When choosing the best materials for superior corrosion resistance, relying on reputable suppliers to guide component decisions can save time and money in the long run.
By Buddy Damm, Senior Scientist, Swagelok Company
Fluid systems for offshore oil and gas platforms can be extraordinarily complex. The systems often include nearly 50,000 feet of tubing, more than 20,000 components, 10,000 fittings, and as many as 8,000 mechanical connections. Since offshore industrial fluid systems are challenging to service, designers must carefully consider which materials they select for these applications. One of the most important elements to think about is the system’s corrosion resistance.
When building a system, components should be made of materials that prevent corrosion damage from affecting the system’s overall performance. Though not the only consideration, component materials matter. Suppliers should certify the initial quality of material and manufacturing, as well as have the materials science expertise to support the choices over the system’s life span. Such expertise and guidance can be the difference between system success or failure (Figure 1).

How to Maintain Quality
Corrosion is virtually inevitable in the harsh conditions of offshore oil and gas platforms. There are multiple forms of corrosion, and each poses a unique threat. Corrosion occurs when metal atoms oxidize, causing the metal’s surface to lose material and the thickness of the component wall to shrink. This could ultimately lead to premature mechanical failure.
In addition, the chemical composition of the fluid being transported may have an impact on a component’s corrosion resistance. An emphasis on quality at each step must prevail, from bar stock qualification to the component’s final inspection.
Corrosion Mechanisms and Mitigation Strategies
Designing for corrosion resistance requires an understanding of the potential types of corrosion, which can be categorized as general corrosion, localized corrosion, or stress-assisted corrosion. General corrosion occurs when a susceptible alloy is exposed to a sufficiently corrosive environment. For example, low-alloy steels exhibit generalized corrosion when exposed to a humid or moist environment. For more aggressive environments, such as acids, alloys with superior corrosion resistance such as stainless steels or nickel-based alloys are necessary to minimize the impact of general corrosion.
Localized corrosion occurs when the passive oxide layer that normally pro tects an alloy from corrosion suffers localized attack. Pitting corrosion and crevice corrosion are the most common examples of localized corrosion. As the chemical reactions of pitting and crevice corrosion progress, the local environment becomes more aggressive, accelerating damage. Selecting alloys with higher Chromium (Cr), Molybdenum (Mo), and Nitrogen (N) contents
enhances resistance to pitting and crevice corrosion.
Stress-assisted corrosion occurs when a susceptible alloy is placed in a corrosive environment and subjected to static or cyclic tensile loads. Common examples include chloride ion (Cl-) stress corrosion cracking (SCC) and sulfide (H2S) stress cracking (SSC).
Resistance to SCC improves with increasing nickel (Ni) content in austenitic stainless steels and Ni-based alloys. In oil and gas environments, multiple stress-assisted corrosion mechanisms can act synergistically. The NACE MR0175 / ISO 15156 standard provides guidance for alloy selection based on the environmental conditions such as acidity (pH), chloride ion and H2S concentration, and temperature. More aggressive environments lead to the need to use more highly alloyed stainless steels or Ni-based alloys.
