In the oil and gas industry, electromechanical cables (EMC) are used whenever services need to be performed during the entire life of the well. As soon as a well is drilled radioactive and sonic tools are lowered to reveal the lithography; this determines where the oil and gas is and whether the well will be economical to produce. Lowering and raising the tools and communicating with them requires an EMC cable.
As it is raised the tool constantly emits a signal, sending information back to the operator to provide a map of the wellbore and the rock formations around it. “Our cables provide the essential communication link between the tools and surface, and with that information the customer can decide whether to go ahead and complete the well,” explains Dustin, who is Global Sales Manager EMC at Camesa.
Once the decision is made to case and cement the well and start production, an EMC is again lowered with perforating charges. These charges punch holes through the well casing into the surrounding rock formation, connecting the wellbore with the oil and gas reservoir.
As part of WireCo WorldGroup, which manufactures, engineers and distributes wire rope, synthetic rope, specialized assemblies and wire products, Camesa specializes in electromechanical cables for the oil and gas industry.
“Our products are typically 30,000-foot long steel cables containing a copper conductor in the middle which conducts electricity. They are armored with special galvanized improved plow steel wires or special alloy wires. The corrosion resistant alloys most commonly used are stainless steel 316, GD 31MO, 27-7 MO and MP35N.”
Correct handling essential
Due to changes in drilling behavior the life expectancy of the cables has reduced in recent years, explains Dustin. “The life of a cable is measured in runs; every time a cable is lowered then lifted out of the well, this is counted as one run.
For years it was common for a cable to achieve 500 to 2,000 runs when used for vertical completions. However now that the market has largely moved into horizontal drilling this is very tough on the cables and lifespans of 200 to 400 runs are now more common. The lifespan of a cable is also strongly influenced by how the operators use and maintain it and the environment it’s being used in. For this reason, correct training is absolutely essential to obtain a full lifespan from each cable.”
The importance of handling these highly complex electromechanical cables correctly is so essential that Camesa has set up an international Cable School to provide onsite, one-on-one training. “Instructors travel the world to train customers how to use the cables properly. We’ve also developed an App that provides a wealth of information to users’ tablets on how to get the longest possible life from cables. Training is typically given to engineers and operators who use the products in the field, as well as purchasing- and asset-managers.
“These are very complex products and we try to educate our customers on important factors such as the correct running speed, the torque inherent in the cables and maintenance that will ensure the maximum lifespan. EMC is a very niche piece of technology, which connects the down-well tools to the surface and they do tend to be overlooked. In reality if they don’t function correctly then literally nothing else will work.”
Corrosive processes
The main corrosive process that Dustin’s team encounters is dealing with sour gas wells. “There are a lot of mature wells that have hydrogen sulfide (H2S) or carbon dioxide (CO2) content. Alloy cables must be used in those wells, although the volume of these, which we sell, is not high because the cost is significantly higher.
As an alloy wireline is five to 10 times the price of a ‘normal’ wireline, typically customers will purchase one alloy cable per camp, or even just one per company and use this on a specialized truck to try and make it last as long as possible.
“Typically the environments that require the use of alloy cables are those where H2S is present. A regular steel cable is not suitable because it will corrode, the wire will become embrittled and there is a risk that the operator will lose tools down-hole.”
Despite the risk, some operators sometimes try to use steel wherever possible and will even run steel EMC into low levels of H2S, explains Dustin. “We don’t recommend using steel in any level of H2S. We always ask our customers to provide details on the environment in which they will be operating including the temperature, pressure, CO2 levels, chlorides, H2S levels, etc.
“This information is run through a computer program called Socrates; it was originally developed for casing and tubulars but it also works well for cables and is the best predictor we have for the survivability of an alloy grade in an H2S environment. Based on this information we make a recommendation and manufacture an alloy EMC to their requirement.”
