Work is picking up in Arizona. The TSCM Taiwan Semi-Conductor Manufacturing Company job is expected to last for several years. This is a large job that will employ up to 500 Union Ironworkers. Another job that has started is the Lucid Motors factory in the nearby city of Casa Grande will employ 200 ironworkers, and a new Intel factory is slated to begin construction in early 2022, employing up to 300 ironworkers. The Ironworkers International Union is the entity that supplies trained ironworkers to the steel erection industry in the United States and Canada.
By George Facista, Apprenticeship Supervisor, Ironworkers Local 75, Phoenix, AZ
Ironworkers and Welding
Union ironworkers erect structural steel, place rebar and post tensioning, install products such as curtain walls, stairs and guard rail systems. They rig and move heavy objects and when required, and they weld all of those things together. Many of these new jobs will be welding jobs.
The Ironworkers union has partnered with The American Welding Society to supply welders to the ironworking industry. The Iron Workers/AWS National Welding Certification Program is a highly respected and nationally recognized program. This partnership with the American Welding Society provides an unparalleled standard of excellence for welder training, qualification and certification. There are currently 104 iron-worker training facilities in the United States that are in this partnership. Local 75 in Phoenix is one of these facilities.
Certification and Specification
On a typical day members of Ironworkers Local 75 will come in to the University of Iron Apprenticeship Training center to attend apprenticeship training classes, update their welding certifications, to practice for an upcoming test, or to hone their welding skills. Members with current welding certifications have to update their credentials every six month, They can have their papers updated at the facility by welding in the process in which they are certified in the presence of one of the training center’s three certified welding inspectors (CWI). The Ironworkers International Union has developed over 100 Welding Procedure Specifications (WPS). A WPS is a document that serves as a guide for the effective creation of a weld that meets all applicable code requirements and production standards. The training center offers several different welding certifications, Welding Performance Qualification Records, or, WPQRs . The most common certifications that are issued are the D1.3, galvanized sheet metal to A-36 ½” steel plate puddle weld certifications, the D1.1/D1.5 Shielded Metal Arc Welding (SMAW) certification, and the D1.1/D1.5 Flux Core Arc Welding (FCAW) certification.
Testing and Inspection
The D1.3 certification test (Figure 1) is an SMAW certification determined by a destructive torsion test. The weld must penetrate the sheet metal and the weld nugget will remain on the base metal. The SMAW test and the FCAW tests are welds completed in the 3G (vertical groove) and 4G (overhead groove position) on 1” thick and 6” long coupons (Figure 2) utilizing a 3/8” x 1” backup bar. The D1.1 code is the AWS code for Structural Welding. The D1.5 code is the AWS Bridge Welding Code.
When the welder tests for the SMAW and FCAW the CWI will conduct the test by observing the welding at several stop points. He or she will have the welder assemble the coupon correctly setting the proper gap between plates against the backup strip that will accommodate the root pass. The welder will stamp pre-determined test numbers on the coupon that will remain on the sample that will be cut out and bent on the bending jig to test the weld. The CWI will observe the initial position of the welding coupons in the welding booth, and will then check the root pass in the welding groove. The welder will then be able to complete the weld but cannot change position of or remove the coupons until the fi nal cover pass has been inspected. The CWI will check on the welder during the test to assure that the test rules are being adhered to and to also confirm that the welding machines are set within the parameters stated in the WPS.
When the final cover pass has been inspected the coupons will be removed from the booth and brought into the CWI testing room. The CWI will inspect the cover pass for proper reinforcement, that is, the amount of weld above the cover pass in relation to the coupon. He or she will look for other things like proper fill, undercut, overlap of weld, porosity, and arc strike on the face of the weld or other discontinuities.
Using a band saw the CWI will cut two samples from each weld coupon. The 3/8” samples will be cut from predetermined locations in the weld coupon that have been pre stamped with the test number that was issued to them. The CWI will twist off the backup bar section and will inspect the root for proper fusion to the backup bar. Next the CWI visually inspects the samples for any discontinuities such as slag in the crosscut section.
A discontinuity of 1/8” is the maximum allowable discontinuity. It could be some slag, a lack of fusion, an air pocket, a crack, or any combination of these that will open beyond 1/8” when the sample is bent in the jig. If a 1/8” flaw is detected before a bend is made, the weld will be failed. If nothing is apparent or a smaller flaw is detected the sample will be side bent with any observable flaws bent to the outside of the bend. (Figure 3)
The local 75 facility conducts other welding tests other than the three described above. Tests given other than those described are usually dictated upon the need by local contractors. Occasionally a job requires that welds meet the D1.8 Seismic Supplement. This test is conducted on a 12” long by 1” thick coupon with a restrictor plate that represents a lower flange beam to column connection web that is placed in the center of the weld. (Figure 4) It is done utilizing various types of flux core wires. This particular test is usually needed in seismic active areas such as the West coast of the United Stated. There are four side bend samples that are cut from this coupon.

