A native of South Texas, Warnock maintained close ties to the Texas oil field from an early age. He went to work for one of the major fluid power distributors in Houston, who invested in his training, leading to his certification from the International Fluid Power Society as a Hydraulic Specialist. Now part of the DSS Tooling Solutions team, Warnock explained, “Almost every- thing we use is stainless steel, from being immersed in sea water.” He added, “While we are a remote operated vehicle company first and foremost, here we do the tooling that the robots use–equipped largely with titanium robotic arms–for specific intervention applications.” With offices spanning the world, including locations in Canada, Nigeria, Saudi Arabia, Trinidad & Tobago and the United Kingdom, the company currently boasts several patents that place them on the forefront of ROV tooling technology. To this end, Warnock shared his hydraulic expertise and experience in dealing with anti-corrosive materials for subsea applications.
The challenges of designing sub-sea tooling
“Everything we do is subsea; we are immersed in salt water,” said Warnock. While this makes every day quite interesting, he explained how this also presents his team with a number of unique high-stakes challenges that underlie all of the company’s tooling initiatives. Firstly, there is the matter of material corrosion. Warnock explains that al- most everything the company designs and constructs is made of stainless steel, which is capable of withstanding prolonged immersion in sea water, not to mention the various types of media that are being pumped, on the process side. From methanol, methyl ethyl glycol, water glycol and other intervention fluids, these tools need to be very resistant and chemically compatible. For this reason, super duplex is very common, as well as Nitronic 60-type stainless. Likewise, Warnock remarked on the use of a lot of titanium for sub- sea and defense applications, which has the dual advantage of anti-corrosion qualities, in addition to being low in weight.
Secondly, there is the issue of high pressure. “Since we are doing subsea intervention, it’s normally very high pressures that we are working on, anywhere up to 20,000 PSI,” he explained. “Even at depths of 12,000 feet, one must take into account the design characteristics that will allow a tool or device to withstand a little under 5000 PSI of ambient pressure.”
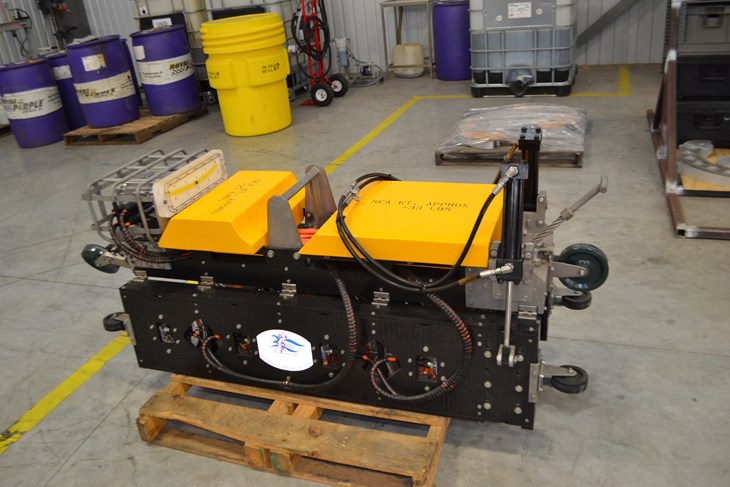
Automated tracking systems
DSS recently integrated a new automated system to assist in parts tracking. When it comes to subsea environments, explained Warnock, whatever labeling is being used tends to disappear, be it through wear, getting sucked in a thruster, damaged by equipment or simply falling off. The implementation of an automated system that not only uses barcodes specifically designed to withstand extreme conditions, but also capable of tracking the entire life of any given part, comes at an extreme advantage. “In many cases, you may spend more in freight and delivery from overseas than the actual worth of the merchandise, just to find out that a given titanium parts shipment, for instance, is only half qualified,” explained Warnock. “So it’s instrumental to have a tracking system whereby we can say, okay this is exactly what was shipped and the product is globally supported,” he adds. The ideal scenario, according to Warnock, is that anyone with a scanner has the capability of instantaneously receiving a part’s exact type and fitting requirements, along with its history, from manufacturing to delivery and throughout the life of the product.
Eureka! A leap in remote sea intervention technologies
Dedicated in part to remote sea intervention and in part to research and development, the DSS team has six patent applications currently in process, pushing the edge of technology in asset integrity devices. “We have a lot of titanium that we use in vessels,” explained Warnock. One project that Warnock shares with Stainless Steel World Americas is their Eureka gamma ray plug localization tool with a titanium pressure vessel, designed to keep weight low and withstand high pressure subsea levels.
The first-of-its-kind Eureka tool, for which Warnock is a co-inventor, is a gamma ray plug localization tool that is providing excellent results. According to Warnock, “Using gamma radiation, we can look through the pipe and see what is going on all the way to the platform. It’s a very easy thing to do that has never been done before.” Helping operators locate blockages, sand bridging, gas hydrates and more, this leading-edge technology is assisting operators in improving flow efficiencies and overall safety; all of which comes at a huge source of pride for Warnock.
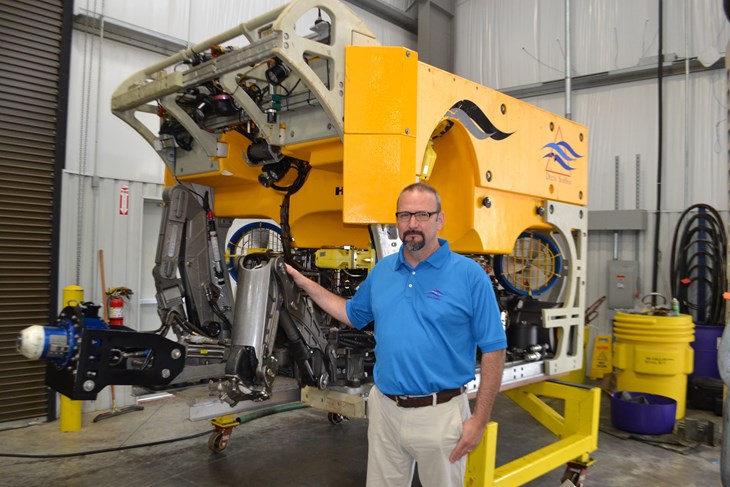
A positive spin on O&G today
It is no secret that the low cost of oil and the resulting industry slowdown has resulted in numerous plant shut-downs and loss of personnel on a global scale. Warnock shed some light on this seemingly grim situation, pointing to a positive industry trend, that he predicts will be of great value in the long term.
“When oil was at 140 dollars a barrel you couldn’t get into any research initiatives, because companies were too busy producing,” he said. So while the question used to be, “when can we get it? ” Now the question is, “how much? ” Warnock suggested that the downturn has resulted in companies now spending money on new initiatives designed to save money out in the field. This movement towards investing in flow assurance and asset integrity projects, stresses Warnock, translates positively in the long term. Companies that were previously focused solely on production, have been forced in many ways to plan better and be more strategic about things, leading to higher efficiencies across the board.
This industry push towards R&D and efficiency-focused initiatives have translated well for DSS. Whether it’s getting an 88,000 barrel a day export line DOT certified in 14 days, or inventing the latest in subsea asset integrity ROV tooling, Warnock commented on the pride he feels in working alongside such dedicated colleagues, as well as his appreciation for the hard-working people who are in the factory manufacturing the various parts that make everything work. For our part, we are glad to have Warnock and the team at DSS forging ahead with new and innovative asset integrity tools, making operations run all the more smoothly in the deep subsea.