With over one hundred years of combined experience, Siderval and its sister mills in Germany and France are able to offer customers high-quality custom steel extruded products. Stainless Steel World Americas had the chance to speak with Laura Zak, Director of Sales and Customer Support for Siderval USA Sales, about the hot steel extrusion process, the importance of research and development, and their goals for the future.
By Brittani Schroeder
Siderval S.p.A. opened its doors in Talamona, Italy in 1972 and has since established itself as a market leader in the steel extrusion process. In October 2003, the company expanded into the Americas, opening Siderval USA Sales, with Laura Zak as their representative in North America. “I had 11 years of steel extrusion experience before meeting Siderval, so it was a perfect fit,” says Zak.
Siderval has concentrated on steel extrusions from the beginning and has acquired a vast knowledge of extrusion production technology over its 30 years of industrial experience. The company is well known and admired for their high-quality standards, and wide service range.
Siderval S.p.A., member of the Calvi Network Hot Extruded Business Unit, consists of Siderval S.p.A. (Italy), Hoesch Schwerter Extruded Profiles, also known as HSEP (Germany), and Cefival (France). All companies produce steel extrusions for over 600 customers worldwide, making approximately 55% of their business produced for export. All three companies share a combined experience of over 100 years in the steel extrusion business and have produced more than 30,000 steel shapes for their customers in stainless steels, carbon steels, alloy steels and titanium grades. Each facility has, on average, 100-150 employees working on the extrusion processes.
Siderval S.p.A./HSEP/Cefival have seen their products used in almost every industrial sector. “Any industry or business that needs a steel shape, if it fits in our range, we can produce it. Our primary industries include energy, medical, railways, bridges, infrastructure, lift systems, heating systems, maritime, aerospace, and food, among many others,” Zak relays. Each company concentrates on different industries, because each has a different size range of shapes it can extrude. She continues, “Our German mill, HSEP, is able to extrude the largest shapes because they have the largest extrusion process; Siderval, located in Italy, is right in the middle and can extrude shapes for almost every industry; the French mill, Cefival, concentrates on the aerospace and nuclear industries because of their smaller size range and knowledge of unique grade and high temperature alloys. They also have the newest extrusion press within the unit.”
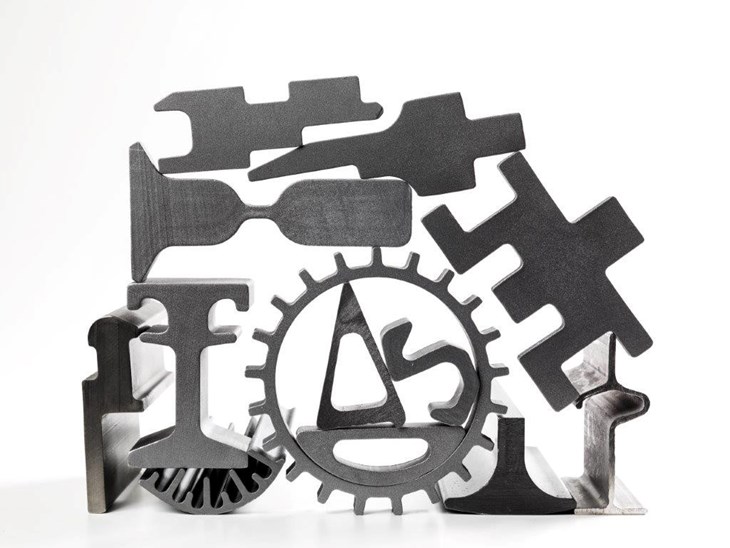
Hot steel extrusion
The extrusion process allows customers to design complex shapes for their unique applications, but without a high cost or excess material waste. “In the extrusion process, we take a round bar of steel and cut it to a specific length. We radius the front end, heat it, and roll it across power glass. It then gets pushed through a die,” Zak says. “The extrusion process is an optimal solution that typically provides financial, environmental and technical benefits to our customers.”
“Waste and cost reductions can be significant when compared with other manufacturing process. Say you have a square of steel and you need to machine the letter T out of that metal. There will be significant scrap from making that T. With an extrusion, we simply push the steel through a die, and you get the shape without the waste,” Zak explains. “This process is especially useful for the aerospace industry. When materials can cost in excess of $52 a pound, it is definitely beneficial to start with a near net shape.” The hot extrusion process can be used to make complex profile shapes, even with metals that are difficult to form.
Another advantage to the extrusion process is the low quantities required. “If we are producing profiles in stainless steel, our minimum requirement is 1,100 pounds, and 4,400 pounds for carbon and alloy steels, compared to the hot rolling of other companies, where mill minimums can be 100,000 pounds with high tooling costs,” says Zak. “The dies for extrusion are inexpensive and can easily be changed. If you have a design, you pay a one-time tooling charge, and you can use that design indefinitely without ever paying tooling charges again. Costs are only associated with new designs.”
