As Corrosion Resistant Alloys celebrates its 20th anniversary this year, Stainless Steel World Americas was pleased to sit down with Justin Kates, Business Development, and Tommy Najar, Vice President, to learn more about the company history, values, and unique model, as well as the vision for the future ahead.
By Sara Mathov
Background and History
Since its inception, Corrosion Resistant Alloys (CRA) has had a singular consistent goal: “to be the fastest, most reliable, quality provider of corrosion resistant alloy pipe and tube in the world.” Beginning as a distributor to the upstream oil and gas industry, CRA transitioned to a manufacturer/distributor, learning along the way. “While most oil country tubular goods (OCTG), mechanical tube, and schedule pipe can be satisfied through direct mill orders, more unexpected project needs are surfacing with high urgency and extremely quick lead times. Throughout our history, we have adapted the way we do business to accommodate our customers’ most critical needs and highest quality standards,” stated Kates.
CRA learned that the real struggle of their customers was accurately forecasting what was needed. This led to excessive inventory build-ups where high carrying costs were real and impactful. “The solution was to improve upon the inefficiencies of distribution, complement the standard mill deliveries, and fi nd a way to offer the customer exactly what they need, when they need it. From this, the just-in-time manufacturing model we operate on today was born,” added Kates.
The just-in-time model, founded on the pain point of not being able to predict the future, offers expedited delivery times, accommodates non-standard mill quantities, and allows for product customizations. “Distributor inventory fluctuates between excessive supply and material shortages based on industry cycles, often leaving customers unable to obtain what they want when they want it. Our model ensures we can provide them with a solution,” said Najar.
The JIT Manufacturing Model Today
With its rich history and strong reputation, CRA continues to provide unique value to its customers. “Customization, flexibility, and innovation are our specialty, and the need for this in the alloy pipe and tube space is growing,” said Najar.
Historically, the company has provided material primarily to the upstream oil and gas sector, and this continues to be the main application of its products.
“We provide martensitic, stainless steel, and nickel alloy tubulars for OCTG and mechanical tubes. We also provide raw material for downhole equipment,” said Kates. “Recently, we have expanded to serve multiple industries where the JIT model adds unique value, including aerospace, chemical processing, deep space, defense, marine, power generation, refining, waste disposal, geothermal, hydrogen production, and carbon capture (CCUS). Our alloys are best suited for high temperatures, high corrosion, high pressure, or any combination of these factors.”
“We specialize in non-standard mill quantities, unique specifications, and quick turnarounds. Our entire process is set up to execute in as quick as two weeks if necessary. We reserve mill capacity and sacrifice volume to accommodate the most urgent requirements,” stated Najar.
