An industrial wonder of the world, Hoover Dam is a concrete arch-gravity dam in the Black Canyon of the Colorado River, located near Boulder City, Nevada, on the border of Arizona. Constructed between 1931 and 1936 during the Great Depression, it was originally known as Boulder Dam. It was officially renamed Hoover Dam, for President Herbert Hoover, by a joint resolution of Congress in 1947.
The Stainless Steel World Americas team traveled from Las Vegas to Hoover Dam—one of 20th century’s most significant architectural marvels. The team toured the dam and power plant to learn about the complex mechanics of the structure, its challenges and the use of different components including valves, hoses, pumps, and stainless steel products at the dam.
By Sarah Bradley & Angelica Pajkovic
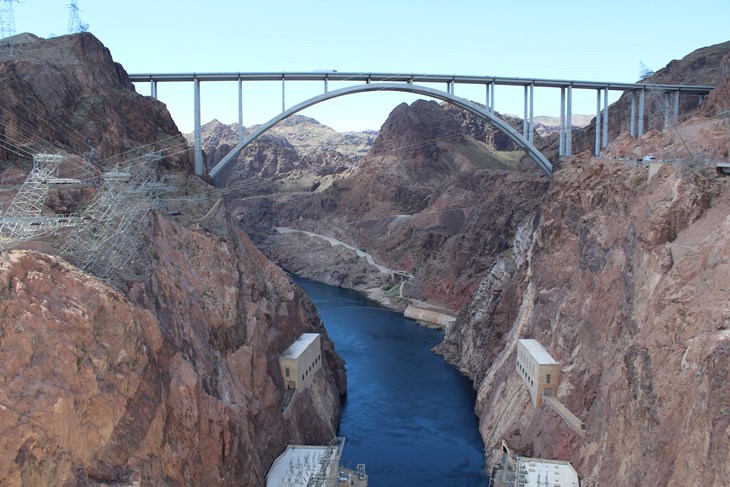
The Black Canyon and nearby Boulder Canyon had been evaluated for their potential to support a dam that would control floods, provide irrigation water and produce hydroelectric power. Thousands of workers were involved in the construction of the engineering feat. Despite being an industrial first, as such a large concrete structure had never before been built, the project was completed more than two years ahead of schedule and the dam was turned over to the federal government on March 1, 1936.
While still a major energy supplier, Hoover Dam is also a major tourist attraction, welcoming nearly a million people each year. Taking in the scenic Nevada landscape, we were excited for the opportunity to tour the dam to learn about its engineering and architectural integrity. We met with John Jorgenson, Weldshop Foreman and Douglas Hendrix, a Bureau of Reclamation Public Affairs Specialist, in a scenic office overlooking Lake Mead—the largest manmade reservoir in the country by potential volume capacity – which was built with the dam’s construction. The lake now serves as a reservoir to the dam and is an integral part of all the functioning’s of the structure.
Hendrix comments, “We are at 41% capacity now in the reservoir. We had more than 100% precipitation this year, so our recovery will be decent, but after 19 consecutive years of drought, it is going to take more than one good above average snowfall or precipitation year here to get back to the full recovery of these reservoirs.”
The dam was considered a phenomenal feat at the time of its completion. “It is considered one of the seven greatest industrial marvels of the world,” Hendrix states. Hendrix discusses how the facility has more than 17 generator units, and when at full reservoir capacity, the dam can generate a solid 2,500 megawatts of electricity—just enough power for over 1.5 million households. Due to the current reservoir capacity and a droppage of the centrifugal force of water at the penstock, the plant is able to maintain about 75% of the structure’s capacity.
Jorgenson himself has come a long way throughout his career. He worked as a journeyman, working in cavitation repair—which is damage caused in turbines due to rapid changes of pressure in a liquid leading to the formation of small vapor-filled cavities. Jorgenson also gained experience working for several years at Parker and Davis dams, both located downstream from the Hoover Dam. Jorgenson oversees leading the maintenance at the power plant. He and his crew take care of the spillways, the intake towers, maintaining piping systems, etc.