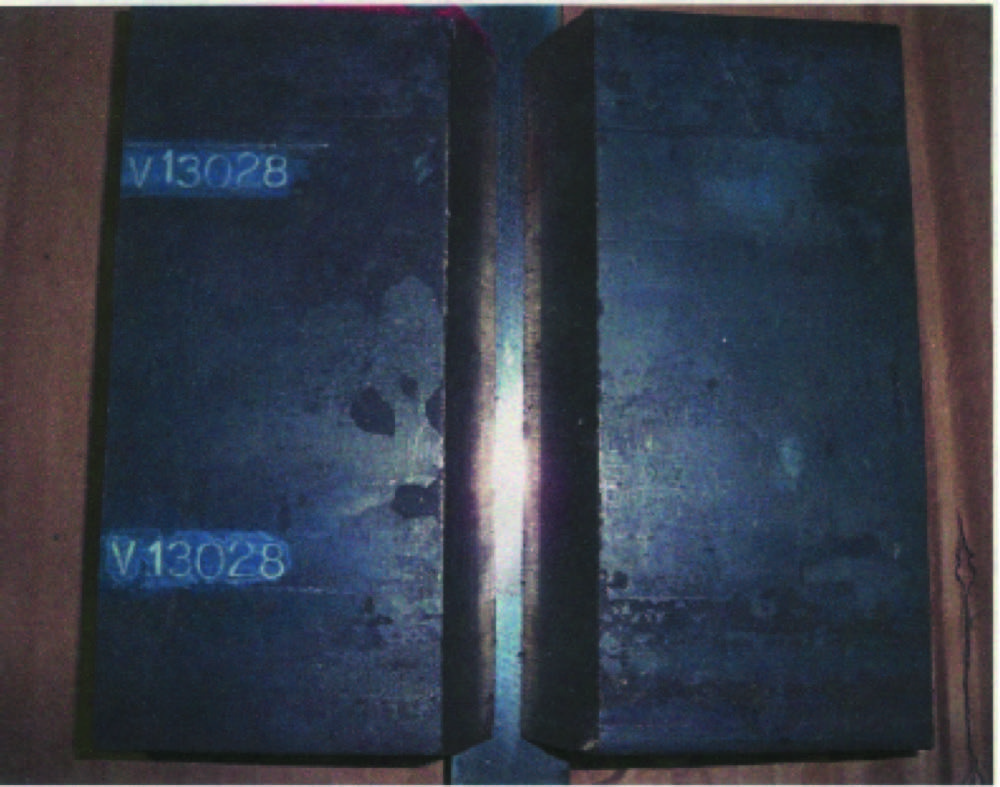

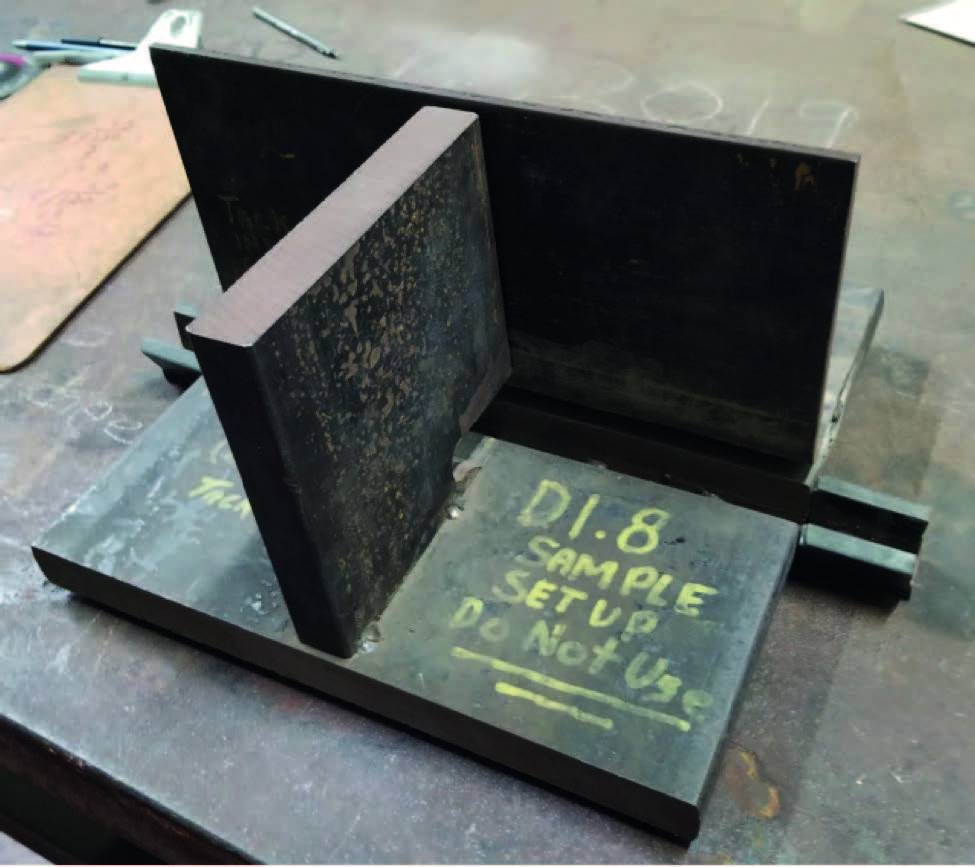
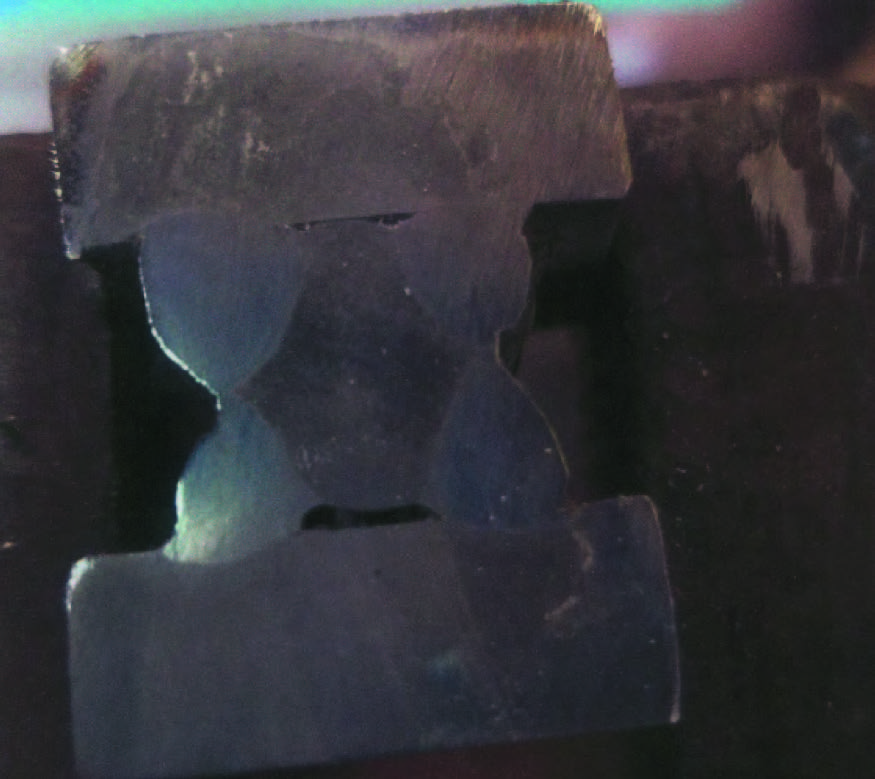
Stainless Steel Certification
Sometimes a stainless steel certification is needed for jobs in the mining industry for such things as linings for kilns or hoppers. Most of these tests use 3/8” or ½” coupons welding A240 Type 304 coupons to each other, or to A36 carbon steel utilizing FCAW-G process that is flux core with a shielding gas, such as CO2 or a CO2 Argon mixture. Other stainless steel tests require Gas Tungsten Arc Welding (GTAW) Tungsten Inert Gas (TIG) welding or with SMAW using AWS E308L-16 filler material electrode. We also have some aluminum certifications that utilize the GTAW and Gas Metal Arc Welding (GMAW) process.
Union ironworkers handle and install reinforcing steel known as rebar. From time to time we are required to weld rebar. The testing requires that ASTM A-706 grade 60 rebar is used. It is welded in the SMAW process with AWS E8018 filler metal electrode. Rebar falls under the AWS Reinforcing Steel Welding Code D1.4. Some of these test require that the weld be cut transversely and macroetch testing be applied to the sample. (Figure 5)
As you travel to the great cities of the U.S. and Canada, like New York, Chicago, San Francisco, and Toronto, you can look to the skyline or visit the buildings, bridges, and infrastructure you can be assured that the foundations, superstructures and features were erected and welded together by Union Ironworkers.