Gerald Solano has been working in the welding industry for over 35 years. Currently, he is the Senior Technical Advisor on Welding Technology for KBR, a world-renowned engineering company, and is also a current AWS Senior Certified Welding Inspector. Stainless Steel World Americas had the privilege of speaking with Solano to learn more about arc welding, welding procedure qualifications, and his overall thoughts about the industry.
By Sara Mathov
A Rewarding Career Path
Gerald Solano began his career studying Welding Technology at Texas State Technical College. Since graduating in 1986, he has had a long career working in a variety of welding industries, such as offshore subsea equipment, and onshore oil and gas, LNG, ammonia, chemicals, power, pipelines and even as an adjunct welding instructor. This long career has exposed him to working with a variety of base metals and industry codes and standards. “I gained expertise in welding and testing numerous ferrous and non-ferrous base metals. Having been in the industry for 35 years, I have had the opportunity to work in the field, in a metallurgical laboratory and, currently, in welding technology and engineering,” said Solano.
While he was working in the materials engineering lab, Solano learned much about cutting and joining processes, base metal properties, test sample preparation and mechanical testing, plus metallurgical evaluations. “In the lab I got plenty of hands-on experience with welding, performing failure analysis and with mechanical testing – both for WPS / PQR and welder performance qualifications,” he said. “I learned not only about welding, but about base metal properties, failure mechanisms, and industry codes and standards (ASME BPVC, B31, ASTM, API, NACE, AWS D1.1, EN, etc.). I have done everything from welding and inspection in the field, to lab work, to now addressing technical welding issues on Welding Procedure Specifications and Procedure Qualification Records. So, I have had a very interesting career.”
His current role is based out of a home office, with the company KBR, where he is the Senior Technical Advisor on Welding Technology. He has progressed to this role over 32 years with the company.
Current Role and Responsibilities
In his current role, Solano is mainly responsible for reviewing welding procedures to be used in fabrication of pressure vessels, piping, tanks, and rotating equipment purchased by KBR for EPC projects. This involves a great number of suppliers, that are both domestic and international. “I mainly work with Codes, standards and specifications, such as the ASME Boiler & Pressure Vessel Code and B31 pipe codes, plus other related industry standards and recommended practices. My primary responsibility is ensuring that the Welding Procedure Specifications are properly qualified and that we receive a weld map to ensure the Welding Procedure Specifications will be properly applied during fabrication,” said Solano. He advises on all segments of KBR’s projects, including refineries, offshore oil and gas, LNG facilities, and petrochemical projects.
Solano’s main responsibility at the moment is in the engineering procurement side of KBR, although KBR does do construction projects. “In this case, I assign internal KBR WPS’ to our construction sites. However, KBR construction does their own procurement of welding consumables. I just make sure that they are purchasing the correct electrode classifications specified on KBR WPS’,” he said.
“Our engineering procurement department has an approved vendor list, which includes pressure vessel, piping, tank and rotating equipment fabricators. The engineering procurement department will send out a bid for quotes, this includes all relevant codes, standards and specifications. Then fabricators submit their prices for building the equipment. Once our project starts, I receive the welding procedures from the purchase order. We know the vendors are from an approved list and the shops being used have been audited many times.”
Following the review of vendor WPS’, Solano tracks the progress and quality of welded fabrication. “When I send WPS’ back to the suppliers, our inspectors in the shops make sure that suppliers follow the pre-approved welding procedures and alert us to any non-confortion that may arise. Occasionally, we have to reject or comment on vendor WPS’. Sometimes, suppliers do not have a WPS qualified for the base metal alloy that the metallurgist has selected, and engineers have designed with.”
Sometimes, when equipment is procured out of Europe, different base metal standards and electrode classification standards are followed. These may not conform to ASME standards. “ European fabricators follow ISO and EN standards that we can accept, but we need data on the base metals and welding consumables to justify acceptance,” said Solano. “What I always try to reason is, while chemistry content may vary slightly, chrome, nickel, molybdenum, carbon, manganese, niobium, silicon, etc. perform the same function wherever you go. They promote hardness, toughness, ferritic or austenitic microstructures, etc. Of course, one must also understand the effects of heat treatments on the base metal, for example – stress relieving, annealing, normalizing, quench and tempering, solution annealing, and more. So, it is mostly interpreting the code, and deciphering what their standards are compared to what we are looking for.”
