Stainless steel is a robust, corrosion-resistant material, and its integrity is highly dependent upon skilled operators that work diligently to ensure the optimization of the material’s lifecycle. Whether it is checking for the presence of corrosion, or for imperfections that might lead to cracks, having systems in place to reliably test and inspect stainless steel will harness the material’s innate durability, placing reliability at the forefront while simultaneously preventing unexpected shutdowns.
This article will revisit the basics. It will provide a brief discussion of how and why stainless steel is tested or inspected, and shed light on the tools and methodologies most commonly utilized to maintain optimal results. It will also discuss the impact of effective testing and the potential of the material’s lifecycle, which can be an effective tool in emission abatement.
By Justin Yule
Nature and Characteristics of Stainless Steel
Stainless steel is a metal alloy of iron, chromium, and other metals like nickel, molybdenum, and carbon. Different blends with different ratios of these metals will produce different types of stainless steel. Chromium is a key element, imparting to the alloy the ability to build a passive oxide layer when exposed to oxygen making this layer is self-repairing. In addition to this, newly produced stainless steel is placed in an acid bath to enhance the passivating process. The result is a product that is both useful and aesthetically appealing.
Stainless steel offers reduced maintenance costs over the long term as it resists corrosion, but it also bears a surface that makes it a reliable building material. It is, however, highly vulnerable to chlorides that destroy the passivating oxidizing film and can corrode the metal. Chlorides are detrimental to the lifecycle of stainless steel, and unfortunately are widely present in the environment. Therefore, special care must be taken to check for damage to the surface of stainless steel before cracks or corrosion develop. The good news is that the metal rewards diligent monitoring with remarkable durability.

What Variants Are There of Stainless Steel?
Stainless steel is a category of metals with many variants. First, there are distinct families of stainless steel, each identified by a different ratio of the key metals. The primary families are: Austenitic, Ferritic, Duplex, and Martensitic. Austenitic is the most widely used. It is understood to be the most corrosion resistant and it is generally non-magnetic. Ferritic stainless steel has no – or very little – nickel, and as a result is a more cost-effective variant. It is generally a tougher and more creep-resistant form than austenitic but carries an inferior surface. Consequently, it is a favored option where visual appeal is not a consideration.
Duplex stainless steel is a combination of the Austenitic and Ferritic variants, capitalizing on the corrosion resistance of the former and the high strength of the latter. This combination is a recent innovation and is exhibited in many proprietary alloys. The Martensitic family of stainless steel is characterized by hardenability and strength, making it a common pick for valves, turbines, and other mechanical parts. Among the families of stainless steel, it is important to note the various grades that are available. These are specified by numerical identifiers (UNS, Unified Number System) and indicate the precise characteristics of the metal. Numerical identifiers of grade are established by system standards. The most common standards are SAE (Society of Automotive Engineers) and ASTM (American Society for Testing and Materials), but others include BS (British Standards) and ISO (International Organization for Standardization).
What Causes Corrosion Resistance in Stainless Steel?
All metals will corrode in certain conditions. Corrosion leads to the progressive weakening and disintegration of the metal, and will jeopardize its function. As stated above, the chromium in stainless steel solves this problem by forming a passive oxide layer when exposed to oxygen. This means that chromium is reacting to oxygen just as any metal does, but the consequence is not rust but a passive, inert layer that is highly unlikely to react with most chemicals. In fact, the aspect of stainless steel that makes it corrosion resistant is the same aspect that makes it a hygienic metal. The passive oxide layer produced by chromium is understood as self-healing because, if a section of metal was cut away from its surface, the suddenly exposed metal – and the chromium therein – would react anew with the oxygen in the air, reforming the layer. With stainless steel able to fend off corrosion so well, it is important for operations teams to be familiar with potential vulnerabilities.

Why Does Stainless Steel Rust?