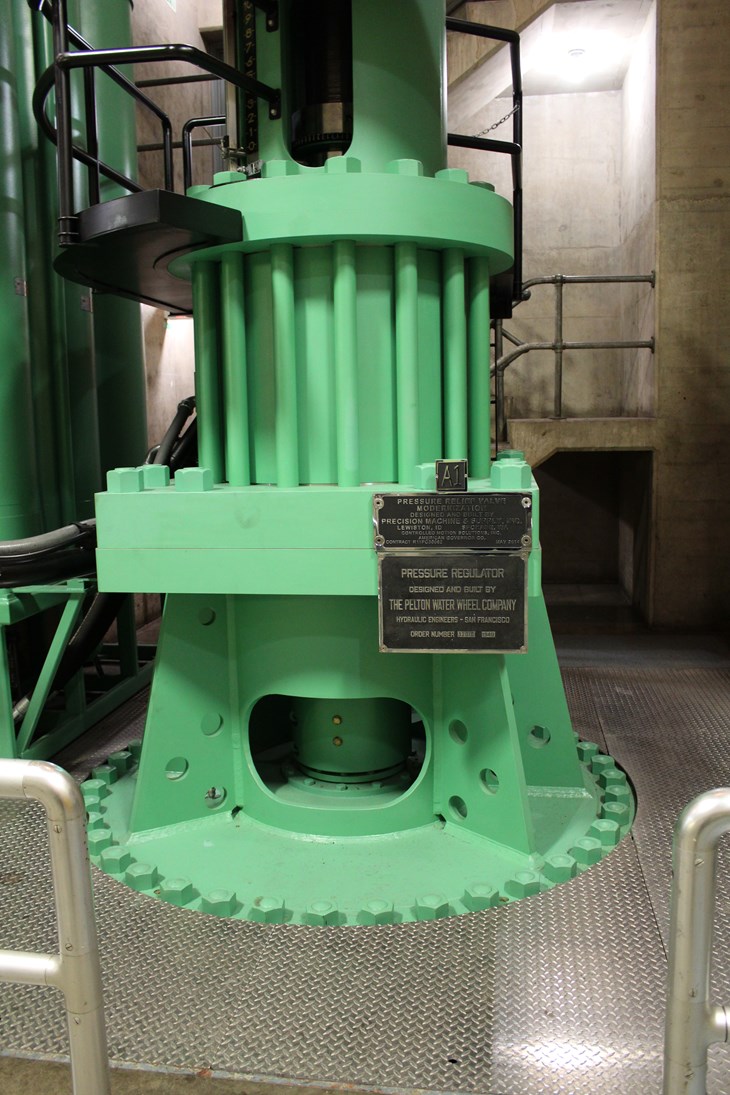
Self-sustaining facility
Day-to-day maintenance
For a structure more than 80 years old, repairs play a big role in the upkeep of the dam. As the plant needs constant maintenance, due to its age, technicians are constantly replacing turbines, transformers, valves, pipelines, hoses, etc. “We deal with quagga mussels, a mussel species indigenous to Africa. They grow exponentially and they are found in the piping systems, cooling systems, trash racks and almost any other place with exposed metal. They really love dams,” Hendrix expresses. “What we have been trying to do is work with a private industry to develop quagga mussel control agents that we could add in the water that will help with the problem. We also employ other measures like ultraviolet microfiltration, and physical cleaning of the piping and valves to get rid of accumulated quagga mussel shells.”
Due to the size and complexity of the plant, the improvement and maintenance process for leaks, welding, repairing and replacement of pipes and valves is constant. Since the commencement of his employment, Jorgenson has made many alterations to the plant. “I have changed the way we weld, the installation process for valves and even the type of valves we pick and choose. We now use more TIG and gas shielded flux core. We weld a lot of pipes and the main pipe we deal with is schedule 80.”
Jorgenson explains how many of the machines and parts in the structure have been in use for a long time. “The biggest cause of failure is just age. The machinery in the dam itself, has been in working since the ‘30s and many parts, including valves have been running for more than four decades,” he says.
A frequent problem the plant runs into is obsolescence of older parts. If a situation arises where an unavailable part is required, it is typically replaced with an updated item “What I am often doing is putting in a ‘back’ on a gate valve, which makes it a modern valve,” Jorgenson explains. “We are constantly trying to modernize and update everything in this plant.”