Although chemistry ranges may vary across the globe, procedure qualifications and requirements are typically the same. “You have to demonstrate strength across the welded joint, ductility, and soundness. Tensile tests, and bend tests, are commonly used. We also sometimes look for corrosion properties, which includes the chemistry content and ferrite testing as well, not just the mechanical properties side.”
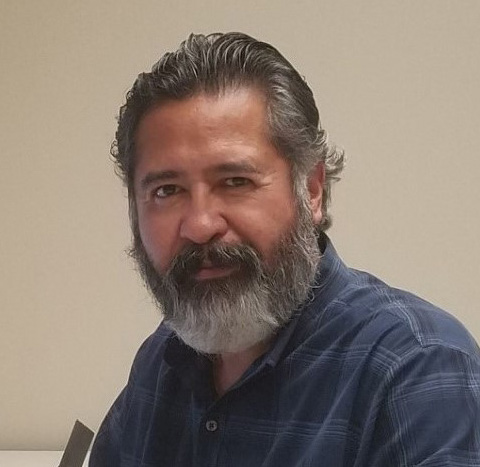
Typical Welding Processes and Welding Variables / Techniques
Solano described the typical welding used at his company as common manual and semi-automatic arc welding processes. “We do shielded metal arc welding, flux core arc welding, gas metal arc welding, and gas tungsten arc welding. KBR does do not do sub-arc welding in the field. However, it is very common to SAW see in the field for tank fabrication” said Solano. “Some of the manufacturers do use more automation, but mostly, fabricators stick to manual and semi-automatic welding processes in the field. Except for perhaps pipeline and tank construction, automation is not as common for field applications as it is for shop applications.”
Welding procedure specification forms specify three different types of welding variables, including essential, supplementary-essential, and non-essential variables. “A change in essential welding variables will influence a change in either the mechanical or chemical properties of the weld,” explained Solano. “A change in the non-essential welding variable may change or influence the quality of the joint. It does not change the chemistry of the weld, and the procedure does not have to be requalified, but you have to specify it, as it may impact the quality.” When notch toughness is a design requirement, supplementary-essential welding variables need to be addressed during qualification and followed during production welding. “You have to document all welding variables down to the specifics.”

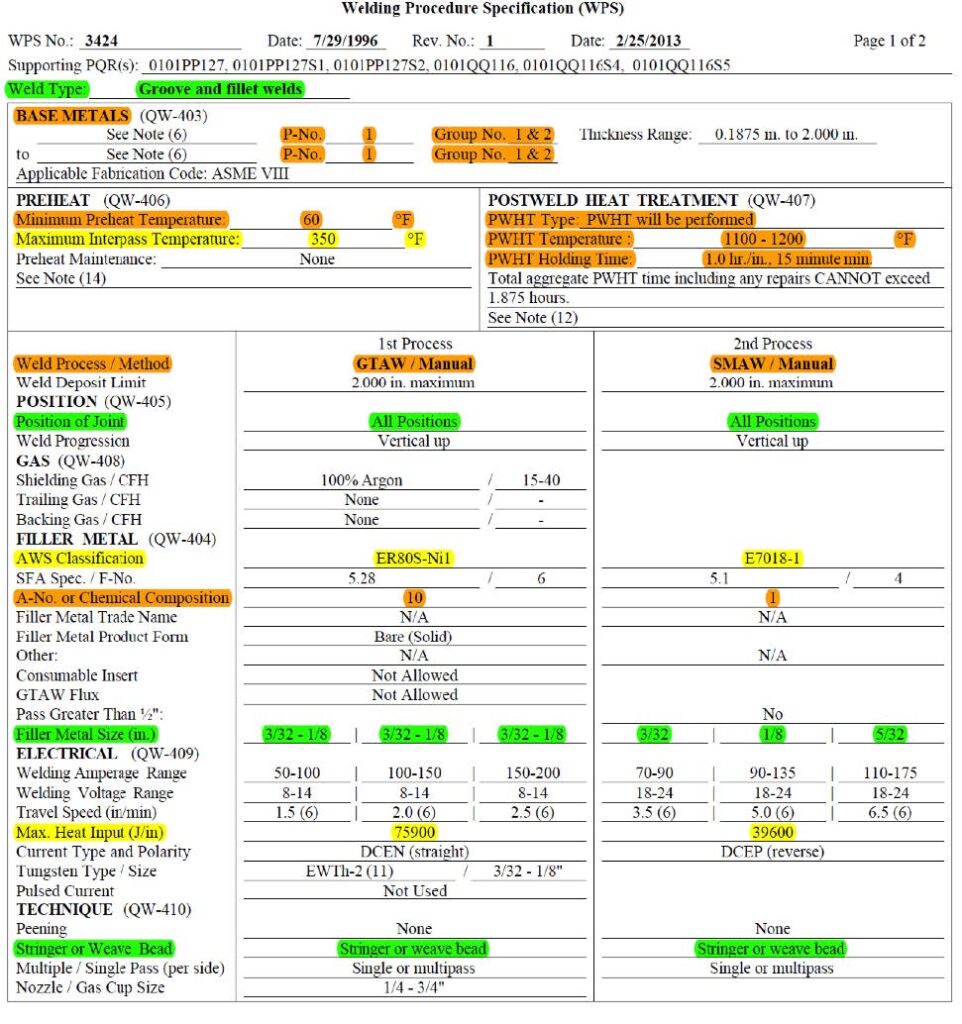
Testing and Challenges
Inspection is also an important part of the quality verification process. Sometimes, welding procedure specifications are not detailed enough or best welding techniques are not used. “Most base metals are fairly weldable, but there are some such as duplex stainless steel and coarse grain, cast stainless steels, where the microstructure is affected by heat input,” said Solano. “An experienced fabricator or welder will understand how important that is. While a shop weld may look good and may pass a hydro test and the required NDE, when you put it in service, the weld heat affected zone could corrode because the heat input was not controlled.”