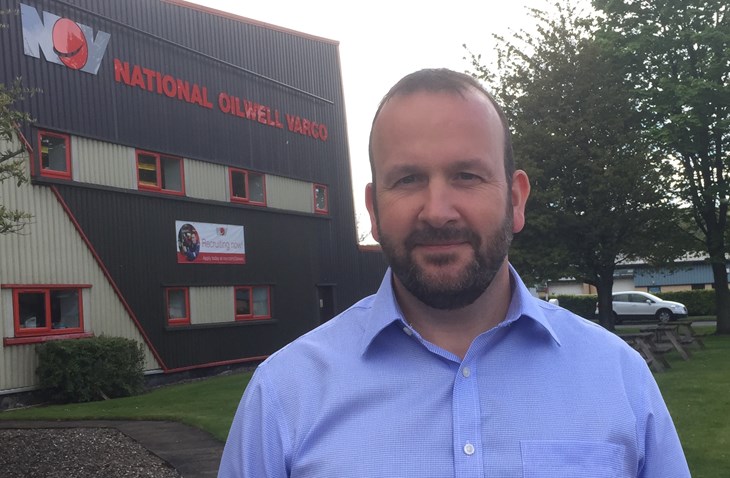
Typical alloys
The alloy electromechanical cables produced by Camesa utilize three grades of materials which are designated generic names, explains Dustin. “We don’t usually use the UNS codes that are associated with a specific alloy because we prefer to purchase from various alloy manufacturers. Our material purchasers negotiate contracts and purchase similar alloys that will meet the same UNS codes.
”The grades we use provide three levels of corrosion resistance: Low (S75 Nickel Stainless), medium (S77 – Enhanced Nickel Stainless) and high (MP35N – Corrosion Resistant MP35).” “We don’t sell a lot of MP35 cables because the alloy is almost pure nickel and subsequently extremely expensive. A lot of customers will initially request an MP35 line but generally they don’t need one. This alloy is only required for the worst conditions and those environments are quite rare. Instead we discuss the customers’ requirements, what the downhole environment will be and what levels of H2S are they encountering and from there we can figure out what kind of alloy they actually need for the most cost effective price.”
Corrosion failures = lost tools
The importance of selecting the correct alloy is underlined by the potentially disastrous consequences of a corrosive failure such as embrittlement in the EMC, which can lead to tools being dropped into a well.
“This does happen occasionally and it means the customer will have to carry out a ‘fishing job’ where a second cable is lowered to retrieve the tools. Depending on how bad the job is it can take up to a month to recover the lost tool. Every day a rig is on location it costs money; if it’s an offshore well you’re looking at between USD $500,000 and USD $1 million per day in rig costs alone, so this is a very costly mistake.”
“Customers often want to push the boundaries and minimize costs where they can, but if they have a failure the results can be dramatic. There is also the risk of damaging the cable itself; of damaging the wellbore to the point that it has to be shut in; and in the case of radioactive tools any potential recovery is extremely complicated. Another consideration is that the tools themselves are very expensive; often over one million dollars. In summary, losing tools is an extremely costly mistake so it’s essential that the correct alloys are specified for the cables holding them.”
Trends in recent years
The past five years have seen a marked increase in demand for alloy wire lines and Dustin expects that trend to continue. “As wellbores or the fields themselves age and the reservoirs become depleted H2S becomes more prevalent. In some cases wells which used to be sweet turn sour over time. For this reason there is a significant trend for more alloy cables in the Middle East. Many of the oil fields in the region have been producing for 50 or even 60 years so we’re starting to see a lot of alloy material sold into that market.”
“Fracking presents another set of problems which are also leading to an increased demand for alloy wirelines. The incorrect use of biocides can introduce bacteria to the wells, which can create sour environments. Another reported problem occurs when insufficiently treated water is used and bacteria are introduced into the well. As the bacteria grow, reproduce and consume oxygen they can actually create an H2S environment.”
Wish list for materials manufacturers
Given the corrosive environments that EMC cables operate in, it’s not surprising that Dustin has some requests for materials suppliers. “The most important thing that would help us is an alloy that has similar tensile strength as steel. One of the downfalls of the alloy cables is that an equivalent steel cable has 10-15 percent more breaking strength in the same diameter cable simply due to its mechanical properties.
