The importance of informing
Yee has a background in chemical engineering and specialization in material science, which has given him the opportunity to gain experience in process engineering, developing SCADA systems, and non-metallic engineering.
After graduating from college in 2009, Yee began his career as a Plant Engineer at United Salt Corporation. In this position he handled the company’s larger project-related problems, which involved coatings, the use of plastics and fiberglass, acid brick towers, and other types of materials in chemical processes. After he had the chance to work on a variety of projects, Yee attained an understanding of what types of materials were best-suited for particular processes and applications, and become more familiar as time went on. It was also during this time that Yee met Richard Taraborelli, who became his mentor.
“That is where the ‘RT’ comes from in RTConsults: Richard Taraborelli. I was still quite green in 2013 when I started the business, however, Rich had been in the business for about 40 years before he retired in 2017 and taught me everything he knew. Since he was my mentor, I carried over a lot of his teachings and dealings in the business and began to help a lot of his clients,” Yee explains. “This would include ensuring that the client was following procedures and industry standards by using the correct materials for a variety of services.”
Industrial coatings use in sulfuric acid, brine, and chlorine plants are not typically touched or dealt with on a regular basis by most industry personnel. This leads to more scrutiny and the need to double check everything to ensure the coatings meet the correct requirements. Chloride levels in the application also need to be regulated and frequently checked before the coating has been applied. “Once I tell customers the steps they need to take after applying the coating, people will often say, ‘Why would I do all that extra work?’ to which I respond with: ‘You have to, otherwise you are going to experience failures because surface preparation is everything.’”
Ensuring that his clients are well-informed is an essential part of Yee’s position, not only at RTConsults, but in the industry as a whole. While there are a number of standards and regulations to follow in order to maintain the required level of quality and safety, there is not enough information available about the various materials and coatings to those who really need it. “In the materials and coatings world there is so much that needs to be covered, and currently, there is not enough information out there,” Yee explains. He warns that while search engines such as Google might have some information available, at times it can actually be more dangerous to search the internet for this type of information. “It would be like self-diagnosing when you are feeling unwell. If you are not ‘brought up’ in the industry it can be difficult to go from knowing absolutely nothing at all to obtaining that complete understanding.”
In order to spread this information to as many people in the industry as possible, Yee has become involved in several professional organizations and chair technical committees including the National Association of Corrosion Engineers (NACE), the American Welding Society (AWS), and the American Society of Mechanical Engineers (ASME). “It is not that we are trying to create barriers for people to understand, but there are some people who just want to know how to run a plant and do not put much thought into the little details that need to be dealt with. Upon realizing what our jobs, roles, and responsibilities are in the coatings, and plastics industry, the people in these plants and companies become interested and supportive; the industry has embraced what we do,” says Yee.

Coatings for projects
RTConsults is heavily involved with the back-end work of many capital projects. At the beginning of each project, Yee must review all fiberglass and coating drawings, as well as the specifications of the piping and tank provided by the client to ensure they conform with the specified service they will be applied to, as well as confirm that the materials of construction are correct for the rated service. While many people would assume the correct materials have been chosen, Yee warns that no chances should be taken. Having had the chance to walk through so many plants in various industries, he has witnessed applications that had been constructed of the wrong material for the specified process.
Once he has received and reviewed the drawings and specifications, Yee then asks the client for the management of change (MOC) or the process conditions that would have been written and signed off by the plant’s process engineers. With the MOC, Yee can then determine whether or not there can be a transition from one material to another, or a change from one process to another. These plans are required because of process safety management (PSM) audits, which is an industry safety standard to manage process risk.
“The MOC must be completed in order for us to move forward. The operations, maintenance, process, and project workers all need to be on the same page about the material that will be used for the specified limits of service,” Yee states. “This could mean hydrochloric acid (HCl) at 20% or 37%, or it can even be at different temperatures. Temperature tends to be the biggest problem with these non-metallic materials because they are very susceptible to freezing or high temperatures, especially the higher temperatures. You can go up 10° and have one material be a more suitable option than another.”
There tends to be a lot of grey area during this process, which means Yee has to ask the client as many questions as possible, including, ‘what are your upset conditions?’ Essentially, when a process has just been started, it cannot be run on normal parameters, which means it must be run must higher. The reason for this is because the cooling water has not been completely activated, or the process is in a steady state. This is considered your upset conditions.
Once Yee and his team have obtained the required information, the next step of the project is the execution. The information is passed along to the procurement department in order to bid out to a fabricator or contractor so they can get the full scope of the work. Every detail of each step must be included, such as welding and laminator procedures and certificates. These certificates will ensure that qualified people working on the project. “The big thing that plants need to look out for are unqualified welders and applicators,” says Yee. “If a weld is done incorrectly on the plastic or steel sheets and does not conform with industry standards, the weld will most likely be the root failure for the process.”