To facilitate the upkeep of the plant regular outages are scheduled– generally starting on October 1, until the last day of April. “As we upgrade the turbines and related infrastructure at Hoover Dam, we integrate the latest technological features and designs into our generators to reduce the degree of cavitation within the system and increase the life of our piping, turbine and other structural components,” says Jorgenson. “You have to understand that this plant is huge, and stuff does not just happen overnight,” he states. “We are constantly updating the plant and every time we do a major overhaul, we put in the latest technology. So these parts that you see are nothing like they were in the 1930s. As the federal government, we understand the need to be judicious with money, so when we upgrade the plant, we know we are looking for redundancy, the expectant life of a part and what will give the best value to us,” Hendrix explains. “We do not always look for the cheapest part, nor do we look for the most expensive part, but we definitely look at all the specs and the life cycle. We want products that will last multiple years through all kinds of different conditions.”
The process to have parts selected is a meticulous one. All the components have to pass through the electrical and mechanical supervisors and foremen. The dam preforms a number of quality checks, and will reject parts if they are not up to the standards or do not promise quality control and longevity. Hendrix comments, “The Region’s engineering division gets together with Hoover Dam’s apprenticeship group to review all the specs of a part as they are very stringent as far as quality is concerned. We would rather pay a little bit extra for quality and have a product last a long time, rather than replace it.”
Rather than exclusively using an approved manufacturers list, Jorgenson highlights that they generally use General Services Administration (GSA), which is a government entity. “If I need 25 12-inch Garbowsky class 300, then I will go to our shop and tell them what I want,” Jorgenson states. Hendrix adds, “What is a little unique here, is that we still do most of our own in-house maintenance, as it is a self-sustaining facility; the money we get from the power sales pays for the structure. We also maintain a physical technical staff here to do repairs.”
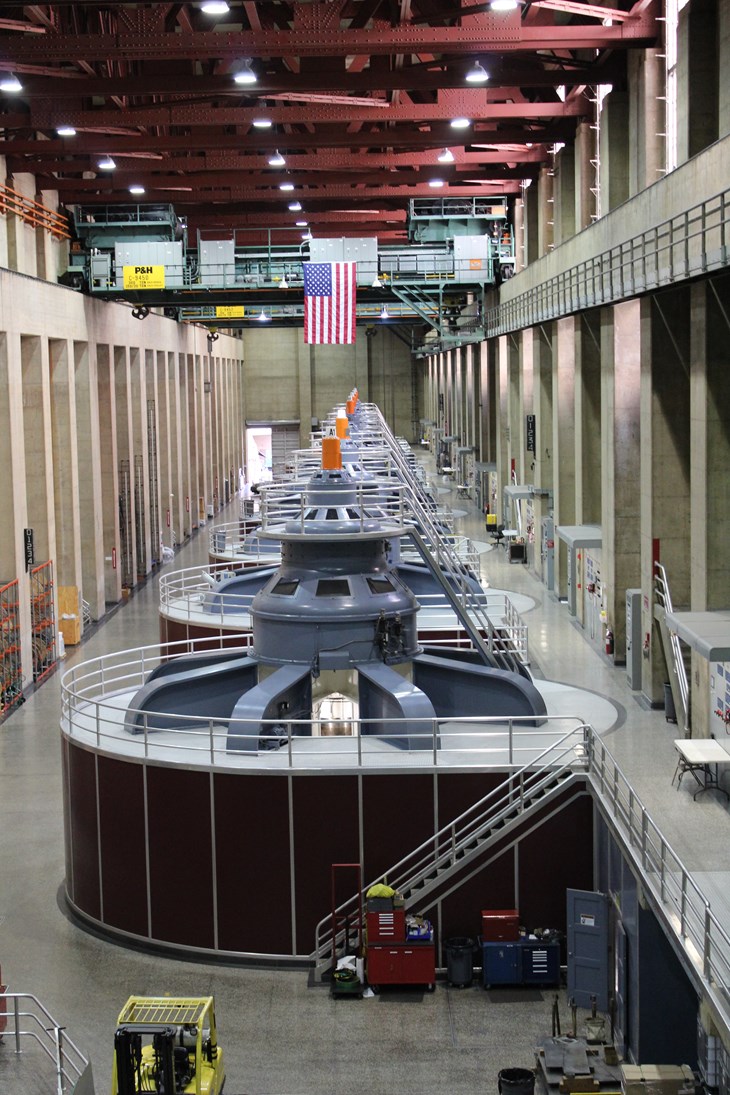
Valves at the Dam
Touring the plant, some of the older technology in the piping systems and a significant amount of valving is evident. Hendrix explained that the plant piping systems use primarily gate, globe, ball and butterfly valves with an average 12-foot diameter and mainly maintenance is on 24 inches down. One of the main applications of the valves in the plant is that they direct the water in one intended direction. “You do not want the water going back to where it is not supposed to,” says Jorgenson.