Siderval’s sister companies, Cefival and HSEP, also have unique capabilities. “Cefival can produce various aerospace grades, extrude a shape, and then take that shape and roll it into a ring. The ring is welded – using a process called flash-butt welding – and machined into jet engine rings,” explains Zak. “HSEP has also been working with bimetallic tubing. This tube has one grade of steel on the outside, and another grade of steel on the inside—for example, carbon on the outside and stainless or alloy on the inside. As the tube is being extruded, the ID of the steel is maintained to meet the customer’s unique needs. We can also offer extruded profiles welded together for specific applications.”
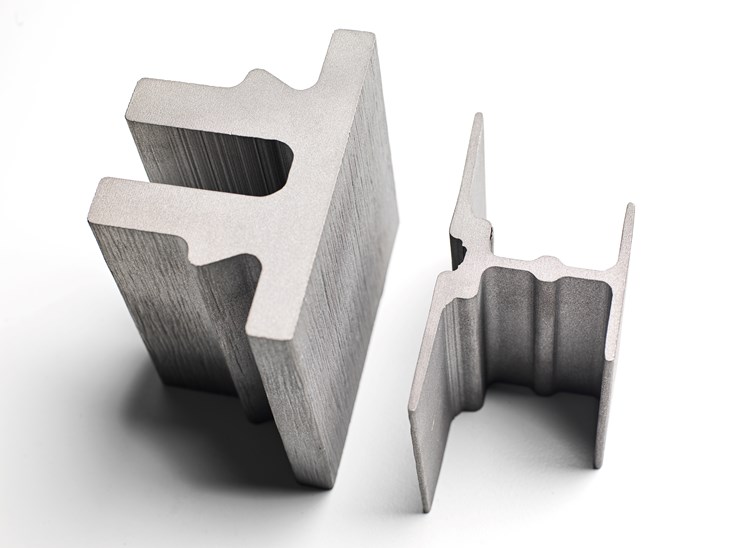
Research and development
Siderval S.p.A./HSEP/Cefival are always looking for ways to improve their manufacturing processes, strengthened by a dedicated research and development team. “We are constantly making new investments in our machinery, educating our personnel and expanding our processes,” Zak relays. “Our research team is very important to the extrusion process as their insight allows us to make stronger, thinner, or more complex products. Some steels are harder to extrude than others, so our research aids us in utilizing different qualities and grades of steel in the future.” Zak mentions carbon steel is the easiest to extrude, whereas Inconel is one of the hardest. It all has to do with the metal’s chemistry, flexibility, heating temperatures, required force, etc.
Siderval also works with Polytech Universities and experimental research centers to further their extrusion technologies. “The extrusion and finishing processes require more advanced and sophisticated technologies to obtain a better product. We invest in getting the right information from the right people,” says Zak.
Recently, Siderval invested in a specific hot straightening machine for titanium profiles. Zak continues, “We needed to invest approximately USD $1.5 million in creating a straightening area that finished the titanium products properly. With titanium, you have to extrude at a lower temperature, and during the finishing phase the titanium must be reheated for stretch straightening and de-twisting.” In contrast, metals such as carbon, stainless and alloy are extruded at a higher temperature, then stretch straightened and de-twisted at room temperature.
Another technology the company has recently invested in is the extraction of the steel shape from the press after it has been extruded. “In the past, an operator would need to manually hook and pull the extruded bar from the press onto the cooling bay, or into water. After a $1.3 million investment, we now have an automated system to keep our operators safe and further expedite the process.” This new automated system is just one of the many automations in the extrusion facilities that are keeping personnel safe.
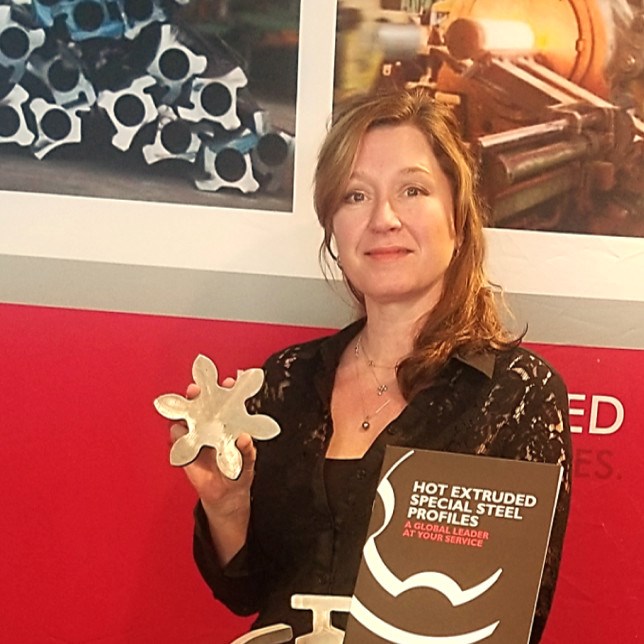
A quality service
Providing quality customer service is of utmost importance for Siderval’s business unit. “To me, it is the most important,” says Zak. “Our companies’ goal is continual improvement of our product quality and technique, while fulfilling the specific need of each individual customer. It is building a relationship, developing trust and always being there for your customer. What inspires me most in this unique position is creating new relationships, discovering new products, and learning how our steel shapes are differently utilized. “Each customer is unique, and our goal is to make business easier for them. Seeing each customer’s design and making that design a reality is something really incredible to witness and be a part of. We are available to our customers almost 24 hours a day.”
