for hydrogen production are natural gas and water. Steam Methane Reforming (SMR) is the most popular, producing the so-called ‘grey-hydrogen’ and also carbon dioxide. Hydrogen can also be obtained by electrolysis of water; and if carbon-neutral technologies are used to generate the electricity required, there is no by-product and the hydrogen thus generated is known as ‘green-hydrogen’. In a nutshell, obtaining hydrogen form natural gas is cheaper, but results in GHG emissions; removing it from water results in zero emissions, but it is more expensive and uses more energy to generate hydrogen that can retrieved from it afterwards.
In steel production, there are basically two ways to use hydrogen. One of them is to replace Pulverized Coal Injection (PCI) in conventional blast furnaces. “However, while the injection of (green) hydrogen into blast furnaces can reduce carbon emissions by up to 20%, this does not offer carbon-neutral steel production because regular coking coal is still a necessary reductant agent in the blast furnace”1.
The second use is related to Direct Reduced Iron (DRI), which is a process that can extract iron from ore via a reducing gas, such as hydrogen. If green hydrogen is used to obtain iron and a renewable-powered Electric Arc Furnace is latter used to obtain steel, this arrangement is capable of delivering carbon-neutral steel. It is worth mentioning that this possibility has already become a reality in at least one place. A company in Sweden delivered the first batch of green-steel only this August4.
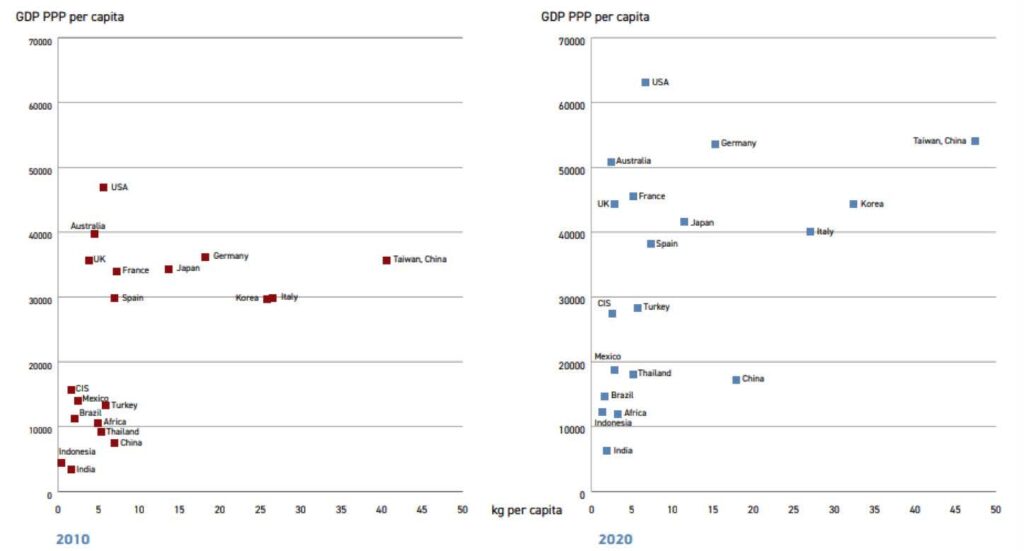
Steel Consumption
Stainless steel is produced in a variety of forms, such as bars, wire, rods, cold rolled flats, coils, sheets, strips, tubes, and castings. These initial forms are then further processed to deliver final products to markets encompassing automotive, building and infrastructure, energy, steel packaging, transport, tool and machinery, and consumer goods. “The global stainless steel market size was valued at USD $ 111.4 billion in 2019 and is anticipated to witness a CAGR (Compound Annual Growth Rate) of 6.3% in terms of revenue from 2020 to 2027”5. Figure 2 shows how global consumption is expected to be in the coming year. End users are scattered all over the world, but certain countries have a higher consumption rate than others, as we can see in Figure 3. The United States has remained leader in consumption in the last 10 years and that position is bound to last. Over the last 20 years, advances in drilling and recovery technology – specifically, horizontal drilling and hydraulic fracturing – have transformed the United States in the largest producer of natural gas in the world, thanks to the exploration of its vast shale formations. Given these new reserves, it is expected that activities related to oil & gas exploration and production, along with petrochemical production, keep the strong drive for stainless steel products in the country.
Another drive for stainless steel products in the United States is the recent passing of a $1tn infrastructure bill by the US House of Representatives. This legislation intends to provide the means to overhaul much of the roads, bridges, and power generation capabilities that have been lagging behind for a number of years. In the case of bridges, for example, duplex stainless steels have grown their market share in building and architecture applications due to mechanical properties and corrosion resistance. They are most suited when high load-bearing capability is required in places where “high concentrations of chlorides are present in the ambient air or where deicing salts are of a concern.”7
On a final note, stainless steel consumption may also arise from some already existing niche applications. For example, environmental concerns have made companies replace plastic takeout containers with stainless steel counter-parts8. It is a small initiative, but given the importance that climate change and plastic waste reduction have taken, this might also become a powerful drive for development of new stainless steel products.
References
1. https://www.mckinsey.com/~/media/McKinsey/Industries/Metals%20and%20Mining/Our%20Insights/Decarbonization%20 challenge%20for%20steel/Decarbonization-challenge-for-steel.pdf
2. https://www.iea.org/reports/iron-and-steel-technology-roadmap
3. https://insights.fastmarkets.com/the-true-price-of-green-steel/
4. https://www.forbes.com/sites/davidrvetter/2021/08/19/how-sweden-delivered-the-worlds-first-fossil-fuel-free-
steel/?sh=557712706b55
5. https://www.grandviewresearch.com/industry-analysis/stainless-steel-market
6. https://www.bbc.com/news/world-us-canada-58152467
7. https://www.worldstainless.org/Files/issf/non-image-files/PDF/Sustainable_Duplex_Stainless_Steel_Bridges.
pdf#:~:text=duplex%20stainless%20steel%20bridge%20can%20be%20built%20with,if%20the%20bridge%20is%20in%20a%20 populated%20area.
8. https://www.cbc.ca/news/science/what-on-earth-takeout-container-reusable-1.6016558
About the Author
Davi Correia is a Senior Mechanical Engineer who has worked at a major Brazil-based oil company for the last 15 years. Correia is part of a multi-disciplinary team that provides technical support for topside piping and equipment of production platforms. During this period, he began to work materials and corrosion and later moved to piping and accessories technology, where he has become one of the lead technical advisors on valve issues. Correia was part of the task force that revised the IOGP S-562 standard and wrote the S-611 standard. Correia has a master’s and a doctor’s degree in welding by the Universidade Federal de Uberlandia.