Stainless Steel World Americas had the unique opportunity to speak to Reza Javaherdashti, an International Referee on Corrosion Disputes, and a Corrosion Trainer, about the phenomena known as MIC. In part one of this two-part article, Javaherdashti speaks about microbial corrosion, biofilms, and what can make a material or environment more susceptible to MIC.
By Brittani Schroeder
Reza Javaherdashti started working in the industrial sector over 30 years ago. When he graduated from university, Javaherdashti realized that one of the most prominent problems in several end-use industries is the impact of depreciation, and how it limits the functionality of equipment. The common term for this would be ‘aging’. “As equipment is put into service, it becomes increasingly vulnerable, until one day it will have to be taken out of service,” says Javaherdashti. “Certain bacteria present on equipment can accelerate the process of aging, and this is what we refer to as microbial corrosion.”
Javaherdashti has a double degree in Metallurgical Engineering and Material Science. He completed both his PhD and post-doctoral studies on microbial corrosion (MIC), specifically on MIC in stainless steels. He continues, “I have performed electrochemical, mechanical, and biological tests on various metals, and I was part of the pioneering team of investigators who studied the effect of bacteria on stress corrosion cracking (SCC) in stainless steels.” Since then, Javaherdashti has dedicated his professional life to studying two things: corrosion management and its principles, and MIC and its management.
Javaherdashti is certified to run training courses on MIC by both the American Society of Mechanical Engineers (ASME) and the Society of Petroleum Engineers (SPE). “I have been involved in more than 300 troubleshooting projects and have authored/co-authored seven reference books on MIC,” he says. “I also have more than 5,000 hours of training experience in various end-use industries around the globe, from power and energy, to the chemical, oil and gas, and aviation industries.”
Javaherdashti was drawn to corrosion training because he felt there were knowledge gaps that needed to be filled in. “There have been a lot of misunderstandings about MIC, both in the proper recognition of MIC and how to define it and treat it,” relays Javaherdashti. “I wanted to reach out to several industries to share my knowledge about corrosion, so that people are able to determine if their equipment is experiencing corrosion, or MIC, and prescribe the correct treatment.”
What is microbial corrosion?
In order to explain MIC, it first needs to be defined as a type of electrochemical corrosion, and not a type of corrosion, since these two are very different from each other. “When we say that MIC is electrochemical corrosion, we imply that the factors that encourage its occurrence are the same as those that would encourage a non-MIC electrochemical corrosion to happen. There are at least three factors that need to be present: the anode—the metal that is highly likely to give off electrons, the cathode—the metal that receives the electrons, and electrolyte—the media through which ions will be able to move around,” explains Javaherdashti. If certain microorganisms—or macro organisms—are capable of establishing anodes, cathodes, and electrolytes, then the problem being experienced is MIC. The micro or macro organisms could be bacteria, archaea, algae, or fungi. He continues, “Some professionals define MIC in terms of bacteria only, but it is important to define it in terms of other types of organisms as well.”
From a morphological point of view, MIC demonstrates itself mostly as pitting; in stainless steels specifically, MIC can appear as patterns resembling ‘tiger stripes’. An important note, however, is that pitting can be caused by non-MIC corrosion as well. “In the 1980s, there was a firm belief that some pitting morphologies were unique to MIC. This is not the case, and luckily nowadays we are more conservative in our beliefs. We must first find the ways by which we can prove the case is MIC, and only then use the pitting as supportive evidence,” says Javaherdashti.
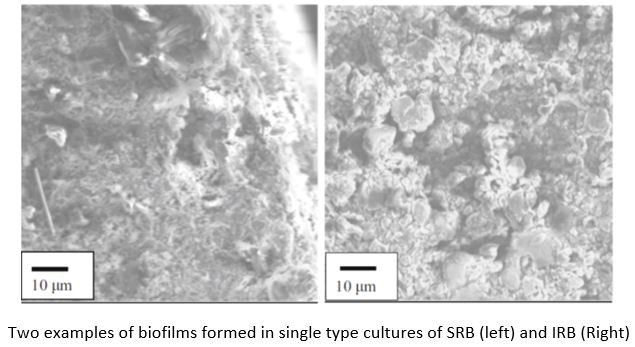
Prone to MIC
There are a few parameters that if present in a system – in addition to the necessary condition of liquid water acting both as an electrolyte and a media – bacteria can survive, and will make the system more receptive of MIC. The first parameter is temperature, and there are three general categories of temperatures that bacteria can adopt themselves to. Thermophilic bacteria prefer temperatures above 60°C; mesophilic bacteria prefer ‘room-temperature’, between 20°C to 40°C; and psychrophiles are capable of being active at very low temperatures. “If the system is working at what we call ‘ambient temperatures’, it is highly probable that there will be a high risk of MIC,” explains Javaherdashti.
