Welding is a joining method that often delivers joints cheaper, faster, and with better mechanical and chemical properties than riveting or bolting. Some applications allow for automation, using robots or mechanical devices to produce miles of welds a day. However, this is not always the case. Geometry and scale, for example, are two of the factors that may force a manufacturer to rely on manual welding. When that happens, some new risks ensue. In this article, we are going to explore a few welding concepts and have a glimpse into some of the common challenges associated with manual welding.
By Hugo Domingues, Tequaly, and Davi Correia, Technical Consultant
What is Welding?
The American Welding Society (AWS) defines welding as ‘A joining process producing coalescence of materials by heating them to the welding temperature, with or without the application of pressure or by the application of pressure alone, and with or without the use of filler metal’.1 For the ISO (International Organization for Standardization), welding is a ‘joining process in which two or more parts are united producing a continuity in the nature of the workpiece material(s) by means of heat or pressure or both, and with or without the use of filler material’.2 Both definitions are vague on purpose, for welding encompasses such a broad range of processes and techniques that finding a definition that fits every occasion is a challenge in itself. Luckily, readers of this magazine are mostly interested in stainless steels and their applications in industrial manufacturing (think pressure vessels). Focusing on these fi elds allow us to ignore the minutiae of the previous definitions and regard welding as connecting metallic pieces by melting parts of them and allowing the metal to fuse together under a protective environment, often with the addition of extra metal to fill in joint gaps.
This simpler definition is aligned with the industries we have previously mentioned and covers the most common arc welding processes used in them, such as Shielded Metal Arc Welding (SMAW), Gas Metal Arc Welding (GMAW), and Gas Tungsten Arc Welding (GTAW). Arc welding processes use an electric arc between an electrode and the working piece to create the necessary heat to fuse parts and filler metal. In the case of SMAW and GMAW, the electrode is consumable and provides the extra metal. In the case of GTAW (also known as TIG, Tungsten Inert Gas), the arc is created between a non-consumable tungsten electrode and any extra metal comes from a rod or a spool. Figure 1 presents a diagram of the GTAW process.
The Human Factor
When done manually, GTAW is one of the most challenging processes for a welder. Delivering welds that are both aesthetically pleasing and sound requires that the welder constantly maintains the following parameters:
– The height and inclination between nozzle and workpiece;
– The speed at which the torch is moving; and
– The speed at which metal is fed into the molten pool.
The welder has two techniques available to comply with the requirements above: freehand and “cup walking” (See Figure 2). In freehand, the nozzle (or cup) floats above the workpiece; and “cup walking” is when the cup is dragged over the weld bead of base metal. “Walking the cup” provides a more comfortable position for the welder, but it is not always possible to use this technique, either due to joint geometry or to avoid scratches in the finished weld. Regardless of the technique, welding with GTAW requires one arm holding a torch and one arm holding the filler metal rod. Both arms must work in harmony, keeping speed and angles, often for minutes at a time, repeatedly through the workday. Different industries have different requirements regarding the skills of a welder. While some might rely on some sort of in-house training, critical applications such structural steel, nuclear facilities, and gas pipelines, to name a few, require a thorough certification program. Certification programs are mandatory according to many design codes, such as ASME and AWS. They involve the welding of a number of test coupons and passing the required nondestructive and destructive examinations.
In theory, “certifications ensure that welders possess skills to perform up to the code they will be working under, as well as a document that the welder is qualified to practice his or her trade under that particular welding code.6” However, that is not always the case. Similar to a driver’s license test, a certification only attests that on a given day, with a particular equipment model, and a particular state of mind, a person successfully performed a set of tasks and was evaluated by a second person. The same way a driver’s license is no guarantee that a driver will never makes mistakes, a certification does not guarantee that a welder will always make sound welds. One of the common reasons for failure is that welding can be very demanding on the body. Welding tube and pipe with GTAW is awarded a triple “T” by many welders, slang for tiring, tedious, and troublesome. Gaps and poor fit-ups require constant attention and even when things are properly aligned, the many shifts in position require a skilled professional. Many welders can deliver a good weld on a test coupon; only a few are capable of delivering an acceptable weld at the end of a long day.