Stainless steel corrosion occurs when environmental conditions cause that passive layer to break down. If the protective oxide cannot reform in a given circumstance, corrosion reactions can progress rapidly. The two most common forms of corrosion are pitting corrosion and crevice corrosion.
Pitting corrosion occurs when chlorides, a common instance being sea-water, react with and start to dissolve the protective layer on stainless steel. Pitting is visible to the naked eye as reddish-brown iron oxide deposits alongside pits on the surface of the metal. However, pitting corrosion can also lead to deeper hidden cavities that will continuously expand and rupture the metal. Common trouble spots for pitting include upward-facing surfaces where liquid like sea water can pool, or downward facing surfaces where droplets gather. In either instance, as the solvent evaporates, the chlorine gets more concentrated in the remaining liquid making it increasingly corrosive. Crevice corrosion is similar to pitting but occurs specifically in crevices where chlorides pool out of sight. Common problem areas can include under clamps, between adjacent tubing, or underneath deposits that sit uncleaned.
What Is a Crack?
Cracking is another possibility for stainless steel that needs to be anticipated and prevented. When undue stress is placed on a metal, damaging the atomic bond strength and separating the material, cracking occurs. While the threshold at which cracking occurs for a given metal can generally be anticipated by the atomic bond strength, ‘artifacts’ in the fabric of the metal, like inclusions or bubbles, can amplify the experienced stress at a specific region.
Another type of cracking is SCC (Stress Corrosion Cracking) which arises when a corroding component is stressed by a load, or by residual welding stress. SCC can be observed as fine clusters of parallel cracks, sometimes eventually forming pinholes. This indicates that SCC has pierced through the thickness of the metal. Taking into consideration that cracks can result in crevice corrosion, it becomes clear that cracks and corrosion are compounding risks; the presence of either increases the risk of the other.

The Broader Importance of Testing and Inspection
Before looking at the range of methods for testing and inspecting stainless steel, it would be helpful to situate and motivate this topic within a broader project. Testing and inspecting stainless steel for imperfections, cracks, and corrosion is not merely a question of prudent maintenance; it is a contribution towards the longevity of building materials and sustainable construction practices. Stainless steel itself brings a lot of possible solutions to the question of greener industry: it is a durable material that does not need to be regularly replaced; it is one hundred percent recyclable; it is a lighter metal requiring less fuel to transport; and it reflects heat well, so that when used in construction it can reduce the need for air-conditioning. To be a true green solution, however, two other things are needed: innovation in green milling, and diligent inspection practices.
Environmental Considerations
More sustainable production practices are sorely needed because the traditional practices are carbon intensive; for every kilogram of stainless steel produced, seven kilograms of CO2 are emitted. Luckily, efforts are underway to change the way things are done. Electric Arc Furnaces (EAF) and Submerged Arc Furnaces are facilitating the switch away from coke-fueled blast furnaces. While the electrification of mills is not new, integrated mills are now turning to EAFs as, alongside being an inherently less carbon intensive process, they make more efficient use of energy, and can be quickly turned on and off, saving time and money.
Where electrification is yet to be implemented, carbon capture and utilization methods are also finding usage. At the cutting edge, Hydrogen Reduction (H-DRI) is an innovation from Europe that can cut emissions by about 95%. Instead of CO2, the waste product of this process is water. However, H-DRI facilities are expensive to set up and currently reliant on public subsidy. In fact, much of the effort to achieve “green steel” is ultimately reliant on the presence and resilience of renewable energy infrastructure. Government policy is the major variable in the sustainability of steel.