Siderval S.p.A./HSEP/Cefival aim to provide their customers with the best experience possible while fulfilling their steel profile needs. “There are only a handful of steel extrusion companies around the globe, and we have three of them under one business unit, so we want to make sure our customers are happy throughout the entire process. We ship orders directly to our customers, handle the freights, and make sure our customers get the solutions they are looking for,” relays Zak.
The Calvi Network Hot Extrusion Business Unit operates to the quality standards of UNI EN ISO 9001, ISO 9100 Aerospace, ISO14001 Environment, NA-DCAP Aerospace, ISO 45001 Security, ISA 50001 Energy, TUV AD-2000MERK-BLTT WO/TRD 100 AD-MERKBLATT ATT WO/TRD 100 AQAP 2120 Ed.I., among many others. Zak says, “We are also equipped to conduct several technological tests: hardness, microhardness and tensile tests, chemical analysis by spectrographic methods, non-destructive testing using magnetoscopic examination, and surface tests for roughness.”
Looking ahead
The extrusion business unit has many plans for the future, including a possible expansion of their facilities into the United States and/or China. “We do not have any stocking facilities yet, but it is something we are looking to do in the future. Some plans have been slightly delayed due to the Coronavirus pandemic. We are continuously looking forward to and excited about our future possibilities.”
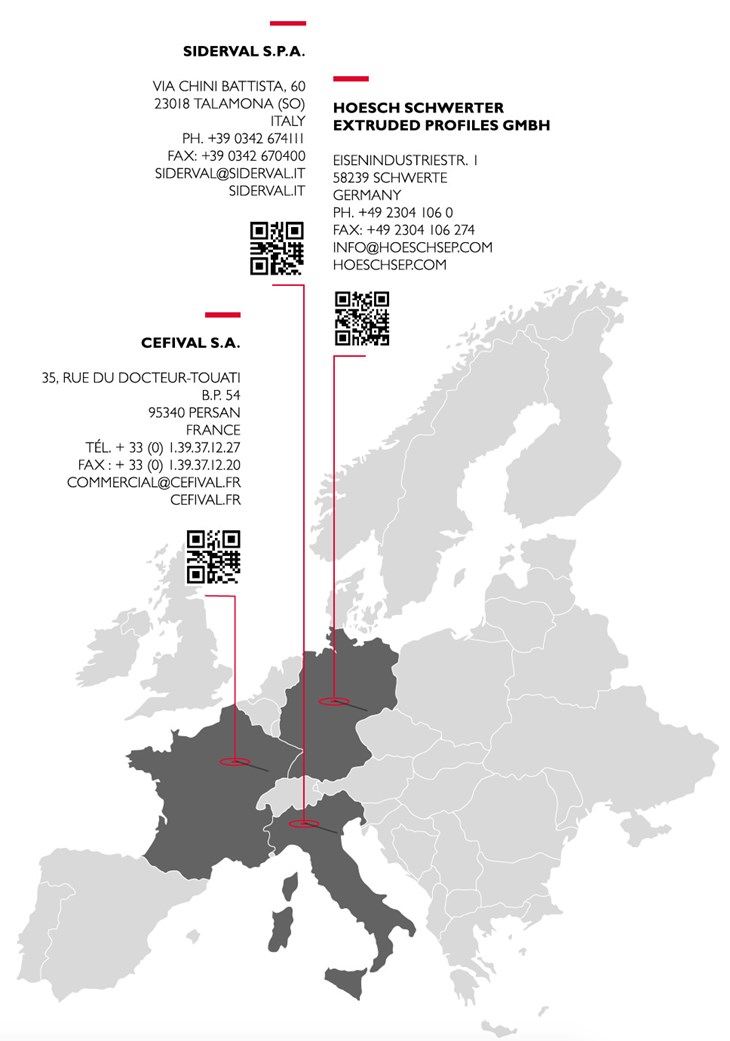