The need for stainless
It is likely that much of the electricity, heat and power in the future will be generated locally and not transmitted long distances. In essence, the world is going to look more like the way it did in the 1920s when most power was generated by units smaller than 100 MW. A significant portion of this energy will be generated by gas engines with some unique stainless steel requirements. Heat will be recovered in stainless steel heat exchangers. Urea for NOx control will be injected with stainless steel distribution systems. The urea delivered to the site will come from production facilities which will make liberal use of stainless steel materials. The reasons for the metamorphosis in energy generating sources are:
- Availability of low cost natural gas (including LNG and shale) in most countries
- Stranded and flared gas and environmental initiatives driving their use
- Small scale LNG and virtual pipeline
- Synthetic gas sources such coal in China and coal bed methane and biogas elsewhere
- Lack of transmission lines in developing countries and cost of transmission lines in developed countries
- Decentralization of energy use (a remote data center will use as much electricity as a small city)
- High cost of central coal and gas turbine combined cycle plants
- The fertilization effect of Co2 from gas engines and impact not only on small greenhouses but large enclosed agricultural operations
Between 2016 and 2020, gas fired engine sales are projected to rise from 5100 MW/yr to 7100 MW/yr for an increase of 40 percent during the period or a CAGR of nine percent.
Growth is projected to continue at the nine percent CAGR through 2030. Gas is likely to be the fuel for 15 percent of the combined heat and power additions in 2020 but that could grow to more than 40 percent by 2030.
The potential of CHP
There is a very large opportunity to reduce greenhouse gases and lower net energy costs with combined heat and power. There are 291,000 potential CHP sites in the U.S with a total of 240,000 MW of capacity. The large world market includes a significant percentage of (30-100 MW) generators driven by both gas and liquid fuels. However the biggest potential is in small sites requiring less than 30 MW.
Agriculture should be viewed independently due to the tremendous potential for CO2 fertilization and significant increases in the world’s food production. GE, Cummins, Wartsila, and others are positioning themselves for a big increase in CHP for greenhouses. The energy created by gas engine cogeneration systems in greenhouses can be used in various ways. The electricity can provide the power for artificial lighting and/or be fed into the public grid. And while the heat can efficiently meet the greenhouse‘s requirements, the CO2 from the engine exhaust gas can help fertilize the plants. That is because the exhaust from gas engines burning natural gas contains approximately 0.2 kg of CO2 per kWh of energy input.
After purification of the exhaust gas with SCR and oxidation catalytic converters it is cooled down by a stainless steel heat exchanger to approximately 55°C and supplied to the greenhouse for CO2 enrichment.
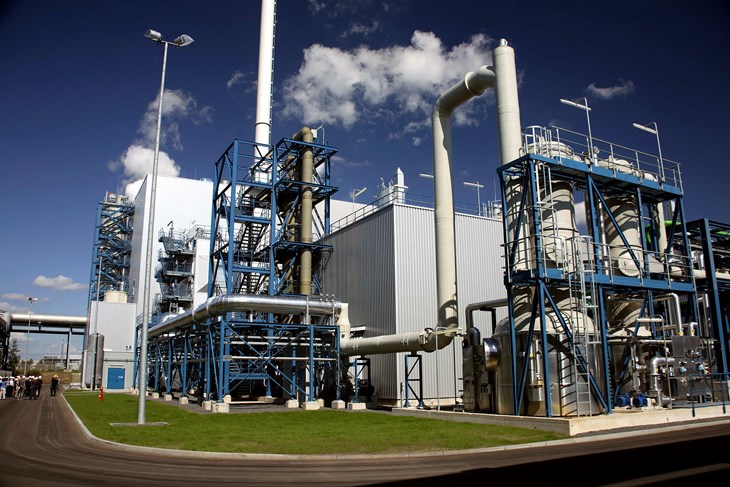
Heat recovery & stainless
Heat recovery is the key to an efficient CHP system. This creates a good potential market for stainless steel. An integrated waste management and energy company in Malmö, Sweden, is using Tranter Plate Heat Exchangers to capture waste heat from boiler flue gas condensate and cool this stream prior to purification and discharge. Gas cleaning from the waste-to-energy boiler takes place in a four-stage scrubber. Heat in the condensate from the top stage of the scrubber is transferred to the district heating loop through a Tranter Model GXD-205 exchanger. During the exchange, the scrubber condensate is cooled to a temperature 1–2 °C (1.8–3.6°F) above the incoming district heating water.
Two other heat exchangers complete the condensate heat recovery and cool- ing process. Plates for all three units were manufactured in 254 SMOTM stainless steel (1.4547) to withstand chlorides and fluorides in the flue gas condensate.
Large-bore gas engines, with a cylinder diameter ranging from 20 to 50 cm, are often used as prime movers for cogeneration of heat and power. In order to be competitive these engines are increasingly upgraded in terms of a high- er output per cylinder volume. Further, a higher output per cylinder volume decreases the negative effect of friction losses and heat losses on the cylinder process. Two-stage turbocharging, based on two turbochargers in series with an intercooler in between, substantially helps to increase the power output per cylinder.
In addition, the emission of undesired species such as particulates is limited by increasingly stringent legislation. This requires a maximum reduction in lubricating oil consumption and also requires a combustion process which is as complete as possible. As a result, the interface between the valve and the valve seat becomes increasingly free of combustion that would otherwise form a protective layer on the valves and valve seats. The much higher peak cylinder pressure than in the past, with values up to 250 bar, increases the stress level that the valves and their seats experience. Improvements in engine performance have therefore resulted in unacceptable valve wear rates, especially for the exhaust valves. Hard facing alloys such as Stellite and Tribaloy are therefore required.
The majority of CHP plants will use solid fuels The NOx generated in combustion needs to be removed. Reduction is accomplished with urea as a reagent. There are needs for stainless steel in the injection area. In some cases there is a urea to ammonia process included in the system.
Looking to the future
The added demand for NOx reduction increases the need for urea. Special stainless steel grades must be used in the high pressure urea process to achieve long service life. The process conditions are highly corrosive and as the corrosion mechanism is complex, the development of suitable alloys has been concentrated in the past on refining existing grades by continuous improvement. The use of these special “urea grades” has resulted in low maintenance costs and long service life. However, new alloys have been developed: some to solve specific corrosion problems like stress corrosion cracking and others to improve safety and reliability of urea plants.
The opportunities for the use of stainless steel in combined heat and power and specifically in the fast growing segment fueled with gas will be substantial and deserves the attention of the stainless steel industry.