As governments worldwide strive to reduce carbon emissions and mitigate the effects of climate change, industries have taken on the challenge of meeting strict carbon reduction targets. Carbon capture has emerged as a crucial player in its ability to achieve these goals. The United States has set itself an ambitious target of capturing and storing 2.0 metric gigatons of CO2 per year by 2050, which could require up to 32 metric megatons of steel for the creation of pipelines, capture units, drilling wells, and other essential infrastructure, according to estimates from the Department of Energy.
By Mark McLeod, Mechanical Engineer, OGC Energy
How Does Carbon Capture, Utilization, And Storage (CCUS) Reduce Emissions?
Carbon Capture, Utilization, and Storage (CCUS) is an umbrella term that encompasses a range of technologies designed to remove CO2 from fluids, including air (Direct Air Capture) and flue gas (Industrial Capture), as well as utilizing or storing the captured CO2 underground. Usually, saline aquifers or abandoned oil and gas wells are used to store these emissions. This article will focus on Industrial Capture.
Industrial capture CCUS technology, which is based on gas sweetening and the removal of CO2 from natural gas, employs amines such as MEA, MDEA, and PIP to separate CO2 from flue gases. The process begins by directing the flue gas to an absorber tower, where aqueous amines bond with CO2 molecules.
The resulting gas mixture is then sent to a stripper tower, where captured CO2 is separated and prepared for further processing and transport. Typically, after capture and separation, the CO2 is dehydrated before being directed to a compressor station and ultimately either to a trunkline or a storage site.
For industries that cannot decarbonize using traditional methods, such as reducing energy consumption or changing processes, carbon capture provides a viable solution to reduce emissions. It is expected that industries such as power generation, steel, cement, and fertilizer production will significantly benefit from the implementation of carbon capture technology.
The Importance of Stainless Steel in CCUS
Stainless steel is playing a crucial role in the proliferation of CCUS technology. Two significant differences set CCUS projects apart from other oil and gas operations: the highly corrosive environment that can be present when there is free water in CO2, which is exacerbated by the presence of impurities from the industrial source.
The other main factor is the potential for low-temperature service due to severe cooling caused by the Joule-Thomson effect. Currently, corrosion-resistant alloys such as duplex stainless steel and high-nickel alloy stainless steel have already been used in large capture plants worldwide, with several large orders of Duplex OCTG already in place for CCUS projects.
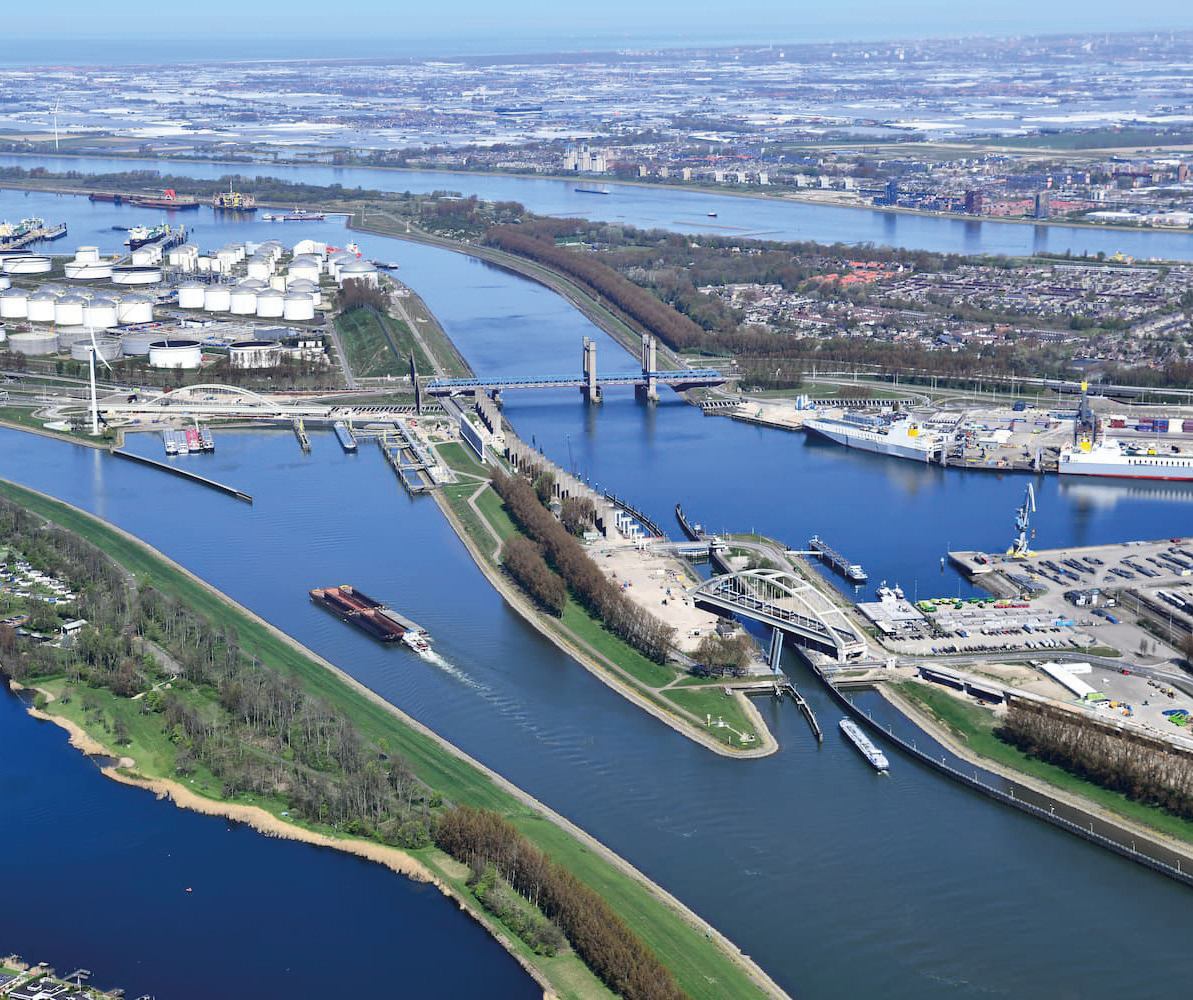
Stainless steel plays a crucial role in numerous CCUS projects. For instance, the Carbfix project in Iceland, which stores CO2 as mineral deposits underground, requires large volumes of water to fuel the process. Since access to fresh water is limited, salt-water is used, demanding the need for stainless steel. The Carbfix project made extensive use of 316(L) stainless steel to protect its asset against saltwater corrosion. Similarly, in Norway, the Sleipner project has been injecting CO2 into a saline aquifer for over 20 years. The condition of the wellhead requires the use of duplex tubing and casing for injection. The selection of the 25Cr Duplex ensures the longest-running CCUS project continues to operate smoothly.