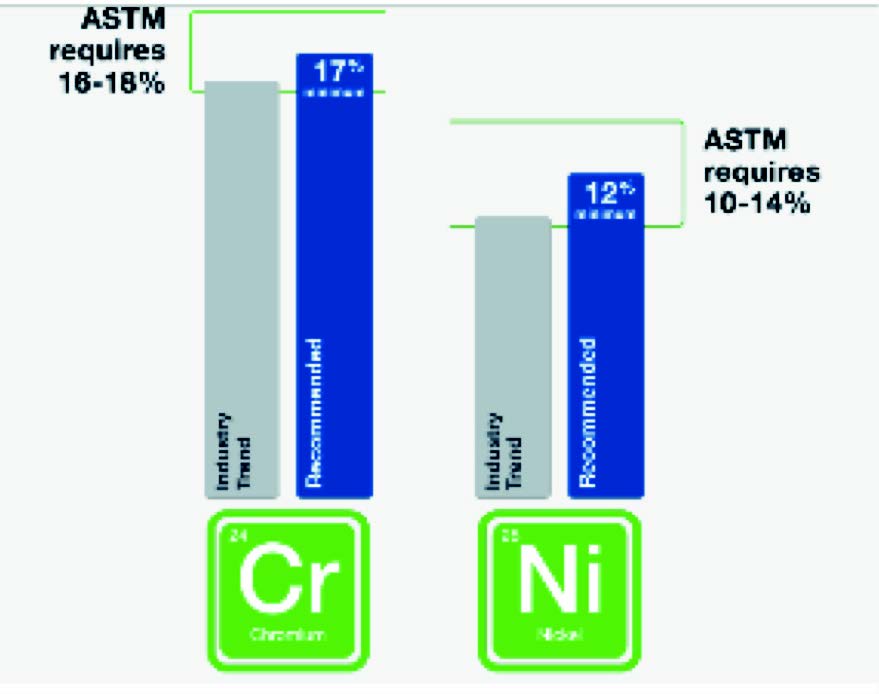
Working With Reliable Suppliers
The simplest way to avoid corrosion problems damaging industrial fluid systems is to work with suppliers with stringent quality control measures. Even the bar stock should be inspected, whether visually or using non destructive testing techniques. In some cases, ensuring corrosion resistance may require specialized testing, which the supplier should provide.
Another way a supplier can help verify the material’s suitability is to check for levels of specifi c elements in the material’s composition. Optimizing the composition of the material alloy is important for corrosion resistance, strength, weldability, and ductility. As an example, adding greater quantities of Ni and Cr in 316 stainless steel than are minimally required by the American Society of Testing and Materials (ASTM International) standard specifications results in materials with better corrosion resistance. A supplier should always provide the chemical composition of a material and indicate compliance with standards published by the International Standards Organization (ISO) and ASTM International (Figure 2).
Maintaining Quality Assurance During Manufacturing
During Manufacturing Reputable suppliers inspect components throughout their production. Verifying that the manufacturer follows best practices during the component’s construction and then testing them afterward helps ensure no corners were cut. Components coming off a manufacturing line should have no visual defects or imperfections that could lead to premature failure. They should be tested to ensure they are leak tight to keep employees safe and reduce overall production costs.
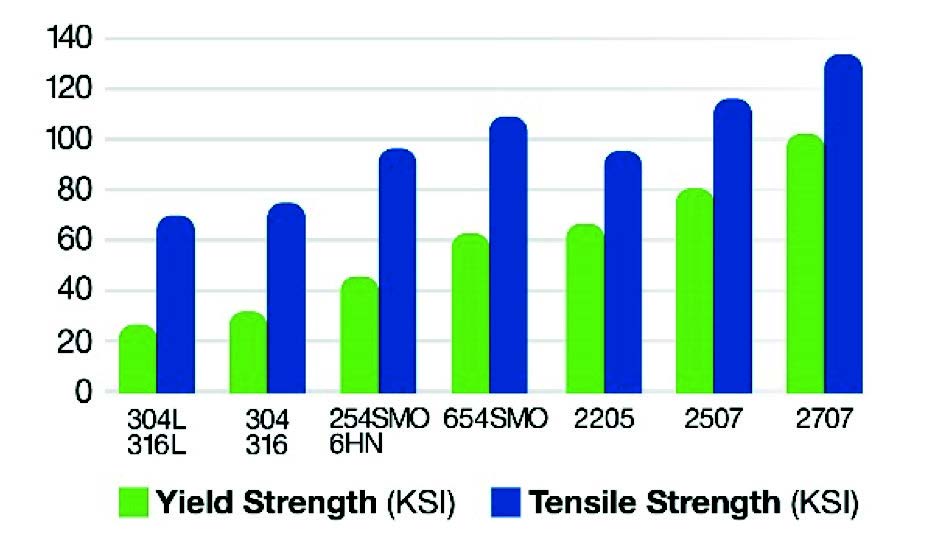
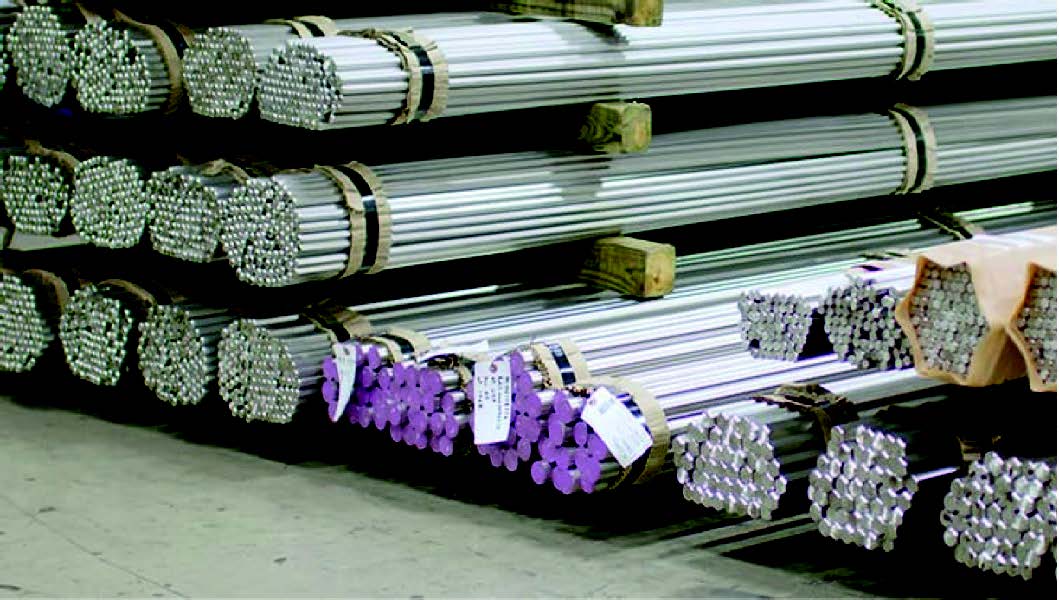
Choosing Suppliers with Materials Science Expertise
If both the materials and components pass manufacture and design standards, deciding which components to use should be application-specific and requires a full understanding of specific operating conditions. A reliable supplier with materials science expertise can guide designers through the process to ensure they choose the right components.