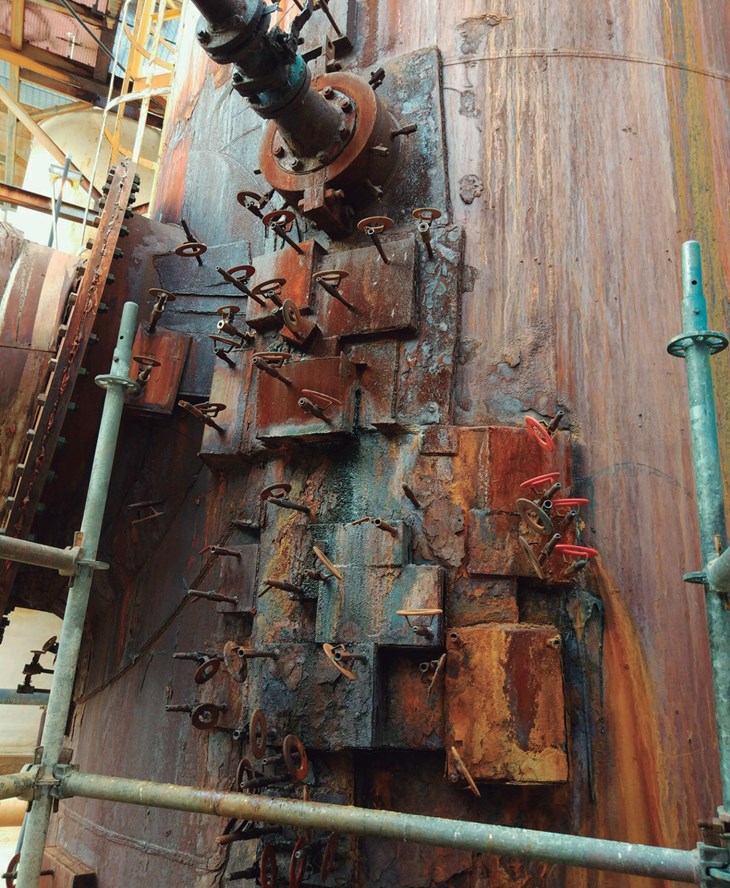
Challenges experienced
While some companies may contact RTConsults to prevent failures, a majority of Yee’s clients have already experienced a failure and are looking for a solution to prevent further issues.
“In the fertilizer industry they install a lot of liners to store phosphoric acid, and in one tank we looked at there were more than 30 holes. The craziest part is the tank had only been in service for about two months. Because the tanks were a rushed order, the coatings had been applied as a liner system during the winter. Unfortunately, those coatings will not catalyze below 40°F or 50°F, so they will just sit there and will not cure,” Yee explains. “The company kept adding more and more layers and the coatings did not bond correctly, which created a pocket of uncured resin and essentially a leak path to the steel.” When a liner is made this way, while it may look like it is a solid liner, soft spots will be present where the coatings never cured, and acid will penetrate these areas in a matter of days.
A client in phosphoric acid production also experienced a similar issue. Producing phosphoric acid for the beverage industry this client had the phosphoric acid contained in a tank with glass flakes in the lining that were exposed to the chemicals because of poor application technique. As a result, the phosphoric acid found a leak path to the steel began to eat at the tank, and the tank began to leak after a year when the warranty period expired. Eventually the floor had to be replaced but caused a year of unfortunate delays and cost to the plant.
Another factor that needs to be considered to avoid failures are trace materials. While engineers may be adamant about using a specific type of material for the construction of an application, they need to be sure that the process will not affect the material’s integrity. A good example of this is 2205 duplex stainless steel. When using this material, there cannot be any free chlorine in the brine solution, but if the process’ pH is abnormal, there is a chance that free chlorine will be present. If there is more than 50 parts per million of free chlorine, the 2205 duplex stainless steel pipes or tank will pit, and the welds will be destroyed.
“In one case, I saw a 3-mile-long pipeline that was completely eaten up in a matter of just two years, precisely for this reason. When we went back to the manufacturer to see what could bedone, they were completely unaware of the free chlorine in the brine solution. They said, ‘Had we known the specifications of the process, we would not have constructed the pipeline out of 2205 duplex stainless steel.’” Having a thorough understanding and maintaining communication between manufacturers and the process engineers are crucial in order to manufacture a safe and productive application. “From there, the engineers can either decide to use Hastelloy 276 or lined PTFE pipes. In this particular case they went with both.”
Failure that shows the pitting in 2205 duplex stainless steel material used where free chlorine was present in brine solution.
Another reason these issues can occur is by not having the correct instrumentation to pick up the trace materials. “If your instrumentation does not pick up these trace materials, it is never ‘there’ until a disaster occurs. Then you must go back and figure out the cause of failure,” Yee states.

Final thoughts
At the end of the day, if Yee has been able to help someone, he is happy. “The part I enjoy the most is helping people. This is stuff that normal, everyday people have problems with. Helping them, whether we get paid or not, is important to me because they are just asking for help.” By attending and participating in conferences, Yee has a platform to bring awareness and educate various industries on how to keep plants productive and safe. “I love that teaching aspect, and now I have the chance to teach my employees the way that Richard would have taught me. Being able to do that is extremely rewarding. Those are my two main reasons to wake up in the morning; promote the truths that are out there that people need to be aware of, and training my employees.”