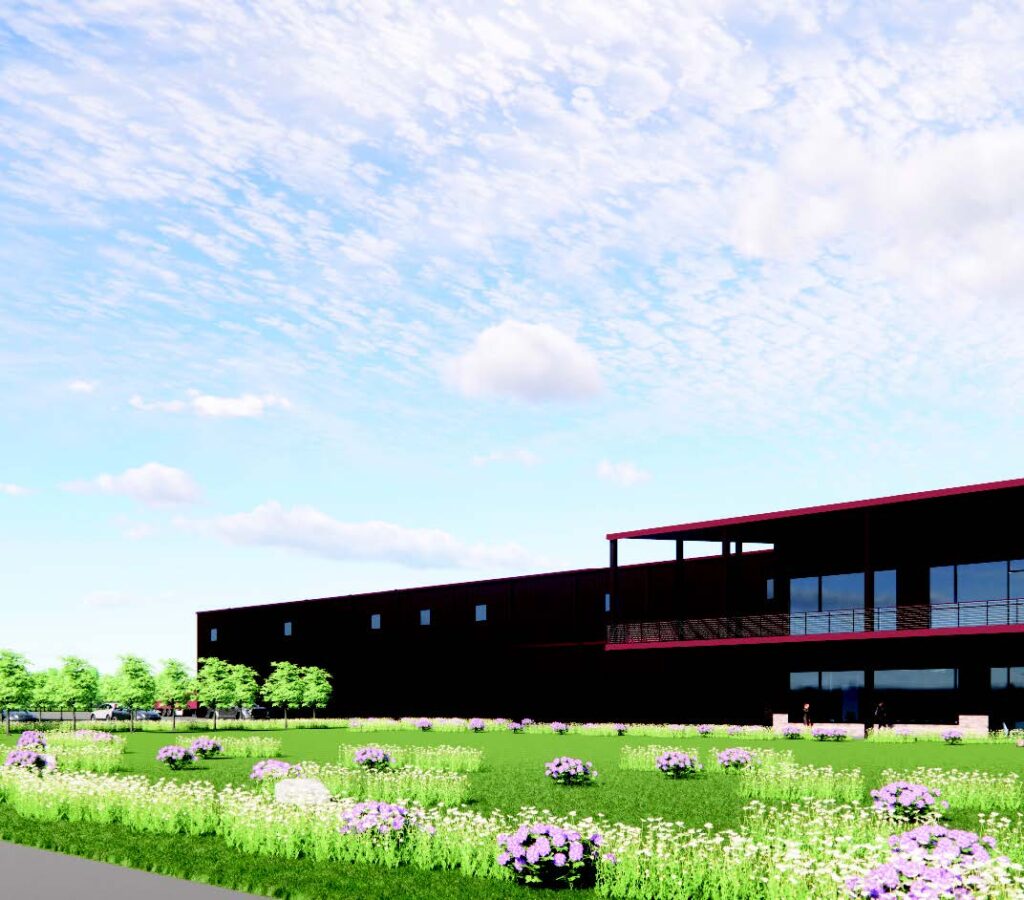

Dedication To Quality & Reliability
CRA’s manufacturing process is similar to other manufacturers; however, their unique value is in the way timelines of operations are managed. “The material starts off as an ingot or continuous cast billet. It is then hot worked to achieve a sound wrought structure and converted to a hollow tube shell by hot working or trepanning. The choice of which process route to use depends on several variables, including quantity and the customer delivery need. The tube shells are annealed to obtain the required microstructure, achieve the finish size and mechanical properties, and then straightened. Finally, non-destructive, destructive, and visual testing are done, then final cutting inspection, and marking,” said Kates. Through the management of this process, CRA can reduce lead times, improve delivery reliability, and accommodate third-party inspection and customer requirements. CRA maintains an ISO certification and is one of only two mills in the USA with an API 5CRA license.
“Just-in-time can often be synonymous with ‘poor planning.’ I previously thought that this was, always the case in my prior roles in Completion Engineering and Operations at international operators. At CRA, we are redefining just-in-time. We focus on reducing the risk of carrying high-cost, obsolete inventory while assuring material is ready when it is needed for our customers. This creates unique options as the sup-ply/demand pendulum is constantly changing. Just-in-time is truly, get what you need, when you need it,” explained Najar.
As a just-in-time manufacturer, CRA is able to pro-vide customization, flexibility, and innovation that is unmatched. Each order is tailored to fi t the customer’s needs, ensuring the correct materials, quantities, and times. “By working alongside our customers from design through construction, we are able to co-create a solution that best accomplishes their goals and objectives on a project while meeting their intended timeline and product specifications,” stated Kates.
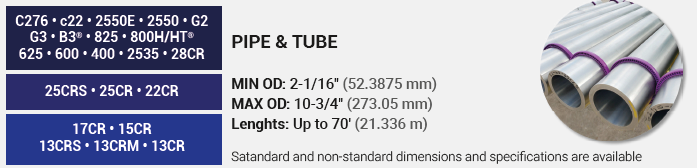
The Future of JIT Manufacturing
The nature of the just-in-time model means customers with unique obstacles come to CRA for help. CRA enjoys rising up to meet the various challenges industries present. To support business in all industries utilizing high alloy tubulars, CRA is opening a new facility in Brenham, TX (facility rendering pictured above). “This facility will be a significant advancement of our vision of being the fastest, most reliable, quality provider of corrosion resistant alloy pipe and tube in the world,” said Kates.
The new manufacturing facility will bring all processes to one location on more than 40 acres. “Equipment that will be housed on campus includes cold pilger mills, rotary and press straighteners, various CNC’s and machine tools, band saws, and pipe inspection facilities. For our customers, this means getting high quality, specialty alloy, seamless pipe and tube just-in-time to meet their project timelines. On a broader scale, it means our ability to better provide creative solutions custom-tailored to changing industry demands,” concluded Najar.