Seeking Higher-Strength Materials
A component’s mechanical properties should be examined before it is chosen for specific applications. Considerations should include tensile strength and ductility. The higher the quality of materials used in the component’s construction, the more likely it will perform as expected, particularly when subjected to high pressures (Figure 3).
Ensuring Component Compatibility
In addition to affecting system performance, corrosion can cost significant money to correct. According to NACE International, corrosion costs the oil and gas industry USD $1.4 billion per year.
Understanding where corrosion is likely to occur and catching it early can help to lower repair costs over time. If system designers choose the right materials at the outset, then system integrity, component life cycles, consistent performance, and safety all improve.
The following steps reduce the impact of corrosion on applications:
• Identifying types of corrosion – what it looks like, where it occurs, and why it happens,
• Selecting materials resistant to corrosion,
• Minimizing locations where corrosion can occur and reducing contact with non-compatible metals, and
• Specifying everything from the supports and clamps to the tubing itself to reduce the potential for corrosion.
The Bottom Line
When choosing between components for offshore oil and gas platforms, selecting premium materials suited for the application minimizes corrosion. Suppliers should provide ongoing support over the life cycle of the system, although not every supplier has the expertise to advise which components will work best for specific applications.
Suppliers with highly credentialed experts on staff can offer fluid system professionals training in materials science and metallurgical engineering, which may help them make the right component selections. Armed with this knowledge, design engineers will develop industrial fluid systems to withstand even the harshest operational conditions.