Stainless Steel World Americas had the opportunity to sit down with Deckard to talk about how he emerged into the EPC market and what kind of experiences he has gained since beginning his career in the sector.
By Brittani Schroeder and Sarah Bradley
An interesting beginning Justin Deckard did not originally plan to be an expert in the piping realm. He went to Texas A&M University and obtained a degree in Ocean Engineering, with a specialization in Coastal Engineering, which included such things as beach water restorations and marina harbors. “Coming out with a degree like that, I had two choices: work for the army or work for the government in some other capacity. I did not want to do that,” Deckard relays. “I even had a job offer to work in Korea, but I wanted to stay closer to home.” Deckard secured an interview at his first engineering company shortly after graduating, through a connection of a college roommate. “He told me that I would not understand what they were doing, because they do not teach it in school, but he would look over my resume. The interview was very casual, but I thought I bombed it. Surprisingly, I had an email offer waiting for me the next morning,” says Deckard.
Deckard spent five years at Mustang Engineering, moved to Jacobs Engineering for four years, returned to Mustang Engineering (rebranded to Wood), and eventually found his place at Arion, where he is now the Piping Department Manager. Through all the companies he has worked for, Deckard has gained a lot of experience from different projects. “I had the opportunity to work on refineries with really big, really hot pipes – everything from 72 inch cooling water lines to 1,200° heater lines. I have worked on many topside projects for a vast range of clients, so I have been exposed to a lot of different realms.”
A day on the job
When Justin Deckard started his career at Arion, he had the opportunity to build his department from the ground up. In his opinion, it was a great situation to be in, rather than taking over a department from a past manager. While there were still a lot of challenges to overcome, there was also a lot of excitement.
Deckard manages piping engineering and design at Arion, and he and his team handle everything from 3D modeling routing, drafting isometrics, piping classifications, to pipe and valve procurement, through to final delivery.
Deckard does not have a typical working day. “Every night before I head home, I make a plan for the next day of all the things I want to do. By 8 a.m. I have to re-evaluate the plan, and then it is re-evaluated again after lunchtime. By the end of the day, I have maybe accomplished a few things that were on my original list,” Deckard admits. “Our team is bringing a lot of experience from past jobs to the company, and we are learning how to make processes better moving forward.” Deckard works with a team of 21 designers and three engineers, with a focus on the offshore and midstream sectors. “We are going to branch out into different areas soon, and I think we are able to do that because we have a strong, diverse, roll-up-the-sleeves-and-get-dirty team.”
Deckard thoroughly enjoys working with his team. “I like that I get to work with such a diverse group, and we are able to make clients successful. We are problem solvers, and when each person has a different background in the industry, we can cover a lot of ground,” he says.
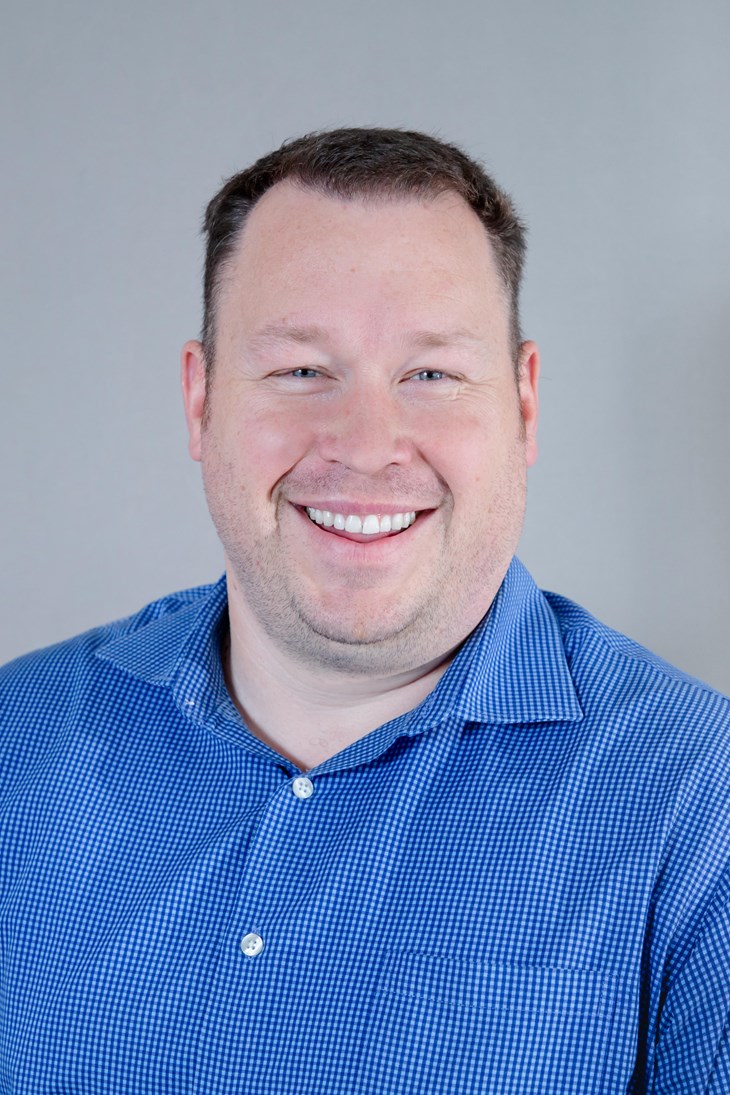
Specialty materials
In Deckard’s line of work, he sees many different materials being used for varying applications. When there is the requirement to work in different environments, it is crucial to consider what the best material is for the application, based on where it will be located. Deckard must ask questions such as, “Are we dealing with corrosion? If so, do we need to have more intricate corrosion-resistant alloys (CRA) present, whether that is nickel or stainless?”
Deckard enjoys being able to work with CRAs because of the complexities that come along with them. “CRAs come with a lot of nuances and intricacies, especially in the piping realm. We will have to work with materials such as clad Inconel alloy 625 or solid Incoloy 825,” Deckard states. It is crucial to consider what the most cost-efficient option is to produce these applications, versus how long the material will last, while also considering any delivery issues that may arise. Due to the difficulty in procuring the more ‘specialty’ alloys, delivery times can be extensive. Mills can take anywhere from 32 to 48 weeks to manufacture and deliver materials, depending on the size and quantity of the order.
In terms of commonly used materials, Deckard has seen the application of Inconel in crude projects because of its ability to withstand the fluid’s corrosiveness and the higher temperatures of the heaters. However, Inconel is not the only CRA used for the construction of heaters. “Normally you would see Alloy 800 HT, which is the heat-tempered version of Alloy 800 H, used to avoid cracking and creep issues. But in one particular case, the client wanted Alloy 800 H,” he explains. “The material came from a licensed provider, and we took the 800 H material through the heater to a place where we could then transition to chrome.” To achieve success, Deckard and the client had plenty of discussions on how to properly complete this transition, and ended up welding a 9 chrome flange to an 800 H pipe. While this was an uncommon situation, Deckard and the client experienced positive results.
When asked if Deckard chooses the materials for each application and project himself, he explains that it is typically the client who will choose. “They will bring us a list of what they will need, and we will work with their approved manufacturers list (AML) to procure the materials. If we somehow get ourselves into a pinch, we are able to deviate from the AML, to either get products quicker or for a lower cost,” he relays.