“Another significant challenge is the lack of a reliable database detailing what alloys should be used in certain environmental conditions. The problem is that cables are very dynamic; for instance they run over sheaves and are pulled in and out of wells, the temperature gradients aren’t consistent over the length of the wellbore, etc. The behaviour of the operators is also a factor; how they store the material, if they subject it to mechanical damage… it’s a challenge to write software that can accurately predict how cables will perform. However a program which would take some of these variables into account and predict the performance of an alloy wireline would certainly be a great benefit.”
Background in the business
With his extended family having a long background in the oil and gas industry Dustin was destined to follow suit after graduating with an economics degree. “I joined Halliburton as a BDFA (Business Development Field Associate) which meant I joined the oil field crews for 18 months. I literally put on a hard hat and steel toes, took a hammer and worked with the fracking and cement crews to learn all about the oil fields from the ground up. It was a great experience, which taught me all the ‘ins and outs’ of the oil field and how a well is drilled.
“After five years I had moved up to managing accounts. Subsequently I was invited to join the WireCo sales team and as Halliburton is our biggest customer it was an ideal move.”
Today Dustin is Global Sales Manager, overseeing all of WireCo’s sales globally, with a team around the world who report directly to him. His team is “intricately involved” with the company’s R&D group and is usually responsible for initiating projects.
“Typically customers want to drill deeper, want stronger cables and want to send more power down the copper. The addition of fiber optics is also becoming a common request to help with data speeds. Another frequent request is for hydrogen sulfide (H2S) resistance, while CO2 corrosion resistance is a constant battle. Sour gas well customers usually want to know the minimum amount of alloy they can get away with in corrosive environments–this is a query we deal with on a weekly basis.”
“One of the best things about my job is that my days are not regimented. It’s not unusual for me not to know where I may be going in any given week; on Mondays I evaluate where I’m needed. This could involve visiting a client’s site, or I may need to schedule an international trip. I’ve just returned from Australia where I attended the World Geothermal Congress Expo. I took the opportunity to visit Brisbane, Melbourne, Sydney, Perth and Adelaide to visit customers and gather market information. The variety of the job is one of the parts I enjoy the most.”
The Hydrochloric Acid Challenge
Occasionally Camesa receives a request for cables to operate in a hydrochloric acid (HCl) environment, particularly in horizontal wells. A hydrochloric acid spearhead is used to pump acid down into the perforation zone, after which an electromechanical cable is used to lower a tool and charges are fired in the acid.
“HCl is extremely corrosive so wireline operators often request HCl resistant alloys,” explains Dustin. “However we have not found any alloy that is resistant to hydrochloric acid; the only solution we can use in this instance is plastic packaging to prevent corrosion. If there is an alloy manufacturer out there who can provide an HCl resistant material I would very much like to hear from them.”
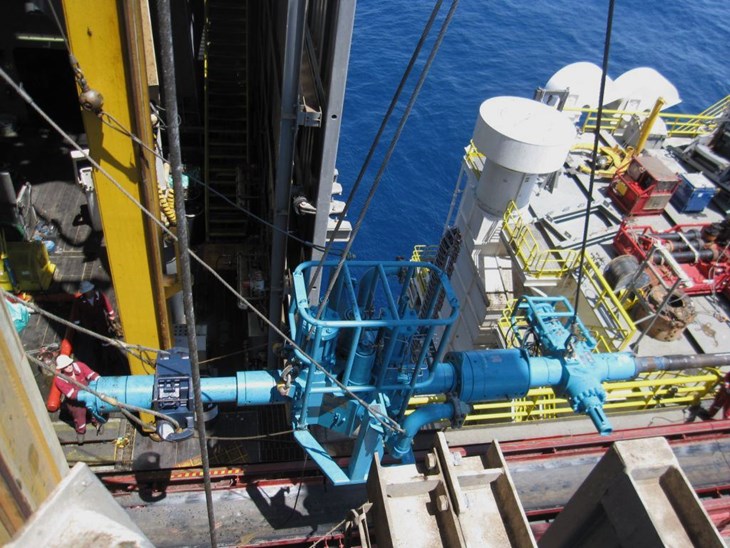