In Part Two of his interview with Stainless Steel World Americas, Lock discussed the various projects he has worked on; as each industry requires certain specifications and standards, each application he constructed was unique and needed to be carefully considered when it came to material selection. During his 10 years as a Project Manager and Consultant, Lock made it his goal to constantly acquire knowledge about different materials and their characteristics in order to best serve his customers and achieve absolute safety and productivity.
By Catarina Muia
Melting metals
In one of his more unique projects, Lock was assigned to a client that was looking to melt-down gold and silver. The end-result was a ceramic knuckle heater, which Lock compares to a brick fire pit. The entire outer shell of the component would be insulated with a ceramic fiber material, and, using a fire pit as an example, the heating elements would be inside the bricks themselves, which would radiate heat toward the center to melt gold and silver. “It is like a clamshell, you can open it up and when the heater dies, you can take it out and replace it with a new heater,” Lock describes. However, at 1,700°F + there are material issues to take into consideration.
First, due to oxidization, the barrel nuts that had been welded together began to fail. The tighter barrel nuts are clamped around the heated component, the better the heat transfer will be. When temperatures are reaching 1,700°F +, however, the welds can break, and the barrel nut springs will deform. The welds can break, and the barrel nut springs will deform. As contact is lost between the barrel nuts and the component, the heater will begin to bake itself instead of the ceramic cauldron, which will cause failures.
For the heating element, Lock initially used Nichrome wire, which heats up very quickly but cannot withstand high temperatures. Once he discovered he needed a more temperature-resistant material, he switched to Kanthal wire which, unlike Nichrome, is slower to heat up but can withstand extremely high temperatures. Lock then swapped the bolts and barrel nuts from 316 stainless steel to 430 stainless steel. “430 Stainless steel will last a lot longer at higher temperatures and is the material that will best withstand corrosion at 1,700°F +,” he says. “If, at any time, you need to construct an element that needs to reach high temperatures and are insulated by anything that is not cladded metal, you want to use 430 stainless steel.”
Challenges faced using exotic alloys
During his 10-year role as a Project Manager and Consultant, Lock was also responsible for procuring the materials that were required for each project. At times, especially when a project required the use of exotic alloys, the procurement of the materials could be the most challenging aspect of the project.
Lock recalls a specific project that required the construction of three circulation heaters for the nuclear medical isotope industry. One of the hard specifications that had been outlined was that all the tubing within the heaters, which would be withstanding hydrochloric acid (HCL), needed to be constructed of tantalum tungsten. The entire body would be cast of aluminum, all the tubing would be tantalum tungsten, and the core heater would made from Incoloy 800. All of the materials would get mixed together into one device and required a Canadian Registration Number (CRN), which is a pressure vessel license, issued by the Technical Standards and Safety Authority (TFSA). The component also required Canadian Standards Association (CSA) and Electrical Safety Authority (ESA) inspections.
“The tubing itself was the hardest thing to find because the specified alloy could only be purchased from one supplier. When I first checked, there was a 16-week lead time on the tubing. I told the supplier that I would like to purchase it so I could manufacture this circulation vessel, and they just said the material was unavailable and they were unable to give me a quote,” Lock recalls. “I explained that they had already quoted me, but they insisted and kept saying no because they were unable to buy from the mine. They could not produce the material and they could not get me what I needed.”
Lock continues to explain that at the time, there were many people in Canada and in the United States (U.S.) that required tantalum tungsten, and there was nothing that could be done about it. Lock went back to the end-user and requested to use alternatives available on the market instead and replace the material every few years, but the customer insisted that tantalum tungsten was a hard specification; “it needed to be this specific tantalum tungsten, and this was a one-shot deal. After going back and forth with the end-user a few times I decided I had to step back because there was nothing I could do, and I let them know that. After about a month, I figured the project was dead, but the tubing ended up on my dock, procured by the stakeholders that were far up in the food chain.”
In this case, it was the procurement of the material that was most challenging for Lock. Certain obscure metals can be very challenging to procure, but materials are specified for a reason, and those specifications should be followed in order to achieve absolute safety and productivity of the application.
Certain applications, such as carbon black furnaces, which is considered an extremely high-temperature furnace typically used for refining in the mining industry, cannot use materials like 316 stainless steel, Inconel, or Pyrosil (an alloy that gives excellent oxidation and nitridation corrosion resistance, and can withstand temperatures up to 2,282°F). These materials will oxidize at such a fast rate that a sensor cannot be kept inside, and temperatures will cause many other issues.