A challenge Solano has seen in the industry is what he described as a ‘shortage of skilled welders.’ “We will always have a shortage of skilled welders because it takes great hand – eye coordination, plus months to years to learn to run perfect weld beads in out of position weld joints. We have qualified welders, but ones with hybrid experience who can switch from welding chrome-moly steel to austenitic stainless steel to duplex stainless steel or nickel alloys are few and far between. There are many welders who can weld carbon steel plate or pipe, but switching to duplex stainless steel or nickel alloy plate or pipe is different and requires different welding techniques,” he said.
“For example, we had an experience where a welding contractor spent too much time welding coarse grain, cast stainless steel. As a casting gets hot and cold, it expands and contracts, and very coarse grain stainless steel castings can crack during welding. There is technique to weld them to avoid cracking, but if the welding contractor does not have experience welding coarse grain stainless steel castings, there can be problems.”
Another challenge comes in when welding austenitic stainless steel pipe – namely, when welding the root pass. “You have to shield off the backside of the weld joint because of the chrome content and nickel content in 300 series stainless steel. If you do not shield the backside with an inert shielding gas, you get oxidization of the root pass and this will cause the root pass to lose its corrosion resistance. However, using an inert gas purge inside the pipe can become very expensive when making field closure welds. Using the gas metal arc welding process with silicon rich filler metals and specialty shielding gases, you can run a root pass from one side without a backing purge on the back-side. That technique saves money in the LNG world right now since austenitic stainless steel pipe is used exclusively for cryogenic service.”
The Advancements Ahead
As the world is seeing an energy transition away from fossil fuels, many expect all segments of the industry to be impacted. Solano described, in his opinion, that although welders have seen some new advancements in welding processes and base metals, the welding industry as a whole is not impacted greatly. “LNG requires cryogenic temperatures. There is plenty of stainless steel pipe, fittings, forgings, plate, and even castings to be welded in LNG facilities,” explained Solano.
A recent newcomer nickel-iron alloy to the LNG industry is 64FeNi, commercially known as INVAR. “Invar (64NiFe) has a different chemical composition than that of standard austenitic stainless steel (18Cr-8Ni) and might be used more going forward. Invar is notable for its uniquely low coefficient of thermal expansion and is used where high dimensional stability is required. Its use may remove the need for expansion loops in piping systems, but this is still to be seen in the future.”
Even with LNG and green hydrogen, or green ammonia, welding processes and qualified, experienced welders will always be needed, said Solano. “If fossil fuels change to clean fuels, the product is different, but the piping systems and pressure vessels will not change. It will be the same welding processes and base metals,” he concluded.