The second parameter is pH levels. Bacteria can survive within certain ranges of pH. Typically, very high pH values do not kill bacteria, which is a major misconception. The thought that increasing the pH will kill bacteria is false, as it will only numb the bacteria – which means they will be inactive, but this does not mean that the bacteria is dead. For example, sulfur oxidizing bacteria can live in a pH value of 1, and sulfate reducing bacteria can live within a pH value of 5 to 9.5.
The third factor would be the availability of nutrients for the bacteria to feed on. The fourth parameter is the hydrodynamics of the fluid. “If the water can be referred to as stagnant, then the likelihood of MIC occurring will be quite high,” Javaherdashti says.
Biofilms
Bacteria can be found in two states in any fluid. They can either be freely flowing, which is referred to as ‘planktonic’, or they can be motionless and, literally speaking, stuck on the surfaces, being referred to as ‘sessile’. When bacteria can find their required nutrients in the bulk solution, they can sense if there is food available and if there are also other bacteria around. When the nutrients start disappearing from the bulk solution, the bacteria realize they must search for the nutrients somewhere else. This will encourage bacteria to ‘land on’ surfaces and start to establish bacteria communities. As these communities mature, they are referred to ‘biofilm’, and this process is called ‘biofilm formation’. The planktonic bacteria settle on surfaces and develop chemical structures that are referred to as extra polymer substance (EPS). “For a regular observer, this EPS would look like slime,” Javaherdashti explains. “As the bacteria develop the EPS structures, the biofilm grows and starts acting as a living net to help the bacteria get enough nutrients, and protects the bacteria from threatening factors that could exist outside the biofilm, such as metallic ions that have a toxic effect on bacteria, or ‘anti-bacterial’ chemicals called biocide.”
During corrosion, metals lose their electrons and subsequently bear positively-charged ions. These positively-charged ions attract negatively-charged bacteria, and due to these electrostatic forces, the bacteria would also be attracted to the metals. This, again, forces the bacteria to reach out for nutrient sources, and contributes to the biofilm.
“I would say biofilm is not the correct term to use,” says Javaherdashti. “I would instead call it terminus, which is a Greek word that addresses an area that is cut off from the outside. The biofilm is neither purely biological, nor a film. Biofilms appear more as a patchy and non-uniform structure than a typical film.” Figure 1 shows examples of how biofilms can grow on steel. The left side of Figure 1 depicts a biofilm formed by sulfate-reducing bacteria (SRB), and the right depicts a biofilm formed by iron-reducing bacteria (IRB). “The left side of Figure 1 we can see the very patchy, non-uniform nature of the biofilm, along with all types of elements that can be found in these structures.”
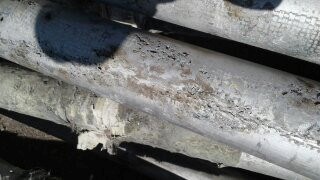
The consequences
As Javaherdashti says, “The importance of anything can be defined as a function of two parameters: cost and consequences. The cost of corrosion is normally between 1% to 6% of the gross domestic product (GDP) of any given country. Typically, it will hang around 5%. When we talk about MIC cost, it can jump up to 40% – if not more, depending how well aware the operators are about MIC and how to control it. That could add up to billions of dollars in any given country.”
The consequences can be divided into two categories: waste of time/energy, and environmental impacts. “If a piece of equipment fails due to MIC, you may have to repair it or completely replace it, which takes time and money,” explains Javaherdashti. “In 2006, a large oil pipeline in Alaska leaked more than 200,000 barrels of oil, and it was due to microbial agents (bacteria). Many hydrostatic-tested pipelines can also fail due to microbial corrosion.” Due to lack of training on MIC, engineers in many industries fail to recognize MIC, which can lead to disastrous outcomes. This is why Reza Javaherdashti has dedicated his career to training others as well.