The water coming down the penstock goes to the butterfly valve, where they have what is called a ‘bypass’—this ensures that too much water does not collect on one side. This essential process is achieved through the installation of 12-inch guard valves, check valves, ‘bypass’ and piping. Jorgenson and his team took a month and half to replace all the working parts in the area, some of which had been running for 40 years.
Jorgenson explains that the pipe crew had recently finished installing twelve, 12-inch swing check valves. “There are many types of valves here, everything that you can imagine, right from old-fashioned gate valves to globe screen check valves.”
Valve and piping challenges
One of the greatest challenges that the maintenance team at Hoover Dam faces, in regard to valves, is galvanic corrosion. “Due to the variety of metals in each valve, the main issue we experience with our valves is galvanic corrosion in our carbon piping. If I have a 12-inch stainless butterfly valve with an electric actuator on it, I have to protect my pipe. Galvanic corrosion is one thing we are fighting constantly,” Jorgenson explains.
Another common issue Jorgenson faces, in regard to valves and piping, is longevity. “One time, the team installed schedule 40 piping with high-pressure capacity. The schedule 40 seamless grade met the pressure rating, but did not meet the longevity,” Jorgenson reveals. “They put that pipe in 35 years ago, and it should have been replaced 20 years ago. Now, any time we put in new piping, we go out and get the best available. We will get schedule 80, 106 grade seamless intended to last 40 to 45 years. We do everything we can to protect, not only the valves, but the piping as well. We coat and paint the piping on the inside; it has a dielectric insulation that protects the piping and valving.”
At the time of our visit contractors are working on re-coating the penstock. “The jet valves, which are a variation on a throttle, are another form of specialty valve. Another really neat valve that we have here is a 30-inch Chapman valve that they are repacking, and it is tied into the 42-inch penstock which is for the house turbines, which is A0N0 (Arizona 0, Nevada 0). The cool thing about this is that this valve has been there since the day it was made. Basically everything here is a valve. This is just on big pressure vessel and it is all tied in together,” Jorgenson explains.
Hoses and expansion joints
When dealing with hoses, Jorgenson explains his preference for a stainless steel braided hoses as they are durable and long-lasting, as well as easy to connect/disconnect. “Since I deal with water, it is very helpful if a joint can be easily disconnected so that I can look in the hose and free it from debris. With a hard pipe, I cannot really do that.” Jorgenson is currently trying to implement something similar with cooling water by not using high-pressure, but by using hoses that will take low pressure, below 150 psi; as long as the flex-lines are pressure-rated they can be used to help deal with the elevation changes in the plant.
Flex lines are seen throughout the dam. Jorgenson explains that in situations where they need to ‘flex’ hard pipes and/or water braided lines; they use a lot of expansion joints. Although PVC hoses are simple and effective, Jorgenson prefers to use other options as the PVC hoses are fragile and do not stand water hammering well. If the hose is to be used for an oil based application, threaded hoses are avoided. Though it is sometimes necessary, he tries to avoid using anything that is not welded.
Stainless steel braided water flex lines are widely used around the facility. “Our machine shops can actually make hoses up to 2 inches,” Jorgenson explains. “As we manufacture a lot of them now, we are able to go up to as much as four inches. We see the value in creating them, especially if we know that the line is never going to suffer from water hammer.”
In addition to using the stainless-steel braided hose, the technicians also use large stainless-steel piping. The structure has older carbon pipe embedded in the concrete which cannot be replaced. Jorgenson explains that he is very conscious when introducing a different metal to make sure that it has a dielectric isolation kit in it so that it does not affect the older parts in the area.