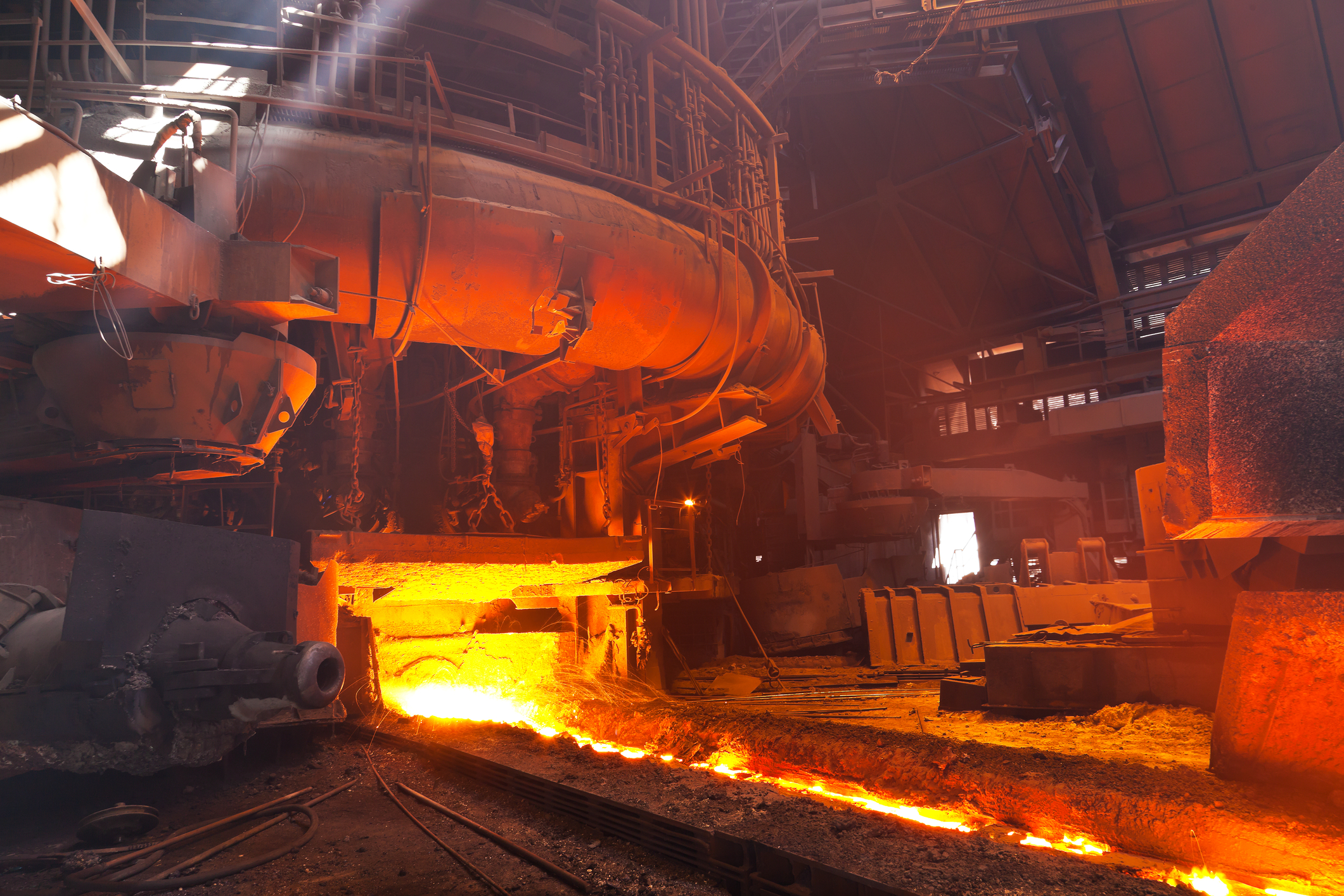
Testing and Inspection
But what can a technician or operations team do to provide diligent care? What are some possible methods that offer to test and inspect stainless steel?
Final Words
The reliability of stainless steel is dependant upon comprehensive testing and inspection practices. From its chemical composition to pain points and failures, testing not only extends the lifecycle of the metal, but it contributes to safe and sustainable applications across the board. Emerging technologies aiding in inspection methods continue to grow with the global push towards emissions abatement while ensuring the integrity of stainless steel goes beyond maintenance.