Proper environments
MIC can become a problem in almost all industries where water is being used in its liquid form, and the temperature and pH levels are appropriate for bacteria to grow. If the linear velocity of the water is below 1.5 meters per second and is in contact with rough surfaces – which could include surfaces made rough from welding – MIC is highly likely to develop. Therefore, one would not need to look for MIC in dry environments. “I will not consider MIC in places where water is not in its liquid form, or superheated conditions where there may only be superheated vapor. Instead, I would consider it in environments near the sea, or a river, because this can support MIC,” says Javaherdashti. “I would also look at the air quality in the area, because bacteria can be transferred via air and can settle themselves onto steel structures and are likely to induce corrosion, with the aid of moisture in the atmosphere as an electrolyte.”
According to Javaherdashti, the main industries affected by MIC are pipelines in oil and gas – upstream and downstream, onshore and offshore – assets in contact with water in all types of thermal power plants, desalination units, water and wastewater treatment facilities, ports and marine structures. “In many industries, people misdiagnose MIC and non-MIC corrosion. When we talk about MIC, we need to remember that it is a form of corrosion that is supported by the action of living, intelligent agents (bacteria and others) that have been around for longer than humans. Therefore, treatment needs to be handled carefully.”
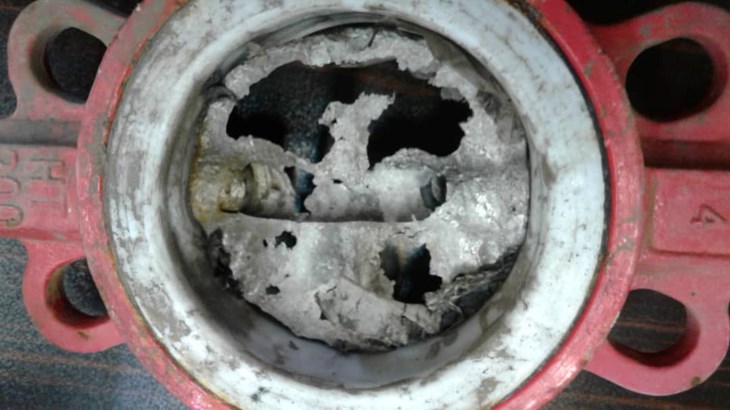
Metal grades and equipment
Many types of metals can be attacked by microbial corrosion. Austenitic 304 stainless steel is regarded as the least resistible stainless steel to MIC, most likely due to its low molybdenum content. “This does not mean that other stainless steels are not susceptible to MIC,” says Javaherdashti. In his own studies, Javaherdashti has discovered that IRB can affect the performance of 2205 duplex stainless steel, and bacteria can also affect 316L stainless steel. “When speaking in general terms, I would say that all engineering materials, whether it is ferrous or non-ferrous, metallic or non-metallic, are highly susceptible to MIC.”
In Figures 2 and 3, MIC can be seen on two assets made of 316L stainless steel. Both have been affected by the corrosive effect of sulfur oxidizing bacteria. In both cases, the material has been corroded quite badly. Both come from Javaherdashti’s own cases.
When discussing what types of equipment are at risk of MIC, Javaherdashti says it could be anything from heat exchangers, to pumps, valves, flow lines and the like. “Almost anything that is exposed to liquid water, and has an appropriate temperature and pH level, and is relatively stagnant, can experience MIC. This also applies to tanks, pipelines, water systems, and ballast tanks.”
There are two common approaches to corrosion. First, is the systems-based approach, and the other is a materials-based approach. The systems-based approach concentrates on the equipment. “For example, an engineer may want to know if in a certain equipment, such as a heat exchanger, pump, valve, or pipeline, MIC could present itself. As noted, it is the systems that are of concern here. In contrast, the materials-based approach discusses the materials that are at higher risk of MIC,” Javaherdashti states. “If I, as a corrosion expert, know under what conditions a specific stainless steel grade can corrode, then it does not matter what industry or what equipment this particular material is being used in.” The industry and equipment would only dictate the working conditions imposed on the material. Therefore, as long as corrosion experts understand the conditions likely to lead to facilitating the corrosion of a particular material, the industry and equipment in which the material is being used, come second in importance.