Imagine for example that fixed, horizontal pipes need to be welded. In welding parlance, this is known as the 5G position, when the pipes cannot be rotated to improve the welder’s comfort. In this case, the welder must move around the pipe in the vertical direction to perform the welding (See Figure 3). Again, many are capable of driving around the block without causing an accident; few drive every day, the whole day, through all the city without making mistakes. And yet, both have driver’s licenses.
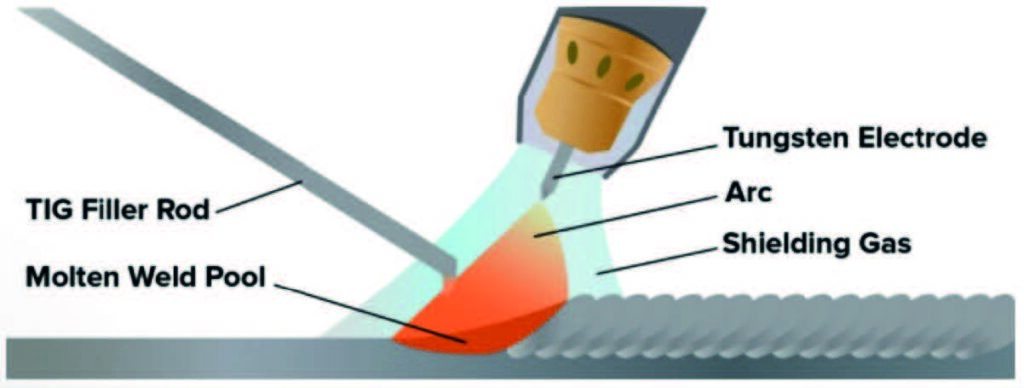
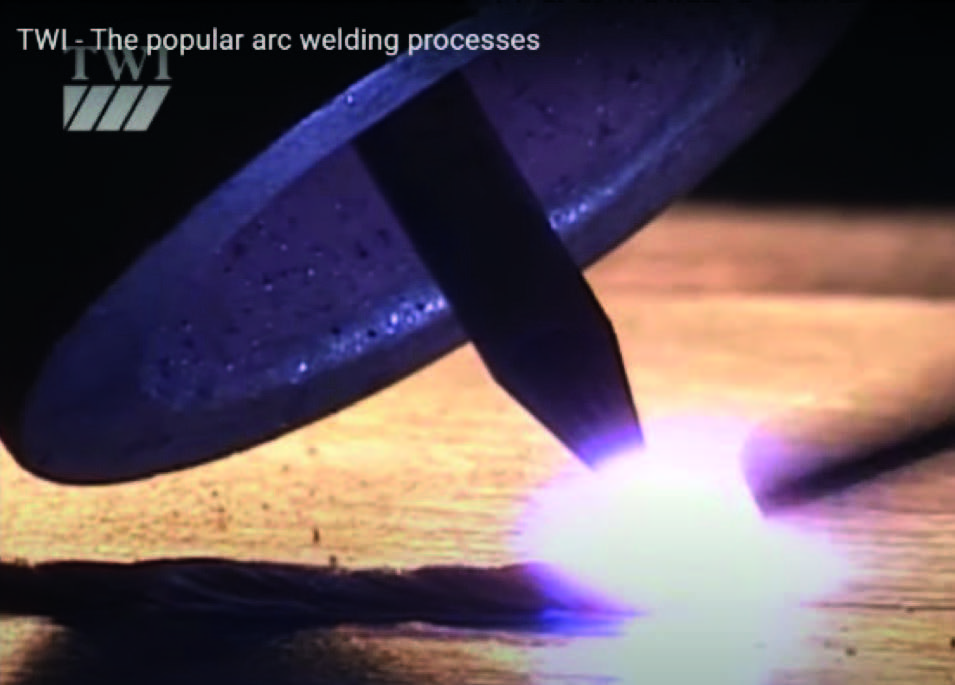
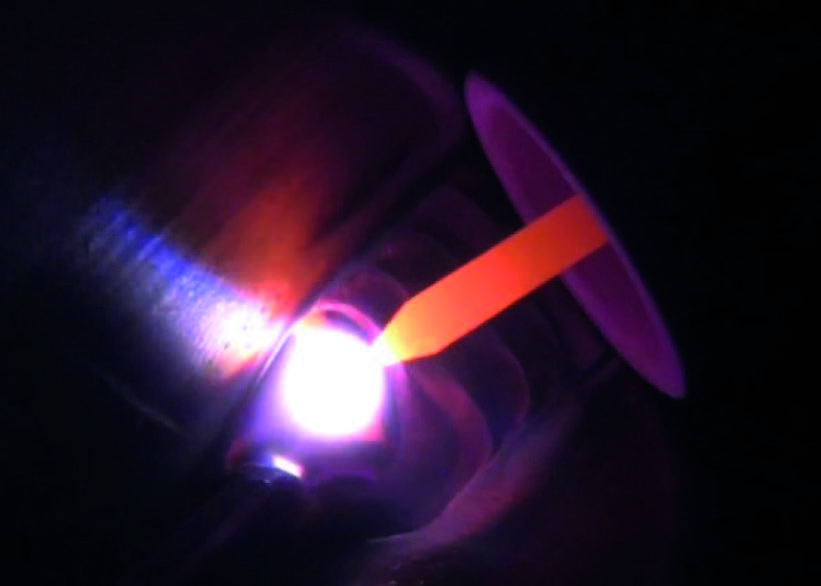
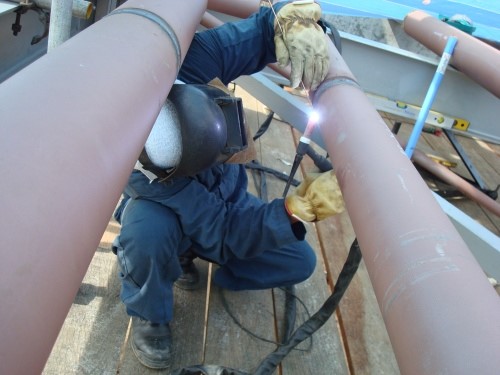
When Things Go Wrong
An automated equipment, adjusted according to a qualified welding procedure, should be able to deliver quality welds as long as parameters are kept within defined ranges. And yet, even automated welds are inspected, as unknown variations may cause defects – such as cracks, lack of penetration or porosities – and pose a danger to future operation.
What holds true for machines is even more important when dealing with welders, which can become bored, tired, complacent, or even, in extreme cases, downright angry. In all these cases, defects can be created and hidden under the looks of a well-made top layer.
Nondestructive examination techniques, such as liquid penetrant, magnetic particle or x-ray, are prescribed by codes and specification to assure weld quality. When a defect is found, repair may require a welding procedure distinct from the one used to deliver the original weld.
Once identified, repair should not proceed without prior identification of the root cause of the defect. For example, a crack may be due to poor joint design and excessive residual stresses. Or it may have been caused by improper control of heat input. The former requires an engineer to rework the design; the latter requires a very tough talk with the welder.