Corrosion and Material Selection
Impurities in industrial CCUS have been shown to facilitate several damage mechanisms. The presence of O2, Chlorides, and CO can lead to stress corrosion of stainless steel, and the formation of H2SO4 due to sulfurous impurities, such as H2S and SO2. This can lead to localized attacks when a separate water-dominated phase forms.
It is important not to rely solely on injection and storage well material standards already present for environments containing H2S or CO2, as there are significant differences when injecting a CO2 stream containing impurities such as O2, NO2, SO2, CO, and H2.
Understanding the resistance of different grades of stainless steel to crevice corrosion, stress corrosion cracking, and de-passivation caused by chlorides, oxygen, and high temperatures is crucial when supplying materials for use in CCUS projects.
Upset conditions experienced by the pipeline, such as loss of process control, small leaks, shut-ins, or sudden decompression, can lead to the formation of acids resulting from impurities when pressures and temperatures change. Additionally, the boundary between the bulk stream and the injection well is likely to experience a large multi-phase boundary, which can cause formation water to wet the wellhead.
In case of a long-term shutdown, this can lead to extensive backflow of formation water. Therefore, it is essential not to rely on existing material standards for environments containing H2S or CO2 when selecting materials for CCUS projects that involve CO2 streams with impurities such as O2, NO2, SO2, CO, and H2.
Selecting the right materials for a CCUS project requires considering low-temperature embrittlement. Materials with higher toughness at low temperatures, like austenitic stainless steels, may be optimal, particularly at depleted gas storage sites where severe Joule-Thomson cooling is a concern.
To ensure proper material selection, stainless steel suppliers will need to work closely with CCUS project teams and consider the unique environmental factors and potential upset conditions involved in CCUS operations.
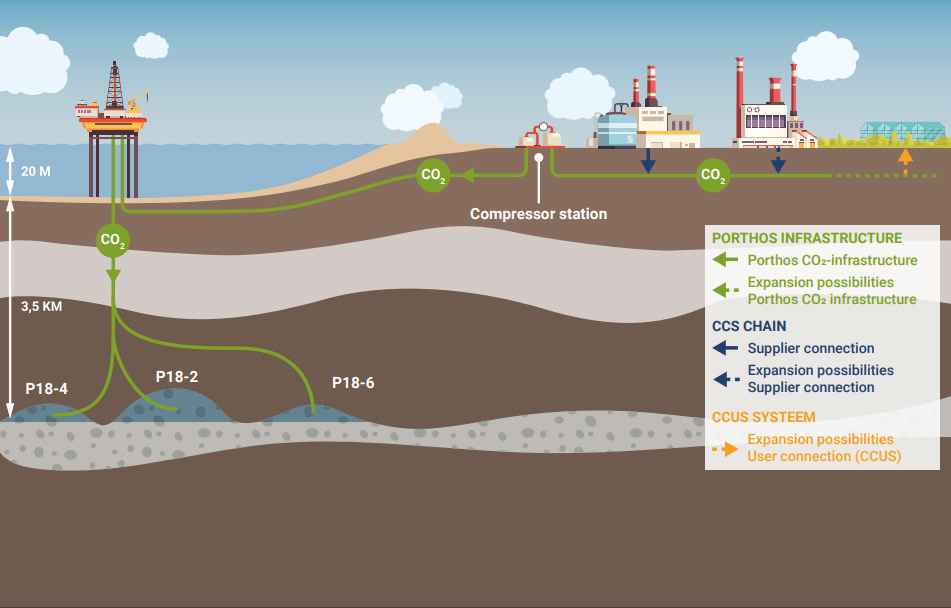
Conclusion
The use of stainless steel in CCUS projects is crucial to ensure long-term integrity and meet the safety requirements for operation. In CCUS systems, stainless steel is primarily used for equipment such as compressors and tubing for injection wells. To effectively capitalize on this emerging market, manufacturers must understand the operating conditions that the wellhead, equipment, and piping components will be exposed to, including the risks posed by impure CO2 under all possible operating conditions.
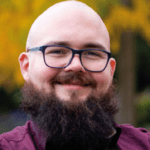