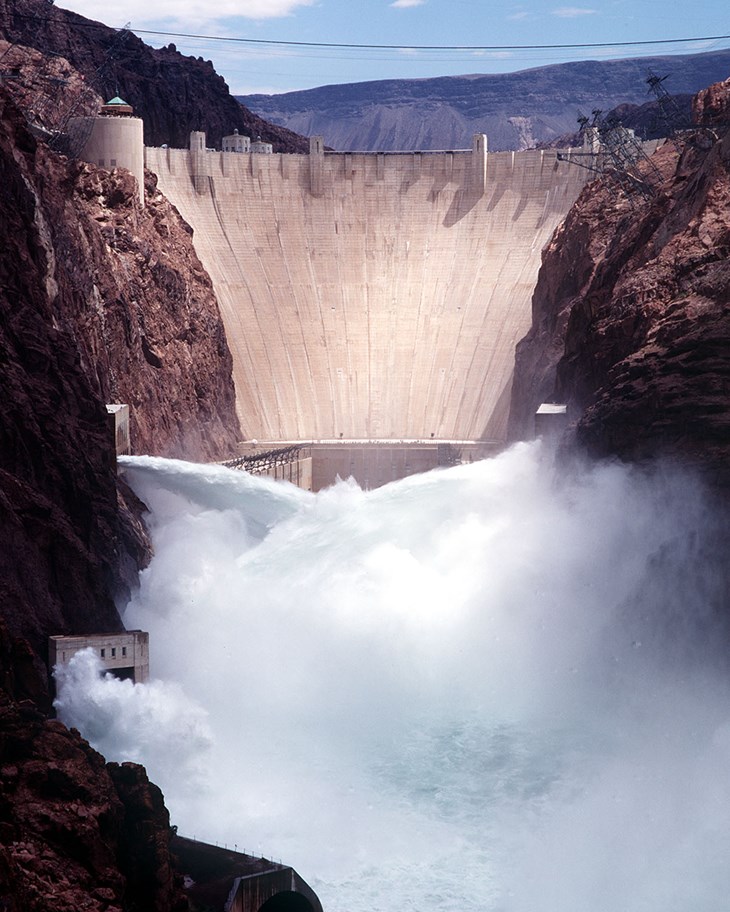
Dam powerful
The next phase of our tour took us 705 feet below ground in a beautiful ornate brass and marble elevator. The total depth of the facility is 726 feet with a width of 660 feet. The generator room, located far beneath the ground, was one of many additional areas we had the opportunity to see. The room houses nine generators – A1 through A9. At the time of our tour, generator ‘A2’ was the only one running. The upper penstock affects A1, A4, A6, A8 and A9, while the lower penstock affects A2, A3, A7, and A5. The primary function of all the generators is to generate electricity from the water as it flows downstream. The dam’s generators provide power for public and private utilities in Nevada, Arizona, and California. “The Bureau of Reclamation does not waste any of the water’s potential because they consider it a valuable resource,” Jorgenson explains. “They prefer all the water go to these generators.”
When the dam was initially built, its primary purpose was to help with water storage. As Los Angeles started growing, the L.A. Power Plant began utilizing the dam for power generation purposes. Hendrix indicated that the power is very coveted on the spot market, and especially in the western part of the country, because if there is an immediate and instant need for power there, they can provide it.
Today, power that is generated in the dam is turned over to the Department of Energy, the Western Area Power Administration. The administration markets and sells all of the power that the dam makes and provides the dam with a percentage of the sale. The money the dam receives from the Department of Energy is then used to help with the upkeep of the facility. Anytime repairs warrant a change of part, the maintenance facility makes sure that they are putting in the most modern and technologically advanced parts. As a result of its continued technology updates, the dam has been able to generate an immense amount of energy while increasing its efficiency.
Favorite part of the job—teaching and mentorship
Speaking of the how the dam is operated, Hendrix recognizes the caliber of talent possessed by the engineers and journeymen working in the facilities. “Through our apprenticeship program we hire people who are very highly trained in specialty welding, metals or related disciplines.” Less and less people now go into these types of trades,” Hendrix comments. “A lot of candidates come here from the Army Corps of Engineers, Public Works or military, things that are immediately transferable. We train people to be millwrights, welders, machinists, pipefitters which is invaluable experience for them.”
The dam offers several extensive four-year apprenticeship programs. From those, mechanical and electrical apprentices are the ones who work with Jorgenson’s team. “It is a pretty tough program because they have to spend a lot of time doing that, they pretty much have given up their lives for four years,” he says. The meticulous program teaches the apprentices a lot of different disciplines and provides hands-on experience with several applications and processes.
Without missing a beat, Jorgenson says ‘teaching’ is his favorite part of his job. He believes it is very important to train and mentor new engineers; when one of his new students is successful it is incredibly rewarding. Why? “Because as a foreman, I get to teach my guys new ways to weld and I enjoy the heck out of that.”