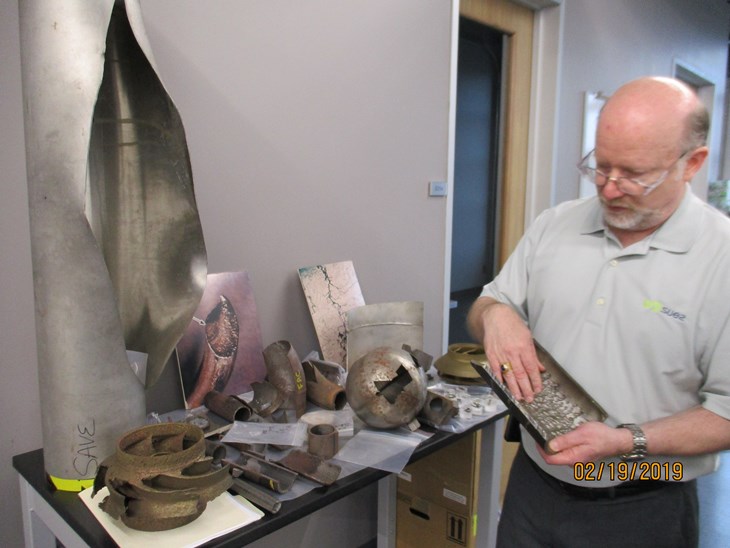
Located just north of Houston, SUEZ’s modernized Lab in Tomball houses 80 employees, 50 of which are highly-trained engineers, chemists, and technicians, who focus on the continual growth of the company’s customer base, through the research and development (R&D) of water and industrial process treatment solutions.
With more than 35 years of experience in metallurgy, Esmacher first found himself in the water and industrial process industry in the early 2000s working at SUEZ WTS, which was then known as Betz Laboratories. Prior to the purchase of the business by SUEZ in September 2017, General Electric (GE), made multiple investments in the company, including the procurement of several equipment-solution companies, to complement SUEZ WTS’s leadership in the chemical treatment sector in the water and process industries.
This new Tomball Lab is another significant investment recently made to upgrade and expand SUEZ WTS’s capabilities and build upon the company’s impressive portfolio of innovative solutions and technologies. Esmacher shares his excitement about how the new Lab is already giving the SUEZ team the opportunity to use advanced testing for various applications, which then opens the door to improving solutions.

Testing capabilities and new technologies
As a global water and industrial process treatment company, SUEZ sees various types of corrosive waters on a daily basis, and therefore, needs to have the correct analytical and simulation techniques available for each situation in order to provide its clients with the best solution. With the new facility came opportunities to expand technology and testing capabilities, and the ability to better cater to the company’s clients.
Water purification
As an example of SUEZ’s leadership in providing novel equipment solutions, the ZeeWeed* ultrafiltration (UF) hollow-fiber membranes are designed for drinking water, wastewater, tertiary and water reuse applications, as well as industrial feed water and reverse osmosis (RO) pre-treatment. The advanced technology is operational in thousands of municipal, industrial, and commercial applications worldwide.
Treatment for specialty additives
Refineries and chemical plants rely on SUEZ’s process treatment for specialty additives. “If we receive samples from customers who have troublesome crude, we help them optimize the treatment in terms of crude stability, emulsion breaking, anti-fouling and corrosion control, in the processing of crude oil. In addition, our scientists in the Tomball Lab help key clients in the chemical process industry troubleshoot problems and propose innovative and environment-friendly solutions, say for polymerization control in production of various industrial monomers such as ethylene, styrene, butadiene, etc.,” Esmacher explains. “For this, our customer service and R&D Labs are crucial. This Lab is where the technicians work on problems seen at the various plants where, for example, a heat exchanger has been introduced, and deposition or corrosion has been found during the troubleshooting process. The Lab helps determine what is wrong via analytical testing, which in turn can provide direction for the selection of treatment additives to optimize up-time and process capabilities.”
“A majority of the Lab equipment simulates operating conditions of a refinery or chemical plant environment. This type of equipment allows us to pinpoint factors that can cause fouling or corrosion at operating plants. In addition, we can experiment with advanced, patented treatment ideas in the Lab before they are subject to full field trials, which is a big advantage,” Esmacher states.
esponse, on-site analysis of crude oils, oil blends, and other hydrocarbon fluids to measure their potential instability and incompatibility and determine if any actions are needed to ensure the crude/blend can be processed without difficulties. This program is part of SUEZ’s investment in its Integrated Solutions for Refining development.
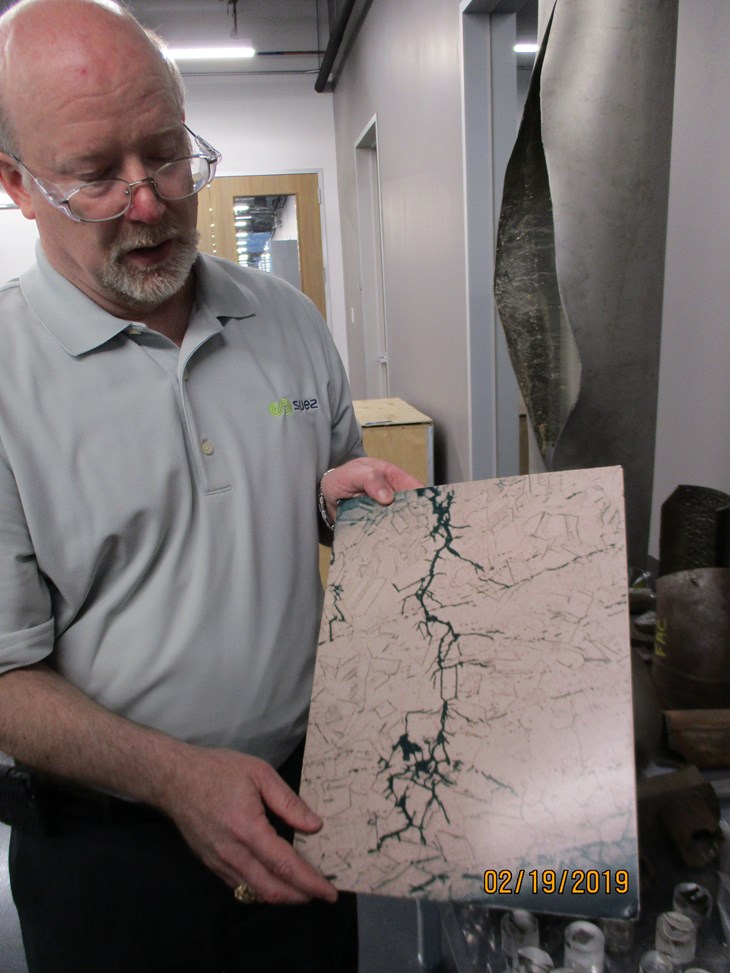
Testing for deposits or corrosion
A newer instrument seen at the Tomball facility, is the state-of-the art Inductive Couple Plasma (ICP) unit. “The ICP helps us to accurately detect very low levels of materials in the water, such as trace metals. The amount of dissolved metal in the water is important information to have,” Esmacher comments. “If you are seeing steel corrosion, for example, it means you have a lot of iron in the cooling water. The ICP is not only a way to acquire accurate values, but to also trace metals in various water systems, not just in cooling water but also in process water environments.”
In some samples there can be hundreds of thousands of small corrosion pits, and each pit has an encapsulate history of how the corrosion product mound or deposit has formed over it. “This is an example of using the SEM and SEM-EDXA to document how corrosion progresses versus established electrochemical corrosion theory, and how we can intervene with a corrosion control program at the customer site.”