In these cases, in order for the flame temperature of blast furnaces to be monitored, Lock would manufacture the furnaces’ outer bodies of ceramic and a 90%+ platinum Type-S thermocouple, and the rest of the components were constructed of rhodium. “The problem is that the costs of the exotic alloys are insane, they are super expensive. Machined, rare earth metals are incredibly expensive. It can go from hundreds of dollars per inch, to thousands of dollars per inch. You go from pricing things to cents per foot, then when using these exotic alloys, you realize you need to make every millimeter count,” he says.
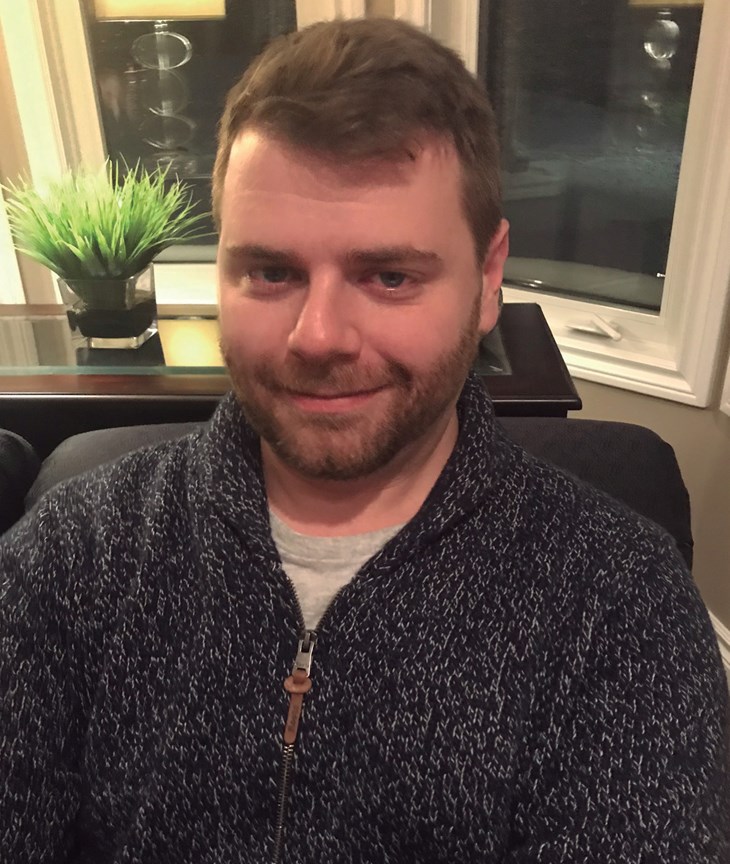
Assisting the next generation
Throughout his 10 years working on projects for end-users, Lock learned it is also crucial to teach and help the next generation of engineers and operators. In order to pass along his knowledge and educate the young minds entering the industrial sectors, Lock would accept university students as clients and help them build their final projects. In one specific case, Lock worked with a group of students and a professor to find a way to maintain a 5 liter (L), 8 L, and 10 L 317 low-carbon stainless steel vessel at approximately 138°F, to have media flow from Teflon tubes into cannabis vape cartridges. The robotic filler would fill around 200 cartridges in an hour. “Prior to the robotic filler, this task was done using a syringe, which means there was no accuracy. This robotic filler kept the oil at the perfect temperature, there were no errors, and because it was all done robotically, there was no need for any human intervention,” says Lock.
The goal of the project was to keep a consistent temperature throughout the entire filling process in order for the media to flow properly through the small pumps in the system. To do this, the stainless steel vessels had to be preheated. “It was not a makeup heat, the tank itself would do a bulk of the heating. The stainless steel vessels were jacketed in silicone rubber heaters, and the Teflon tubes that the cannabis oil would flow through, were also wrapped in spiralled silicone rubber heaters.”
To complete this project, Lock had to know the wall thickness of the stainless steel, the mass of the tank, the contents of the tank, and the insulations that needed to surround the tank to determine the wattage required to reach and maintain predetermined temperatures. It was crucial for him to also know and understand the properties of the stainless steel including its inner and outer environments, the grade, the surface finish, the elements used to create the steel in order to understand the interaction between heat going into it, how much heat could be absorbed, and how much heat would be lost due to radiation. In this case, the material used was 317 low-carbon stainless steel, which is typically used in the pharmaceutical industry.
The project brought success to the group of students and the professor, who eventually opened up their own pharmaceutical company. For this reason, Lock knows it is important to spend time with students. Even if he did not have all the answers to their questions, he would direct them to the correct company. “It is really important to me that the next generation has the right tools to be successful,” Lock expresses. “A lot of people do not want to give knowledge for free, but they are students. So many of their projects turned out to be awesome, and they would go on to win prizes and grants. When you support people in Academia, for every handful of failures you are going to get a winner, and that winner offsets everything else.”