Identifying Problems and Repairs
An example of identifying a problem was location a crack, and then creating a plan. The service was performed as follows – we made a transverse notch in the direction of the crack (to avoid its expansion). We started the removal positioning the cut from the south end (toward the center of the crack) and north end (toward the center of the crack avoiding its enlargement).
At the end, to remove the crack, welders used the penetrating liquid test to analyze if there were traces of a leak, and found that the crack had been successfully removed. In the case of a weld in stainless steel, welders started to weld by injecting nitrogen into the inner part of the tube to obtain a uniform root without discontinuity, because stainless steel requires this internal protection.
References
1. AWS A3.0M/A3.0:2010, Standard Welding Terms and Defi nitions, 12th Edition
2. ISO/TR 25901-1:2016, Welding and allied processes — Vocabulary — Part 1: General terms
3. https://www.weldingsuppliesfromioc.com/blog/stick-vs-mig-vs-tig-which-process-is-right-for-you/
4. https://www.youtube.com/watch?v=aq-rIpiY-y0
5. https://www.weldingtipsandtricks.com/walk-the-cup.html
6. https://questtech.ca/blog/asme-welding-certifi cation-explained/
7. https://heatsschoolofweldingtechnology.wordpress.com/2008/12/16/5g-welding-position/.
About the Authors
Hugo Domingues is a welder for the Brazilian company Tequaly. He has held this role for over 6 years, and has 18 years of experience as a welder.
Davi Correia is a Senior Mechanical Engineer who has worked at a major Brazil-based oil company for the last 15 years. Correia is part of a multi-disciplinary team that provides technical support for topside piping and equipment of production platforms.